- お役立ち記事
- “Revolutionizing Japanese Manufacturing: The Role of Serial Communication in Modern Production”
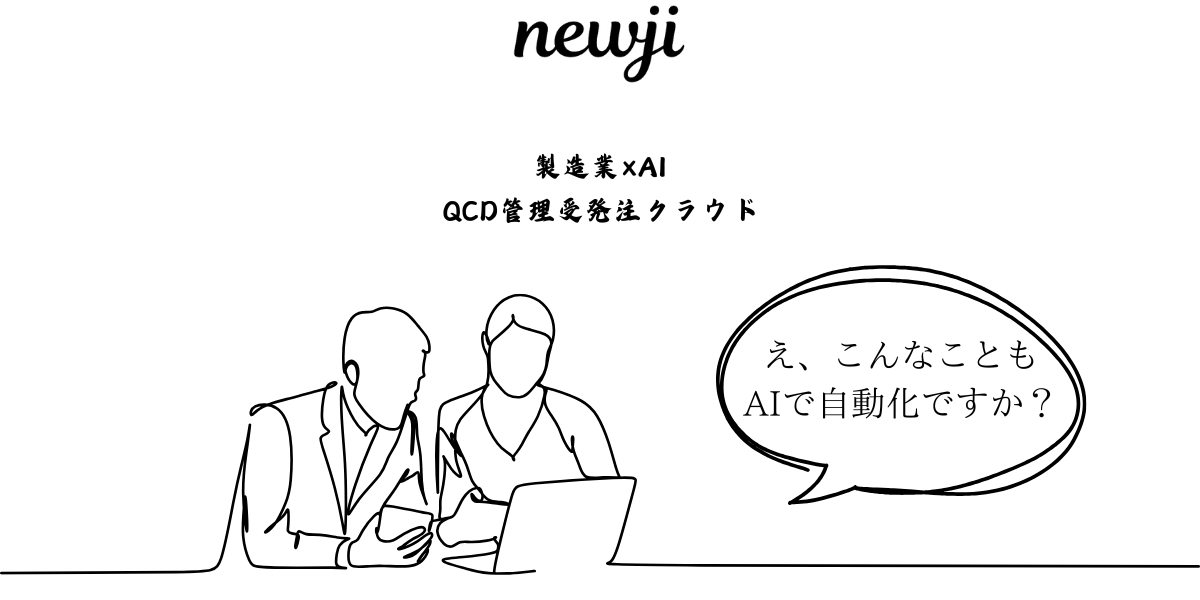
“Revolutionizing Japanese Manufacturing: The Role of Serial Communication in Modern Production”
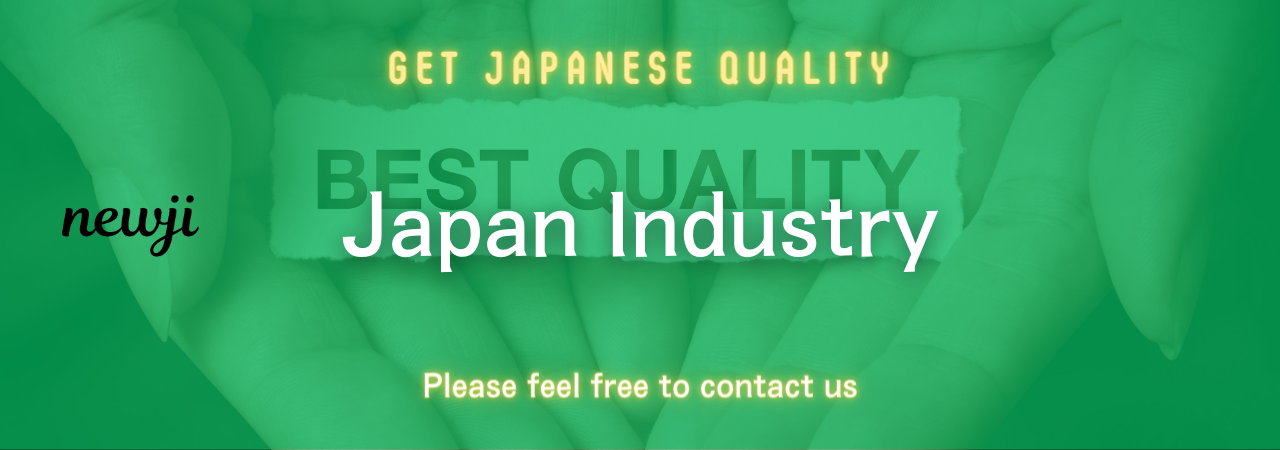
Serial communication has played a vital role in transforming modern production processes, especially in the realm of Japanese manufacturing. With a relentless pursuit of efficiency and precision, Japanese manufacturers have always embraced cutting-edge technologies to stay ahead of the curve. Serial communication, in particular, has provided a seamless method to transfer data between multiple devices in a production line, ushering in unprecedented levels of automation, control, and coordination. This article delves into the practical aspects of serial communication in Japanese manufacturing, exploring its advantages and disadvantages, best practices, and the current market conditions.
目次
Understanding Serial Communication
Serial communication is a method of transmitting data between devices using a serial protocol, which sends data one bit at a time over a communication channel. This contrasts with parallel communication, where multiple bits are transmitted simultaneously. Serial communication is particularly advantageous for long-distance data transfer and is widely utilized in industrial automation, where it ensures synchronization and accuracy.
Types of Serial Communication
There are several types of serial communication protocols, each catering to different requirements and applications:
– **RS-232:** Commonly used for short-distance communication.
– **RS-485:** Ideal for applications requiring longer distance and multi-drop communication.
– **USB (Universal Serial Bus):** Widely used for communication between computers and peripheral devices.
– **CAN (Controller Area Network) Bus:** Predominantly used in automotive and industrial applications for reliable, real-time communication.
– **Ethernet:** Though typically a network protocol, it is increasingly being used for real-time industrial communication.
Advantages of Serial Communication in Manufacturing
Japanese manufacturing has thrived on the back of several advantages provided by serial communication:
1. Enhanced Precision and Control
Serial communication protocols enable precise control over machinery and robotic systems by ensuring reliable and accurate data transfer. This leads to higher product quality and consistency.
2. Flexibility and Scalability
Serial communication systems can easily accommodate additional devices, allowing manufacturers to expand or modify production lines without significant overhauls. This flexibility is crucial for adapting to market changes or new product requirements.
3. Cost-Effectiveness
Implementing serial communication can be more cost-effective compared to parallel communication, especially for long-distance applications. Additionally, it often requires fewer physical connections, reducing wiring costs and simplifying maintenance.
4. Robustness and Reliability
Protocols such as CAN Bus and RS-485 are designed for robust performance in industrial environments, offering high resistance to electrical noise and ensuring reliable data transmission even in harsh conditions.
5. Integration with Automation Systems
Serial communication protocols seamlessly integrate with advanced automation systems, facilitating the use of sensors, actuators, and controllers to optimize production processes.
Disadvantages and Challenges
Despite its advantages, serial communication comes with its own set of challenges:
1. Data Transfer Speed
Compared to parallel communication, serial communication typically has lower data transfer speeds. This can be a constraint in applications requiring rapid data exchange.
2. Complexity in Implementation
Designing and implementing serial communication systems can be complex, requiring thorough planning and expertise to ensure compatibility and efficient data flow across all devices.
3. Limited Distance
While protocols like RS-485 support long-distance communication, others like RS-232 are limited to shorter ranges, necessitating the use of repeaters or advanced protocols for extensive setups.
4. Maintenance and Troubleshooting
Diagnosing issues in serial communication networks can be challenging, as problems may arise from multiple sources, including wiring, device compatibility, or protocol mismatches.
5. Initial Setup Costs
Although serial communication systems can be cost-effective in the long run, the initial setup costs, including hardware and integration, can be substantial.
Best Practices in Implementing Serial Communication
To harness the full potential of serial communication in manufacturing, it’s essential to adhere to best practices:
1. Conduct a Thorough Needs Assessment
Before implementing serial communication, assess the specific needs of your production line, including data transfer requirements, distance, and environmental conditions. This ensures the selection of the most suitable protocol and hardware.
2. Standardize Protocols
Standardizing on a few serial communication protocols across your production facilities can simplify maintenance, training, and integration with existing systems.
3. Invest in Quality Hardware
Opt for high-quality connectors, cables, and devices designed for industrial use. This investment pays off in terms of reliability and longevity, minimizing downtime and maintenance costs.
4. Ensure Proper Shielding and Grounding
Proper shielding and grounding of cables can significantly reduce electrical noise and signal interference, ensuring reliable data transmission.
5. Provide Adequate Training
Train your technical staff thoroughly on the implemented serial communication protocols and troubleshooting techniques. This is crucial for swift issue resolution and smooth operation.
6. Regular Monitoring and Maintenance
Implement regular monitoring of the communication network to detect and resolve issues proactively. Scheduled maintenance can prevent unexpected disruptions and extend the system’s lifespan.
Market Conditions and Trends
The market for serial communication technologies is continually evolving, driven by advancements in automation and industrial control systems:
1. Growing Demand for Industrial Automation
The increasing adoption of industrial automation is fueling the demand for reliable communication systems. Serial communication plays a pivotal role in connecting various automated devices, making it a cornerstone of modern manufacturing.
2. Integration with IoT and Industry 4.0
The advent of IoT and Industry 4.0 has highlighted the need for seamless data exchange between devices. Serial communication technologies are being integrated with IoT platforms to enable real-time data monitoring and analytics, enhancing decision-making and operational efficiency.
3. Emergence of Ethernet-Based Protocols
Ethernet-based serial communication protocols are gaining traction due to their high data transfer speeds and ability to handle complex industrial networks. Manufacturers are increasingly adopting Ethernet solutions to future-proof their production lines.
4. Investment in R&D
Manufacturers and technology providers are investing heavily in research and development to enhance the capabilities of serial communication protocols. Innovations in data transmission speeds, security, and compatibility are expected to drive the market forward.
Conclusion
Serial communication has undeniably revolutionized Japanese manufacturing, providing a robust, flexible, and cost-effective solution for data transfer in modern production environments. By understanding its advantages and challenges, and adhering to best practices, manufacturers can leverage serial communication to achieve heightened efficiency, precision, and control.
As market conditions continue to evolve with advancements in industrial automation and IoT, serial communication remains a critical component for any forward-thinking manufacturing enterprise. Adopting these technologies not only ensures competitiveness but also aligns with the continuous improvement ethos that is synonymous with Japanese manufacturing.
資料ダウンロード
QCD調達購買管理クラウド「newji」は、調達購買部門で必要なQCD管理全てを備えた、現場特化型兼クラウド型の今世紀最高の購買管理システムとなります。
ユーザー登録
調達購買業務の効率化だけでなく、システムを導入することで、コスト削減や製品・資材のステータス可視化のほか、属人化していた購買情報の共有化による内部不正防止や統制にも役立ちます。
NEWJI DX
製造業に特化したデジタルトランスフォーメーション(DX)の実現を目指す請負開発型のコンサルティングサービスです。AI、iPaaS、および先端の技術を駆使して、製造プロセスの効率化、業務効率化、チームワーク強化、コスト削減、品質向上を実現します。このサービスは、製造業の課題を深く理解し、それに対する最適なデジタルソリューションを提供することで、企業が持続的な成長とイノベーションを達成できるようサポートします。
オンライン講座
製造業、主に購買・調達部門にお勤めの方々に向けた情報を配信しております。
新任の方やベテランの方、管理職を対象とした幅広いコンテンツをご用意しております。
お問い合わせ
コストダウンが利益に直結する術だと理解していても、なかなか前に進めることができない状況。そんな時は、newjiのコストダウン自動化機能で大きく利益貢献しよう!
(Β版非公開)