- お役立ち記事
- Revolutionizing Japanese Manufacturing: The Role of mmWave Technology in the Future of Industry
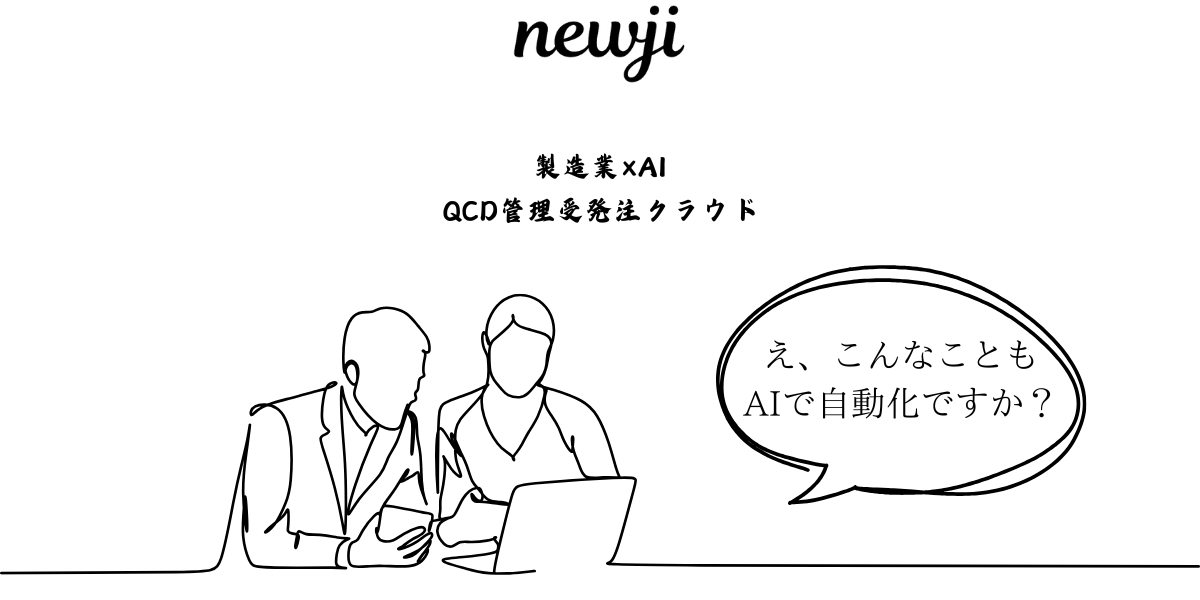
Revolutionizing Japanese Manufacturing: The Role of mmWave Technology in the Future of Industry
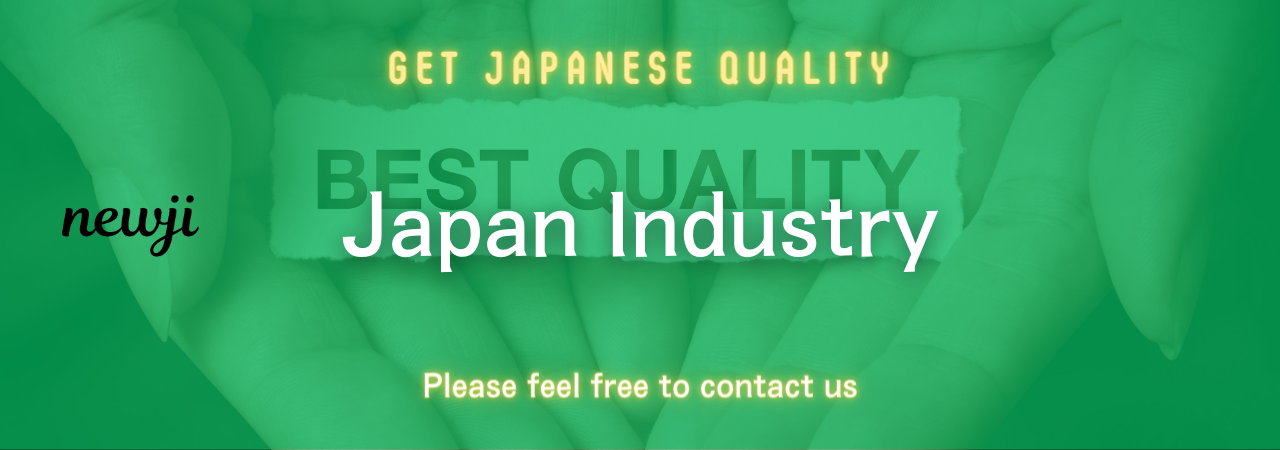
目次
Introduction to mmWave Technology in Manufacturing
The future of Japanese manufacturing stands at the cusp of a new era, driven by advancements in millimeter-wave (mmWave) technology. With its potential to dramatically enhance industrial processes, improve efficiency, and enable unprecedented innovation, mmWave is poised to redefine how industries operate and compete in a global marketplace. This article delves into the intricacies of mmWave technology, its application in manufacturing, and the opportunities it presents for procurement and purchasing professionals.
Understanding mmWave Technology
mmWave refers to the segment of the electromagnetic spectrum between 30 GHz and 300 GHz. These high-frequency waves can support a wide array of applications due to their ability to carry large amounts of data at extremely high speeds. However, they also exhibit limited range and are more susceptible to physical obstructions compared to lower frequency waves. These characteristics make mmWave technology a double-edged sword: full of potential but requiring precise application to be beneficial in industrial settings.
Key Characteristics and Benefits
Among the most notable advantages of mmWave technology is its high bandwidth capacity. This capability allows for the transmission of large amounts of data in real-time, crucial for applications such as high-definition video streaming, real-time analytics, and complex machine-to-machine communications.
Additionally, mmWave technology offers low latency, making it ideal for scenarios where immediate feedback or instantaneous data transmission is required. This is particularly beneficial in automation and robotics, where timely data is essential for operational efficiency.
Challenges and Limitations
Despite its advantages, mmWave technology also comes with its own set of challenges. One of the primary limitations is its poor penetration ability. Physical obstacles such as walls and even heavy rain can significantly degrade signal quality. This necessitates meticulous infrastructure planning and potentially higher investment in signal boosters and repeaters.
Furthermore, the technological complexity and higher cost associated with mmWave deployments can be prohibitive for some companies. This makes it essential for organizations to conduct thorough cost-benefit analyses and strategize the integration of mmWave with existing systems carefully.
Applications of mmWave Technology in Manufacturing
mmWave technology holds transformative potential for various facets of manufacturing, including production management, quality control, and factory automation. Below, we explore some key applications.
Enhanced Automation and Robotics
One of the most promising applications of mmWave technology in manufacturing is its use in enhancing automation and robotics. The low latency and high data transmission rates of mmWave enable real-time communication between machines, leading to more synchronized and efficient operations. For instance, robotic arms can receive live feedback from sensors, allowing them to make instantaneous adjustments and perform more complex tasks.
Smart Manufacturing and IoT
Integration of mmWave with the Internet of Things (IoT) can create a smarter, more connected factory environment. IoT devices equipped with mmWave communication capabilities can share data seamlessly, leading to smarter decision-making and predictive maintenance. For example, machines can communicate their operational status in real-time, alerting maintenance teams to potential issues before they lead to costly downtimes.
Quality Control and Inspection
In quality control, mmWave technology can be employed in advanced imaging and inspection systems. These systems can utilize high-frequency waves to detect minute defects in materials or finished products, ensuring higher quality standards. The high data rates also mean that inspection results can be processed and analyzed in near real-time, speeding up the quality control process.
Supplier Negotiation Techniques
Effective supplier negotiation is critical when integrating mmWave technology into your manufacturing processes. Here are some best practices to consider.
Understanding the Supplier’s Capabilities
Before entering negotiations, it’s crucial to thoroughly understand your supplier’s technological capabilities. Assess their experience with mmWave technology, their production capacity, and the quality of their products. This knowledge will empower you to negotiate better terms and ensure that the supplier can meet your technological and operational requirements.
Leveraging Cost-Benefit Analysis
Use detailed cost-benefit analyses to build your case during negotiations. Highlight how the integration of mmWave technology will lead to long-term cost savings and efficiency improvements. This approach can help in negotiating better pricing, favorable payment terms, or other concessions from the supplier.
Building Strategic Partnerships
Rather than viewing negotiations as a one-time transaction, aim to build long-term strategic partnerships with your suppliers. This approach fosters collaboration and can lead to mutual benefits such as shared R&D, exclusive supply agreements, and priority support. Strategic partnerships are particularly valuable in navigating the complexities and evolving nature of mmWave technology.
Market Conditions and Trends
Understanding the broader market conditions and trends related to mmWave technology can provide valuable insights for procurement and purchasing decisions.
Global Adoption and Investment
Globally, the adoption of mmWave technology is on the rise, driven by its potential in various high-tech applications. Significant investments in 5G infrastructure, where mmWave plays a crucial role, signal a growing market for this technology. Keeping an eye on global trends can help you anticipate shifts in supply and demand, allowing for more strategic procurement planning.
Regulatory Environment
The regulatory landscape for mmWave technology is evolving, with many countries establishing guidelines for spectrum usage. Understanding these regulations is essential for compliance and can influence your procurement strategy. For instance, securing frequency licenses or ensuring that your mmWave equipment meets local standards can prevent legal hurdles and operational disruptions.
Technological Advancements
Technological advancements continually shape the capabilities and applications of mmWave technology. Staying informed about the latest developments can help you make more informed purchasing decisions and ensure that you leverage the most current and effective solutions.
Best Practices for Implementing mmWave Technology
Successful integration of mmWave technology requires careful planning and execution. Here are some best practices to guide you.
Comprehensive Needs Assessment
Start with a thorough needs assessment to determine how mmWave technology can best serve your manufacturing processes. Identify specific pain points and operational goals that mmWave can address. This assessment will inform your procurement strategy and ensure that you invest in solutions that deliver tangible benefits.
Pilot Projects and Phased Implementation
Consider implementing pilot projects to test mmWave technology in specific areas of your production process. Pilot projects allow you to evaluate the technology’s performance and identify potential issues before a full-scale rollout. Based on the results, you can devise a phased implementation plan that minimizes disruptions and ensures a smooth transition.
Collaboration and Training
Collaboration with technology providers and suppliers is crucial for successful implementation. Work closely with these partners to tailor the technology to your specific needs and ensure seamless integration with existing systems. Additionally, invest in training for your staff to familiarize them with the new technology and maximize its benefits.
Continuous Monitoring and Optimization
Once implemented, continuously monitor the performance of mmWave technology in your operations. Use data analytics to track key performance indicators and identify areas for improvement. Regularly update your systems and processes to keep pace with technological advancements and evolving market conditions.
Conclusion
mmWave technology holds transformative potential for the future of Japanese manufacturing. From enhanced automation and IoT integration to advanced quality control systems, its applications are vast and impactful. However, realizing these benefits requires careful planning, strategic negotiations with suppliers, and an understanding of market conditions and trends.
By adopting best practices such as comprehensive needs assessments, pilot projects, and continuous optimization, manufacturing companies can successfully integrate mmWave technology into their operations. In doing so, they not only improve efficiency and productivity but also position themselves at the forefront of innovation, ready to compete in a rapidly evolving global market.
資料ダウンロード
QCD調達購買管理クラウド「newji」は、調達購買部門で必要なQCD管理全てを備えた、現場特化型兼クラウド型の今世紀最高の購買管理システムとなります。
ユーザー登録
調達購買業務の効率化だけでなく、システムを導入することで、コスト削減や製品・資材のステータス可視化のほか、属人化していた購買情報の共有化による内部不正防止や統制にも役立ちます。
NEWJI DX
製造業に特化したデジタルトランスフォーメーション(DX)の実現を目指す請負開発型のコンサルティングサービスです。AI、iPaaS、および先端の技術を駆使して、製造プロセスの効率化、業務効率化、チームワーク強化、コスト削減、品質向上を実現します。このサービスは、製造業の課題を深く理解し、それに対する最適なデジタルソリューションを提供することで、企業が持続的な成長とイノベーションを達成できるようサポートします。
オンライン講座
製造業、主に購買・調達部門にお勤めの方々に向けた情報を配信しております。
新任の方やベテランの方、管理職を対象とした幅広いコンテンツをご用意しております。
お問い合わせ
コストダウンが利益に直結する術だと理解していても、なかなか前に進めることができない状況。そんな時は、newjiのコストダウン自動化機能で大きく利益貢献しよう!
(Β版非公開)