- お役立ち記事
- Revolutionizing Japanese Manufacturing: The Role of High-Definition Controllers (HDC) in Modern Robot Controllers
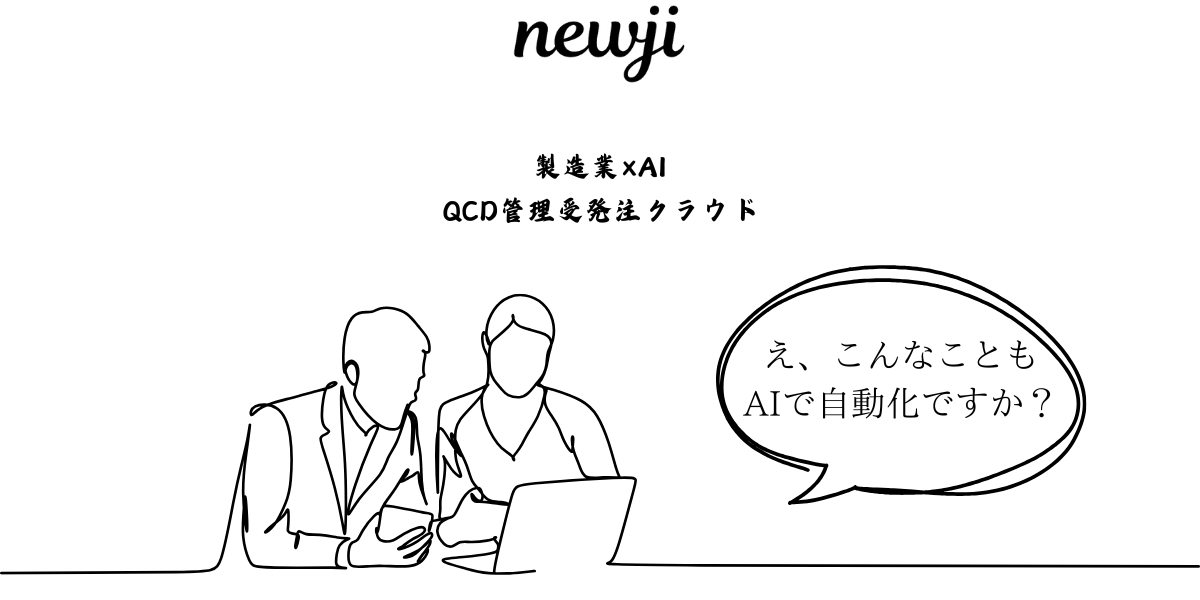
Revolutionizing Japanese Manufacturing: The Role of High-Definition Controllers (HDC) in Modern Robot Controllers
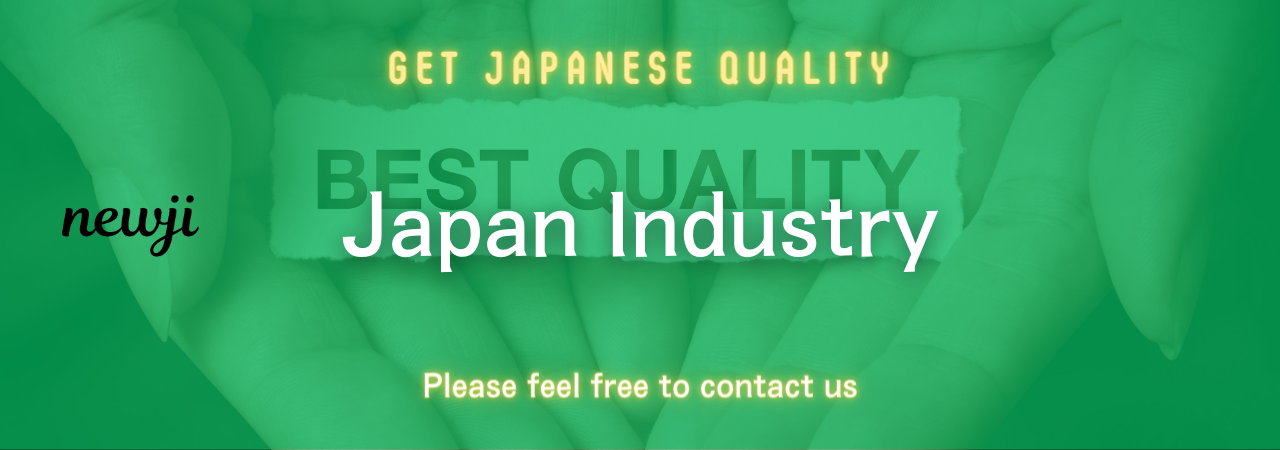
目次
Introduction to High-Definition Controllers (HDC)
High-Definition Controllers (HDC) represent a groundbreaking innovation in the world of robotic automation. These controllers offer precision, flexibility, and reliability, thereby revolutionizing modern manufacturing processes. In the highly competitive landscape of global manufacturing, staying ahead of technological advancements is not just desirable, but essential.
Japanese manufacturers, in particular, have embraced the integration of HDC into their robotic systems. This shift has facilitated numerous process improvements and has opened new avenues for operational excellence.
The Role of HDC in Japanese Manufacturing
Enhancing Precision and Accuracy
In manufacturing, precision and accuracy are paramount. HDCs enable unprecedented levels of control over robotic operations. This accuracy is crucial, particularly in industries such as automotive, electronics, and aerospace, where the margin for error is infinitesimal. Japanese manufacturers have consistently been at the forefront of producing high-quality, reliable products. The adoption of HDC in robot controllers has further cemented their reputation for precision engineering.
Improving Flexibility and Adaptability
One of the significant advantages of HDC is their flexibility. These controllers can adapt to various tasks and operational changes with minimal downtime. In the dynamic manufacturing environment, the ability to quickly switch tasks or adjust processes can lead to substantial productivity gains. Japanese firms have leveraged this flexibility to maintain high volumes of production while meeting diverse market demands.
Advantages of HDC in Manufacturing
Increased Efficiency
HDCs streamline processes, reducing manual intervention and thereby enhancing overall efficiency. Robots equipped with HDC can execute complex tasks more quickly and consistently. This improvement translates to lower operational costs and higher throughput, which are critical in maintaining a competitive edge.
Cost Savings
While the initial investment in HDC technology can be substantial, the long-term cost benefits are significant. Reduced waste, minimized errors, and lowered labor costs contribute to overall savings. Japanese manufacturers have found that these savings often offset the initial expenses within a relatively short period.
Enhanced Quality Control
Quality control is an area where HDCs excel. With precise control, the variability in product quality is minimized, leading to a consistently high output standard. This improvement not only satisfies customer expectations but also reduces the need for rework and warranty claims.
Challenges and Considerations
Initial Investment
The implementation of HDC technology requires a considerable upfront investment. Costs include not only the purchase of new equipment but also training for staff and potential downtime during the transition period. This financial burden can be a barrier for smaller manufacturers.
Integration with Existing Systems
Another challenge is the integration of HDCs with existing manufacturing systems. Ensuring compatibility and seamless performance can be complex and time-consuming. Japanese companies have often mitigated this risk by working closely with specialized integrators who understand the nuances of both the new and legacy systems.
Maintenance and Upkeep
While HDC technology can reduce operational issues, it also necessitates regular maintenance to ensure peak performance. Manufacturers must invest in skilled personnel or training programs to keep the systems running smoothly. This requirement can add to the ongoing operational costs.
Supplier Negotiation Techniques
Understanding Market Conditions
Effective negotiation with suppliers requires a deep understanding of current market conditions. This knowledge allows purchasing departments to leverage the best prices and terms. Japanese companies typically conduct extensive market research to stay informed about technological advancements, supplier capabilities, and cost trends.
Building Long-Term Relationships
Japanese manufacturers often prioritize building long-term relationships with their suppliers. These relationships are founded on trust, mutual benefit, and shared goals. Long-term partnerships can lead to better pricing, priority service, and collaborative innovation.
Flexibility and Customization
Negotiating for flexibility and customization options is also crucial. Suppliers who can tailor their products and services to meet specific needs are more valuable. Japanese firms frequently negotiate terms that allow for flexible scaling and customization to better adapt to changing production requirements.
Quality and Compliance
Ensuring that suppliers adhere to stringent quality and compliance standards is non-negotiable. Regular audits, quality checks, and compliance reviews are part of the negotiation process. Japanese companies are known for their rigorous standards, and this diligence extends to their supplier relationships.
Best Practices in Implementing HDC
Pilot Testing
Pilot testing is a critical step before full-scale implementation. A pilot program allows for real-world testing in a controlled environment. Japanese manufacturers typically start with a pilot phase to identify and address potential issues before broader deployment.
Employee Training
Successful implementation of HDC technology depends heavily on employee competency. Comprehensive training programs ensure that staff are well-equipped to operate and maintain the new systems. Japanese firms invest significantly in training to maximize the potential of their technological investments.
Continuous Improvement
The adoption of HDC is not a one-time event but a continuous process of improvement. Regular reviews and updates are necessary to stay abreast of technological advancements and to optimize performance. Japanese manufacturers thrive on a culture of kaizen, or continuous improvement, which aligns perfectly with the iterative nature of technological enhancements.
Collaboration with Technology Providers
Working closely with technology providers can yield significant benefits. These providers offer insights into best practices, ongoing support, and updates. Japanese firms often engage in collaborative partnerships with leading technology providers to ensure they remain at the cutting edge of innovation.
The Future of HDC in Manufacturing
IoT and Industry 4.0
The Internet of Things (IoT) and Industry 4.0 are shaping the future of manufacturing. HDC technology will play a pivotal role in this transformation. By integrating HDC with IoT devices, manufacturers can achieve greater connectivity, real-time monitoring, and advanced data analytics. Japanese companies are at the forefront of this integration, continually exploring new ways to harness these technologies.
Artificial Intelligence and Machine Learning
Artificial Intelligence (AI) and Machine Learning (ML) are set to revolutionize HDC further. These technologies can predict maintenance needs, optimize operations, and enhance decision-making processes. Japanese manufacturers are investing in AI and ML to complement their HDC systems and gain a competitive advantage.
Sustainability and Environmental Impact
Sustainability is increasingly becoming a key consideration in manufacturing. HDC technology can contribute to more efficient use of resources, reduced waste, and lower energy consumption. Japanese firms are incorporating sustainability goals into their HDC strategies, ensuring that their innovation contributes positively to the environment.
Customization and Personalization
The demand for customized and personalized products is rising. HDC allows for greater flexibility in manufacturing processes to meet these demands. Japanese companies are leveraging HDC to offer more tailored solutions to their customers, distinguishing themselves in a crowded market.
Conclusion
High-Definition Controllers are revolutionizing the landscape of modern manufacturing. By enhancing precision, efficiency, and flexibility, these controllers offer significant advantages while also presenting certain challenges. Japanese manufacturers, known for their dedication to quality and innovation, are at the forefront of adopting and optimizing HDC technology.
Through effective supplier negotiations, embracing best practices, and continuous improvement, they are setting new benchmarks in manufacturing excellence. As the future of HDC unfolds with advancements in IoT, AI, and sustainability, Japan’s manufacturing sector is well-poised to lead the global industry into a new era of technological proficiency and operational superiority.
資料ダウンロード
QCD調達購買管理クラウド「newji」は、調達購買部門で必要なQCD管理全てを備えた、現場特化型兼クラウド型の今世紀最高の購買管理システムとなります。
ユーザー登録
調達購買業務の効率化だけでなく、システムを導入することで、コスト削減や製品・資材のステータス可視化のほか、属人化していた購買情報の共有化による内部不正防止や統制にも役立ちます。
NEWJI DX
製造業に特化したデジタルトランスフォーメーション(DX)の実現を目指す請負開発型のコンサルティングサービスです。AI、iPaaS、および先端の技術を駆使して、製造プロセスの効率化、業務効率化、チームワーク強化、コスト削減、品質向上を実現します。このサービスは、製造業の課題を深く理解し、それに対する最適なデジタルソリューションを提供することで、企業が持続的な成長とイノベーションを達成できるようサポートします。
オンライン講座
製造業、主に購買・調達部門にお勤めの方々に向けた情報を配信しております。
新任の方やベテランの方、管理職を対象とした幅広いコンテンツをご用意しております。
お問い合わせ
コストダウンが利益に直結する術だと理解していても、なかなか前に進めることができない状況。そんな時は、newjiのコストダウン自動化機能で大きく利益貢献しよう!
(Β版非公開)