- お役立ち記事
- Revolutionizing Japanese Manufacturing: The Role of Heat-Treated and Surface-Treated High-Precision Machined Components
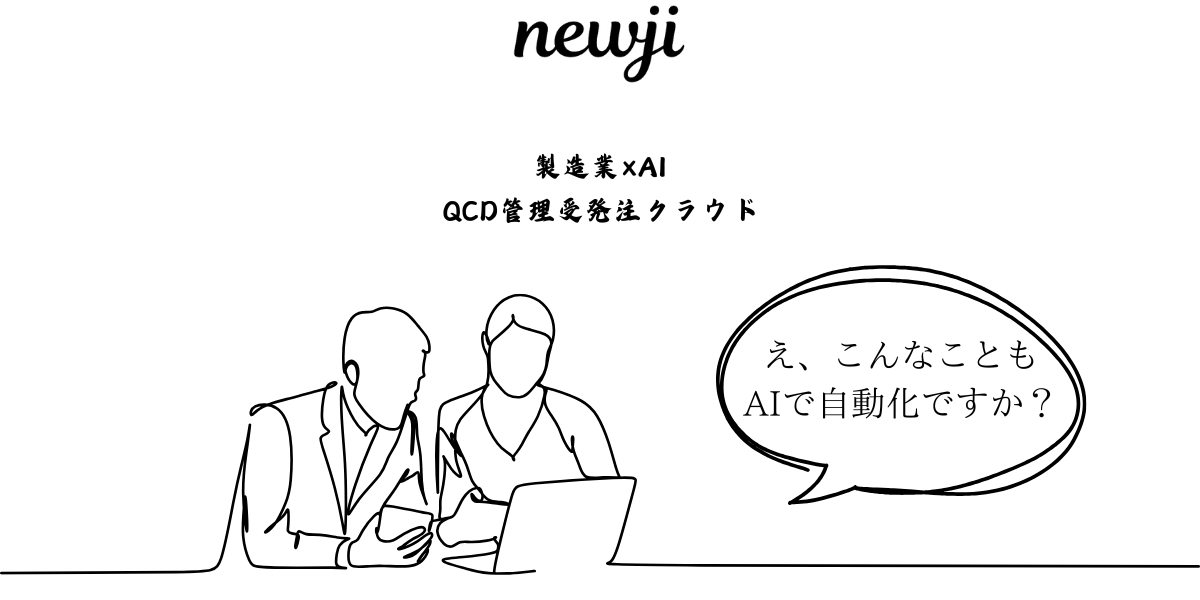
Revolutionizing Japanese Manufacturing: The Role of Heat-Treated and Surface-Treated High-Precision Machined Components
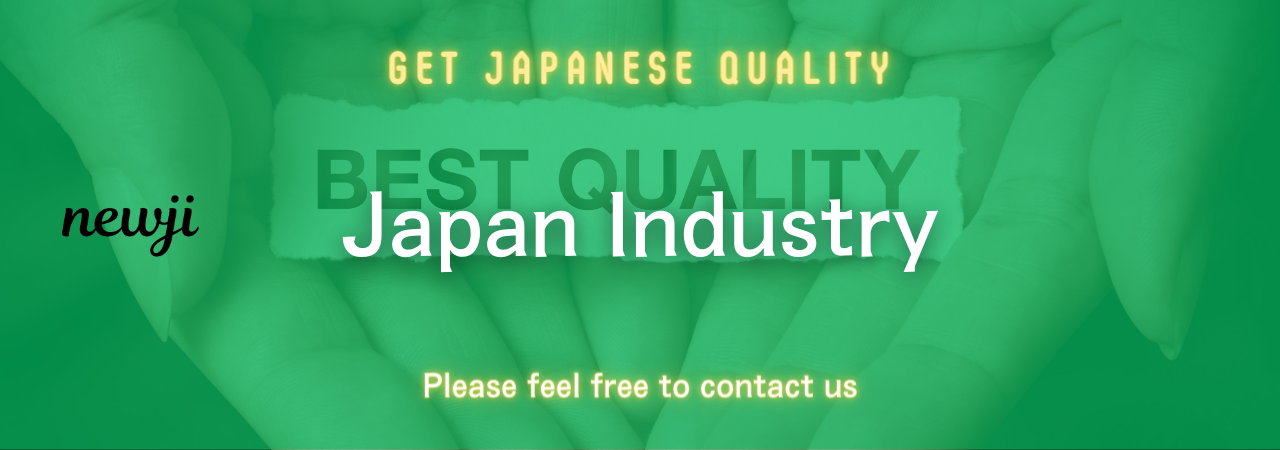
目次
Introduction to High-Precision Machined Components in Japanese Manufacturing
Japanese manufacturing has long been synonymous with precision, quality, and innovation.
The integration of heat-treated and surface-treated high-precision machined components has been pivotal in maintaining Japan’s competitive edge in the global market.
These advanced processes not only enhance the performance and longevity of components but also optimize manufacturing efficiency and product reliability.
In this article, we delve into the role of these specialized components, exploring their advantages, challenges, procurement strategies, and best practices within the Japanese manufacturing landscape.
The Importance of Heat-Treated High-Precision Machined Components
Enhancing Material Properties
Heat treatment processes, such as annealing, quenching, and tempering, are critical in altering the physical and mechanical properties of metals.
These processes increase hardness, tensile strength, and wear resistance, making components more durable and capable of withstanding rigorous operational demands.
Improving Component Longevity
By enhancing material properties, heat treatment significantly extends the lifespan of machined components.
This reduction in wear and tear translates to lower maintenance costs and increased reliability in end-user applications.
Facilitating Complex Designs
Heat-treated components can maintain structural integrity even in intricate designs, allowing manufacturers to produce complex parts without compromising on strength or precision.
The Role of Surface Treatment in High-Precision Machined Components
Corrosion Resistance
Surface treatments, including plating, anodizing, and coating, protect components from corrosion and environmental degradation.
This protection is essential for components exposed to harsh conditions, ensuring consistent performance and appearance over time.
Reducing Friction and Wear
Surface treatments can create smooth interfaces, reducing friction between moving parts.
This reduction not only improves the efficiency of mechanical systems but also minimizes wear, further enhancing component durability.
Aesthetic Enhancement
Beyond functional benefits, surface treatments can improve the visual appeal of components.
This is particularly important in consumer-facing products where appearance can influence purchasing decisions.
Advantages of Heat-Treated and Surface-Treated Components
Superior Performance
Heat-treated and surface-treated components exhibit enhanced mechanical properties, leading to superior performance in demanding applications.
Increased Durability
The improved hardness and resistance to wear and corrosion result in longer-lasting components, reducing the frequency of replacements and associated costs.
Cost Efficiency
While the initial investment in specialized treatments may be higher, the extended lifespan and reduced maintenance needs translate to overall cost savings.
Customization Potential
These treatments offer flexibility in customizing components to meet specific performance criteria, allowing manufacturers to cater to diverse industry needs.
Disadvantages and Challenges
Higher Initial Costs
The advanced processes involved in heat and surface treatments require specialized equipment and expertise, leading to higher upfront costs.
Extended Production Times
Additional treatment steps can lengthen the manufacturing timeline, potentially impacting delivery schedules and responsiveness to market demands.
Quality Control Complexity
Ensuring consistent treatment quality necessitates stringent quality control measures, adding layers of complexity to the production process.
Supplier Negotiation Techniques for High-Precision Components
Understanding Supplier Capabilities
Thoroughly evaluate potential suppliers’ technical capabilities, including their expertise in heat and surface treatments, to ensure they meet quality standards.
Building Strong Relationships
Fostering long-term partnerships with suppliers can lead to better terms, priority in production schedules, and collaborative problem-solving.
Transparent Communication
Maintain open lines of communication regarding specifications, expectations, and feedback to ensure alignment and address issues promptly.
Leveraging Competitive Bidding
Encourage competition among suppliers by soliciting multiple bids, which can help negotiate more favorable pricing and terms.
Market Conditions Influencing Procurement
Global Supply Chain Dynamics
Fluctuations in global supply chains can impact availability and lead times for specialized components, necessitating strategic procurement planning.
Technological Advancements
Rapid advancements in manufacturing technologies require suppliers to continuously update their processes and capabilities, influencing procurement decisions based on innovation readiness.
Regulatory Standards
Compliance with international and local regulations concerning material usage and treatment processes can affect supplier selection and component specifications.
Economic Factors
Economic conditions, including currency exchange rates and trade policies, play a significant role in cost considerations and supplier negotiations.
Best Practices in Procuring Heat-Treated and Surface-Treated Components
Detailed Specification Documentation
Provide comprehensive specifications, including material grades, treatment processes, and tolerances, to ensure suppliers understand and can meet requirements accurately.
Supplier Audits and Assessments
Conduct regular audits and assessments of suppliers to verify their adherence to quality standards and operational capabilities.
Diversifying Supplier Base
Avoid dependency on a single supplier by developing relationships with multiple vendors, enhancing supply chain resilience.
Integrating Quality Control Measures
Implement stringent quality control protocols both internally and collaboratively with suppliers to maintain high component standards.
Emphasizing Continuous Improvement
Encourage a culture of continuous improvement, where both manufacturers and suppliers seek to optimize processes, reduce waste, and enhance component quality.
Case Studies: Success Stories in Japanese Manufacturing
Automotive Industry
Japanese automotive giants leverage heat-treated and surface-treated components to achieve high reliability and performance in their vehicles, contributing to their global reputation for excellence.
Electronics Sector
In consumer electronics, precision components ensure device longevity and functionality, with surface treatments providing protection against environmental factors.
Aerospace Applications
The aerospace industry relies on these advanced components for critical applications, where failure is not an option, underscoring the importance of precision and durability.
Future Trends in High-Precision Component Manufacturing
Industry 4.0 and Smart Manufacturing
Integration of IoT and automation in manufacturing processes will enhance precision, reduce errors, and increase efficiency in producing high-precision components.
Advanced Materials Development
Ongoing research into new materials and alloys will lead to components with superior properties, further pushing the boundaries of manufacturing capabilities.
Sustainability Initiatives
Environmental considerations are driving the adoption of eco-friendly treatment processes and sustainable materials, aligning with global sustainability goals.
Customization and On-Demand Production
The demand for customized components is increasing, with manufacturers adopting flexible production systems to meet specific customer needs promptly.
Conclusion
Heat-treated and surface-treated high-precision machined components are at the forefront of revolutionizing Japanese manufacturing.
Their ability to enhance performance, durability, and efficiency makes them indispensable across various industries.
While there are challenges in terms of costs and production complexity, strategic procurement practices and strong supplier relationships can mitigate these issues.
As the manufacturing landscape evolves with technological advancements and sustainability imperatives, the role of these advanced components will continue to grow, ensuring that Japanese manufacturing remains a global leader in quality and innovation.
資料ダウンロード
QCD調達購買管理クラウド「newji」は、調達購買部門で必要なQCD管理全てを備えた、現場特化型兼クラウド型の今世紀最高の購買管理システムとなります。
ユーザー登録
調達購買業務の効率化だけでなく、システムを導入することで、コスト削減や製品・資材のステータス可視化のほか、属人化していた購買情報の共有化による内部不正防止や統制にも役立ちます。
NEWJI DX
製造業に特化したデジタルトランスフォーメーション(DX)の実現を目指す請負開発型のコンサルティングサービスです。AI、iPaaS、および先端の技術を駆使して、製造プロセスの効率化、業務効率化、チームワーク強化、コスト削減、品質向上を実現します。このサービスは、製造業の課題を深く理解し、それに対する最適なデジタルソリューションを提供することで、企業が持続的な成長とイノベーションを達成できるようサポートします。
オンライン講座
製造業、主に購買・調達部門にお勤めの方々に向けた情報を配信しております。
新任の方やベテランの方、管理職を対象とした幅広いコンテンツをご用意しております。
お問い合わせ
コストダウンが利益に直結する術だと理解していても、なかなか前に進めることができない状況。そんな時は、newjiのコストダウン自動化機能で大きく利益貢献しよう!
(Β版非公開)