- お役立ち記事
- “Revolutionizing Japanese Manufacturing: The Rise of Wearable Motion Sensors”
月間77,185名の
製造業ご担当者様が閲覧しています*
*2025年2月28日現在のGoogle Analyticsのデータより
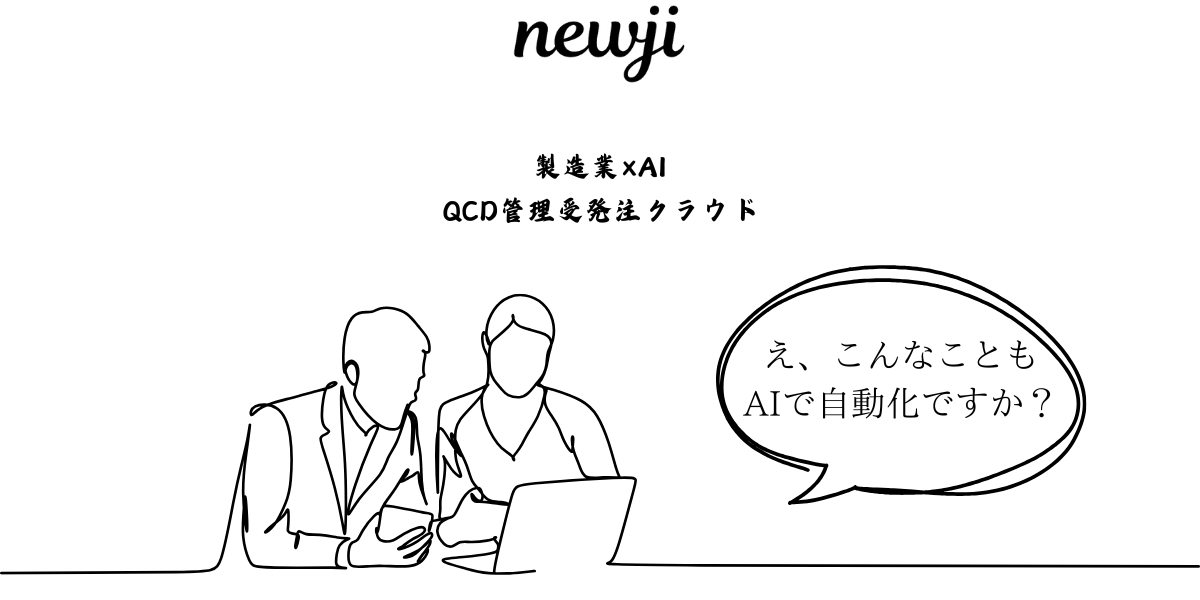
“Revolutionizing Japanese Manufacturing: The Rise of Wearable Motion Sensors”
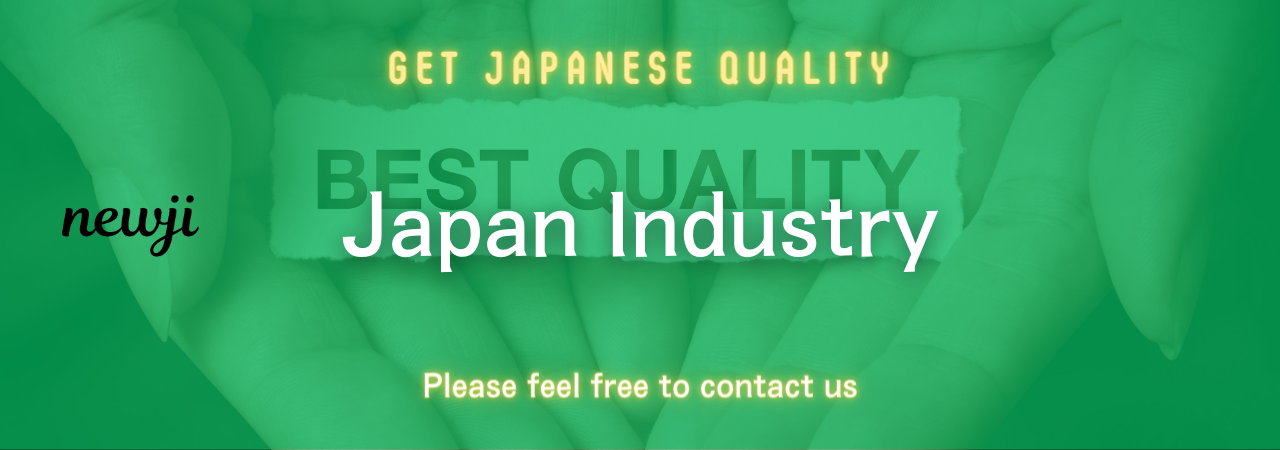
目次
Introduction
Japanese manufacturing has long been synonymous with precision, quality, and innovation. In recent years, the integration of wearable motion sensors has begun to revolutionize the industry, enhancing both productivity and worker safety. These advanced devices are transforming traditional manufacturing processes, offering new opportunities for efficiency and competitiveness on a global scale.
The Role of Wearable Motion Sensors in Modern Manufacturing
Wearable motion sensors are devices that track and analyze the movement of workers and machinery in real-time. By collecting data on various parameters such as speed, posture, and frequency of movements, these sensors provide valuable insights into operational efficiency and potential areas for improvement.
Enhancing Worker Safety
One of the primary benefits of wearable motion sensors is the enhancement of worker safety. By monitoring movements, these sensors can detect unsafe postures or repetitive motions that may lead to injuries. Alerts can be generated to prompt immediate corrective actions, thereby reducing the risk of accidents and promoting a safer working environment.
Improving Operational Efficiency
Wearable motion sensors contribute to operational efficiency by providing data that can be analyzed to streamline processes. For instance, by identifying bottlenecks in production lines or inefficient movements, manufacturers can make informed decisions to optimize workflows, reduce downtime, and increase overall productivity.
Advantages of Implementing Wearable Motion Sensors
The adoption of wearable motion sensors offers numerous advantages to Japanese manufacturing companies, contributing to their sustained global competitiveness.
Data-Driven Decision Making
With real-time data collection, manufacturers can make informed decisions based on accurate and timely information. This data-driven approach allows for precise adjustments to manufacturing processes, leading to improved product quality and reduced waste.
Enhanced Quality Control
Wearable sensors enable continuous monitoring of manufacturing processes, ensuring that products meet stringent quality standards. By detecting deviations early, manufacturers can implement corrective measures swiftly, maintaining consistency and reliability in their products.
Cost Reduction
By optimizing workflows and reducing inefficiencies, wearable motion sensors help in lowering operational costs. Additionally, preventing workplace injuries through improved safety measures can significantly reduce expenses related to medical treatments and lost workdays.
Disadvantages and Challenges
Despite the numerous benefits, the implementation of wearable motion sensors in manufacturing is not without challenges. Understanding these potential drawbacks is crucial for successful integration.
Initial Investment Costs
The deployment of wearable motion sensors requires a substantial initial investment in technology and infrastructure. Small to medium-sized enterprises may find it challenging to allocate the necessary funds, potentially slowing down adoption rates.
Data Privacy Concerns
The collection of data on worker movements raises privacy concerns. It is essential for companies to establish clear policies and ensure transparency in how the data is used to maintain trust and comply with privacy regulations.
Integration with Existing Systems
Integrating wearable motion sensors with existing manufacturing systems can be complex. Compatibility issues and the need for specialized personnel to manage and interpret the data may pose significant hurdles.
Supplier Negotiation Techniques for Wearable Motion Sensors
Effective negotiation with suppliers is critical to securing the best terms and ensuring the successful implementation of wearable motion sensors.
Understanding Supplier Capabilities
Before entering negotiations, it is essential to thoroughly understand the supplier’s capabilities, including their technology offerings, production capacity, and reliability. This knowledge helps in assessing whether a supplier can meet the specific needs of your manufacturing processes.
Leveraging Long-Term Partnerships
Building long-term relationships with suppliers can lead to more favorable terms and better support. Demonstrating a commitment to a lasting partnership can encourage suppliers to offer competitive pricing and prioritize your orders.
Negotiating for Customization
Manufacturing processes can be unique, and off-the-shelf solutions may not always suffice. Negotiating for customized wearable motion sensors that cater to specific operational requirements can enhance the effectiveness of the technology implementation.
Securing After-Sales Support
Ensuring robust after-sales support is crucial for the ongoing maintenance and optimization of wearable motion sensors. Negotiating terms that include comprehensive support services can help mitigate potential downtime and technical issues.
Market Conditions and Trends
Understanding the current market conditions and emerging trends is vital for manufacturers looking to adopt wearable motion sensors.
Increasing Demand for Automation
The global trend towards automation in manufacturing is driving the demand for advanced technologies like wearable motion sensors. As companies strive for higher efficiency and reduced human error, these sensors become integral components of automated systems.
Advancements in Sensor Technology
Continuous advancements in sensor technology are making wearable motion sensors more accurate, reliable, and cost-effective. Innovations such as improved battery life, wireless connectivity, and enhanced data analytics capabilities are expanding their applicability across various manufacturing sectors.
Focus on Sustainability
Sustainability is becoming a key focus for manufacturers. Wearable motion sensors contribute to sustainable practices by optimizing resource use, reducing waste, and improving energy efficiency, aligning with global sustainability goals.
Best Practices for Implementing Wearable Motion Sensors
To maximize the benefits of wearable motion sensors, manufacturers should adhere to best practices throughout the implementation process.
Comprehensive Needs Assessment
Conducting a thorough needs assessment helps in identifying the specific requirements and goals for integrating wearable motion sensors. This step ensures that the chosen technology aligns with the overall business objectives and operational needs.
Employee Training and Engagement
Educating employees about the benefits and proper use of wearable motion sensors is essential for successful adoption. Engaging workers in the implementation process fosters a positive attitude towards the technology and encourages active participation.
Data Management and Analysis
Effective data management practices are crucial for handling the large volumes of data generated by wearable motion sensors. Implementing robust data analysis tools and processes enables manufacturers to extract actionable insights and drive continuous improvement.
Regular Maintenance and Updates
Maintaining the wearable motion sensors through regular inspections and software updates ensures their optimal performance. Proactive maintenance helps in preventing technical issues and extending the lifespan of the devices.
Conclusion
The rise of wearable motion sensors represents a significant shift in Japanese manufacturing, offering enhanced safety, efficiency, and competitiveness. By understanding the advantages and addressing the challenges, manufacturers can effectively integrate this technology into their operations. Strategic supplier negotiations, awareness of market trends, and adherence to best practices are essential for leveraging the full potential of wearable motion sensors. As the manufacturing landscape continues to evolve, wearable motion sensors will undoubtedly play a pivotal role in shaping the future of the industry.
資料ダウンロード
QCD管理受発注クラウド「newji」は、受発注部門で必要なQCD管理全てを備えた、現場特化型兼クラウド型の今世紀最高の受発注管理システムとなります。
ユーザー登録
受発注業務の効率化だけでなく、システムを導入することで、コスト削減や製品・資材のステータス可視化のほか、属人化していた受発注情報の共有化による内部不正防止や統制にも役立ちます。
NEWJI DX
製造業に特化したデジタルトランスフォーメーション(DX)の実現を目指す請負開発型のコンサルティングサービスです。AI、iPaaS、および先端の技術を駆使して、製造プロセスの効率化、業務効率化、チームワーク強化、コスト削減、品質向上を実現します。このサービスは、製造業の課題を深く理解し、それに対する最適なデジタルソリューションを提供することで、企業が持続的な成長とイノベーションを達成できるようサポートします。
製造業ニュース解説
製造業、主に購買・調達部門にお勤めの方々に向けた情報を配信しております。
新任の方やベテランの方、管理職を対象とした幅広いコンテンツをご用意しております。
お問い合わせ
コストダウンが利益に直結する術だと理解していても、なかなか前に進めることができない状況。そんな時は、newjiのコストダウン自動化機能で大きく利益貢献しよう!
(β版非公開)