- お役立ち記事
- “Revolutionizing Japanese Manufacturing: The Role of Blenders in Crafting Precision and Innovation”
月間77,185名の
製造業ご担当者様が閲覧しています*
*2025年2月28日現在のGoogle Analyticsのデータより
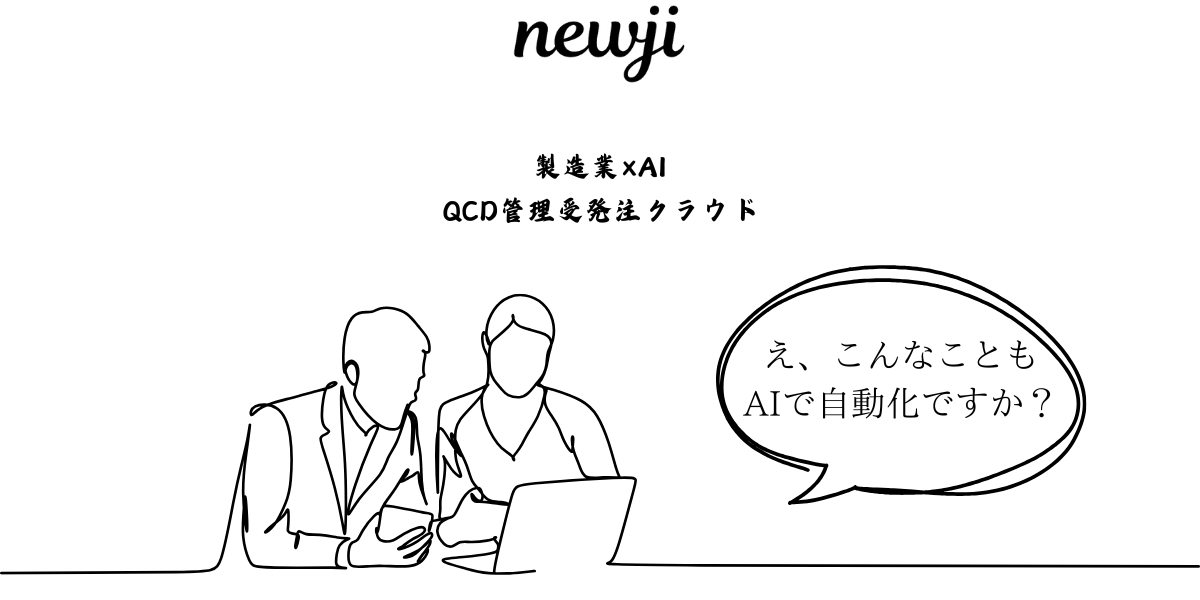
“Revolutionizing Japanese Manufacturing: The Role of Blenders in Crafting Precision and Innovation”
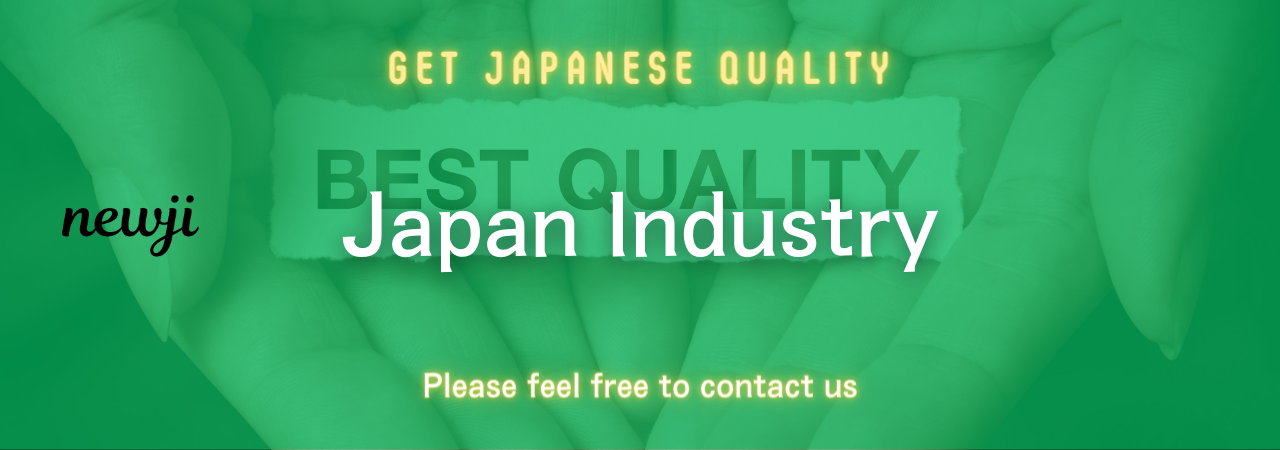
目次
Introduction to Japanese Manufacturing Excellence
Japanese manufacturing has long been synonymous with precision, innovation, and efficiency. The country’s commitment to quality and continuous improvement has set global standards across various industries. Central to this success is the strategic integration of advanced machinery and technology, including the pivotal role of blenders in enhancing manufacturing processes. This article explores how blenders contribute to revolutionizing Japanese manufacturing by fostering precision and driving innovation.
The Role of Blenders in Manufacturing Processes
Blenders, traditionally associated with the food and beverage industry, have found critical applications in manufacturing settings. In Japanese manufacturing, blenders are utilized for mixing, blending, and homogenizing materials with exceptional accuracy. Their role extends beyond mere mixing; they are integral in ensuring uniformity and consistency in products, which is essential for maintaining high-quality standards.
Precision Mixing for Quality Assurance
Precision is a cornerstone of Japanese manufacturing. Blenders equipped with advanced control systems ensure that materials are mixed in exact proportions, minimizing variability and enhancing product quality. This level of precision is particularly important in industries such as pharmaceuticals, electronics, and automotive manufacturing, where consistency can significantly impact performance and reliability.
Innovation through Advanced Blending Technologies
Japanese manufacturers are at the forefront of developing innovative blending technologies. These advancements include computer-controlled blending systems, which allow for real-time adjustments and monitoring. Such technologies enable manufacturers to experiment with new material combinations and processes, fostering innovation and enabling the creation of cutting-edge products.
Advantages of Utilizing Blenders in Japanese Manufacturing
Integrating blenders into manufacturing processes offers numerous advantages that align with the principles of Japanese manufacturing excellence. These benefits contribute to enhanced efficiency, better product quality, and increased flexibility in production.
Enhanced Efficiency and Productivity
Blenders streamline the mixing process, reducing the time and labor required to achieve homogeneous mixtures. Automated blending systems can operate continuously, improving overall production rates and enabling manufacturers to meet high demand without compromising quality.
Improved Product Consistency
Consistency is crucial in maintaining brand reputation and customer satisfaction. Blenders ensure that each batch of product meets the same rigorous standards, reducing the likelihood of defects and variations. This reliability is vital in sectors where precision is non-negotiable, such as electronics and automotive parts manufacturing.
Flexibility in Production
Modern blenders offer versatility, allowing manufacturers to handle a wide range of materials and adjust blending parameters quickly. This flexibility enables rapid response to market changes and the ability to customize products according to specific customer needs, enhancing competitiveness in global markets.
Challenges and Considerations in Implementing Blenders
While the integration of blenders offers significant benefits, manufacturers must navigate certain challenges to maximize their potential. Understanding these considerations is essential for successful implementation and sustained operational excellence.
Initial Investment and Cost
Advanced blending systems require substantial initial investment in equipment and technology. Manufacturers must carefully assess the cost versus the expected benefits, ensuring that the investment aligns with long-term strategic goals and provides a positive return on investment.
Technical Expertise and Training
Operating sophisticated blenders necessitates specialized knowledge and skills. Investing in employee training and development is crucial to ensure that staff can effectively manage and maintain blending systems, optimizing their performance and preventing downtime.
Integration with Existing Systems
Seamlessly integrating blenders with existing manufacturing processes and systems can be complex. Manufacturers must plan and execute integration strategies carefully to avoid disruptions and ensure that new blending technologies complement and enhance current operations.
Supplier Negotiation Techniques for Blenders
Effective negotiation with suppliers is critical in acquiring high-quality blenders at competitive prices. Japanese manufacturers often employ specific strategies to secure favorable terms and build strong supplier relationships.
Building Long-term Partnerships
Japanese business culture emphasizes long-term relationships over short-term gains. Manufacturers prioritize building trust and mutual respect with suppliers, fostering collaborations that benefit both parties through sustained cooperation and shared goals.
Leveraging Market Knowledge
A deep understanding of the blending technology market allows manufacturers to negotiate effectively. By staying informed about market trends, supplier capabilities, and pricing dynamics, manufacturers can secure better deals and ensure they are receiving the best possible products and services.
Quality and Performance Standards
Japanese manufacturers maintain rigorous quality standards and clearly communicate these expectations to suppliers. By setting high-performance benchmarks, they ensure that suppliers deliver blenders that meet or exceed required specifications, contributing to overall manufacturing excellence.
Market Conditions and Trends in Blending Technology
The blending technology market is continuously evolving, influenced by advancements in materials science, automation, and digitalization. Understanding current market conditions and emerging trends is vital for manufacturers seeking to stay competitive and leverage new opportunities.
Advancements in Automation and AI
The integration of automation and artificial intelligence in blending systems is transforming manufacturing processes. Smart blenders equipped with AI capabilities can optimize mixing parameters in real-time, enhance predictive maintenance, and improve overall operational efficiency.
Emphasis on Sustainability
Sustainability is becoming a key focus in manufacturing, driving demand for energy-efficient and eco-friendly blending technologies. Manufacturers are increasingly adopting blenders that reduce energy consumption, minimize waste, and support sustainable production practices.
Customization and Flexibility
There is a growing demand for customized and flexible blending solutions that can accommodate diverse materials and production requirements. Manufacturers are seeking blenders that offer modular designs, easy scalability, and adaptable configurations to meet the unique needs of various industries.
Best Practices for Maximizing Blender Efficiency
To fully leverage the benefits of blenders in manufacturing, adopting best practices is essential. These practices ensure optimal performance, extend equipment lifespan, and maintain high-quality standards.
Regular Maintenance and Calibration
Consistent maintenance and calibration of blending systems are crucial for ensuring accurate and reliable performance. Establishing a preventive maintenance schedule helps identify and address potential issues before they escalate, reducing downtime and maintaining product quality.
Continuous Training and Skill Development
Investing in ongoing training programs for employees ensures that staff remain proficient in operating and troubleshooting blending systems. Continuous skill development fosters a culture of excellence and empowers employees to contribute to process improvements.
Data-Driven Decision Making
Utilizing data analytics to monitor blending performance and process metrics enables manufacturers to make informed decisions. Analyzing data helps identify trends, optimize blending parameters, and implement corrective actions promptly, enhancing overall efficiency and quality.
Case Studies: Success Stories in Japanese Manufacturing
Examining real-world examples of Japanese manufacturers successfully integrating blenders provides valuable insights into best practices and the transformative impact of blending technology.
Electronic Components Manufacturing
A leading electronics manufacturer adopted advanced blending systems to improve the homogeneity of conductive materials used in circuit boards. The integration of precise blenders resulted in enhanced product reliability and performance, enabling the company to secure a larger market share.
Automotive Parts Production
An automotive supplier implemented high-precision blending technology to produce composite materials for lightweight vehicle components. The improved mixing accuracy reduced material waste and production costs, while maintaining stringent quality standards required by automotive manufacturers.
Pharmaceutical Manufacturing
A pharmaceutical company integrated specialized blenders into its production lines to ensure consistent mixing of active ingredients. This integration enhanced product efficacy and compliance with regulatory standards, reinforcing the company’s reputation for quality and reliability.
Future Outlook: The Evolving Role of Blenders in Manufacturing
As manufacturing continues to advance, the role of blenders is expected to expand, driven by technological innovations and evolving industry demands. The future landscape will see blenders becoming more intelligent, interconnected, and integral to sustainable manufacturing practices.
Integration with Industry 4.0
Blenders will increasingly become part of the Industry 4.0 ecosystem, integrating with IoT devices, sensors, and digital platforms. This connectivity will enable real-time monitoring, data sharing, and seamless automation, enhancing overall manufacturing agility and responsiveness.
Enhanced Customization Capabilities
Future blending technologies will offer greater customization options, allowing manufacturers to tailor blending processes to specific product requirements with ease. This adaptability will support the production of highly specialized and personalized products, catering to diverse market needs.
Sustainability and Green Manufacturing
Blenders will play a pivotal role in advancing sustainable manufacturing practices. Innovations aimed at reducing energy consumption, utilizing eco-friendly materials, and minimizing waste will be at the forefront, aligning blending technologies with global sustainability goals.
Conclusion
Blenders have emerged as a critical component in revolutionizing Japanese manufacturing, driving precision, innovation, and efficiency across various industries. By leveraging advanced blending technologies, Japanese manufacturers are able to maintain their competitive edge, ensure high-quality standards, and foster continuous improvement. As the manufacturing landscape evolves, the role of blenders will continue to expand, supporting sustainable practices and enabling the creation of innovative products that meet the demands of a dynamic global market.
資料ダウンロード
QCD管理受発注クラウド「newji」は、受発注部門で必要なQCD管理全てを備えた、現場特化型兼クラウド型の今世紀最高の受発注管理システムとなります。
ユーザー登録
受発注業務の効率化だけでなく、システムを導入することで、コスト削減や製品・資材のステータス可視化のほか、属人化していた受発注情報の共有化による内部不正防止や統制にも役立ちます。
NEWJI DX
製造業に特化したデジタルトランスフォーメーション(DX)の実現を目指す請負開発型のコンサルティングサービスです。AI、iPaaS、および先端の技術を駆使して、製造プロセスの効率化、業務効率化、チームワーク強化、コスト削減、品質向上を実現します。このサービスは、製造業の課題を深く理解し、それに対する最適なデジタルソリューションを提供することで、企業が持続的な成長とイノベーションを達成できるようサポートします。
製造業ニュース解説
製造業、主に購買・調達部門にお勤めの方々に向けた情報を配信しております。
新任の方やベテランの方、管理職を対象とした幅広いコンテンツをご用意しております。
お問い合わせ
コストダウンが利益に直結する術だと理解していても、なかなか前に進めることができない状況。そんな時は、newjiのコストダウン自動化機能で大きく利益貢献しよう!
(β版非公開)