- お役立ち記事
- Revolutionizing Japanese Manufacturing: The Rise of the Screw Tightening Robot
月間76,176名の
製造業ご担当者様が閲覧しています*
*2025年3月31日現在のGoogle Analyticsのデータより
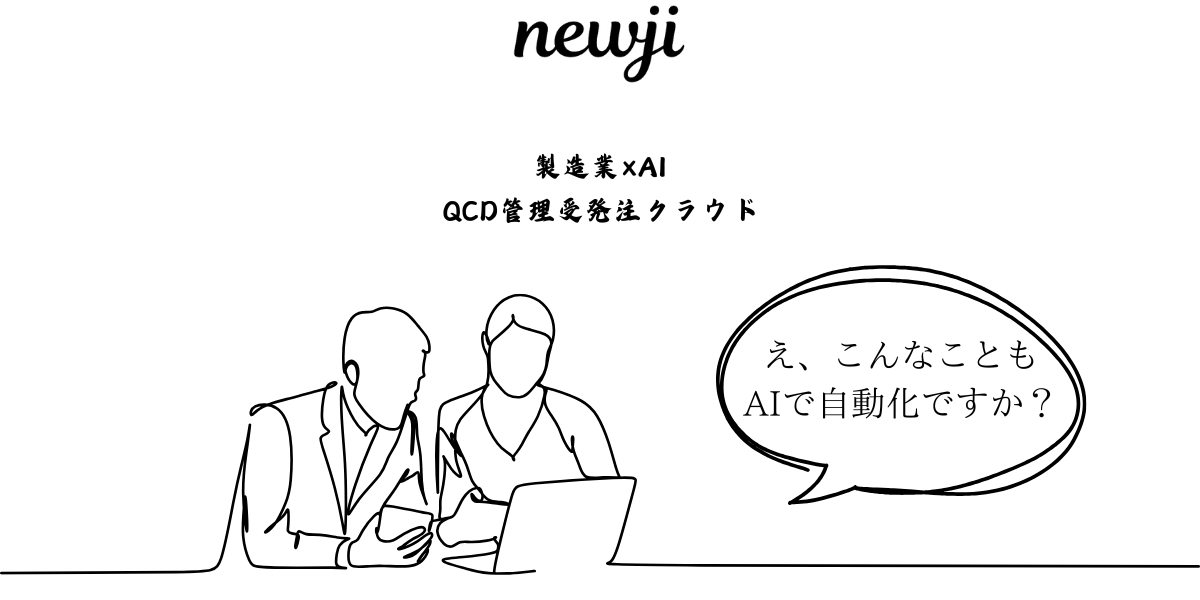
Revolutionizing Japanese Manufacturing: The Rise of the Screw Tightening Robot
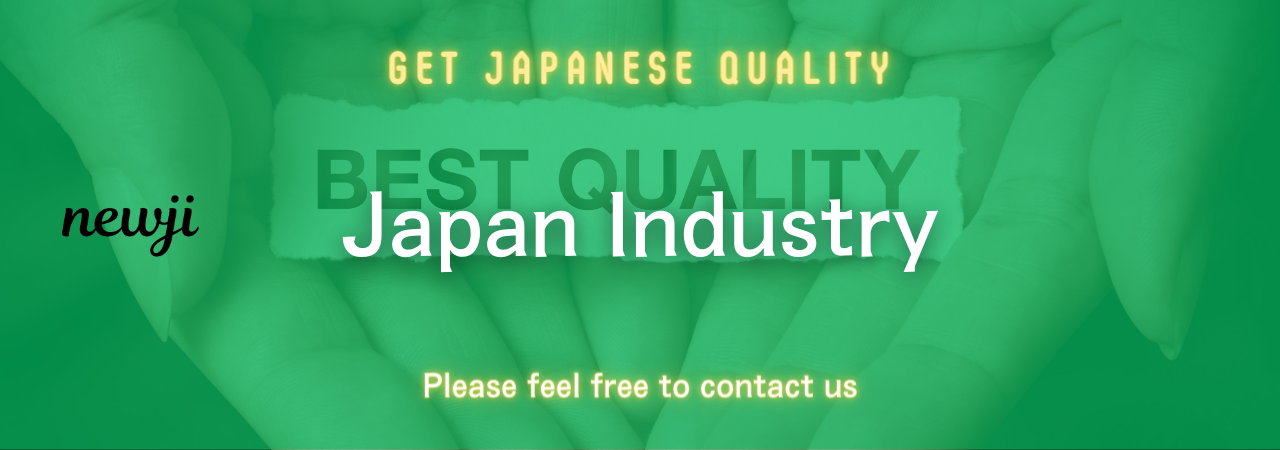
目次
Introduction to the Screw Tightening Robot Revolution
The manufacturing industry in Japan has long been recognized for its precision and efficiency.
Recent advancements have introduced the screw tightening robot, a technology set to transform production lines.
This innovation promises to enhance quality control, streamline procurement processes, and optimize overall factory operations.
Advantages of Implementing Screw Tightening Robots
Enhanced Precision and Consistency
Screw tightening robots ensure that each screw is fastened with exact torque specifications.
This reduces human error and increases the uniformity of products.
Consistent screw tightening leads to higher product reliability and customer satisfaction.
Increased Production Efficiency
Automating the screw tightening process accelerates assembly times.
Robots can operate continuously without fatigue, significantly boosting production rates.
This efficiency gain allows manufacturers to meet higher demand without compromising quality.
Cost Reduction
While the initial investment in robotics may be significant, long-term savings are substantial.
Robots reduce labor costs and minimize waste caused by incorrect screw tightening.
Additionally, preventive maintenance of robots can extend machinery lifespan, further lowering costs.
Improved Worker Safety
Automating repetitive and strenuous tasks such as screw tightening minimizes the risk of workplace injuries.
This allows human workers to focus on more complex and value-added activities.
A safer work environment contributes to higher employee morale and reduced absenteeism.
Data Integration and Analytics
Modern screw tightening robots are equipped with sensors and connectivity features.
They can collect and transmit data on performance metrics and operational efficiency.
This data can be analyzed to identify trends, predict maintenance needs, and inform strategic decisions.
Challenges and Disadvantages
High Initial Investment
Implementing robotic systems requires significant capital expenditure.
Small and medium-sized enterprises may find it challenging to allocate resources for such investments.
However, financing options and long-term cost savings can mitigate this barrier.
Technical Complexity
Integrating robots into existing production lines demands technical expertise.
Manufacturers must invest in training and possibly hire specialized personnel.
Ongoing maintenance and troubleshooting can also present challenges.
Potential Job Displacement
Automation may lead to concerns about job losses.
Manufacturers must balance automation with workforce development to ensure employees can transition to other roles.
Investing in employee training programs can alleviate these concerns and promote a harmonious work environment.
Dependence on Suppliers
Relying on robotic solutions from specific suppliers can create dependencies.
Manufacturers must carefully select reliable partners and consider backup options to mitigate risks associated with supplier failures or delays.
Supplier Negotiation Techniques
Understanding Supplier Capabilities
Before entering negotiations, thoroughly assess the supplier’s technical expertise and production capacity.
This ensures that the supplier can meet your quality and quantity requirements.
Building Strong Relationships
Cultivating a collaborative relationship with suppliers can lead to more favorable terms.
Open communication and mutual trust are essential for long-term partnerships.
Leveraging Volume for Better Pricing
Negotiating bulk purchasing agreements can secure discounts and better pricing structures.
Commitments to larger orders can provide suppliers with the confidence to offer competitive rates.
Ensuring Flexibility in Contracts
Incorporate clauses that allow for adjustments based on changing needs or market conditions.
Flexibility can help navigate unforeseen challenges without significant disruptions.
Evaluating Total Cost of Ownership
Consider all costs associated with procurement, including shipping, installation, and maintenance.
A comprehensive understanding of the total cost will lead to more informed negotiation outcomes.
Market Conditions Affecting Screw Tightening Robots
Technological Advancements
Rapid advancements in robotics and automation technology continuously reshape the market.
Staying abreast of these changes is crucial for maintaining a competitive edge.
Global Supply Chain Dynamics
Global events, such as pandemics or geopolitical tensions, can impact the availability and cost of robotic components.
Manufacturers must develop resilient supply chains to mitigate these risks.
Economic Factors
Economic growth influences investment in manufacturing technologies.
During periods of economic expansion, demand for automation solutions like screw tightening robots increases.
Regulatory Environment
Compliance with local and international regulations is essential when implementing robotic systems.
Manufacturers must ensure that their operations adhere to safety and environmental standards.
Competitive Landscape
The increasing adoption of robotics by competitors necessitates timely investment in similar technologies.
Failure to innovate can result in loss of market share and diminished competitive positioning.
Best Practices for Successful Implementation
Comprehensive Needs Assessment
Conduct a thorough analysis of your current manufacturing processes to identify areas where robotics can add value.
This helps in selecting the appropriate robotic solutions that align with your operational goals.
Strategic Planning and Integration
Develop a clear implementation plan that outlines timelines, resource allocation, and integration steps.
Ensure that robotics integration complements existing workflows and systems.
Employee Training and Development
Invest in training programs to equip employees with the necessary skills to operate and maintain robotic systems.
Empowering your workforce enhances overall productivity and reduces the learning curve associated with new technologies.
Continuous Monitoring and Optimization
Regularly monitor the performance of screw tightening robots to identify areas for improvement.
Use data analytics to optimize operations and ensure that the robots are functioning at peak efficiency.
Collaborative Supplier Partnerships
Work closely with suppliers to ensure seamless integration and support throughout the implementation process.
Collaborative partnerships can lead to customized solutions tailored to your specific manufacturing needs.
Case Studies: Success Stories in Japanese Manufacturing
Automotive Industry Transformation
Japanese automotive manufacturers have successfully integrated screw tightening robots into their assembly lines.
This has resulted in significant improvements in production speed and product quality, reinforcing Japan’s position as a leader in the global automotive market.
Electronics Manufacturing Excellence
Electronics companies in Japan have adopted screw tightening robots to enhance the precision of component assembly.
The automation of screw tightening has reduced defects and increased the reliability of electronic devices, contributing to higher consumer trust and brand reputation.
Consumer Goods Production
Manufacturers of consumer goods have leveraged screw tightening robots to accommodate high variability in product designs.
The flexibility of robotic systems allows for rapid adjustments, enabling manufacturers to meet diverse consumer demands efficiently.
Future Trends in Screw Tightening Robotics
Artificial Intelligence Integration
The incorporation of AI into screw tightening robots will enable smarter decision-making and predictive maintenance.
AI-driven robots can adapt to changing production environments and optimize operations in real-time.
Collaborative Robotics (Cobots)
Cobots designed to work alongside human workers will become more prevalent.
These robots enhance human capabilities and foster a more interactive and adaptive manufacturing environment.
Enhanced Connectivity and IoT
The integration of Internet of Things (IoT) technologies will enable greater connectivity between robots and other manufacturing systems.
This connectivity facilitates seamless data exchange and enhances overall operational efficiency.
Customization and Flexibility
Future screw tightening robots will offer greater customization options to cater to specific industry needs.
Flexible robots can handle a wider range of tasks, making them more versatile and valuable in diverse manufacturing settings.
Energy Efficiency Improvements
Advancements in energy-efficient technologies will reduce the power consumption of screw tightening robots.
This contributes to more sustainable manufacturing practices and lowers operational costs.
Strategies for Maximizing ROI
Optimal Resource Allocation
Ensure that investments in screw tightening robots are strategically allocated to areas with the highest potential return.
Prioritize critical processes where automation can deliver the most significant benefits.
Scalability and Future-Proofing
Select robotic solutions that can scale with your business growth and adapt to evolving manufacturing requirements.
Future-proofing your investment ensures long-term viability and maximizes ROI.
Performance Benchmarking
Establish clear performance metrics to evaluate the effectiveness of screw tightening robots.
Regular benchmarking against industry standards helps in identifying areas for improvement and measuring ROI accurately.
Maintenance and Support Plans
Implement proactive maintenance schedules to prevent downtime and extend the lifespan of robotic systems.
Reliable support from suppliers ensures that any issues are promptly addressed, safeguarding your investment.
Continuous Improvement Culture
Foster a culture of continuous improvement where feedback and innovation are encouraged.
Engaging employees in the optimization process enhances the effectiveness of robotic solutions and drives sustained ROI.
Conclusion
The rise of screw tightening robots is revolutionizing Japanese manufacturing, offering numerous advantages such as enhanced precision, increased efficiency, and cost reduction.
However, challenges such as high initial investment and technical complexity must be addressed through strategic planning and robust supplier partnerships.
By leveraging best practices and staying attuned to market trends, manufacturers can successfully implement robotic solutions and achieve significant operational improvements.
The future of manufacturing lies in the seamless integration of advanced robotics, positioning Japan at the forefront of industrial innovation.
資料ダウンロード
QCD管理受発注クラウド「newji」は、受発注部門で必要なQCD管理全てを備えた、現場特化型兼クラウド型の今世紀最高の受発注管理システムとなります。
ユーザー登録
受発注業務の効率化だけでなく、システムを導入することで、コスト削減や製品・資材のステータス可視化のほか、属人化していた受発注情報の共有化による内部不正防止や統制にも役立ちます。
NEWJI DX
製造業に特化したデジタルトランスフォーメーション(DX)の実現を目指す請負開発型のコンサルティングサービスです。AI、iPaaS、および先端の技術を駆使して、製造プロセスの効率化、業務効率化、チームワーク強化、コスト削減、品質向上を実現します。このサービスは、製造業の課題を深く理解し、それに対する最適なデジタルソリューションを提供することで、企業が持続的な成長とイノベーションを達成できるようサポートします。
製造業ニュース解説
製造業、主に購買・調達部門にお勤めの方々に向けた情報を配信しております。
新任の方やベテランの方、管理職を対象とした幅広いコンテンツをご用意しております。
お問い合わせ
コストダウンが利益に直結する術だと理解していても、なかなか前に進めることができない状況。そんな時は、newjiのコストダウン自動化機能で大きく利益貢献しよう!
(β版非公開)