- お役立ち記事
- “Revolutionizing Japanese Manufacturing: The Role of Data Centers in Industry 4.0”
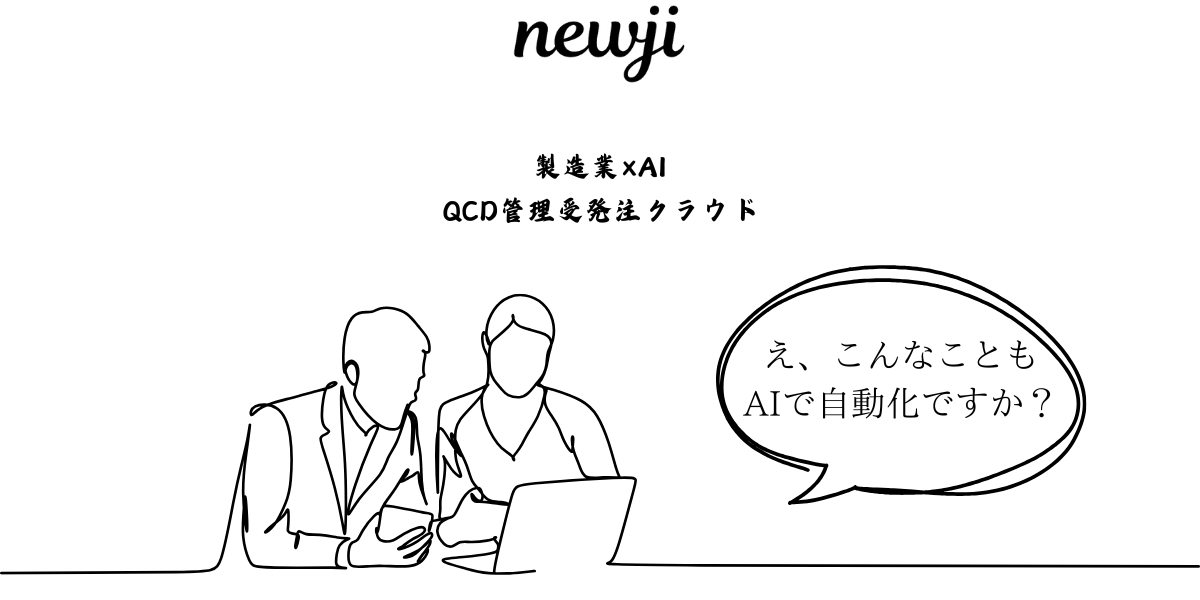
“Revolutionizing Japanese Manufacturing: The Role of Data Centers in Industry 4.0”
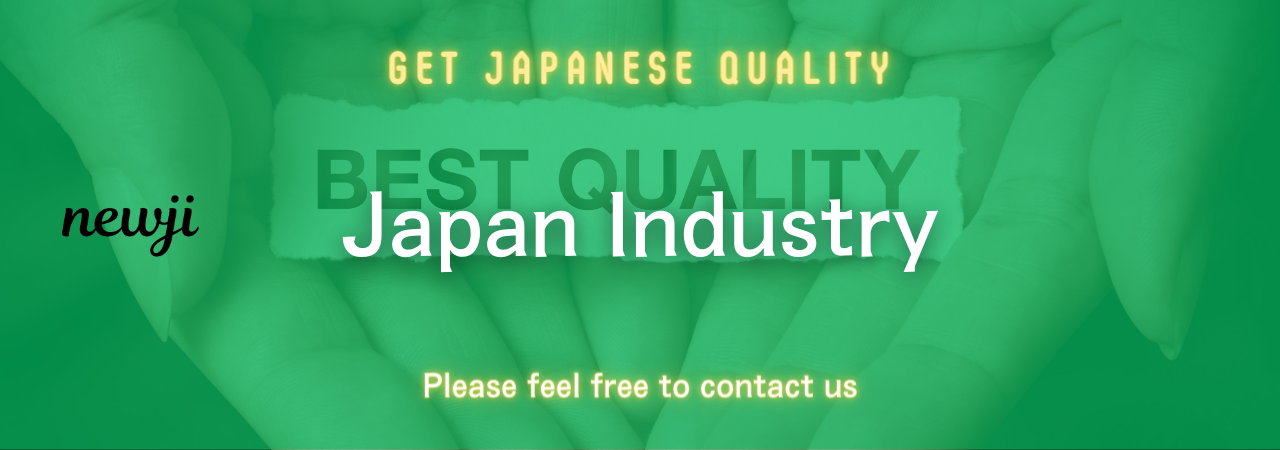
目次
Introduction to Industry 4.0
Industry 4.0, also known as the Fourth Industrial Revolution, represents a paradigm shift in manufacturing processes.
It encompasses the integration of cyber-physical systems, the Internet of Things (IoT), big data analytics, and cloud computing within industrial production.
Japan, renowned for its pioneering manufacturing techniques and robust supply chains, is at the forefront of adopting Industry 4.0 methodologies.
A pivotal player in this transition is the data center, which serves as the backbone for storing and processing the vast amounts of data generated by Industry 4.0 technologies.
The Evolution of Manufacturing in Japan
Historically, Japan’s manufacturing prowess has been driven by kaizen, or continuous improvement, and just-in-time production methodologies.
These philosophies have ensured minimal waste, optimal inventory management, and high-quality production.
Incorporating the principles of Industry 4.0 into this already sophisticated framework necessitates an emphasis on data collection, real-time analysis, and seamless integration across all production stages.
Data centers play a crucial role by acting as centralized hubs where this data is stored, processed, and analyzed to drive intelligent decision-making.
The Role of Data Centers in Industry 4.0
Data Storage and Management
One of the foremost functions of data centers in Industry 4.0 is data storage and management.
Manufacturing environments are now inundated with data from sensors, machines, and IoT devices.
This data, ranging from operational metrics to quality control logs, needs to be stored securely and accessed quickly for real-time processing.
Data Processing and Analytics
Data, in its raw form, holds little value unless processed and analyzed to derive meaningful insights.
Data centers provide the computational power and infrastructure necessary to run complex algorithms and machine learning models.
These analytics enable manufacturers to predict equipment failures, optimize production schedules, and improve product quality by identifying patterns and anomalies that humans might overlook.
Edge Computing
Although data centers are essential, not all data needs to be sent to centralized locations for processing.
Edge computing facilitates real-time data analysis at the source.
In a manufacturing setup, this means that data from machines and sensors can be analyzed on the factory floor itself.
This minimizes latency and allows for instant decision-making, thereby enhancing overall operational efficiency.
Cloud Integration
Cloud technology complements data centers by offering scalable storage and computing resources.
It allows for the seamless integration of disparate systems and data sources across global supply chains.
Japanese manufacturers can leverage cloud-based platforms to collaborate more effectively with suppliers and customers worldwide, ensuring that production processes are agile and responsive to market demands.
Advantages of Data Centers in Japanese Manufacturing
Enhanced Operational Efficiency
The integration of data centers helps in streamlining manufacturing processes.
From predictive maintenance to production scheduling, data-driven insights ensure that operations run smoothly and efficiently.
The ability to anticipate and mitigate potential issues can lead to significant cost savings and reduced downtime.
Improved Quality Control
Data collected from various stages of production can be analyzed to monitor and enhance product quality.
Real-time analytics can immediately flag any deviations from quality standards, allowing for corrective actions to be taken instantaneously.
This leads to higher customer satisfaction and lower return rates.
Supply Chain Optimization
Data centers enable better visibility and control over the supply chain.
From procuring raw materials to delivering finished products, data-driven insights can optimize every stage, ensuring timely deliveries and optimal inventory levels.
This is particularly crucial for just-in-time manufacturing practices that rely heavily on precise supply chain coordination.
Facilitation of Innovation
Access to advanced data analytics and computational resources fosters a culture of innovation.
Japanese manufacturers can experiment with new production methods, materials, and technologies.
Data centers also enable the simulation and testing of new ideas in a virtual environment before implementing them on the production floor, reducing risk and accelerating innovation cycles.
Challenges and Disadvantages
High Initial Costs
Setting up and maintaining data centers requires substantial initial investment.
The costs associated with advanced hardware, software, cooling systems, and security can be prohibitive for smaller manufacturers.
However, the long-term benefits often justify the initial expenditure.
Data Security Concerns
With the increasing amount of data being generated and stored, data security becomes paramount.
Data centers must implement robust security measures to protect against cyber-attacks and data breaches.
This includes encryption, multi-factor authentication, and regular security audits.
Skill Gap
The successful implementation of Industry 4.0 technologies requires a skilled workforce proficient in data analytics, machine learning, and cybersecurity.
There is often a gap between the available skillset and the required expertise.
Manufacturers must invest in training and development programs to bridge this gap.
Integration Challenges
For established manufacturers with legacy systems, integrating new Industry 4.0 technologies can be challenging.
It involves a complete overhaul of existing processes and systems, which can be time-consuming and disruptive.
A phased approach and careful planning can mitigate some of these challenges.
Best Practices for Leveraging Data Centers
Collaborative Approach
Collaboration between IT, operations, and data analysis teams is crucial for the successful implementation of data center technologies.
Regular communication and feedback loops ensure that the insights derived from data analytics are effectively applied to optimize manufacturing processes.
Scalable Solutions
Manufacturers should invest in scalable data center solutions that can grow with their business.
This ensures that the infrastructure can handle increasing data volumes and processing demands as operations expand.
Focus on Data Quality
The quality of insights derived from data analytics is directly proportional to the quality of data collected.
Implementing stringent data validation and cleansing processes ensures that the data being analyzed is accurate and reliable.
Continuous Improvement
The principles of kaizen, or continuous improvement, should be applied to data center operations as well.
Regularly reviewing performance metrics, identifying areas for improvement, and implementing changes ensures that data center capabilities are continually optimized.
The Future of Japanese Manufacturing with Data Centers
The integration of data centers within the framework of Industry 4.0 positions Japanese manufacturing for a prosperous future.
As data analytics, IoT, and machine learning technologies continue to evolve, the role of data centers will only become more critical.
By embracing these technologies, Japanese manufacturers can maintain their competitive edge, drive innovation, and achieve new levels of operational excellence.
Conclusion
The adoption of Industry 4.0 principles through the effective use of data centers represents a monumental shift in Japanese manufacturing.
While the journey involves challenges and substantial investment, the benefits in terms of operational efficiency, quality control, and supply chain optimization are undeniable.
By leveraging best practices and fostering a collaborative, data-driven culture, Japanese manufacturers can revolutionize their operations and lead the way in the Fourth Industrial Revolution.
資料ダウンロード
QCD調達購買管理クラウド「newji」は、調達購買部門で必要なQCD管理全てを備えた、現場特化型兼クラウド型の今世紀最高の購買管理システムとなります。
ユーザー登録
調達購買業務の効率化だけでなく、システムを導入することで、コスト削減や製品・資材のステータス可視化のほか、属人化していた購買情報の共有化による内部不正防止や統制にも役立ちます。
NEWJI DX
製造業に特化したデジタルトランスフォーメーション(DX)の実現を目指す請負開発型のコンサルティングサービスです。AI、iPaaS、および先端の技術を駆使して、製造プロセスの効率化、業務効率化、チームワーク強化、コスト削減、品質向上を実現します。このサービスは、製造業の課題を深く理解し、それに対する最適なデジタルソリューションを提供することで、企業が持続的な成長とイノベーションを達成できるようサポートします。
オンライン講座
製造業、主に購買・調達部門にお勤めの方々に向けた情報を配信しております。
新任の方やベテランの方、管理職を対象とした幅広いコンテンツをご用意しております。
お問い合わせ
コストダウンが利益に直結する術だと理解していても、なかなか前に進めることができない状況。そんな時は、newjiのコストダウン自動化機能で大きく利益貢献しよう!
(Β版非公開)