- お役立ち記事
- Revolutionizing Japanese Manufacturing: The Rise of Ultrasonic Welding Processing OEM Solutions
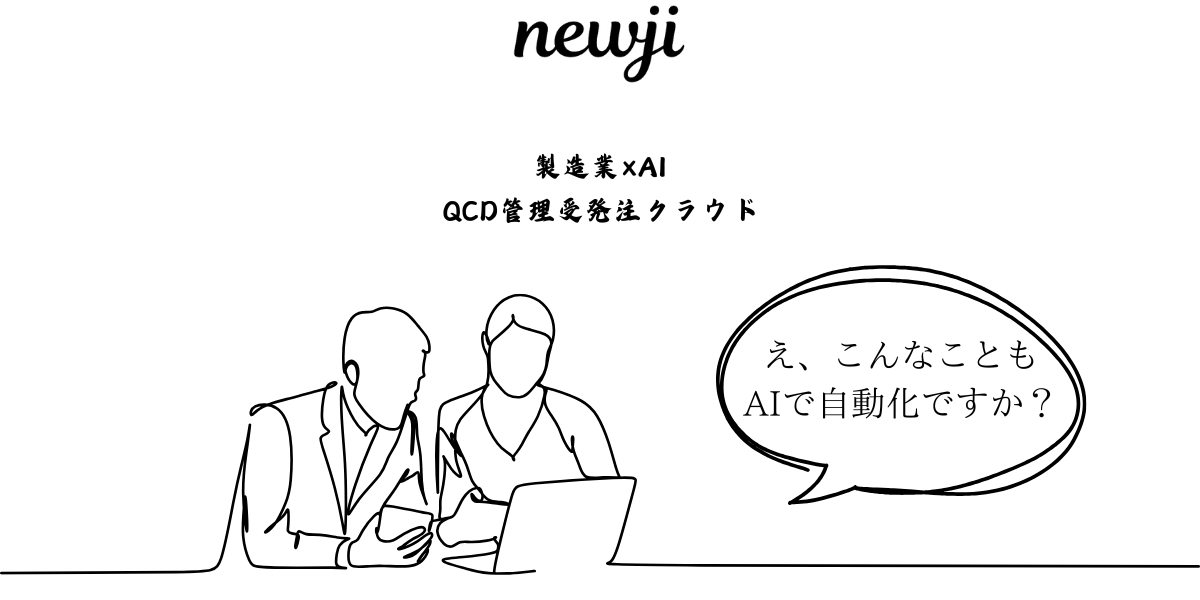
Revolutionizing Japanese Manufacturing: The Rise of Ultrasonic Welding Processing OEM Solutions
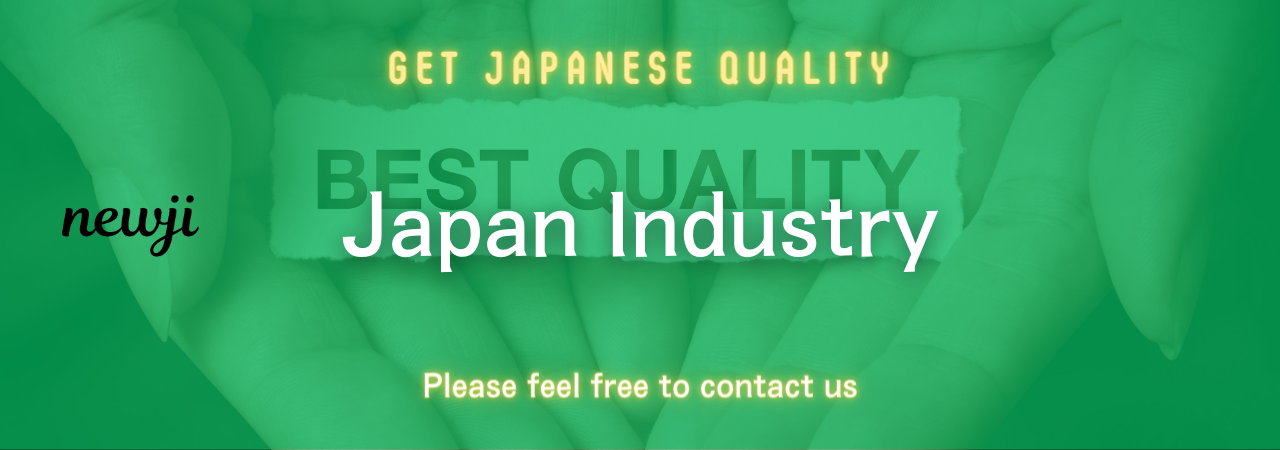
目次
Introduction to Ultrasonic Welding and Its Ascendancy in Japanese Manufacturing
Japanese manufacturing has long been synonymous with quality, precision, and efficiency.
As global competition intensifies, innovative techniques like ultrasonic welding are becoming indispensable in ensuring continued excellence.
Ultrasonic welding is a non-contact process utilizing high-frequency ultrasonic vibrations to weld materials, primarily plastics and metals.
This technique has gained traction due to its speed, reliability, and eco-friendliness.
Understanding Ultrasonic Welding: A Primer
What is Ultrasonic Welding?
Ultrasonic welding involves converting high-frequency electrical energy into mechanical vibrations, which generate localized heat through friction at the interface of the materials being joined.
This process enables strong and uniform bonds without requiring additional adhesives or fillers.
Advantages of Ultrasonic Welding
The benefits of ultrasonic welding are multifold:
– **Speed and Efficiency**: The process takes only a few seconds, significantly reducing production time.
– **Clean and Eco-Friendly**: As it doesn’t require adhesives or solvents, the process is environmentally friendly and eliminates contamination risks.
– **Strong and Durable Bonds**: Ultrasonic welding creates homogeneous joints, ensuring high strength and durability.
– **Versatility**: It is suitable for joining a wide range of materials, including hard-to-weld plastics and metals.
Applications in Japanese Manufacturing
Japanese industries have rapidly adopted ultrasonic welding across various sectors such as automotive, electronics, and medical devices.
Its precision and reliability align perfectly with the country’s stringent quality control standards.
From assembling intricate electronic components to fabricating complex automotive parts, ultrasonic welding is ingrained in Japan’s manufacturing processes.
Prospective Benefits of Utilizing Ultrasonic Welding OEM Solutions
Cost Reduction
Opting for Original Equipment Manufacturer (OEM) solutions in ultrasonic welding can lead to substantial cost savings.
By outsourcing this specialized process, manufacturers can avoid the significant capital investment required for purchasing and maintaining advanced welding equipment.
Access to Expertise
Japanese OEM providers bring decades of technical expertise to the table.
Their deep-rooted knowledge in material science and welding technologies ensures that clients receive top-notch services and end products that meet international standards.
Flexibility and Scalability
Working with subcontracted OEMs allows manufacturers to scale production up or down based on market demand without the logistical challenges of equipment reconfiguration or workforce retraining.
This flexibility can be crucial for staying competitive in a volatile market.
Quality Assurance
Japanese manufacturers are renowned for their rigorous quality control procedures.
OEM solutions extend this quality assurance to their clients, guaranteeing that every welded product meets exacting specifications and performance metrics.
Focus on Core Competencies
By outsourcing welding processes to specialized OEMs, companies can focus on their core competencies such as product design, marketing, and sales.
This concentrated focus can drive innovation and improve overall business performance.
Challenges of Implementing Ultrasonic Welding in Manufacturing
Initial Investment
The primary barrier is the high initial cost associated with setting up ultrasonic welding capabilities, including the purchase of high-frequency ultrasonic generators and precision welding tools.
However, partnering with OEMs can mitigate this cost.
Material Limitations
While ultrasonic welding is highly effective for specific materials, it may not be suitable for all types.
Materials with high thermal conductivity or those with certain composite structures might pose challenges.
Design Constraints
Parts and components need to be designed considering the specific requirements of ultrasonic welding.
This may necessitate changes in existing designs or limitations on new designs, which can be a considerable constraint.
Technical Proficiency
Ultrasonic welding requires highly skilled operators who understand the intricacies of the technology.
This can necessitate additional training and hiring specialized personnel.
Effective Supplier Negotiation Techniques
Clear Communication
Ensure there is a clear understanding of your requirements and expectations.
Regular updates and open communication channels can foster a cooperative environment.
Volume Leveraging
Buying in bulk often translates into cost savings.
Leverage large orders to negotiate better pricing and terms.
Quality and Performance Metrics
Set clear metrics for quality and performance to avoid any ambiguity.
These parameters should be mutually agreed upon and reviewed periodically.
Long-Term Partnerships
Cultivate long-term relationships with suppliers.
Establishing trust can lead to better terms, improved service, and collaborative innovation.
Analyzing Market Conditions and Trends
Growth of High-Performance Plastics
The demand for high-performance plastics in automotive and electronics industries is on the rise.
Ultrasonic welding is ideally suited to meet this growing demand due to its ability to create strong, durable bonds without degrading the material.
Increasing Focus on Sustainability
As industries put more emphasis on green manufacturing practices, ultrasonic welding’s eco-friendly nature is making it a preferred choice over traditional welding techniques.
Technological Advancements
Advancements in ultrasonic welding equipment, such as digital control systems and adaptive welding technologies, are enhancing precision and efficiency.
Staying updated with these trends is crucial for maintaining a competitive edge.
Trade Policies and Regulations
Changes in international trade policies and regulations can impact supply chains and costs.
Being aware of these changes and adjusting procurement strategies accordingly is essential.
Best Practices for Successful Implementation
Thorough Feasibility Studies
Conduct in-depth feasibility studies to determine the suitability of ultrasonic welding for your specific applications.
This includes material compatibility tests, design assessments, and cost-benefit analyses.
Collaborative Design Approaches
Work closely with your OEM partners in the design phase to ensure that parts are optimized for ultrasonic welding.
Collaboration can result in better designs and enhanced process efficiencies.
Robust Training Programs
Invest in training programs for your operators and engineers.
A well-trained workforce is critical to maximizing the benefits of ultrasonic welding.
Regular Maintenance and Upgrades
Ensure that welding equipment is regularly maintained and upgraded as per the latest technological advancements.
This will not only enhance performance but also increase the longevity of the equipment.
Quality Management Systems
Implement stringent quality management systems that include regular inspections, testing, and quality audits.
This will ensure consistent product quality and adherence to international standards.
Conclusion: The Future of Ultrasonic Welding in Japanese Manufacturing
The rise of ultrasonic welding processing OEM solutions is a testament to Japan’s unwavering commitment to innovation and quality in manufacturing.
As industries increasingly seek efficient, reliable, and eco-friendly welding solutions, the prominence of ultrasonic welding will continue to grow.
By leveraging the expertise, cost benefits, and flexibility offered by Japanese OEMs, companies worldwide can revolutionize their manufacturing processes and maintain a competitive edge.
Staying abreast of market trends, focusing on continuous improvement, and fostering collaborative partnerships with suppliers will be key to unlocking the full potential of ultrasonic welding.
Ultimately, embracing this advanced welding technology will not only enhance product quality and efficiency but also pave the way for sustainable, future-ready manufacturing practices.
資料ダウンロード
QCD調達購買管理クラウド「newji」は、調達購買部門で必要なQCD管理全てを備えた、現場特化型兼クラウド型の今世紀最高の購買管理システムとなります。
ユーザー登録
調達購買業務の効率化だけでなく、システムを導入することで、コスト削減や製品・資材のステータス可視化のほか、属人化していた購買情報の共有化による内部不正防止や統制にも役立ちます。
NEWJI DX
製造業に特化したデジタルトランスフォーメーション(DX)の実現を目指す請負開発型のコンサルティングサービスです。AI、iPaaS、および先端の技術を駆使して、製造プロセスの効率化、業務効率化、チームワーク強化、コスト削減、品質向上を実現します。このサービスは、製造業の課題を深く理解し、それに対する最適なデジタルソリューションを提供することで、企業が持続的な成長とイノベーションを達成できるようサポートします。
オンライン講座
製造業、主に購買・調達部門にお勤めの方々に向けた情報を配信しております。
新任の方やベテランの方、管理職を対象とした幅広いコンテンツをご用意しております。
お問い合わせ
コストダウンが利益に直結する術だと理解していても、なかなか前に進めることができない状況。そんな時は、newjiのコストダウン自動化機能で大きく利益貢献しよう!
(Β版非公開)