- お役立ち記事
- “Revolutionizing Japanese Manufacturing: The Precision and Art of Ceramic Machining”
月間76,176名の
製造業ご担当者様が閲覧しています*
*2025年3月31日現在のGoogle Analyticsのデータより
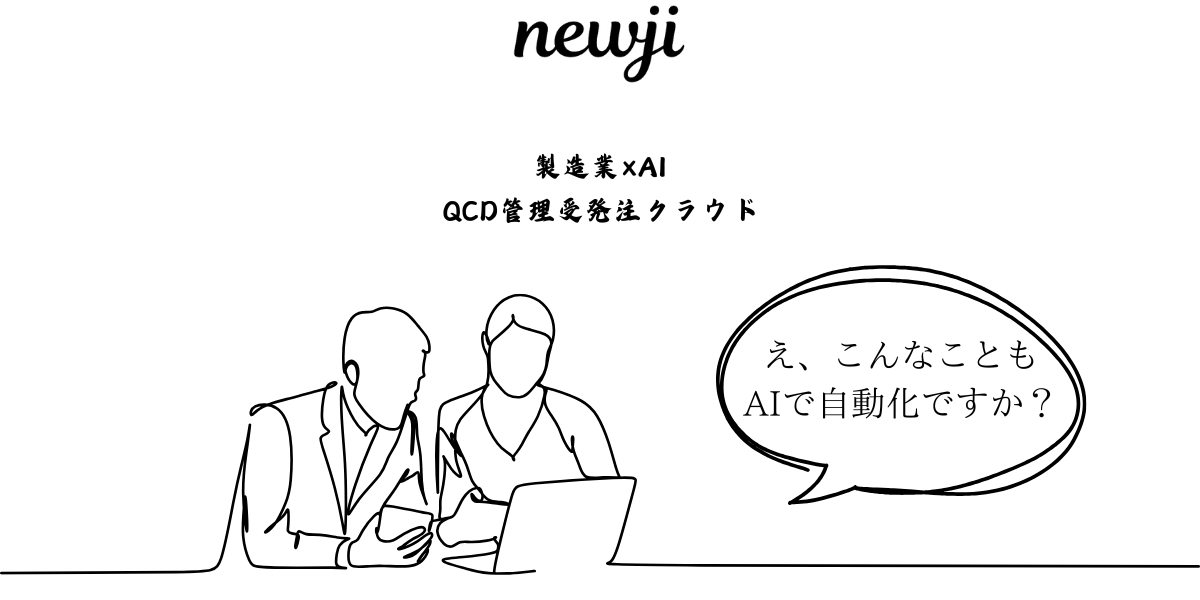
“Revolutionizing Japanese Manufacturing: The Precision and Art of Ceramic Machining”
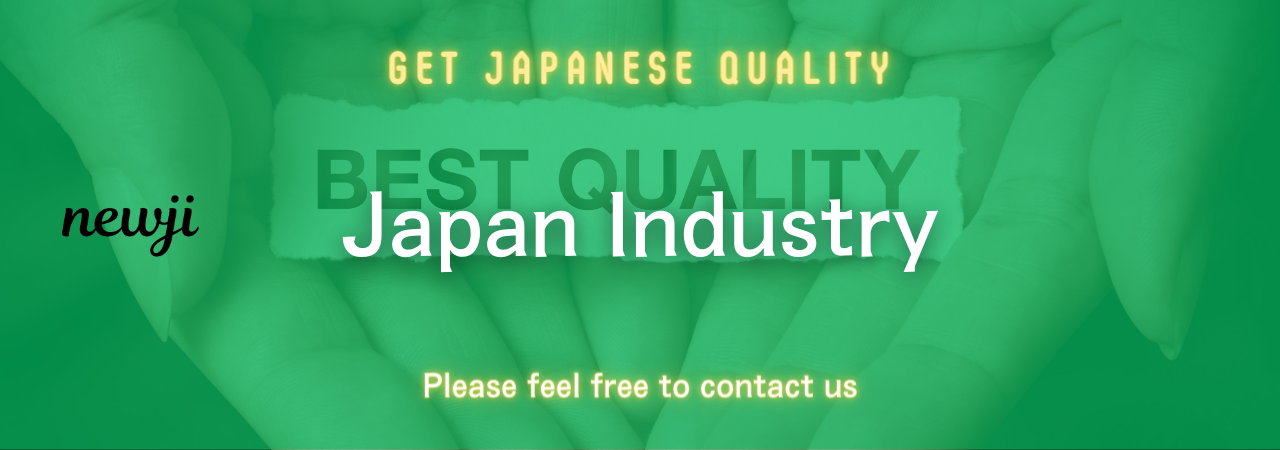
目次
Introduction
Japanese manufacturing is globally renowned for its precision, efficiency, and quality.
One of the most intricate yet transformative aspects of this industry is ceramic machining.
This process involves working with ceramics—a category of inorganic, nonmetallic materials known for their exceptional hardness and heat resistance.
When precision machining meets the art of ceramic materials, the results are often revolutionary.
From aerospace to electrical engineering, ceramic components play a crucial role in diverse high-tech industries.
The Importance of Ceramic Machining in Manufacturing
Ceramic machining has become increasingly essential in manufacturing due to the unique properties of ceramic materials.
These materials offer a high degree of thermal and electrical insulation, resistance to wear and corrosion, and the ability to withstand extreme temperatures and harsh environments.
Such attributes make ceramics ideal for high-performance applications in fields like aerospace, medical devices, and renewable energy.
However, machining ceramics is not without its challenges.
Due to their hardness and brittleness, ceramics are difficult to machine using traditional methods.
In this context, Japan stands out due to its innovative techniques and specialized expertise in ceramic machining.
Why Choose Japanese Suppliers for Ceramic Machining?
Japanese suppliers are often the go-to choice for high-precision ceramic machining for several reasons.
First, Japan’s long history in manufacturing excellence means that their suppliers bring a wealth of experience and advanced technological capabilities.
Second, the country places a strong emphasis on quality and continuous improvement through practices like Kaizen.
These factors combine to make Japanese suppliers highly reliable and capable of delivering superior ceramic components.
Market Conditions and Trends
The global market for ceramic machining has been experiencing steady growth, driven by increased demand from sectors such as electronics, aerospace, and healthcare.
Currently, Japan captures a significant share of this market, thanks to its advanced machining technologies and strong network of skilled suppliers.
Moreover, Japanese manufacturers are continually investing in research and development, further propelling them ahead in the industry.
With the rising trend of automation and smart factories, Japanese companies are well-positioned to maintain their competitive edge.
Advantages of Ceramic Machining in Japan
Opting for Japanese suppliers for ceramic machining comes with numerous advantages that can significantly impact the overall quality and efficiency of your manufacturing processes.
High Precision and Quality
Japanese manufacturers are synonymous with precision.
Advanced equipment, coupled with meticulously maintained standards, ensures that even the most complex ceramic parts meet stringent specifications.
This high level of precision translates to better performance, reliability, and longevity of the final product.
Advanced Technological Integration
Technological prowess is a hallmark of Japanese manufacturing.
From automated machining centers to advanced CAD/CAM software, Japanese facilities are equipped with state-of-the-art technologies.
This ensures not only the accuracy of the ceramic components but also facilitates faster turnaround times and greater consistency in production.
Skilled Labor Force
One of the key strengths of Japanese manufacturing lies in its highly skilled workforce.
Technicians and engineers undergo rigorous training and continuous learning, which keeps them updated with the latest machining techniques and innovations.
Their expertise becomes particularly invaluable when dealing with the complexities of ceramic machining.
Strong Focus on Research and Development
Japanese companies are heavily invested in R&D, which keeps them at the forefront of technological advancements.
This focus on innovation helps in developing new ceramic materials and machining techniques, continually pushing the boundaries of what is possible.
Consequently, businesses that collaborate with Japanese suppliers often benefit from cutting-edge solutions tailored to meet specific requirements.
Challenges in Ceramic Machining
Despite its numerous advantages, ceramic machining comes with its own set of challenges. Understanding these can help in making informed decisions and overcoming potential hurdles.
Material Hardness and Brittleness
Ceramics are extremely hard and brittle, which makes them inherently difficult to machine.
Traditional machining methods like drilling or milling can cause cracks, fractures, or even total part failure.
Specialized equipment and techniques are required to achieve the desired precision without damaging the material.
High Production Costs
The need for specialized equipment and skilled labor makes ceramic machining more expensive than machining metals or plastics.
Initial setup and tooling costs can be high, impacting the overall budget, especially for smaller production runs.
Lack of Flexibility
Once the machining process has been set up, making changes can be challenging and costly.
For instance, altering the design or specifications of a ceramic part may require new tooling and a complete re-evaluation of the machining process.
Such constraints make it less flexible compared to other types of machining.
Negotiation Techniques with Japanese Suppliers
Navigating supplier relationships requires a well-considered approach, especially in the context of Japanese businesses where cultural nuances play a crucial role.
Building Trust
Trust is a cornerstone of Japanese business culture.
Long-term relationships are often prioritized over short-term gains.
Engaging in open, honest communication and consistently fulfilling commitments will go a long way in establishing a strong partnership.
Understanding “Nemawashi”
Nemawashi is an informal process of laying the groundwork for decisions by talking to key people and gaining their support.
Before formal meetings, understanding the perspectives and gaining the buy-in of influential figures within the supplier organization can be very beneficial.
The Etiquette of Negotiations
In Japan, formalities are important.
Punctuality, the exchange of business cards, and polite language are essential.
Additionally, showing respect for the supplier’s expertise and taking a humble approach can foster goodwill and facilitate smoother negotiations.
Clear and Detailed Communication
Japanese suppliers appreciate clear, detailed, and concise communication.
Providing comprehensive documentation and specifications helps in minimizing misunderstandings and ensures that both parties are aligned on expectations and requirements.
Best Practices in Ceramic Machining
Implementing best practices can help in achieving the highest levels of precision, quality, and efficiency in ceramic machining.
Selective Material Choice
Choosing the right ceramic material for your application is crucial.
Different types of ceramics have distinct properties.
For instance, alumina is known for its strength and wear resistance, while zirconia offers better toughness and thermal insulation.
Working closely with your supplier to select the appropriate material can significantly affect the performance and cost-effectiveness of the final product.
Using Advanced Machining Techniques
Employ advanced techniques such as laser machining, ultrasonic machining, and Electrical Discharge Machining (EDM) for optimal results.
These methods are particularly effective in managing the hardness and brittleness of ceramics, thereby reducing the risk of damage and improving precision.
Quality Control and Inspection
Rigorous quality control is vital in ceramic machining.
Using precision measurement tools like Coordinate Measuring Machines (CMM) ensures that each part meets the necessary specifications.
Moreover, regular inspections during the production process can help in identifying and addressing issues before they escalate.
Continuous Improvement
Adopting a culture of continuous improvement or Kaizen can result in incremental enhancements in the machining process.
Encourage collaboration and feedback among engineers, technicians, and operators to identify opportunities for optimization and innovation.
A Case Study: Success in Ceramic Machining
Consider a leading aerospace firm that required high-precision ceramic components for turbine engines.
Initially, the company faced several challenges, including high failure rates and extended lead times.
Collaborating with a Japanese supplier, they underwent a comprehensive review of their material and machining processes.
Material Selection and Machining Technique
After in-depth consultations, they opted for stabilized zirconia for its exceptional toughness and thermal properties.
The Japanese supplier employed advanced EDM techniques to achieve the desired precision.
Quality Assurance
Through a robust quality control program, they implemented interim checks and detailed inspections to ensure each part met stringent criteria.
Outcome
This partnership reduced the failure rate by 40% and achieved a 20% improvement in lead times, showcasing the transformative impact of advanced ceramic machining techniques.
Conclusion
Revolutionizing Japanese manufacturing through ceramic machining unveils a world of precision, innovation, and excellence.
By tapping into Japan’s expertise, advanced technologies, and strong quality control mechanisms, businesses can achieve superior ceramic components that meet demanding applications.
Understanding the challenges and leveraging best practices further ensure that these benefits are fully realized.
Navigating supplier relationships with cultural sensitivity and clear communication turns these collaborations into long-term, mutually beneficial partnerships.
Embrace the art and precision of ceramic machining from Japan to catalyze your manufacturing success.
資料ダウンロード
QCD管理受発注クラウド「newji」は、受発注部門で必要なQCD管理全てを備えた、現場特化型兼クラウド型の今世紀最高の受発注管理システムとなります。
ユーザー登録
受発注業務の効率化だけでなく、システムを導入することで、コスト削減や製品・資材のステータス可視化のほか、属人化していた受発注情報の共有化による内部不正防止や統制にも役立ちます。
NEWJI DX
製造業に特化したデジタルトランスフォーメーション(DX)の実現を目指す請負開発型のコンサルティングサービスです。AI、iPaaS、および先端の技術を駆使して、製造プロセスの効率化、業務効率化、チームワーク強化、コスト削減、品質向上を実現します。このサービスは、製造業の課題を深く理解し、それに対する最適なデジタルソリューションを提供することで、企業が持続的な成長とイノベーションを達成できるようサポートします。
製造業ニュース解説
製造業、主に購買・調達部門にお勤めの方々に向けた情報を配信しております。
新任の方やベテランの方、管理職を対象とした幅広いコンテンツをご用意しております。
お問い合わせ
コストダウンが利益に直結する術だと理解していても、なかなか前に進めることができない状況。そんな時は、newjiのコストダウン自動化機能で大きく利益貢献しよう!
(β版非公開)