- お役立ち記事
- Revolutionizing Japanese Manufacturing: The Rise of Arc Welding Robots
月間77,185名の
製造業ご担当者様が閲覧しています*
*2025年2月28日現在のGoogle Analyticsのデータより
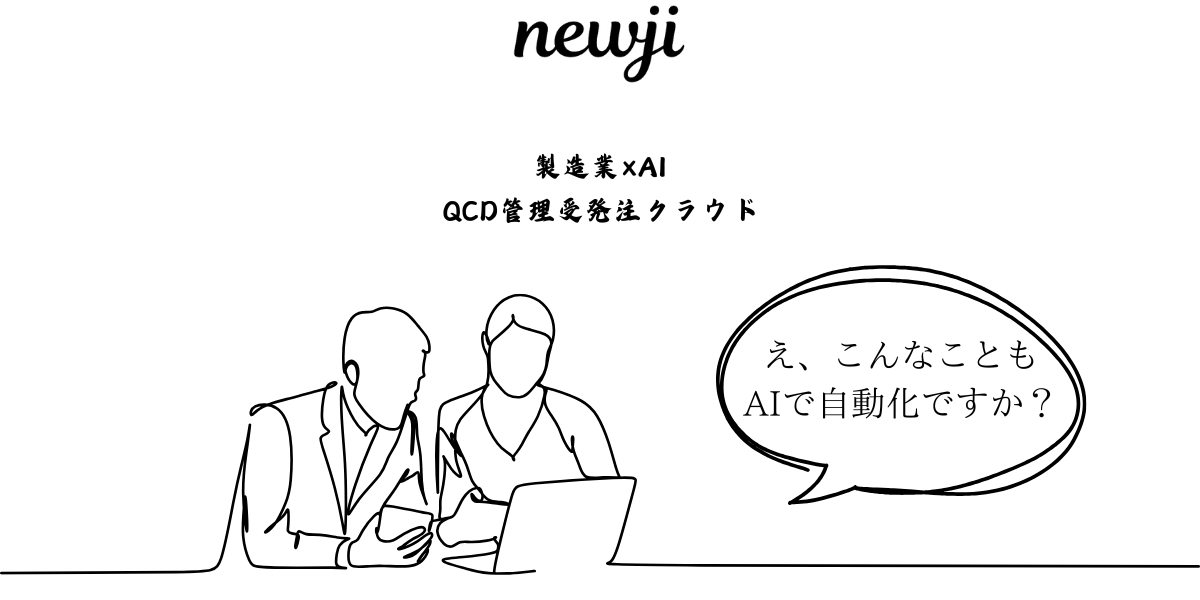
Revolutionizing Japanese Manufacturing: The Rise of Arc Welding Robots
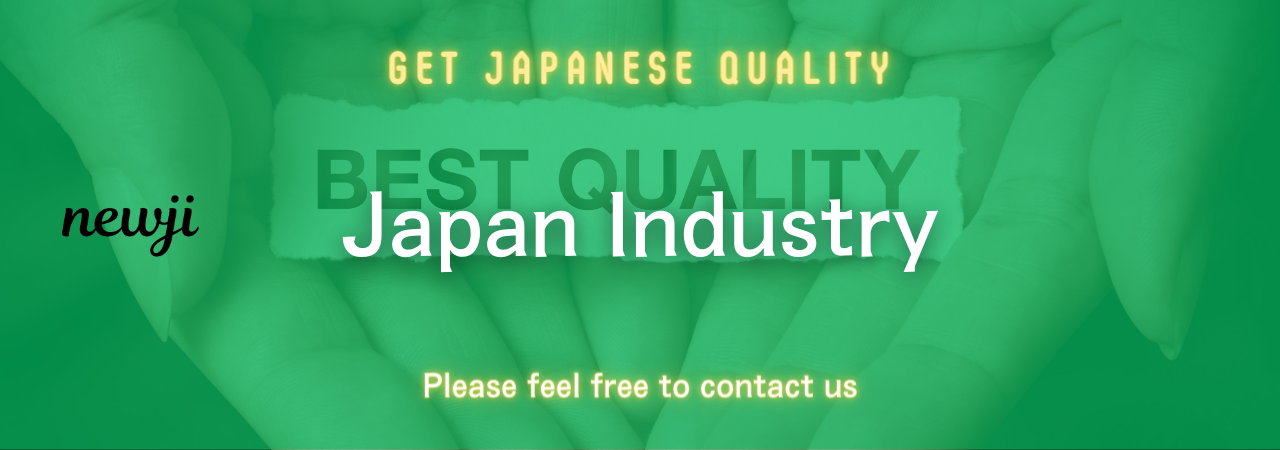
目次
Introduction
The landscape of Japanese manufacturing is undergoing a significant transformation with the integration of advanced technologies.
Among these, arc welding robots are at the forefront, revolutionizing production processes.
This shift is not only enhancing efficiency but also redefining the role of procurement and purchasing in the industry.
Understanding the rise of arc welding robots in Japanese manufacturing is crucial for businesses aiming to leverage these advancements.
This article delves into the practical aspects of procuring these robots, explores their advantages and disadvantages, and provides insights into effective supplier negotiation techniques.
By examining market conditions and best practices, manufacturers can make informed decisions to optimize their operations and maintain a competitive edge.
The Evolution of Arc Welding Robots
Arc welding robots have evolved significantly over the past few decades, driven by advancements in robotics and automation.
Initially, these robots were limited in functionality and required extensive human intervention.
However, recent innovations have enhanced their precision, speed, and adaptability, making them integral to modern manufacturing.
Japanese manufacturers, renowned for their emphasis on quality and efficiency, have been pivotal in this evolution.
They have developed robots capable of handling complex welding tasks with minimal supervision.
This evolution is a testament to Japan’s commitment to maintaining its leadership in manufacturing technology.
Advantages of Arc Welding Robots in Japanese Manufacturing
Increased Precision and Consistency
Arc welding robots offer unmatched precision, ensuring consistent weld quality across production batches.
This consistency reduces defects and improves the overall quality of manufactured products.
By minimizing human error, robots contribute to a more reliable manufacturing process.
Enhanced Efficiency and Productivity
The automation of welding processes significantly boosts productivity.
Robots can operate continuously without breaks, leading to higher output rates.
This increased efficiency allows manufacturers to meet growing demand without compromising on quality.
Cost Savings
While the initial investment in arc welding robots is substantial, the long-term cost savings are significant.
Reduced labor costs, lower defect rates, and increased production efficiency contribute to a favorable return on investment.
Additionally, robots help in minimizing material wastage, further enhancing cost-effectiveness.
Improved Workplace Safety
Welding involves exposure to intense heat and hazardous fumes.
By automating these processes, manufacturers can protect workers from occupational hazards.
This not only enhances safety but also complies with stringent workplace safety regulations.
Flexibility and Scalability
Modern arc welding robots are highly adaptable, capable of handling various welding tasks with ease.
This flexibility allows manufacturers to scale operations and adapt to changing production needs seamlessly.
Robots can be reprogrammed for different tasks, enhancing the versatility of the manufacturing process.
Challenges and Disadvantages
High Initial Investment
The acquisition of arc welding robots requires a significant initial capital outlay.
This investment can be a barrier for small and medium-sized enterprises looking to adopt automation technologies.
Technical Complexity
Implementing and maintaining welding robots demands specialized technical expertise.
Manufacturers may need to invest in training or hire skilled personnel to manage these advanced systems.
Integration with Existing Systems
Integrating robots into existing manufacturing workflows can be challenging.
Compatibility issues may arise, necessitating modifications to current processes or infrastructure.
Dependency on Suppliers
Reliance on robotic suppliers, particularly those in Japan, can create dependencies.
Supply chain disruptions or changes in supplier policies can impact production schedules and operational efficiency.
Maintenance and Downtime
Despite their reliability, robots require regular maintenance to operate optimally.
Unscheduled downtime due to technical issues can disrupt manufacturing processes and affect output.
Supplier Negotiation Techniques for Procurement
Understand the Market
Before entering negotiations, it is essential to have a comprehensive understanding of the arc welding robot market.
This includes knowledge of key suppliers, pricing trends, and technological advancements.
Build Strong Relationships
Japanese business culture places a high value on relationships and trust.
Building a strong rapport with suppliers can lead to better terms, priority service, and long-term partnerships.
Leverage Volume Purchases
Negotiating for bulk purchases can secure favorable pricing and terms.
Suppliers are often more willing to offer discounts and tailored solutions to customers committing to larger orders.
Emphasize Long-Term Partnership
Positioning your procurement strategy as a commitment to a long-term partnership can be advantageous.
Suppliers are more inclined to provide support and flexibility to partners with whom they foresee enduring collaborations.
Negotiate Service and Support Terms
Beyond the purchase price, negotiating comprehensive service and support terms is crucial.
This includes warranties, maintenance agreements, and technical support, ensuring the longevity and reliability of the robots.
Understand Cultural Nuances
Being mindful of Japanese business etiquette and cultural practices can enhance negotiation outcomes.
Respect, patience, and attentiveness are key traits valued in Japanese negotiations.
Market Conditions for Arc Welding Robots
The global manufacturing sector is experiencing a surge in automation adoption, with Japan leading the charge in robotics technology.
Several factors are influencing the market conditions for arc welding robots:
Technological Advancements
Continuous innovations in robotics and artificial intelligence are making arc welding robots more capable and efficient.
These advancements are driving demand as manufacturers seek to stay competitive.
Labor Shortages
A declining workforce in manufacturing industries is pushing companies towards automation solutions.
Arc welding robots help mitigate the impact of labor shortages by maintaining production levels.
Economic Factors
Economic stability and growth in key markets impact investment in automation technologies.
During periods of economic expansion, manufacturers are more likely to invest in advanced robotics.
Regulatory Environment
Stringent safety and quality regulations in the manufacturing sector necessitate the adoption of automated solutions like arc welding robots to ensure compliance.
Global Supply Chain Dynamics
Disruptions in global supply chains have underscored the importance of efficient and reliable manufacturing processes.
Arc welding robots contribute to more resilient production systems by enhancing operational efficiency.
Competitive Pressure
Intense competition in the manufacturing sector drives the adoption of technologies that can provide a competitive edge.
Arc welding robots offer manufacturers the ability to produce high-quality products at lower costs, thereby enhancing competitiveness.
Best Practices in Procuring Arc Welding Robots from Japan
Conduct Thorough Supplier Research
Before engaging with suppliers, perform comprehensive research to identify reputable manufacturers.
Evaluate suppliers based on their technological capabilities, reputation, and customer feedback.
Assess Total Cost of Ownership
Consider all associated costs, including purchase price, installation, training, maintenance, and potential downtime.
A holistic view of the total cost of ownership ensures more accurate budgeting and financial planning.
Request Detailed Proposals
Obtain detailed proposals from multiple suppliers to compare offerings.
Ensure that proposals include specifications, pricing, service terms, and implementation timelines.
Verify Compliance and Certifications
Ensure that the arc welding robots meet industry standards and certifications.
Compliance with safety and quality regulations is essential for seamless integration into your manufacturing processes.
Foster Transparent Communication
Maintain open and transparent communication channels with suppliers.
Clear communication helps in setting expectations, addressing concerns promptly, and ensuring alignment on project goals.
Implement Pilot Programs
Before full-scale deployment, consider implementing pilot programs to test the functionality and compatibility of the robots.
Pilot programs allow for the identification and resolution of potential issues in a controlled environment.
Invest in Training
Provide comprehensive training for your staff to operate and maintain the arc welding robots effectively.
Well-trained personnel can maximize the benefits of automation and minimize operational disruptions.
Plan for Future Scalability
Ensure that the procurement strategy accommodates future scalability.
Selecting robots that can be easily upgraded or expanded supports long-term growth and adaptability.
Monitor and Evaluate Performance
Regularly monitor the performance of the arc welding robots to ensure they meet expected standards.
Continuous evaluation helps in identifying areas for improvement and optimizing operational efficiency.
Building Strong Relationships with Japanese Suppliers
Establishing robust relationships with Japanese suppliers is key to successful procurement.
Japanese business culture emphasizes trust, respect, and mutual benefit, which are critical for long-term partnerships.
Embrace Cultural Sensitivity
Understanding and respecting Japanese cultural norms can enhance interactions with suppliers.
This includes punctuality, formality in communication, and appreciation for hierarchical structures.
Engage in Regular Communication
Frequent and consistent communication fosters trust and ensures alignment on project objectives.
Regular updates and feedback sessions can preempt misunderstandings and facilitate smoother collaborations.
Show Commitment to Partnership
Demonstrate your commitment to the partnership by being reliable and honoring agreements.
This builds trust and encourages suppliers to prioritize your business needs.
Provide Mutual Value
Seek ways to create value for both parties in the partnership.
This may include sharing market insights, collaborating on innovation, or supporting each other’s business goals.
Understanding Cultural Nuances
Navigating cultural differences is essential when dealing with Japanese suppliers.
A nuanced understanding of Japanese business etiquette can prevent potential conflicts and foster a harmonious working relationship.
Respect Hierarchical Structures
Japanese companies often have well-defined hierarchical structures.
Acknowledging and respecting these hierarchies during interactions is important for maintaining professionalism.
Exercise Patience in Negotiations
Business negotiations in Japan may take longer compared to Western counterparts.
Patience and persistence are essential traits to navigate the negotiation process effectively.
Prioritize Group Harmony
Japanese business culture values group harmony and consensus.
Encouraging collaborative discussions and group decision-making can lead to more successful outcomes.
Avoid Confrontational Approaches
Maintaining a non-confrontational and respectful demeanor is crucial.
Constructive criticism should be delivered tactfully to preserve the relationship.
Appreciate Formalities
Formalities, such as exchanging business cards with both hands and bowing during greetings, are integral to Japanese business etiquette.
Observing these practices demonstrates respect and fosters positive impressions.
Conclusion
The rise of arc welding robots is fundamentally transforming Japanese manufacturing, driving enhancements in precision, efficiency, and safety.
For manufacturers seeking to adopt these advanced technologies, understanding the intricacies of procurement and purchasing is vital.
Navigating the challenges associated with high initial investments and technical complexities requires strategic planning and informed decision-making.
Supplier negotiation techniques, coupled with an appreciation of Japanese cultural nuances, can significantly influence procurement success.
By adhering to best practices and staying attuned to market conditions, businesses can effectively integrate arc welding robots into their manufacturing processes.
Ultimately, the strategic adoption of arc welding robots positions manufacturers to achieve greater operational excellence and maintain a competitive advantage in the global market.
資料ダウンロード
QCD管理受発注クラウド「newji」は、受発注部門で必要なQCD管理全てを備えた、現場特化型兼クラウド型の今世紀最高の受発注管理システムとなります。
ユーザー登録
受発注業務の効率化だけでなく、システムを導入することで、コスト削減や製品・資材のステータス可視化のほか、属人化していた受発注情報の共有化による内部不正防止や統制にも役立ちます。
NEWJI DX
製造業に特化したデジタルトランスフォーメーション(DX)の実現を目指す請負開発型のコンサルティングサービスです。AI、iPaaS、および先端の技術を駆使して、製造プロセスの効率化、業務効率化、チームワーク強化、コスト削減、品質向上を実現します。このサービスは、製造業の課題を深く理解し、それに対する最適なデジタルソリューションを提供することで、企業が持続的な成長とイノベーションを達成できるようサポートします。
製造業ニュース解説
製造業、主に購買・調達部門にお勤めの方々に向けた情報を配信しております。
新任の方やベテランの方、管理職を対象とした幅広いコンテンツをご用意しております。
お問い合わせ
コストダウンが利益に直結する術だと理解していても、なかなか前に進めることができない状況。そんな時は、newjiのコストダウン自動化機能で大きく利益貢献しよう!
(β版非公開)