- お役立ち記事
- Revolutionizing Japanese Manufacturing: The Role of Photoelectric Sensors and Switches
Revolutionizing Japanese Manufacturing: The Role of Photoelectric Sensors and Switches
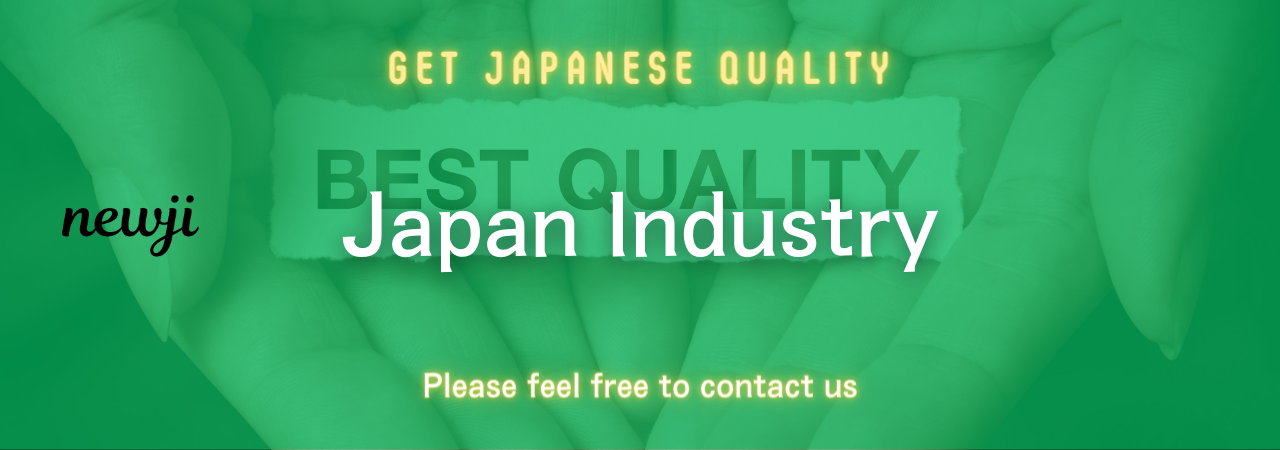
目次
Introduction
Japanese manufacturing has long been lauded for its precision, efficiency, and commitment to quality.
One of the key elements contributing to this success is the integration of advanced technologies like photoelectric sensors and switches.
These devices play a crucial role in enhancing production efficiency, ensuring quality control, and optimizing logistics.
In this article, we will explore the structural role of photoelectric sensors and switches in Japanese manufacturing, their advantages and disadvantages, supplier negotiation techniques, market conditions, and best practices.
The Importance of Photoelectric Sensors and Switches
Photoelectric sensors and switches are prominent in the automation and optimization processes in modern manufacturing.
These components are integral in detecting presence, absence, or changes in the physical properties of objects on the production line.
Enhancing Production Efficiency
In the realm of production management, photoelectric sensors offer unparalleled accuracy in detecting objects, ensuring that automation systems can perform tasks with high precision.
This, in turn, limits waste, reduces operational delays, and boosts overall productivity.
For example, in assembly lines, these sensors can detect the positioning of components, enabling robotic arms to perform tasks accurately, reducing human error.
Quality Control
Japanese manufacturing is synonymous with quality.
Photoelectric sensors and switches ensure that every product meets stringent quality standards.
By detecting defects or irregularities in real-time, these sensors make it possible to automate quality control.
For example, in the production of electronic devices, photoelectric sensors can inspect circuit boards for misalignments or missing components, ensuring only high-quality products leave the factory.
Optimizing Logistics and Inventory Management
In logistics and inventory management, photoelectric sensors are useful in tracking inventory levels precisely.
They help in monitoring the flow of goods in and out of warehouses, ensuring that inventory levels are accurately maintained.
This significantly reduces the risk of overstocking or stockouts, optimizing supply chain efficiency.
Advantages of Using Photoelectric Sensors and Switches in Manufacturing
Precision and Accuracy
The primary advantage of photoelectric sensors is their precision and accuracy.
These devices can detect very minute changes in the physical properties of objects, ensuring that production processes are carried out flawlessly.
Reliability
Photoelectric sensors are renowned for their durability and reliability.
They can function effectively in various environmental conditions such as dust, moisture, and varying temperatures.
This makes them highly reliable for continuous use in manufacturing environments.
Versatility
These sensors are versatile and can be used in various applications across different industries, from automotive to electronics manufacturing.
Their ability to adapt to different functions makes them a valuable asset in any manufacturing setup.
Cost-Effectiveness
Although the initial investment in photoelectric sensors and switches might be high, the long-term cost benefits are significant.
By improving production efficiency and reducing waste and defects, these sensors contribute to substantial cost savings over time.
Disadvantages of Using Photoelectric Sensors and Switches
Initial Cost
The initial investment for integrating photoelectric sensors and switches into the manufacturing process can be high.
This includes not only the cost of the sensors themselves but also the expenses related to installation, calibration, and employee training.
Maintenance Requirements
Consistent maintenance is crucial for ensuring that photoelectric sensors operate effectively.
Without regular upkeep, sensors may become misaligned or dirty, leading to inaccurate readings and potential production issues.
Complexity
The integration of these sensors into existing production systems can be complex.
It requires a deep understanding of both the technology and the specific requirements of the manufacturing process, making it essential to have skilled personnel on hand.
Potential Downtime
In the event of sensor failure, production processes may experience downtime, leading to delays and potential financial losses.
Having a contingency plan in place is critical to mitigate these risks.
Supplier Negotiation Techniques
Understanding Supplier Capabilities
Before entering negotiations, it’s crucial to understand the capabilities and limitations of potential suppliers.
This includes their production capacity, quality control standards, and how well they can meet your specific requirements.
Building Relationships
In Japan, building strong, long-term relationships with suppliers is often valued over short-term gains.
Fostering trust and demonstrating a commitment to mutual benefits can lead to better negotiation outcomes and more favorable terms.
Volume Leverage
Purchasing in larger volumes can often lead to significant discounts.
When negotiating with suppliers, emphasize your expected volume needs to secure better pricing and terms.
Quality Standards
Clearly define your quality standards and ensure that the supplier can meet them consistently.
This is crucial in maintaining the high level of quality associated with Japanese manufacturing.
Lead Time and Flexibility
Discuss lead times and the supplier’s ability to accommodate changes or rush orders.
Flexibility is important in maintaining a smooth production process, especially when demand fluctuates.
Current Market Conditions
Supply Chain Disruptions
Recent global events, such as the pandemic, have caused significant disruptions in supply chains.
Japanese manufacturers have had to adapt to these changes, emphasizing the need for reliable suppliers of photoelectric sensors and switches.
Technological Advancements
Rapid advancements in sensor technology continue to influence market conditions.
Manufacturers are increasingly seeking out the latest technologies to maintain a competitive edge.
Environmental Regulations
Stricter environmental regulations are impacting the materials and manufacturing processes used in producing photoelectric sensors.
This trend is pushing suppliers to adopt more sustainable practices, which can affect availability and cost.
Best Practices for Implementing Photoelectric Sensors and Switches
Integration Planning
Before implementation, thorough planning is essential.
This includes understanding your system’s requirements, selecting the appropriate sensors, and developing a detailed integration plan.
Training and Support
Ensure that your team is well-trained in the operation and maintenance of photoelectric sensors.
Continuous training and technical support from suppliers can greatly improve the effectiveness of these devices.
Regular Maintenance
Implement a regular maintenance schedule to ensure sensors remain in optimal working condition.
Regular cleaning, calibration, and inspection are crucial for avoiding disruptions.
Performance Monitoring
Consistently monitor the performance of sensors to detect any issues early.
This proactive approach can prevent minor problems from escalating into significant production interruptions.
Conclusion
Photoelectric sensors and switches are transforming Japanese manufacturing by enhancing efficiency, ensuring quality, and optimizing logistics.
While there are challenges associated with their implementation, the long-term benefits far outweigh the initial costs.
By leveraging the insights from this article, manufacturers can effectively integrate these technologies, negotiate with suppliers, and stay ahead in the competitive landscape.
Embracing these advancements will not only uphold the high standards of Japanese manufacturing but also pave the way for future innovations.
資料ダウンロード
QCD調達購買管理クラウド「newji」は、調達購買部門で必要なQCD管理全てを備えた、現場特化型兼クラウド型の今世紀最高の購買管理システムとなります。
ユーザー登録
調達購買業務の効率化だけでなく、システムを導入することで、コスト削減や製品・資材のステータス可視化のほか、属人化していた購買情報の共有化による内部不正防止や統制にも役立ちます。
NEWJI DX
製造業に特化したデジタルトランスフォーメーション(DX)の実現を目指す請負開発型のコンサルティングサービスです。AI、iPaaS、および先端の技術を駆使して、製造プロセスの効率化、業務効率化、チームワーク強化、コスト削減、品質向上を実現します。このサービスは、製造業の課題を深く理解し、それに対する最適なデジタルソリューションを提供することで、企業が持続的な成長とイノベーションを達成できるようサポートします。
オンライン講座
製造業、主に購買・調達部門にお勤めの方々に向けた情報を配信しております。
新任の方やベテランの方、管理職を対象とした幅広いコンテンツをご用意しております。
お問い合わせ
コストダウンが利益に直結する術だと理解していても、なかなか前に進めることができない状況。そんな時は、newjiのコストダウン自動化機能で大きく利益貢献しよう!
(Β版非公開)