- お役立ち記事
- Revolutionizing Japanese Manufacturing: The Rise of Innovative Picking Systems
月間76,176名の
製造業ご担当者様が閲覧しています*
*2025年3月31日現在のGoogle Analyticsのデータより
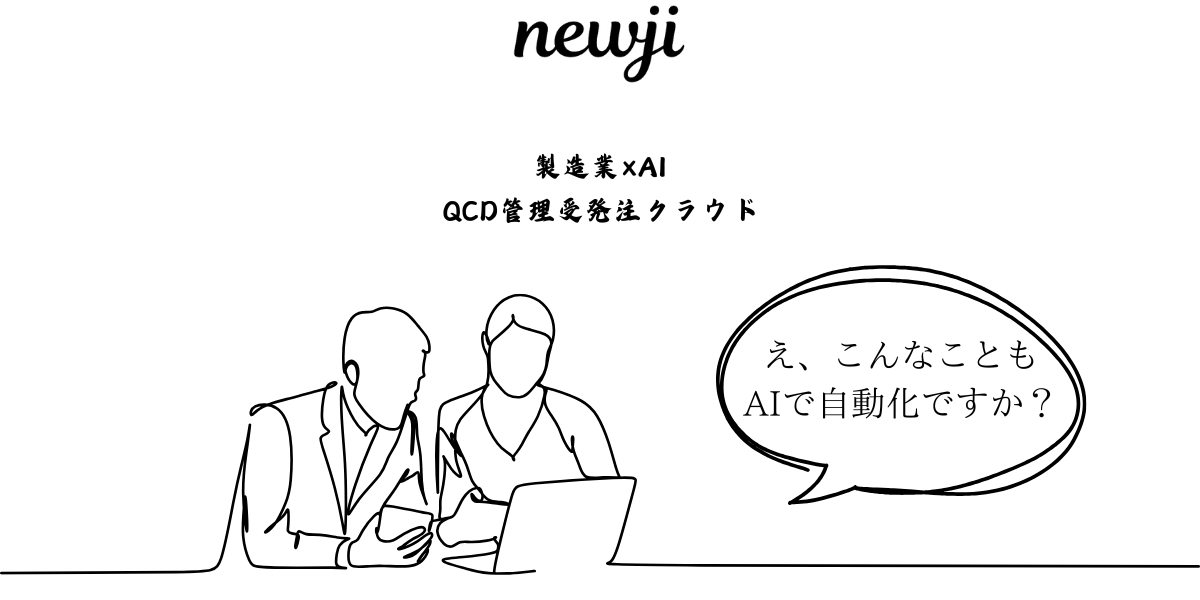
Revolutionizing Japanese Manufacturing: The Rise of Innovative Picking Systems
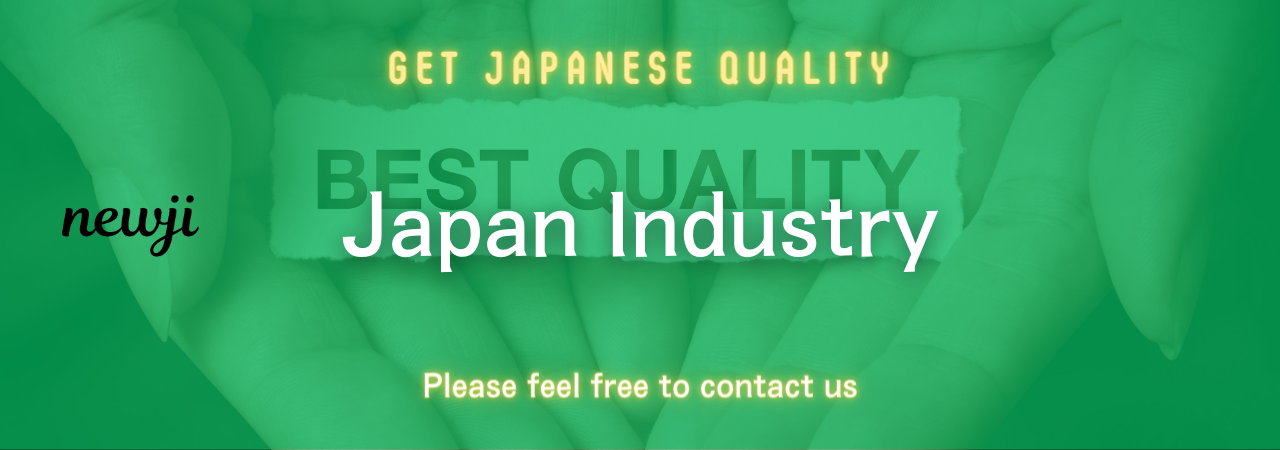
目次
Introduction to Innovative Picking Systems in Japanese Manufacturing
Japanese manufacturing has long been renowned for its precision and efficiency.
In recent years, the industry has seen a significant transformation with the introduction of innovative picking systems.
These advanced systems are revolutionizing the way components are selected and assembled, enhancing overall productivity and reducing errors.
The integration of cutting-edge technologies such as automation, artificial intelligence, and robotics has played a pivotal role in this evolution.
As a result, Japanese manufacturers are setting new standards in production efficiency and quality control.
Advantages of Innovative Picking Systems
Enhanced Efficiency and Productivity
Innovative picking systems streamline the selection process, significantly reducing the time required to locate and gather components.
Automation minimizes manual intervention, allowing for faster production cycles and increased output.
This boost in productivity enables manufacturers to meet higher demand without compromising quality.
Improved Accuracy and Quality Control
Advanced picking systems incorporate precision technologies that ensure components are selected accurately.
This reduces the likelihood of errors, leading to higher product quality and consistency.
Moreover, real-time monitoring and data analytics help identify and rectify issues promptly, maintaining stringent quality standards.
Cost Reduction
By automating the picking process, manufacturers can lower labor costs and minimize waste.
Efficient inventory management systems prevent overstocking and reduce storage expenses.
Additionally, reduced error rates translate to fewer defective products, decreasing the costs associated with returns and rework.
Scalability and Flexibility
Innovative picking systems are designed to be scalable, allowing manufacturers to adjust their operations based on demand fluctuations.
The flexibility of these systems enables easy integration with existing workflows and the ability to accommodate new product lines.
This adaptability ensures that manufacturers can remain competitive in a dynamic market environment.
Data-Driven Decision Making
These systems generate vast amounts of data, providing valuable insights into production processes.
Analyzing this data helps in identifying trends, optimizing workflows, and making informed decisions.
Data-driven strategies enhance overall operational efficiency and support continuous improvement initiatives.
Disadvantages and Challenges
High Initial Investment
The implementation of innovative picking systems requires a substantial initial investment in technology and infrastructure.
For some manufacturers, especially smaller enterprises, the cost can be a significant barrier to adoption.
Securing the necessary funding and justifying the return on investment can pose challenges.
Technical Complexity
Advanced picking systems involve sophisticated technologies that require specialized knowledge and expertise.
Training employees to operate and maintain these systems can be time-consuming and costly.
Furthermore, integrating new technologies with existing systems may present technical challenges.
Maintenance and Downtime
Automated systems are prone to technical issues and require regular maintenance to function optimally.
Unplanned downtime can disrupt production schedules and lead to delays.
Ensuring consistent maintenance and having contingency plans in place are essential to mitigate these risks.
Dependence on Technology
Reliance on automated systems makes manufacturers vulnerable to cyber threats and technological failures.
Protecting sensitive data and ensuring the security of these systems is critical.
Any breaches or malfunctions can have severe repercussions on production and business operations.
Supplier Negotiation Techniques
Building Strong Relationships
Establishing trust and fostering long-term partnerships with suppliers is crucial.
Open communication and collaboration help in aligning objectives and ensuring mutual benefits.
Regular interactions and feedback sessions strengthen these relationships, leading to more favorable negotiation outcomes.
Understanding Supplier Capabilities
Gaining a deep understanding of suppliers’ strengths and limitations enables more effective negotiations.
Assessing their technological capabilities, production capacity, and financial stability provides valuable insights.
This knowledge helps in setting realistic expectations and negotiating terms that are beneficial for both parties.
Leveraging Market Knowledge
Staying informed about market trends, industry standards, and technological advancements is essential.
This information empowers buyers to make informed decisions and negotiate from a position of strength.
Understanding the competitive landscape allows manufacturers to identify opportunities for cost savings and improvements.
Flexible Contract Terms
Negotiating flexible contract terms that allow for adjustments based on changing needs can be advantageous.
Including clauses that address scalability, performance metrics, and quality standards ensures that both parties remain aligned.
Flexibility in contracts facilitates adaptability and responsiveness to market dynamics.
Performance-Based Agreements
Incorporating performance-based terms incentivizes suppliers to maintain high standards.
Linking compensation to performance metrics such as delivery times, quality levels, and innovation contributions encourages excellence.
This approach fosters accountability and drives continuous improvement.
Market Conditions Influencing the Rise of Innovative Picking Systems
Global Supply Chain Dynamics
The globalization of supply chains has increased the complexity and demand for efficient picking systems.
Manufacturers are seeking solutions that can seamlessly integrate with diverse suppliers and distribution networks.
Innovative picking systems offer the flexibility and scalability needed to manage these complex supply chains effectively.
Technological Advancements
Rapid advancements in technologies like robotics, AI, and machine learning have enabled the development of sophisticated picking systems.
These technologies enhance the capabilities of picking systems, making them more efficient and reliable.
Continuous innovation drives the adoption of these systems as manufacturers strive to stay ahead in the competitive landscape.
Economic Pressures
Economic uncertainties and fluctuating market demands compel manufacturers to optimize their operations.
Innovative picking systems provide the efficiency and cost savings necessary to navigate economic challenges.
By improving productivity and reducing waste, these systems contribute to financial resilience and sustainability.
Labor Market Trends
A shrinking labor pool and rising labor costs in certain regions make automation an attractive option.
Innovative picking systems reduce dependence on manual labor, mitigating the impact of labor shortages and cost increases.
This shift towards automation supports consistent production levels and controlled labor expenses.
Customer Expectations
Increasing customer demands for high-quality products delivered promptly have heightened the need for efficient manufacturing processes.
Innovative picking systems enhance the ability to meet these expectations by improving accuracy and speeding up production cycles.
Meeting customer expectations is crucial for maintaining competitiveness and fostering brand loyalty.
Best Practices for Procurement and Purchasing
Comprehensive Supplier Evaluation
Conducting thorough evaluations of potential suppliers ensures that they can meet the requirements for innovative picking systems.
Assess criteria such as technological expertise, reliability, quality standards, and financial stability.
This due diligence process minimizes risks and fosters strong partnerships with capable suppliers.
Strategic Sourcing
Adopting a strategic approach to sourcing involves identifying and leveraging suppliers that offer the best value.
Consider factors beyond cost, such as quality, innovation, and service capabilities.
Strategic sourcing aligns procurement activities with long-term business goals, enhancing overall competitiveness.
Collaborative Planning
Engaging in collaborative planning with suppliers facilitates better alignment of production schedules and inventory management.
Sharing forecasts, demand projections, and production plans fosters transparency and coordination.
This collaboration reduces lead times and ensures that innovative picking systems are well-integrated into the production process.
Continuous Improvement
Implementing continuous improvement practices ensures that procurement and purchasing processes remain efficient and effective.
Regularly assess performance metrics, seek feedback, and identify areas for enhancement.
Encouraging a culture of continuous improvement drives innovation and sustains operational excellence.
Risk Management
Proactively identifying and mitigating risks associated with procurement processes is essential.
Develop contingency plans to address potential disruptions, such as supplier failures, technological issues, or market fluctuations.
Effective risk management ensures resilience and maintains the smooth operation of manufacturing processes.
Leveraging Technology
Utilizing procurement software and tools enhances the efficiency and accuracy of purchasing activities.
Automation of routine tasks frees up resources for strategic initiatives and decision-making.
Technology integration supports data-driven insights, improving the overall effectiveness of procurement strategies.
Case Studies: Successful Implementation of Innovative Picking Systems
Case Study 1: Toyota’s Automated Warehousing
Toyota implemented an automated picking system in its warehousing operations to enhance efficiency and reduce errors.
The system utilizes robotics and AI to manage inventory and streamline the picking process.
As a result, Toyota achieved significant improvements in production speed and accuracy, reinforcing its position as a leader in automotive manufacturing.
Case Study 2: Sony’s Smart Manufacturing
Sony adopted smart picking systems integrated with IoT devices to optimize its manufacturing processes.
The system provides real-time data on inventory levels and production status, allowing for dynamic adjustments.
This innovation led to increased flexibility, reduced downtime, and enhanced product quality across Sony’s manufacturing facilities.
Case Study 3: Panasonic’s Lean Manufacturing
Panasonic integrated innovative picking systems into its lean manufacturing strategy to minimize waste and maximize efficiency.
The automated system supports Just-In-Time (JIT) production by ensuring timely and accurate component delivery.
This integration resulted in streamlined operations, lower inventory costs, and improved overall productivity.
Future Trends in Picking Systems and Japanese Manufacturing
Integration of Artificial Intelligence
The future of picking systems will see deeper integration of artificial intelligence, enabling more intelligent and adaptive operations.
AI-driven systems can predict demand patterns, optimize picking routes, and enhance decision-making processes.
This advancement will further increase efficiency and reduce operational costs.
IoT and Connectivity
The Internet of Things (IoT) will play a crucial role in the evolution of picking systems, providing seamless connectivity between devices and systems.
Enhanced connectivity facilitates real-time data exchange, enabling more synchronized and responsive manufacturing operations.
IoT integration will lead to smarter factories with improved automation and data-driven insights.
Advanced Robotics
Robotics technology will continue to advance, offering more sophisticated and capable picking systems.
Collaborative robots (cobots) will work alongside human operators, enhancing productivity and safety.
The development of more versatile and intelligent robots will expand the applications of picking systems across various manufacturing sectors.
Sustainability and Green Manufacturing
Sustainability will become a key focus in the development of picking systems, aligning with global environmental goals.
Innovative systems will incorporate energy-efficient technologies and sustainable materials, reducing their environmental impact.
Green manufacturing practices will not only benefit the environment but also enhance the brand reputation and meet consumer expectations.
Customization and Personalization
As consumer demands become more personalized, picking systems will need to adapt to handle customized orders efficiently.
Flexible and modular picking systems will enable manufacturers to cater to individual preferences without compromising on speed or accuracy.
This trend towards customization will drive the need for more adaptable and responsive picking technologies.
Conclusion
The rise of innovative picking systems is transforming Japanese manufacturing, driving significant improvements in efficiency, accuracy, and cost-effectiveness.
While the adoption of these advanced technologies presents challenges such as high initial investments and technical complexities, the long-term benefits far outweigh the drawbacks.
By implementing best practices in procurement and purchasing, fostering strong supplier relationships, and staying abreast of market trends, manufacturers can successfully navigate the transition to modern picking systems.
As technology continues to evolve, the integration of AI, IoT, and advanced robotics will further revolutionize the manufacturing landscape, ensuring that Japanese manufacturers remain at the forefront of global innovation and competitiveness.
資料ダウンロード
QCD管理受発注クラウド「newji」は、受発注部門で必要なQCD管理全てを備えた、現場特化型兼クラウド型の今世紀最高の受発注管理システムとなります。
ユーザー登録
受発注業務の効率化だけでなく、システムを導入することで、コスト削減や製品・資材のステータス可視化のほか、属人化していた受発注情報の共有化による内部不正防止や統制にも役立ちます。
NEWJI DX
製造業に特化したデジタルトランスフォーメーション(DX)の実現を目指す請負開発型のコンサルティングサービスです。AI、iPaaS、および先端の技術を駆使して、製造プロセスの効率化、業務効率化、チームワーク強化、コスト削減、品質向上を実現します。このサービスは、製造業の課題を深く理解し、それに対する最適なデジタルソリューションを提供することで、企業が持続的な成長とイノベーションを達成できるようサポートします。
製造業ニュース解説
製造業、主に購買・調達部門にお勤めの方々に向けた情報を配信しております。
新任の方やベテランの方、管理職を対象とした幅広いコンテンツをご用意しております。
お問い合わせ
コストダウンが利益に直結する術だと理解していても、なかなか前に進めることができない状況。そんな時は、newjiのコストダウン自動化機能で大きく利益貢献しよう!
(β版非公開)