- お役立ち記事
- “Revolutionizing Japanese Manufacturing: The Role of Anodizing Processing OEMs”
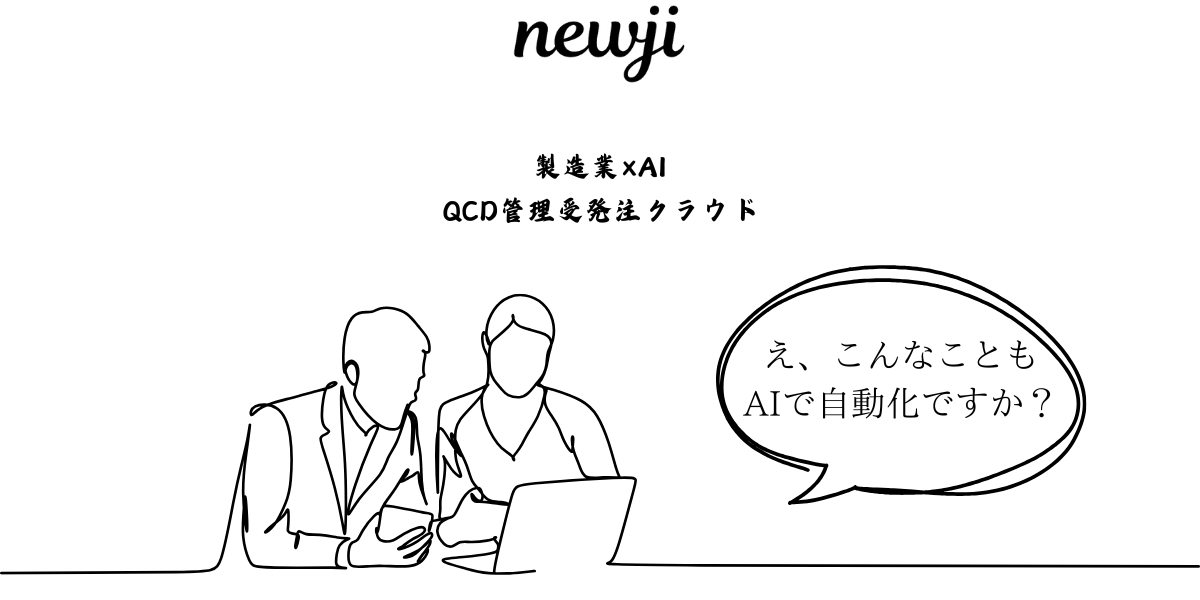
“Revolutionizing Japanese Manufacturing: The Role of Anodizing Processing OEMs”
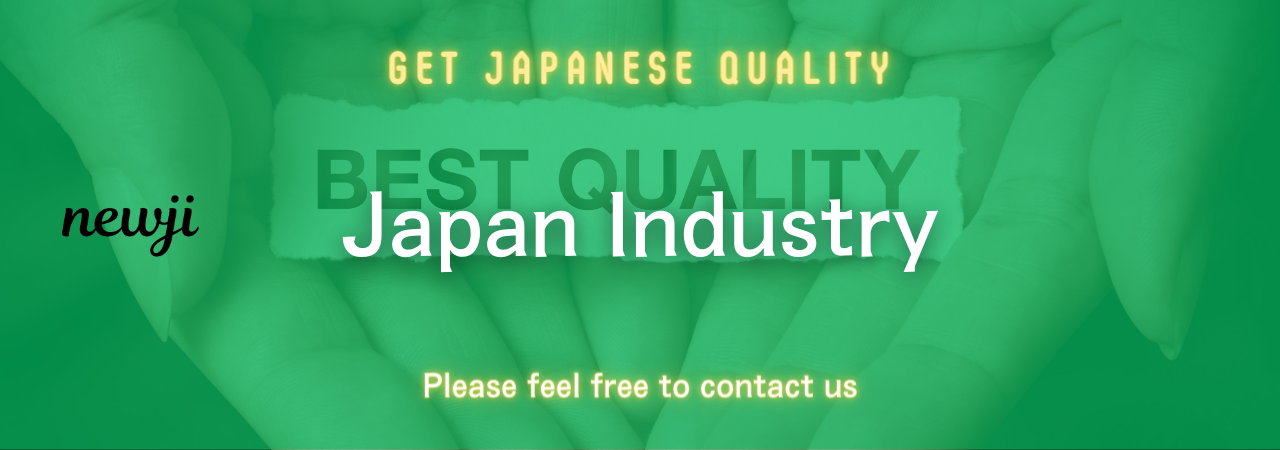
目次
Introduction
In the global manufacturing landscape, Japan stands out as a beacon of technological prowess and quality. One of the critical components contributing to this reputation is the role of Original Equipment Manufacturers (OEMs) specializing in anodizing processing. Anodizing, a surface treatment process, enhances the durability and appearance of metal components, making it indispensable in various industries, including automotive, electronics, and aerospace. This article delves into how Japanese anodizing processing OEMs are revolutionizing manufacturing processes worldwide by leveraging advanced technologies, stringent quality control, and strategic procurement practices.
Understanding Anodizing Processing
Anodizing is an electrochemical process that converts the metal surface into a durable, corrosion-resistant, anodic oxide finish. This process not only enhances the aesthetic appeal of metals like aluminum but also improves their wear resistance and lifespan. In Japan, anodizing processing has evolved into a sophisticated industry, driven by meticulous craftsmanship and continuous innovation.
The Anodizing Process Explained
The anodizing process involves several key steps:
1. **Surface Preparation**: Cleaning the metal surface to remove impurities.
2. **Electrolytic Treatment**: Submerging the metal in an acid electrolyte bath and applying an electric current to form the anodic oxide layer.
3. **Sealing**: Closing the pores of the anodic layer to enhance corrosion resistance.
4. **Finishing**: Applying dyes or other treatments to achieve the desired appearance.
Japanese OEMs have refined each of these steps to ensure uniformity, precision, and high performance.
Advantages of Japanese Anodizing Processing OEMs
Japanese anodizing OEMs offer numerous advantages that set them apart in the global market. These benefits stem from Japan’s commitment to quality, innovation, and efficient manufacturing practices.
High-Quality Standards
Japan is renowned for its stringent quality control measures. OEMs adhere to international standards such as ISO 9001, ensuring that every anodizing process meets or exceeds the required specifications. This dedication minimizes defects and ensures the longevity of processed components.
Advanced Technology
Japanese manufacturers invest heavily in research and development, leading to the adoption of cutting-edge technologies in anodizing. Automation and precision machinery enhance process accuracy, reduce human error, and increase production efficiency.
Customization and Flexibility
Japanese OEMs excel in providing customized anodizing solutions tailored to specific client needs. Whether it’s unique color requirements or specialized surface finishes, these manufacturers offer flexibility that accommodates diverse industry demands.
Efficient Supply Chain Management
Japan’s robust logistics infrastructure ensures timely delivery of anodized components. OEMs benefit from efficient supply chain management practices, reducing lead times and ensuring consistent product availability.
Challenges and Disadvantages
Despite the numerous advantages, procuring anodizing services from Japanese OEMs presents certain challenges that businesses must navigate.
Higher Costs
The premium quality and advanced technology offered by Japanese OEMs often come at a higher price point compared to competitors from other regions. This cost factor can impact the overall budget of manufacturing projects, especially for small to medium-sized enterprises.
Cultural and Language Barriers
Collaborating with Japanese suppliers may involve overcoming cultural differences and language barriers. Miscommunication can lead to delays or misunderstandings, affecting the procurement process and project timelines.
Longer Lead Times
Depending on the location of the purchasing company, international shipping can result in longer lead times. This delay may pose challenges in projects requiring quick turnarounds or urgent component deliveries.
Supplier Negotiation Techniques with Japanese OEMs
Effective negotiation is crucial when engaging with Japanese anodizing processing OEMs. Understanding the cultural nuances and business etiquette can significantly enhance the negotiation outcomes.
Building Relationships
In Japan, building strong, trust-based relationships is essential. Investing time in establishing rapport through regular communication and face-to-face meetings can foster mutual respect and long-term partnerships.
Understanding Cultural Norms
Japanese business culture emphasizes harmony, respect, and consensus. Approaching negotiations with humility, patience, and a willingness to find mutually beneficial solutions can lead to more favorable agreements.
Detail-Oriented Discussions
Japanese OEMs appreciate thoroughness and attention to detail. Presenting clear, well-structured proposals with comprehensive information demonstrates professionalism and facilitates smoother negotiations.
Flexibility and Compromise
Being open to compromise and flexible in negotiations can help bridge gaps between differing expectations. Demonstrating a cooperative attitude encourages Japanese suppliers to reciprocate, fostering win-win scenarios.
Market Conditions for Anodizing Processing in Japan
Understanding the current market landscape is vital for effective procurement and purchasing strategies. Japan’s anodizing processing industry is influenced by various factors, including economic trends, technological advancements, and regulatory frameworks.
Economic Stability
Japan’s stable economy provides a conducive environment for manufacturing and high-quality anodizing services. Economic stability attracts international businesses seeking reliable suppliers with consistent production capabilities.
Technological Innovation
The continuous pursuit of innovation keeps Japanese OEMs at the forefront of anodizing technology. Investments in automation, robotics, and eco-friendly processes enhance efficiency and sustainability, aligning with global industry trends.
Regulatory Environment
Japan’s stringent environmental and safety regulations ensure that anodizing processing adheres to high standards. Compliance with these regulations not only guarantees product safety but also enhances the reputation of OEMs on the international stage.
Competitive Landscape
While Japanese OEMs are leaders in quality and technology, the market is competitive with numerous players striving for excellence. This competition drives continuous improvement and innovation, benefiting clients through better services and products.
Best Practices for Procurement and Purchasing from Japanese Suppliers
Adopting best practices in procurement and purchasing can maximize the benefits of partnering with Japanese anodizing processing OEMs.
Thorough Supplier Evaluation
Conduct comprehensive evaluations of potential suppliers, considering factors such as quality certifications, technological capabilities, production capacity, and financial stability. Site visits and audits can provide deeper insights into the supplier’s operations.
Clear Communication of Requirements
Ensure that all specifications, quality standards, and delivery expectations are clearly communicated. Detailed documentation and regular updates can prevent misunderstandings and ensure that the OEM fully comprehends the project’s needs.
Establishing Long-Term Partnerships
Fostering long-term relationships with Japanese suppliers can lead to better terms, priority treatment, and collaboration on new projects. Consistent business engagement builds trust and encourages suppliers to invest in better services and innovations.
Leveraging Technology for Collaboration
Utilize digital tools and platforms to enhance collaboration, track orders, and manage supply chains effectively. Real-time data sharing and transparent processes improve efficiency and responsiveness in procurement activities.
Implementing Continuous Improvement
Adopt a mindset of continuous improvement by regularly reviewing procurement processes and supplier performance. Feedback mechanisms and performance metrics can identify areas for enhancement, driving better outcomes over time.
Technological Advancements and Factory Efficiency
Japanese anodizing OEMs leverage advanced technologies to enhance factory efficiency and product quality. These technological advancements are pivotal in maintaining Japan’s competitive edge in the global market.
Automation and Robotics
Automation streamlines the anodizing process, reducing manual intervention and increasing precision. Robotics enhance consistency in production, minimize errors, and enable higher production volumes without compromising quality.
Energy-Efficient Processes
Japanese manufacturers prioritize energy efficiency in their operations. Implementing energy-saving technologies not only reduces operational costs but also aligns with global sustainability goals, appealing to environmentally conscious clients.
Smart Manufacturing Solutions
Integrating Internet of Things (IoT) and smart manufacturing solutions allows for real-time monitoring and data analysis. This connectivity enhances decision-making, predictive maintenance, and overall operational efficiency.
Advanced Surface Treatment Technologies
Continuous research leads to the development of innovative surface treatment methods. These advancements improve the performance characteristics of anodized components, meeting the evolving demands of diverse industries.
Quality Control in Japanese Anodizing OEMs
Quality control is a cornerstone of Japanese manufacturing excellence. Anodizing OEMs implement rigorous quality assurance protocols to ensure that each component meets the highest standards.
Comprehensive Testing Procedures
Japanese OEMs conduct extensive testing at various stages of the anodizing process. Tests for thickness, adhesion, color consistency, and corrosion resistance ensure that the final product fulfills all specifications.
Statistical Process Control
Utilizing statistical methods to monitor and control the anodizing process helps maintain consistent quality. Data-driven approaches enable OEMs to identify and address deviations promptly.
Employee Training and Expertise
A skilled workforce is essential for maintaining quality standards. Continuous training programs ensure that employees are proficient in the latest techniques and equipped to handle complex anodizing processes.
Certification and Compliance
Adhering to international quality certifications and industry standards reinforces the credibility of Japanese OEMs. Certifications like ISO 14001 for environmental management further enhance their reputation.
Logistics and Supply Chain Considerations
Efficient logistics and supply chain management are critical for the seamless procurement of anodized components from Japan. Understanding these elements ensures timely and cost-effective delivery.
Strategic Location Advantages
Japan’s strategic location facilitates efficient shipping routes to major global markets. Proximity to key manufacturing hubs reduces transit times and shipping costs, benefiting international clients.
Inventory Management Practices
Japanese OEMs employ just-in-time (JIT) inventory management to minimize excess stock and reduce storage costs. This practice ensures that components are produced and delivered as needed, enhancing responsiveness to demand fluctuations.
Transportation and Distribution Networks
A robust transportation infrastructure, including advanced ports and logistics services, supports the efficient distribution of anodized products. Partnerships with reliable shipping carriers further streamline the supply chain.
Risk Management Strategies
Implementing comprehensive risk management strategies safeguards the supply chain against disruptions. Diversifying suppliers, maintaining safety stock, and utilizing technology for supply chain visibility help mitigate potential risks.
Future Trends in Japanese Manufacturing and Anodizing Services
The Japanese manufacturing sector is poised for significant advancements, driven by technological innovations and evolving market demands. Anticipating these trends can help businesses stay ahead in procurement and purchasing strategies.
Sustainable and Eco-Friendly Practices
Sustainability is becoming a key focus in manufacturing processes. Japanese OEMs are integrating eco-friendly practices, such as reducing energy consumption, minimizing waste, and using environmentally benign chemicals in anodizing, aligning with global sustainability initiatives.
Digital Transformation and Industry 4.0
Embracing Industry 4.0 technologies, including artificial intelligence, machine learning, and big data analytics, enhances operational efficiency and fosters innovation in anodizing processes. These technologies enable predictive maintenance, real-time monitoring, and data-driven decision-making.
Customization and Personalization
As industries demand more customized solutions, Japanese OEMs are developing flexible anodizing processes that can accommodate bespoke requirements. Advanced technologies allow for precise control over color, texture, and finish, catering to diverse client needs.
Enhanced Collaboration and Integration
The future of manufacturing lies in seamless collaboration between suppliers and clients. Enhanced integration through digital platforms facilitates better communication, real-time data sharing, and collaborative problem-solving, leading to more efficient procurement processes.
Focus on Quality and Innovation
Continuous improvement and innovation remain at the heart of Japanese manufacturing. OEMs are investing in research to develop new anodizing techniques, improve process efficiency, and enhance the performance characteristics of anodized components.
Conclusion
Japanese anodizing processing OEMs play a pivotal role in revolutionizing manufacturing by delivering high-quality, durable, and aesthetically pleasing metal components. Their commitment to excellence, advanced technological integration, and strategic procurement practices set them apart in the global market. While challenges such as higher costs and cultural barriers exist, the advantages of partnering with Japanese suppliers—ranging from superior quality and customization to efficient supply chain management—offer substantial benefits. By adopting best practices in procurement, fostering strong supplier relationships, and staying abreast of market trends, businesses can effectively harness the strengths of Japanese anodizing OEMs to drive innovation and maintain competitive edge in their respective industries.
資料ダウンロード
QCD調達購買管理クラウド「newji」は、調達購買部門で必要なQCD管理全てを備えた、現場特化型兼クラウド型の今世紀最高の購買管理システムとなります。
ユーザー登録
調達購買業務の効率化だけでなく、システムを導入することで、コスト削減や製品・資材のステータス可視化のほか、属人化していた購買情報の共有化による内部不正防止や統制にも役立ちます。
NEWJI DX
製造業に特化したデジタルトランスフォーメーション(DX)の実現を目指す請負開発型のコンサルティングサービスです。AI、iPaaS、および先端の技術を駆使して、製造プロセスの効率化、業務効率化、チームワーク強化、コスト削減、品質向上を実現します。このサービスは、製造業の課題を深く理解し、それに対する最適なデジタルソリューションを提供することで、企業が持続的な成長とイノベーションを達成できるようサポートします。
オンライン講座
製造業、主に購買・調達部門にお勤めの方々に向けた情報を配信しております。
新任の方やベテランの方、管理職を対象とした幅広いコンテンツをご用意しております。
お問い合わせ
コストダウンが利益に直結する術だと理解していても、なかなか前に進めることができない状況。そんな時は、newjiのコストダウン自動化機能で大きく利益貢献しよう!
(Β版非公開)