- お役立ち記事
- Revolutionizing Japanese Manufacturing: The Rise of Industrial Robots
月間77,185名の
製造業ご担当者様が閲覧しています*
*2025年2月28日現在のGoogle Analyticsのデータより
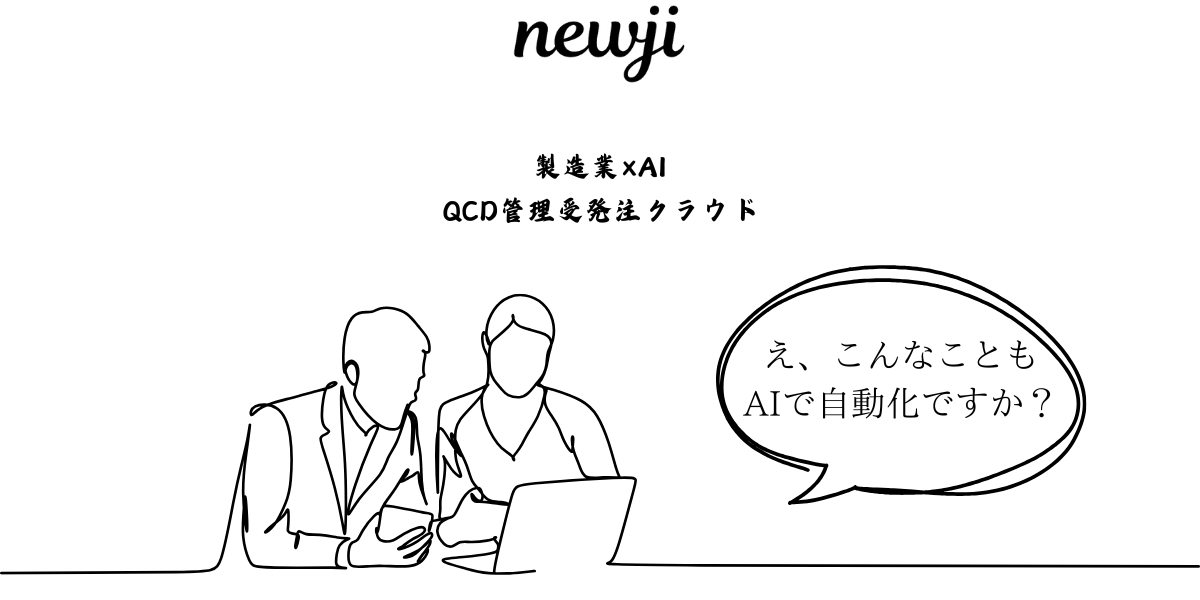
Revolutionizing Japanese Manufacturing: The Rise of Industrial Robots
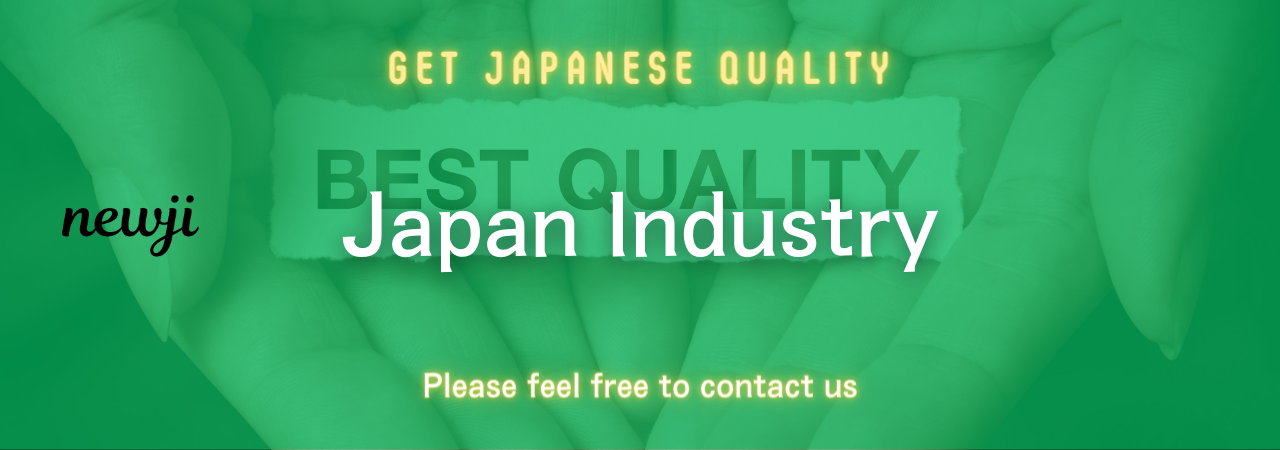
目次
Introduction
Japanese manufacturing has long been synonymous with innovation, precision, and efficiency.
In recent years, the integration of industrial robots has transformed the landscape of this sector.
The rise of these advanced machines is not merely a trend but a revolution that is reshaping production processes.
This article delves into the multifaceted impact of industrial robots on Japanese manufacturing.
It explores the advantages and disadvantages, procurement and purchasing strategies, market conditions, and best practices.
Drawing from over two decades of experience in procurement and purchasing within major manufacturing companies, this analysis provides a comprehensive overview of how industrial robots are revolutionizing the industry.
The Evolution of Industrial Robots in Japanese Manufacturing
Historical Background
The journey of industrial robots in Japan began in the late 20th century.
Initially, robots were primarily used for repetitive and hazardous tasks in automotive and electronics manufacturing.
Pioneering companies like FANUC and Kawasaki Heavy Industries led the charge in developing versatile robotic solutions.
These early adopters set the foundation for Japan’s reputation as a global leader in robotics technology.
Over time, advancements in artificial intelligence and machine learning have enhanced the capabilities of industrial robots, enabling more complex and adaptive functions.
Current Trends
Today, the integration of industrial robots extends beyond traditional manufacturing sectors.
Industries such as pharmaceuticals, food and beverage, and aerospace are increasingly adopting robotic solutions.
Collaborative robots, or cobots, are gaining popularity due to their ability to work alongside human workers safely.
The use of autonomous mobile robots (AMRs) in logistics and supply chain management is another significant trend.
These robots improve efficiency by automating material handling and distribution tasks.
Moreover, the rise of the Internet of Things (IoT) has facilitated the development of interconnected robotic systems, enhancing real-time data exchange and decision-making.
Advantages of Adopting Industrial Robots
Increased Efficiency and Productivity
One of the primary benefits of industrial robots is the substantial increase in efficiency and productivity.
Robots operate with precise timing and consistent performance, leading to higher output rates.
They can work continuously without fatigue, significantly reducing production downtime.
This consistency ensures that manufacturing processes meet stringent quality standards consistently.
Improved Quality and Consistency
Industrial robots enhance product quality by minimizing human errors and variability.
Their ability to perform tasks with high precision ensures uniformity in production.
This consistency is crucial for maintaining brand reputation and meeting customer expectations.
Moreover, robots can handle delicate tasks that require meticulous attention, further improving product quality.
Enhanced Safety
Robots take over hazardous tasks, reducing the risk of workplace injuries.
They can operate in environments that are unsafe for humans, such as high-temperature areas or spaces with toxic substances.
By delegating dangerous duties to robots, companies can ensure a safer workplace for their employees.
Cost Savings
While the initial investment in robotics can be significant, the long-term cost savings are substantial.
Robots reduce labor costs by performing tasks that would otherwise require multiple human workers.
They also decrease the likelihood of errors and defects, minimizing waste and rework expenses.
Moreover, robots can extend the operational hours of manufacturing facilities without additional labor costs.
Challenges and Disadvantages
Initial Investment Costs
The upfront cost of acquiring and implementing industrial robots is a significant barrier for many companies.
Costs include not only the purchase of robotic equipment but also expenses related to integration, training, and maintenance.
Small and medium-sized enterprises (SMEs) may find it challenging to allocate the necessary capital for such investments.
Workforce Adaptation
The introduction of robots can lead to workforce displacement, causing concerns among employees.
Workers may need to adapt to new roles that require different skill sets, leading to potential resistance.
Companies must invest in training and development programs to facilitate this transition and mitigate the impact on their workforce.
Maintenance and Downtime
While robots enhance productivity, they also require regular maintenance to function optimally.
Breakdowns or malfunctions can lead to significant production delays.
Establishing robust maintenance schedules and having skilled technicians available are critical to minimizing downtime.
Integration Complexity
Integrating robots into existing manufacturing systems can be complex and time-consuming.
Companies must ensure that the new robotic systems are compatible with current technologies and processes.
This integration often requires extensive planning and coordination across various departments.
Procurement and Purchasing Perspectives
Supplier Negotiation Techniques
Effective negotiation with robotic suppliers is crucial for obtaining favorable terms and ensuring quality.
Key strategies include:
– Conducting thorough market research to understand pricing trends and vendor capabilities.
– Engaging in long-term partnership discussions to secure better pricing and support.
– Leveraging competitive bids to drive down costs and enhance service agreements.
– Negotiating flexible payment terms and warranty conditions to mitigate financial risks.
Evaluating Market Conditions
Understanding the current market landscape is essential for informed procurement decisions.
Factors to consider include:
– Technological advancements and the availability of the latest robotic solutions.
– Supplier reliability and the stability of their supply chains.
– Price fluctuations and economic indicators that may impact costs.
– Regulatory changes and industry standards relevant to robotic integration.
Quality Assurance in Procurement
Ensuring the quality of industrial robots is paramount to successful implementation.
Companies should:
– Assess the reputation and track record of potential suppliers.
– Request detailed specifications and performance metrics.
– Conduct site visits or request demonstrations to evaluate product capabilities.
– Implement stringent quality control measures to verify that robots meet required standards before finalizing purchases.
Strategic Sourcing
Adopting a strategic approach to sourcing can optimize procurement processes.
Strategies include:
– Diversifying supplier bases to reduce dependency on a single source.
– Building partnerships with key suppliers for mutual growth and innovation.
– Utilizing technology and data analytics to streamline procurement operations.
– Focusing on total cost of ownership rather than just initial purchase price.
Market Conditions
Global Supply Chain Dynamics
The global supply chain plays a significant role in the availability and cost of industrial robots.
Disruptions such as geopolitical tensions, natural disasters, or pandemics can affect supply continuity.
Companies must develop resilient supply chain strategies, including alternative sourcing and inventory management, to mitigate these risks.
Technological Advancements
Rapid advancements in robotics technology influence market conditions.
Innovations such as artificial intelligence, machine learning, and IoT integration enhance robot capabilities.
Staying abreast of these developments is essential for companies to remain competitive and adopt the most efficient solutions.
Economic Factors
Economic conditions, including inflation rates, currency fluctuations, and interest rates, impact procurement decisions.
Economic stability facilitates investment in robotics, while volatility may hinder capital expenditures.
Companies must monitor economic indicators to time their investments effectively.
Cultural and Regulatory Environment
Japan’s regulatory framework and cultural attitudes towards automation influence the adoption of industrial robots.
Supportive policies and incentives can accelerate robotic integration, while stringent regulations may pose challenges.
Understanding and navigating these factors are critical for successful procurement and implementation.
Best Practices for Implementing Industrial Robots
Strategic Planning and Integration
Successful implementation begins with meticulous planning.
Steps include:
– Assessing current manufacturing processes to identify areas that can benefit from automation.
– Setting clear objectives and defining the scope of robot integration.
– Developing a phased implementation plan to manage the transition smoothly.
– Ensuring that robotic systems are compatible with existing technologies and workflows.
Training and Development
Investing in workforce training is essential to maximize the benefits of industrial robots.
Training programs should focus on:
– Operating and maintaining robotic systems.
– Understanding safety protocols and best practices.
– Developing skills for overseeing automated processes and troubleshooting issues.
– Encouraging a culture of continuous learning to adapt to evolving technologies.
Collaboration Between Departments
Effective implementation requires collaboration across various departments, including procurement, engineering, production, and quality control.
This interdisciplinary approach ensures that all aspects of robotic integration are addressed comprehensively.
Regular communication and coordinated efforts facilitate smoother transitions and enhance overall efficiency.
Continuous Improvement and Feedback
Post-implementation, companies should establish mechanisms for continuous improvement.
Gathering feedback from operators and analyzing performance data helps identify areas for enhancement.
Implementing iterative improvements ensures that robotic systems evolve to meet changing production demands and technological advancements.
Case Studies of Japanese Manufacturers
Toyota Motor Corporation
Toyota has been at the forefront of integrating industrial robots into its manufacturing processes.
The company’s use of robots in assembly lines has significantly increased production efficiency and product quality.
Toyota’s emphasis on continuous improvement, or “Kaizen,” ensures that robotic systems are regularly evaluated and optimized.
This approach has enabled Toyota to maintain its competitive edge in the global automotive market.
Panasonic Corporation
Panasonic employs a diverse range of industrial robots across its electronics manufacturing facilities.
Robots handle tasks such as component assembly, quality inspection, and packaging.
By automating these processes, Panasonic has achieved higher precision and reduced production costs.
The company’s investment in robotics aligns with its commitment to technological innovation and excellence.
Mitsubishi Electric
Mitsubishi Electric utilizes industrial robots in both production and logistics operations.
The company’s robots are integrated with IoT technologies to enable real-time monitoring and data analysis.
This integration enhances operational visibility and facilitates proactive maintenance.
Mitsubishi Electric’s strategic use of robotics exemplifies the benefits of blending automation with intelligent systems.
Future Outlook
The future of industrial robots in Japanese manufacturing is poised for continued growth and evolution.
Advancements in artificial intelligence and machine learning will further enhance robotic capabilities, enabling more autonomous and intelligent operations.
The integration of robotics with advanced manufacturing technologies like additive manufacturing and smart factories will create more flexible and responsive production systems.
Moreover, the ongoing emphasis on sustainability will drive the development of energy-efficient and eco-friendly robotic solutions.
As Japanese manufacturers continue to innovate, industrial robots will play an increasingly pivotal role in shaping the future of manufacturing.
Conclusion
The rise of industrial robots is revolutionizing Japanese manufacturing, bringing unprecedented levels of efficiency, quality, and innovation.
While the adoption of robotics presents challenges such as high initial costs and workforce adaptation, the long-term benefits far outweigh these obstacles.
Strategic procurement and purchasing practices, coupled with a deep understanding of market conditions and best practices, are essential for successful implementation.
Japanese manufacturers that effectively integrate industrial robots into their operations stand to gain a significant competitive advantage in the global market.
As technology continues to advance, the symbiotic relationship between humans and robots will drive the future of manufacturing, ensuring sustained growth and excellence.
資料ダウンロード
QCD管理受発注クラウド「newji」は、受発注部門で必要なQCD管理全てを備えた、現場特化型兼クラウド型の今世紀最高の受発注管理システムとなります。
ユーザー登録
受発注業務の効率化だけでなく、システムを導入することで、コスト削減や製品・資材のステータス可視化のほか、属人化していた受発注情報の共有化による内部不正防止や統制にも役立ちます。
NEWJI DX
製造業に特化したデジタルトランスフォーメーション(DX)の実現を目指す請負開発型のコンサルティングサービスです。AI、iPaaS、および先端の技術を駆使して、製造プロセスの効率化、業務効率化、チームワーク強化、コスト削減、品質向上を実現します。このサービスは、製造業の課題を深く理解し、それに対する最適なデジタルソリューションを提供することで、企業が持続的な成長とイノベーションを達成できるようサポートします。
製造業ニュース解説
製造業、主に購買・調達部門にお勤めの方々に向けた情報を配信しております。
新任の方やベテランの方、管理職を対象とした幅広いコンテンツをご用意しております。
お問い合わせ
コストダウンが利益に直結する術だと理解していても、なかなか前に進めることができない状況。そんな時は、newjiのコストダウン自動化機能で大きく利益貢献しよう!
(β版非公開)