- お役立ち記事
- Revolutionizing Japanese Manufacturing: The Rise of Transport and Delivery Robots
Revolutionizing Japanese Manufacturing: The Rise of Transport and Delivery Robots
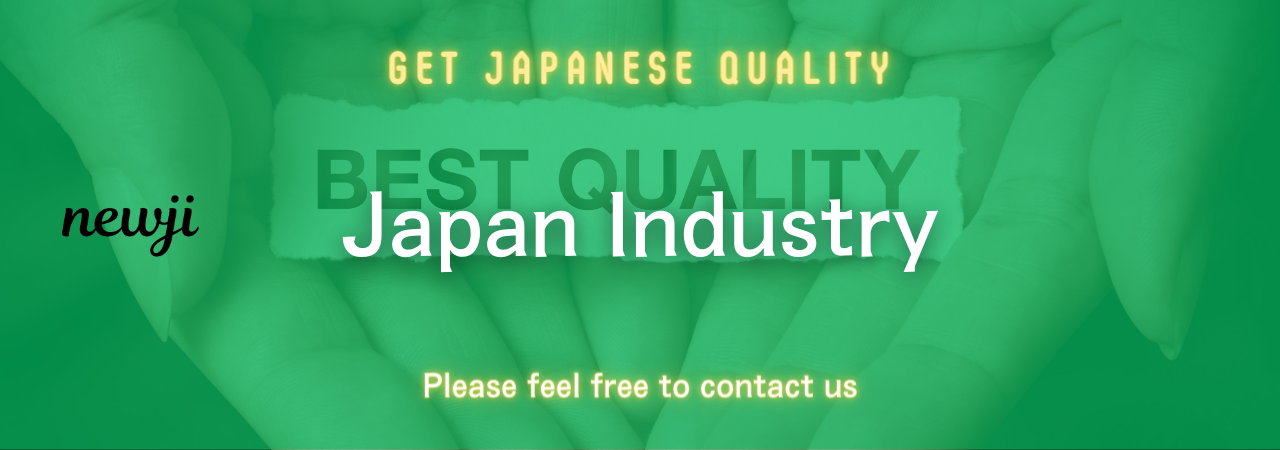
目次
Introduction
The manufacturing industry in Japan has long been admired for its efficiency, precision, and dedication to quality.
As global demands evolve and technology advances, the sector continues to innovate, embracing new tools and methods to maintain its competitive edge.
One of the most transformative trends in recent years is the integration of transport and delivery robots into manufacturing processes.
This article explores the profound impact of these robots, examining their advantages, challenges, and best practices for integrating them into production environments.
The Role of Transport and Delivery Robots in Japanese Manufacturing
The Evolution of Robotics in Manufacturing
Japan has been a pioneer in the development and implementation of robotics within the manufacturing sector.
From the early days of industrial robots that focused on repetitive tasks, we have now transitioned to a new era where robots are capable of much more versatile functions.
Transport and delivery robots are among these innovations, designed to move materials and finished products throughout manufacturing plants with minimal human intervention.
Advantages of Transport and Delivery Robots
Increased Efficiency
One of the primary benefits of integrating transport and delivery robots in manufacturing is the significant boost in efficiency.
These robots can operate 24/7, ensuring a continuous flow of materials and products without the need for breaks.
Reduced human involvement in transport tasks also minimizes errors and delays, facilitating a more streamlined production process.
Labor Cost Reduction
Deploying robots for transport tasks can lead to considerable savings in labor costs.
Where previously a significant portion of the workforce was dedicated to moving materials around the factory, robots can now take over these tasks, allowing employees to focus on more complex and value-added activities.
Improved Safety
Manufacturing environments often present safety hazards, particularly in areas where heavy loads are transported.
Robots can navigate these environments safely, reducing the risk of accidents and injuries.
This not only improves overall workplace safety but also minimizes downtime and associated costs from workplace incidents.
Consistency and Precision
Robots provide consistent performance, ensuring materials are delivered on time and to the correct locations.
This precision reduces the likelihood of production delays and ensures that manufacturing processes are not interrupted by misdeliveries or errors in material handling.
Challenges in Implementing Transport and Delivery Robots
High Initial Investment
One of the primary obstacles manufacturers face is the high initial cost of acquiring and implementing robotic systems.
This includes the cost of robots themselves, integration into existing systems, and the necessary training for personnel.
While the long-term savings and efficiency gains can justify the investment, the upfront costs can be daunting for some businesses.
Technological Integration
Integrating new robotic systems with existing technology can be complex.
This process often requires an overhaul of current logistics and production management systems to ensure that robots can communicate seamlessly with other machinery and software.
Ensuring compatibility and smooth operation can be challenging and time-consuming.
Maintenance and Upkeep
Robots, like any other machinery, require regular maintenance to operate effectively.
This adds an additional layer of complexity to factory operations.
Manufacturers must invest in training maintenance personnel or establish contracts with service providers to ensure robots remain in optimal condition, thus avoiding unexpected downtimes.
Dependence on Technology
A significant shift towards robotic transport systems increases a factory’s dependence on technology.
While this can lead to improved efficiency, it also means that any technological malfunction or failure can have more pronounced effects on the production process.
Having robust contingency plans and backup systems becomes essential.
Best Practices for Implementing Transport and Delivery Robots
Assessing Needs and Suitability
Before implementing transport and delivery robots, it is crucial to conduct a thorough assessment of your factory’s needs and suitability for robotic integration.
This involves analyzing current workflows, identifying bottlenecks, and understanding the specific requirements of your production process.
Not all factories will benefit equally from robotics, so a tailored approach is essential.
Pilot Programs
Starting with a pilot program can provide valuable insights into how robots will interact with existing processes and highlight any potential issues before a full-scale implementation.
This allows for adjustments and ensures that the transition to robotic systems is smooth and efficient.
Employee Training and Involvement
Successfully integrating robots into manufacturing processes requires the cooperation and involvement of the workforce.
Comprehensive training programs should be implemented to ensure employees are comfortable working alongside robots and understand how to manage and troubleshoot them.
Encouraging an inclusive approach where employees are involved in the implementation process can also reduce resistance to change.
Regular Review and Optimization
Once robots are implemented, continuous monitoring and regular reviews are essential.
This helps in identifying areas for further optimization and ensures that the robots are performing at their best.
Technological advancements are rapid, so staying updated with the latest developments can provide opportunities for further improvements.
Supplier Negotiation Techniques for Procuring Robots
Understanding Market Conditions
One of the first steps in the procurement process is to have a keen understanding of the current market conditions.
This involves researching the latest trends, technological advancements, and the competitive landscape of transport and delivery robots.
Being well-informed provides a strong foundation for negotiating with suppliers.
Leverage Volume for Better Deals
Larger orders often grant more bargaining power when dealing with suppliers.
If your company is looking to procure several robots or has plans to expand usage in the future, communicating this potential volume to suppliers can lead to more favorable terms and discounts.
Focus on Total Cost of Ownership
When negotiating with suppliers, it is crucial to consider the total cost of ownership (TCO) rather than just the initial purchase price.
TCO includes installation costs, maintenance, expected lifespan, and potential productivity gains or savings.
A robot with a higher upfront cost might have lower running costs and offer better long-term value.
Customization and Support Services
Each manufacturing environment has unique requirements, and off-the-shelf solutions may not always be ideal.
Engaging suppliers who are willing to customize their robots to meet specific needs can be highly beneficial.
Additionally, robust support services, including training, maintenance, and troubleshooting, should be a critical part of the negotiation focus.
Building Long-Term Partnerships
Developing long-term relationships with suppliers can provide ongoing benefits.
A partnership approach encourages suppliers to deliver high-quality products and services, knowing that they are working towards a sustainable business relationship.
This can also lead to better after-sales support and preferential treatment for future needs.
The Future of Transport and Delivery Robots in Japanese Manufacturing
Technological Advancements
The field of robotics is evolving swiftly, with continuous innovations expected to enhance the capabilities of transport and delivery robots.
Future developments may include improved artificial intelligence (AI) for better navigation and decision-making, enhanced energy efficiency, and integration with other cutting-edge technologies such as the Internet of Things (IoT) and 5G connectivity.
Expanding Applications
While transport and delivery have been the primary applications of these robots, future advancements may expand their roles within manufacturing environments.
This may include more complex material handling, assembly tasks, and even maintenance roles.
The versatility of robots is expected to increase, allowing them to undertake an even broader range of functions.
Impact on Workforce Dynamics
As robots become more integrated into manufacturing processes, the dynamics of the workforce will inevitably shift.
This may lead to a greater emphasis on technical skills, with a growing need for employees who can manage, program, and maintain robotic systems.
Continuous education and training will be essential to ensure the workforce remains adept at working alongside advanced automation.
Sustainability and Efficiency
Transport and delivery robots can contribute significantly to sustainability efforts within manufacturing.
Their precision and efficiency reduce wastage, and advancements in energy-efficient technologies will further reduce the environmental footprint of manufacturing operations.
This aligns with global trends towards more sustainable industrial practices.
Conclusion
Transport and delivery robots are revolutionizing Japanese manufacturing, offering immense benefits in efficiency, cost savings, safety, and precision.
While there are challenges, such as high initial costs and the complexity of integration, the long-term advantages make a compelling case for their adoption.
By following best practices, engaging in effective supplier negotiations, and staying current with technological advancements, manufacturers can successfully harness the power of these robots to remain competitive in an increasingly automated world.
As we look to the future, the potential for transport and delivery robots to further transform manufacturing is vast, promising an era of unprecedented efficiency and innovation.
資料ダウンロード
QCD調達購買管理クラウド「newji」は、調達購買部門で必要なQCD管理全てを備えた、現場特化型兼クラウド型の今世紀最高の購買管理システムとなります。
ユーザー登録
調達購買業務の効率化だけでなく、システムを導入することで、コスト削減や製品・資材のステータス可視化のほか、属人化していた購買情報の共有化による内部不正防止や統制にも役立ちます。
NEWJI DX
製造業に特化したデジタルトランスフォーメーション(DX)の実現を目指す請負開発型のコンサルティングサービスです。AI、iPaaS、および先端の技術を駆使して、製造プロセスの効率化、業務効率化、チームワーク強化、コスト削減、品質向上を実現します。このサービスは、製造業の課題を深く理解し、それに対する最適なデジタルソリューションを提供することで、企業が持続的な成長とイノベーションを達成できるようサポートします。
オンライン講座
製造業、主に購買・調達部門にお勤めの方々に向けた情報を配信しております。
新任の方やベテランの方、管理職を対象とした幅広いコンテンツをご用意しております。
お問い合わせ
コストダウンが利益に直結する術だと理解していても、なかなか前に進めることができない状況。そんな時は、newjiのコストダウン自動化機能で大きく利益貢献しよう!
(Β版非公開)