- お役立ち記事
- Revolutionizing Japanese Manufacturing: The Rise of SOI (Silicon-on-Insulator) Technology
月間76,176名の
製造業ご担当者様が閲覧しています*
*2025年3月31日現在のGoogle Analyticsのデータより
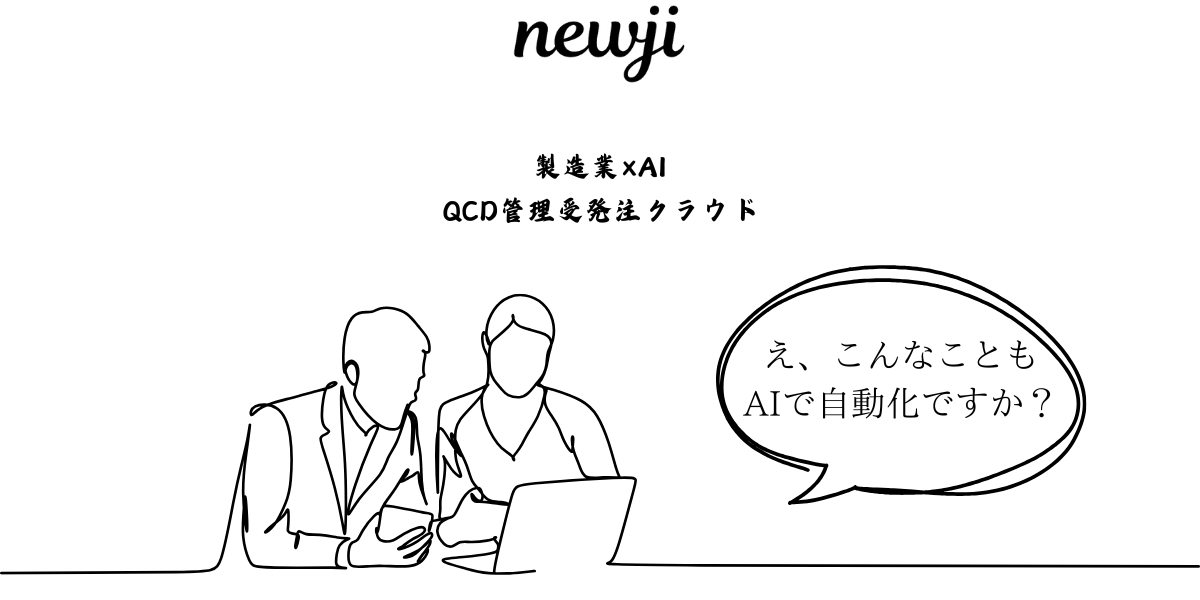
Revolutionizing Japanese Manufacturing: The Rise of SOI (Silicon-on-Insulator) Technology
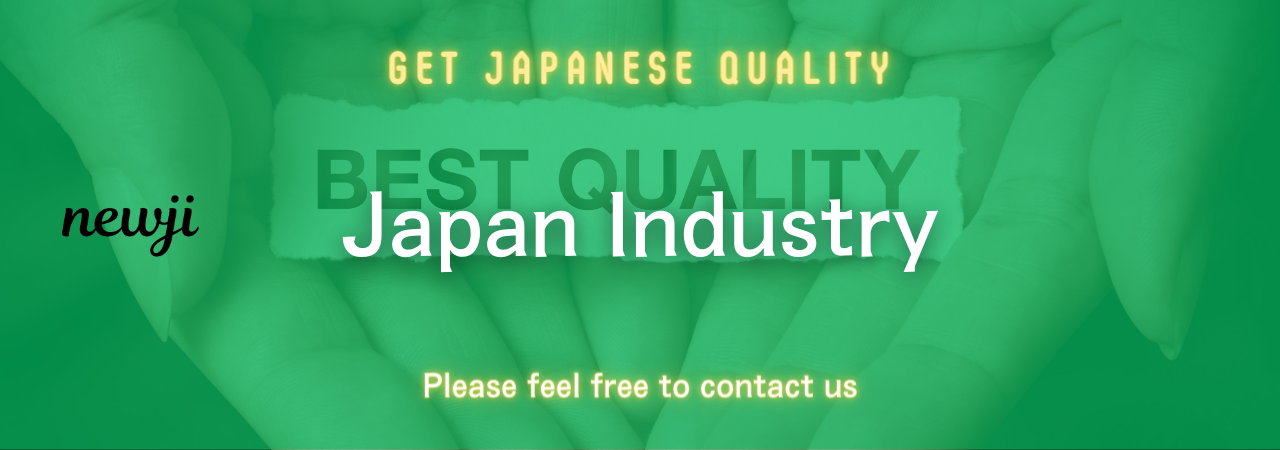
目次
Introduction to SOI Technology in Japanese Manufacturing
Japan has long been a leader in the manufacturing sector, renowned for its precision, quality, and innovative technologies. One such advancement revolutionizing the landscape is SOI, or Silicon-on-Insulator, technology. This cutting-edge approach is transforming semiconductor manufacturing, offering enhanced performance, reduced power consumption, and increased reliability. For procurement and purchasing professionals, understanding SOI technology’s implications is crucial for strategic sourcing, supplier negotiations, and maintaining a competitive edge in the global market.
The Fundamentals of SOI Technology
What is Silicon-on-Insulator (SOI) Technology?
Silicon-on-Insulator (SOI) technology involves layering a thin layer of silicon over an insulating substrate, typically silicon dioxide. This structure reduces parasitic device capacitance, enhancing speed and reducing power consumption in semiconductor devices. By isolating the active silicon layer from the bulk substrate, SOI technology minimizes leakage currents, leading to more efficient and reliable electronic components.
Evolution of SOI in Japanese Manufacturing
Japan’s commitment to innovation has propelled SOI technology from a niche application to a mainstream manufacturing process. Japanese semiconductor companies have invested heavily in research and development, refining SOI techniques to meet the demands of high-performance computing, mobile devices, and automotive electronics. This evolution reflects Japan’s broader strategy to maintain its technological supremacy in the global market.
Advantages of SOI Technology in Manufacturing
Enhanced Performance and Efficiency
SOI technology significantly boosts semiconductor performance by reducing parasitic capacitance. This allows for faster switching speeds and lower power consumption, which are critical for modern electronics that demand high efficiency and performance.
Improved Thermal Management
The insulating layer in SOI structures helps manage heat more effectively, preventing overheating and extending the lifespan of electronic components. This is particularly beneficial for applications in automotive and industrial sectors where reliability is paramount.
Reduced Leakage Currents
By isolating the silicon layer from the substrate, SOI technology minimizes leakage currents, leading to lower power usage and greater energy efficiency. This is essential for battery-powered devices and large-scale data centers looking to reduce energy costs.
Challenges and Disadvantages of SOI Technology
Higher Production Costs
Implementing SOI technology can be more costly compared to traditional bulk silicon processes. The additional materials and complex manufacturing steps contribute to increased production expenses, which may be a barrier for some manufacturers.
Technical Complexity
The fabrication of SOI wafers requires precise control and advanced equipment, making the process technically challenging. Manufacturers must invest in specialized machinery and skilled personnel to manage the complexities of SOI production.
Supply Chain Considerations
Sourcing high-quality insulators and maintaining a reliable supply chain for SOI materials can be difficult. Fluctuations in the availability of key components may impact production schedules and overall efficiency.
Procurement and Purchasing Strategies for SOI Technology
Identifying Reliable Suppliers
Establishing strong relationships with reputable SOI technology suppliers is essential. Procurement professionals should conduct thorough due diligence, evaluating suppliers based on their technical capabilities, quality standards, and track record in delivering high-performance SOI products.
Negotiating Favorable Terms
Effective negotiation strategies can help secure better pricing, favorable payment terms, and reliable delivery schedules. Understanding the supplier’s cost structure and market conditions can provide leverage during negotiations, ensuring mutually beneficial agreements.
Quality Assurance and Standards Compliance
Ensuring that suppliers adhere to stringent quality standards is crucial. Implementing comprehensive quality assurance processes and requiring compliance with international standards can mitigate risks associated with defective or subpar SOI components.
Market Conditions and Trends in SOI Technology
Growing Demand for High-Performance Electronics
The increasing demand for high-performance and energy-efficient electronics drives the adoption of SOI technology. Sectors such as automotive, telecommunications, and consumer electronics are key drivers, pushing manufacturers to integrate SOI solutions to meet market expectations.
Advancements in SOI Manufacturing Processes
Ongoing advancements in SOI manufacturing, including the development of advanced wafer bonding techniques and integration with other semiconductor technologies, are expanding the applications and benefits of SOI. Staying abreast of these innovations is essential for procurement professionals to leverage the latest efficiencies and capabilities.
Competitive Landscape
Japan’s semiconductor industry is highly competitive, with major players continuously investing in SOI technology to maintain their market position. Understanding the competitive dynamics and strategic initiatives of key manufacturers can inform procurement strategies and supplier selection.
Best Practices for Procuring SOI Technology
Strategic Sourcing
Adopting strategic sourcing practices ensures that procurement decisions align with the company’s long-term goals. This involves analyzing the total cost of ownership, assessing supplier reliability, and considering the technological roadmap of SOI advancements.
Building Collaborative Relationships
Fostering collaborative relationships with suppliers can lead to innovation and continuous improvement. Engaging in joint development projects and sharing market insights can enhance product offerings and streamline the supply chain.
Risk Management
Implementing robust risk management strategies is vital to mitigate potential disruptions in the supply chain. This includes diversifying suppliers, maintaining safety stocks, and developing contingency plans to address unforeseen challenges.
Supplier Negotiation Techniques for SOI Technology
Understanding Supplier Motivations
Gaining insights into what drives suppliers can enhance negotiation outcomes. Understanding their cost structures, profit margins, and strategic priorities allows procurement professionals to tailor their negotiation approaches effectively.
Leveraging Market Intelligence
Utilizing market intelligence data provides a competitive edge during negotiations. Knowledge of market prices, demand trends, and technological advancements enables informed decision-making and better negotiation leverage.
Creating Win-Win Scenarios
Focusing on creating mutually beneficial agreements fosters long-term partnerships. Negotiating terms that provide value to both parties, such as volume discounts or shared investment in technology development, enhances collaboration and sustainability.
Implementing SOI Technology: Best Practices
Integrating SOI into Existing Manufacturing Processes
Seamlessly integrating SOI technology into current manufacturing workflows requires careful planning and coordination. Assessing the compatibility of existing equipment, training personnel, and optimizing process parameters are critical steps to ensure a smooth transition.
Continuous Improvement and Innovation
Adopting a mindset of continuous improvement encourages ongoing optimization of SOI processes. Regularly reviewing performance metrics, soliciting feedback from stakeholders, and staying updated with technological advancements can drive sustained enhancements in manufacturing efficiency and product quality.
Sustainability and Environmental Considerations
Incorporating sustainability practices into SOI manufacturing aligns with global environmental standards. Minimizing waste, reducing energy consumption, and utilizing eco-friendly materials not only benefit the environment but also enhance the company’s reputation and compliance with regulatory requirements.
Case Studies: Successful Implementation of SOI Technology in Japan
Case Study 1: Automotive Electronics Enhancement
A leading Japanese automotive manufacturer integrated SOI technology to develop more efficient and reliable electronic control units (ECUs). The adoption of SOI allowed for better thermal management and reduced power consumption, resulting in enhanced vehicle performance and lower energy usage.
Case Study 2: Consumer Electronics Innovation
A top-tier Japanese semiconductor company leveraged SOI technology to produce high-speed processors for smartphones and tablets. The improved performance and energy efficiency provided by SOI chips contributed to the development of sleek, long-lasting devices that gained significant market share.
Future Outlook for SOI Technology in Japanese Manufacturing
As technology continues to evolve, the role of SOI in Japanese manufacturing is expected to grow. Innovations such as 3D integration, advanced lithography techniques, and integration with emerging technologies like artificial intelligence and the Internet of Things will further expand the applications and benefits of SOI. For procurement and purchasing professionals, staying informed about these trends and proactively adapting sourcing strategies will be essential to capitalize on the opportunities presented by SOI technology.
Conclusion
SOI technology represents a significant advancement in semiconductor manufacturing, offering numerous benefits that enhance performance, efficiency, and reliability. Japan’s leadership in this field is a testament to its commitment to innovation and quality. For professionals in procurement and purchasing, understanding the intricacies of SOI technology is vital for strategic sourcing, effective supplier negotiations, and maintaining a competitive advantage in the global market. By embracing best practices, fostering collaborative relationships, and staying abreast of industry trends, manufacturing companies can fully leverage the potential of SOI technology to drive growth and success.
資料ダウンロード
QCD管理受発注クラウド「newji」は、受発注部門で必要なQCD管理全てを備えた、現場特化型兼クラウド型の今世紀最高の受発注管理システムとなります。
ユーザー登録
受発注業務の効率化だけでなく、システムを導入することで、コスト削減や製品・資材のステータス可視化のほか、属人化していた受発注情報の共有化による内部不正防止や統制にも役立ちます。
NEWJI DX
製造業に特化したデジタルトランスフォーメーション(DX)の実現を目指す請負開発型のコンサルティングサービスです。AI、iPaaS、および先端の技術を駆使して、製造プロセスの効率化、業務効率化、チームワーク強化、コスト削減、品質向上を実現します。このサービスは、製造業の課題を深く理解し、それに対する最適なデジタルソリューションを提供することで、企業が持続的な成長とイノベーションを達成できるようサポートします。
製造業ニュース解説
製造業、主に購買・調達部門にお勤めの方々に向けた情報を配信しております。
新任の方やベテランの方、管理職を対象とした幅広いコンテンツをご用意しております。
お問い合わせ
コストダウンが利益に直結する術だと理解していても、なかなか前に進めることができない状況。そんな時は、newjiのコストダウン自動化機能で大きく利益貢献しよう!
(β版非公開)