- お役立ち記事
- Revolutionizing Japanese Manufacturing: The Role of Cutting-Edge Analysis Software
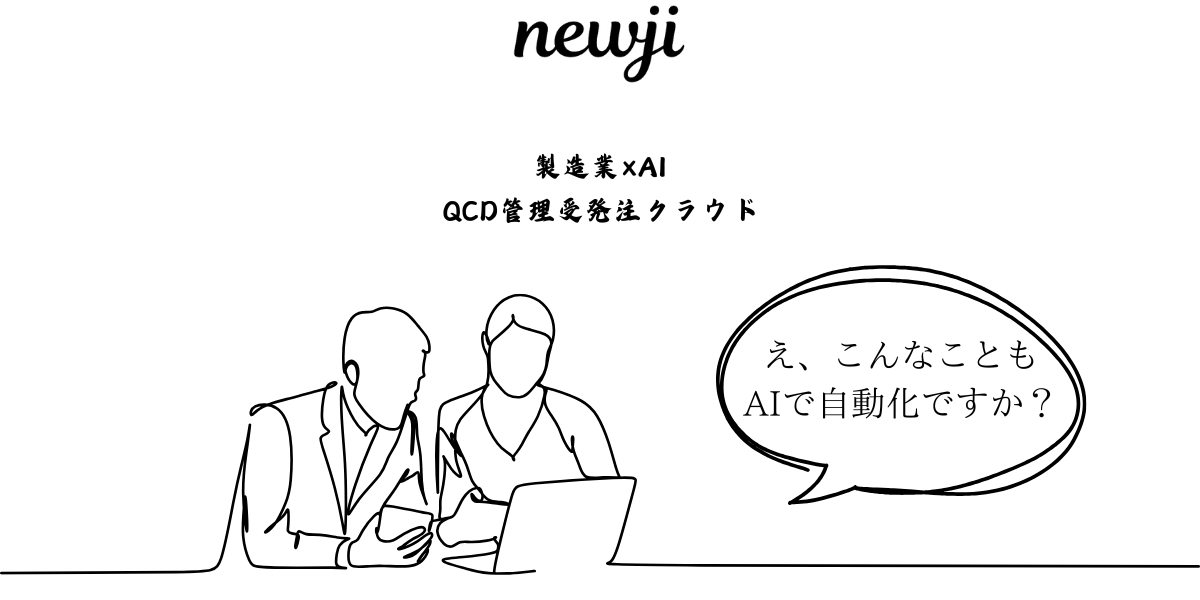
Revolutionizing Japanese Manufacturing: The Role of Cutting-Edge Analysis Software
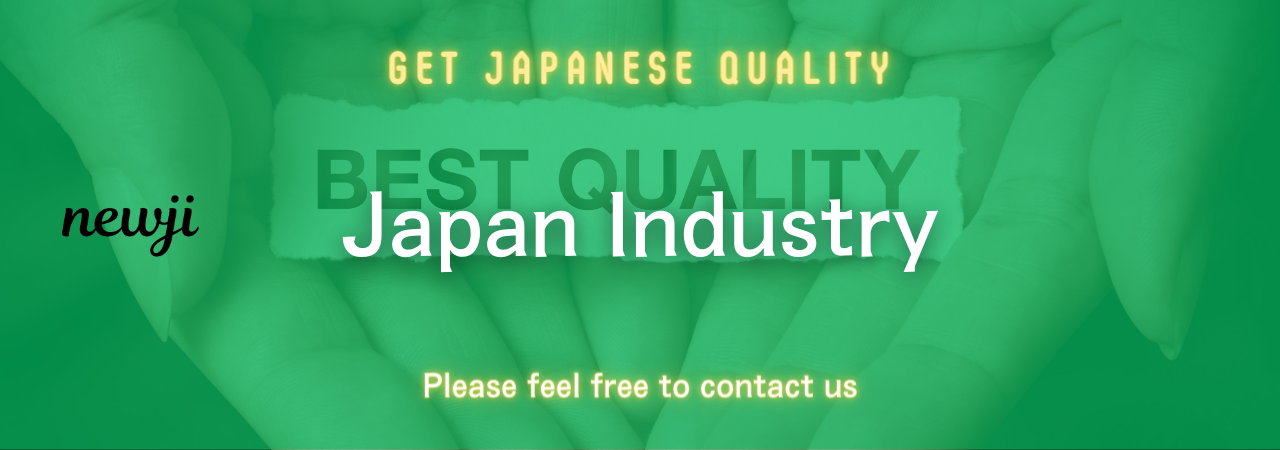
目次
Introduction
Japanese manufacturing has long been synonymous with quality, precision, and innovation. In an increasingly competitive global market, staying ahead requires continuous improvement and adaptation. Cutting-edge analysis software has emerged as a pivotal tool in transforming Japanese manufacturing processes. This article explores the role of advanced analysis software in revolutionizing Japanese manufacturing, providing insights into its benefits, challenges, and best practices from a procurement and purchasing perspective.
The Evolution of Analysis Software in Manufacturing
From Traditional Methods to Digital Transformation
Historically, Japanese manufacturers relied on manual data collection and analysis to manage production processes. While effective to a degree, these traditional methods often led to inefficiencies and limited the ability to respond swiftly to market changes. The digital transformation brought about by advanced analysis software has significantly altered this landscape. Today, manufacturers utilize sophisticated tools that offer real-time data processing, predictive analytics, and automation, enabling more informed decision-making and streamlined operations.
Key Features of Cutting-Edge Analysis Software
Modern analysis software in manufacturing encompasses a range of features designed to enhance operational efficiency and product quality. Key features include:
– **Real-Time Data Monitoring:** Allows for continuous tracking of production metrics.
– **Predictive Maintenance:** Anticipates equipment failures before they occur, reducing downtime.
– **Quality Control Integration:** Ensures products meet stringent quality standards through automated inspections.
– **Supply Chain Analytics:** Optimizes procurement and inventory management by analyzing supplier performance and demand patterns.
– **Advanced Reporting:** Provides comprehensive reports that aid in strategic planning and process improvement.
Benefits for Japanese Manufacturers
Enhancing Efficiency and Reducing Costs
Advanced analysis software significantly boosts operational efficiency by automating routine tasks and optimizing resource allocation. This leads to cost reductions in areas such as labor, energy consumption, and material waste. By identifying bottlenecks and inefficiencies, manufacturers can streamline processes, resulting in faster production cycles and increased output.
Improving Quality Control
Quality is a cornerstone of Japanese manufacturing excellence. Cutting-edge analysis software enhances quality control by enabling precise monitoring of production parameters and automating inspection processes. This reduces the risk of defects, ensures consistent product quality, and minimizes the costs associated with rework and waste.
Facilitating Data-Driven Decision Making
In the era of big data, the ability to leverage information effectively is crucial. Analysis software provides manufacturers with actionable insights derived from vast amounts of data. This empowers decision-makers to make informed choices regarding production strategies, supplier selection, and market trends, thereby enhancing competitiveness and responsiveness to market demands.
Challenges and Disadvantages
While the adoption of advanced analysis software offers numerous benefits, it also presents certain challenges:
– **High Initial Investment:** The cost of implementing sophisticated software solutions can be substantial, posing a barrier for smaller manufacturers.
– **Integration with Existing Systems:** Ensuring compatibility with current infrastructure and processes requires careful planning and execution.
– **Training and Skill Development:** Employees must be trained to effectively use new software, which involves time and resources.
– **Data Security Concerns:** With increased digitalization, safeguarding sensitive data becomes paramount to prevent breaches and cyber threats.
Supplier Negotiation Techniques Aided by Analysis Software
Effective supplier negotiation is critical in procurement and purchasing. Analysis software provides valuable data that can enhance negotiation strategies:
– **Performance Metrics:** Detailed insights into supplier performance, such as delivery timelines and quality standards, enable more informed negotiations.
– **Cost Analysis:** Understanding the cost structures and identifying areas for cost savings strengthens bargaining positions.
– **Demand Forecasting:** Accurate demand predictions allow manufacturers to negotiate better terms based on anticipated volume requirements.
– **Risk Assessment:** Identifying potential risks associated with suppliers helps in negotiating favorable terms that mitigate these risks.
Market Conditions Influencing Software Adoption
Several market conditions impact the adoption of advanced analysis software in Japanese manufacturing:
– **Global Competition:** Intense competition drives the need for technological advancements to maintain market position.
– **Supply Chain Complexity:** As supply chains become more global and intricate, the need for sophisticated analytics to manage them effectively increases.
– **Technological Advancements:** Rapid developments in AI, machine learning, and IoT provide new capabilities that manufacturers can leverage.
– **Regulatory Requirements:** Compliance with international standards and regulations necessitates the use of accurate and reliable analysis tools.
Best Practices for Implementing Analysis Software in Manufacturing
Successful implementation of analysis software requires strategic planning and execution. Best practices include:
– **Assessing Needs and Goals:** Clearly define what the organization aims to achieve with the software to ensure it aligns with business objectives.
– **Choosing the Right Software:** Select software that fits the specific needs of the manufacturing processes and integrates seamlessly with existing systems.
– **Comprehensive Training Programs:** Invest in training employees to maximize the software’s potential and ensure smooth adoption.
– **Phased Implementation:** Gradually integrate the software into operations to manage the transition effectively and address any issues promptly.
– **Continuous Evaluation and Improvement:** Regularly assess the software’s performance and make necessary adjustments to enhance its effectiveness.
Case Studies: Success Stories in Japanese Manufacturing
Several Japanese manufacturers have successfully leveraged cutting-edge analysis software to enhance their operations:
– **Toyota:** By implementing advanced analytics in their production lines, Toyota has achieved remarkable improvements in efficiency and quality, reinforcing their reputation for reliability.
– **Panasonic:** Panasonic utilizes predictive maintenance software to minimize downtime and maintain consistent production levels, resulting in cost savings and increased output.
– **Sony:** Sony’s adoption of data-driven decision-making tools has enabled them to better manage their supply chain, ensuring timely delivery and high-quality products.
These case studies highlight the tangible benefits of integrating analysis software into manufacturing processes, showcasing how it can drive success and sustainability.
Future Trends in Manufacturing Analysis Software
The landscape of manufacturing is continually evolving, and so is analysis software. Future trends include:
– **Artificial Intelligence and Machine Learning:** Enhanced predictive capabilities and automation will further optimize manufacturing processes.
– **Integration with IoT Devices:** Increased connectivity will provide more granular data, enabling deeper insights and more precise control.
– **Cloud-Based Solutions:** Greater adoption of cloud technologies will offer scalability and flexibility, making advanced analytics more accessible.
– **Augmented Reality (AR) and Virtual Reality (VR):** These technologies will complement analysis software by providing immersive data visualization and interactive planning tools.
Staying abreast of these trends will be essential for manufacturers aiming to maintain their competitive edge.
Conclusion
Cutting-edge analysis software is revolutionizing Japanese manufacturing by driving efficiency, enhancing quality control, and enabling data-driven decision-making. While the adoption of such technologies presents challenges, the benefits far outweigh the drawbacks, offering significant advantages in procurement and purchasing, supplier negotiations, and overall market competitiveness. By following best practices and leveraging the latest advancements, Japanese manufacturers can continue to uphold their reputation for excellence and innovate for the future.
資料ダウンロード
QCD調達購買管理クラウド「newji」は、調達購買部門で必要なQCD管理全てを備えた、現場特化型兼クラウド型の今世紀最高の購買管理システムとなります。
ユーザー登録
調達購買業務の効率化だけでなく、システムを導入することで、コスト削減や製品・資材のステータス可視化のほか、属人化していた購買情報の共有化による内部不正防止や統制にも役立ちます。
NEWJI DX
製造業に特化したデジタルトランスフォーメーション(DX)の実現を目指す請負開発型のコンサルティングサービスです。AI、iPaaS、および先端の技術を駆使して、製造プロセスの効率化、業務効率化、チームワーク強化、コスト削減、品質向上を実現します。このサービスは、製造業の課題を深く理解し、それに対する最適なデジタルソリューションを提供することで、企業が持続的な成長とイノベーションを達成できるようサポートします。
オンライン講座
製造業、主に購買・調達部門にお勤めの方々に向けた情報を配信しております。
新任の方やベテランの方、管理職を対象とした幅広いコンテンツをご用意しております。
お問い合わせ
コストダウンが利益に直結する術だと理解していても、なかなか前に進めることができない状況。そんな時は、newjiのコストダウン自動化機能で大きく利益貢献しよう!
(Β版非公開)