- お役立ち記事
- Revolutionizing Japanese Manufacturing: The Role of Thermal Conductive Putty in Efficient Heat Management
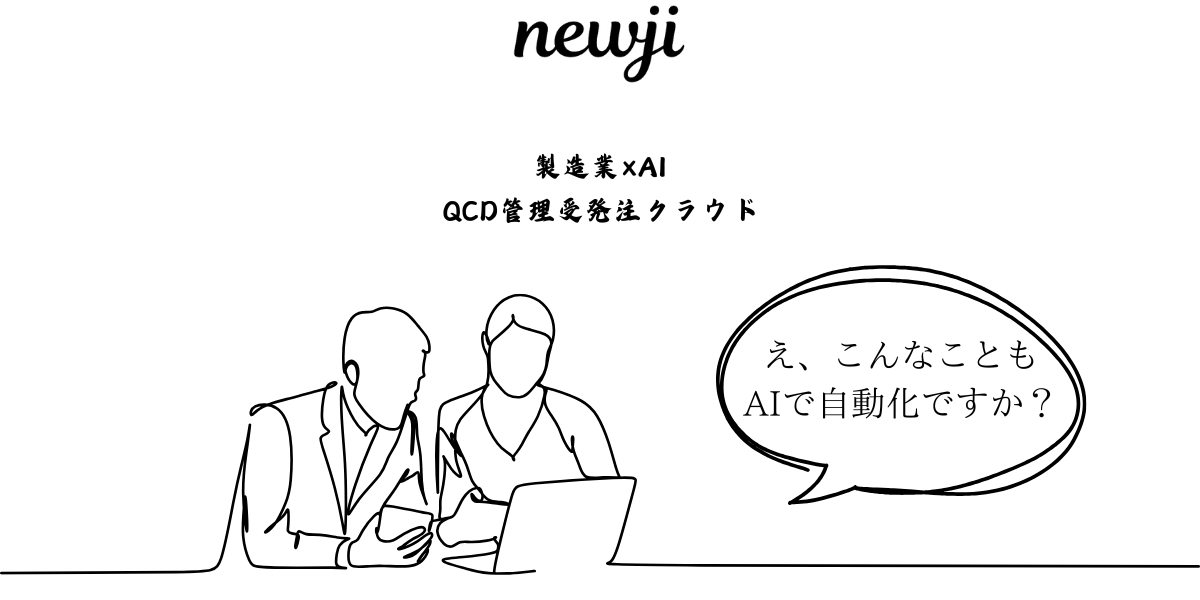
Revolutionizing Japanese Manufacturing: The Role of Thermal Conductive Putty in Efficient Heat Management
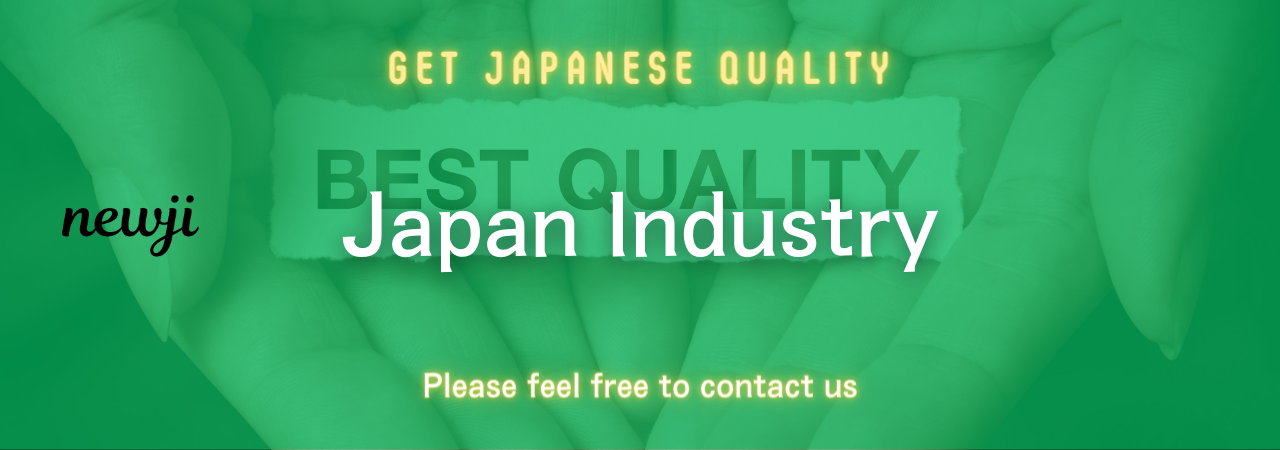
目次
Introduction to Thermal Conductive Putty in Japanese Manufacturing
In the competitive landscape of manufacturing, efficient heat management is pivotal for ensuring product reliability and performance. Japanese manufacturing has long been at the forefront of technological innovation, continually integrating advanced materials to enhance production processes. One such material making significant strides is thermal conductive putty. This versatile compound plays a crucial role in managing heat dissipation, thereby revolutionizing manufacturing practices across various industries.
The Importance of Heat Management
Effective heat management is essential in manufacturing for several reasons. Excessive heat can lead to equipment malfunction, reduced lifespan of components, and compromised product quality. By controlling temperature, manufacturers can ensure consistent performance, minimize downtime, and extend the durability of machinery and products. Thermal conductive putty offers a solution by facilitating efficient heat transfer, thereby maintaining optimal operating conditions.
Impact on Production Efficiency
Efficient heat dissipation directly correlates with production efficiency. Equipment that operates within ideal temperature ranges tends to perform better, reducing the likelihood of overheating and subsequent delays. Thermal conductive putty contributes to smoother operations by ensuring that heat is evenly distributed and dissipated, preventing hotspots that can cause equipment failures.
Enhancing Product Quality
Consistent temperature control is vital for maintaining product quality, especially in precision manufacturing. Variations in temperature can affect material properties, leading to defects and inconsistencies. By utilizing thermal conductive putty, manufacturers can achieve precise heat management, ensuring that products meet stringent quality standards.
Advantages of Thermal Conductive Putty in Manufacturing
The adoption of thermal conductive putty in manufacturing processes offers numerous benefits that enhance operational efficiency and product integrity.
Superior Thermal Conductivity
Thermal conductive putty provides excellent thermal conductivity, enabling efficient heat transfer between components. This property is essential for applications where rapid dissipation of heat is required to maintain system stability and performance.
Flexibility and Versatility
Unlike rigid thermal materials, putty maintains flexibility, allowing it to conform to irregular surfaces and accommodate thermal expansion and contraction. This adaptability makes it suitable for a wide range of applications, from electronics assembly to heavy machinery.
Ease of Application
Thermal conductive putty is user-friendly, requiring minimal preparation and application steps. Its pliable nature allows for easy spreading and coverage, reducing the time and effort needed for installation. This ease of use translates to cost savings and increased productivity on the manufacturing floor.
Enhanced Durability
High-quality thermal conductive putties are durable and resistant to environmental factors such as moisture, chemicals, and temperature fluctuations. This resilience ensures long-term performance, reducing the need for frequent replacements and maintenance.
Challenges and Considerations
While thermal conductive putty offers significant advantages, manufacturers must address certain challenges to optimize its effectiveness.
Material Compatibility
Ensuring compatibility between the putty and the substrates involved is critical. Incompatible materials can lead to poor adhesion, reduced thermal conductivity, and potential contamination. Manufacturers need to select putties that are specifically designed for their application materials to achieve the best results.
Application Techniques
Proper application is essential for maximizing the benefits of thermal conductive putty. Inadequate spreading or uneven coverage can compromise heat dissipation and lead to suboptimal performance. Training and standardized procedures are necessary to ensure consistent and effective application.
Cost Management
While thermal conductive putty can lead to long-term cost savings through improved efficiency and reduced maintenance, initial investment costs may be higher compared to traditional materials. Manufacturers must evaluate the return on investment and consider factors such as material costs, application time, and lifespan to make informed purchasing decisions.
Procurement and Purchasing Strategies
Effective procurement and purchasing strategies are vital for integrating thermal conductive putty into manufacturing processes successfully. Leveraging expertise in supplier negotiation and market analysis can yield significant benefits.
Supplier Evaluation
Selecting the right supplier is crucial for acquiring high-quality thermal conductive putty. Manufacturers should assess potential suppliers based on criteria such as product quality, reliability, financial stability, and compliance with industry standards. Building strong relationships with reputable suppliers ensures a consistent supply of superior materials.
Negotiation Techniques
Successful negotiation involves more than just securing the lowest price. Manufacturers should aim for value-driven agreements that consider factors like delivery schedules, payment terms, and after-sales support. Establishing clear communication and understanding mutual goals can lead to more favorable and sustainable contracts.
Market Analysis
Staying informed about market conditions is essential for strategic procurement. Understanding trends in supply and demand, pricing fluctuations, and technological advancements enables manufacturers to make proactive purchasing decisions. Regular market analysis helps in anticipating changes and adjusting procurement strategies accordingly.
Supply Chain Management
Integrating thermal conductive putty into the supply chain requires meticulous planning and coordination. Manufacturers should work closely with suppliers to ensure timely deliveries, maintain adequate inventory levels, and mitigate risks associated with supply disruptions. Implementing robust supply chain management practices enhances overall operational resilience.
Best Practices for Implementing Thermal Conductive Putty
Adopting best practices in the use of thermal conductive putty can significantly enhance its effectiveness and contribute to overall manufacturing excellence.
Standardized Application Procedures
Developing and adhering to standardized application procedures ensures consistency and reliability in heat management. Clear guidelines on surface preparation, putty application, curing times, and quality checks help maintain high standards across production batches.
Training and Skill Development
Investing in training programs for employees ensures that the workforce is skilled in applying thermal conductive putty correctly. Proper training reduces the risk of errors, enhances efficiency, and fosters a culture of quality and continuous improvement.
Quality Control and Testing
Implementing rigorous quality control measures is essential for verifying the performance of thermal conductive putty. Regular testing for thermal conductivity, adhesion strength, and durability ensures that the material meets the required specifications and contributes effectively to heat management.
Continuous Improvement
Manufacturers should adopt a mindset of continuous improvement, regularly reviewing and refining their use of thermal conductive putty. Gathering feedback from the production floor, monitoring performance metrics, and staying updated with technological advancements enable ongoing optimization of heat management practices.
Technological Advancements and Innovations
The field of thermal management is constantly evolving, with ongoing innovations enhancing the capabilities and applications of thermal conductive putty.
Material Enhancements
Advancements in material science have led to the development of putties with improved thermal conductivity, flexibility, and durability. Nanotechnology, for instance, enables the incorporation of nanoparticles that enhance heat transfer properties and overall performance.
Integration with Automation
Automated application systems are being integrated into manufacturing processes to ensure precise and consistent application of thermal conductive putty. Automation reduces manual labor, minimizes errors, and increases throughput, aligning with the goals of factory efficiency and productivity.
Sustainability Initiatives
Sustainability is a growing concern in manufacturing, prompting the development of eco-friendly thermal conductive putties. Manufacturers are increasingly seeking materials that are non-toxic, recyclable, and free from harmful chemicals, aligning with broader environmental goals and regulatory requirements.
Case Studies: Successful Implementation in Japanese Manufacturing
Examining real-world examples of thermal conductive putty implementation provides valuable insights into its practical applications and benefits.
Electronics Manufacturing
A leading electronics manufacturer in Japan integrated thermal conductive putty into their assembly process for high-performance semiconductor devices. By improving heat dissipation, they achieved higher device reliability and extended product life cycles. The implementation also reduced the incidence of thermal-related defects, enhancing overall product quality.
Automotive Industry
In the automotive sector, a major manufacturer employed thermal conductive putty in the production of electric vehicle components. Efficient heat management was critical for battery performance and safety. The use of putty facilitated better thermal regulation, contributing to improved battery longevity and vehicle performance.
Heavy Machinery Production
A Japanese heavy machinery manufacturer incorporated thermal conductive putty into their engine assembly process. Enhanced heat dissipation resulted in reduced engine wear and lower maintenance costs. The modification also allowed for more compact engine designs without compromising performance, providing a competitive edge in the market.
Future Outlook
The future of thermal conductive putty in Japanese manufacturing looks promising, with ongoing research and development poised to unlock new potential applications and enhancements.
Emerging Applications
As industries diversify and technology advances, new applications for thermal conductive putty are emerging. From renewable energy systems to advanced robotics, the versatility of putty makes it a valuable component in a wide array of cutting-edge technologies.
Integration with Smart Manufacturing
The rise of smart manufacturing and the Internet of Things (IoT) provide opportunities for integrating thermal conductive putty with intelligent systems. Sensors and monitoring tools can be combined with putty applications to provide real-time data on temperature management, enabling proactive adjustments and predictive maintenance.
Enhanced Performance Materials
Ongoing research aims to develop putties with even higher thermal conductivity, improved environmental resistance, and greater adaptability to diverse applications. These advancements will further strengthen the role of thermal conductive putty in efficient heat management and manufacturing excellence.
Conclusion
Thermal conductive putty is a transformative material in Japanese manufacturing, offering superior heat management capabilities that enhance production efficiency and product quality. By adopting strategic procurement and purchasing practices, addressing implementation challenges, and embracing best practices, manufacturers can leverage the full potential of thermal conductive putty. As technological advancements continue to evolve, the role of putty in efficient heat management will only become more integral, solidifying its position as a cornerstone of manufacturing innovation and excellence.
資料ダウンロード
QCD調達購買管理クラウド「newji」は、調達購買部門で必要なQCD管理全てを備えた、現場特化型兼クラウド型の今世紀最高の購買管理システムとなります。
ユーザー登録
調達購買業務の効率化だけでなく、システムを導入することで、コスト削減や製品・資材のステータス可視化のほか、属人化していた購買情報の共有化による内部不正防止や統制にも役立ちます。
NEWJI DX
製造業に特化したデジタルトランスフォーメーション(DX)の実現を目指す請負開発型のコンサルティングサービスです。AI、iPaaS、および先端の技術を駆使して、製造プロセスの効率化、業務効率化、チームワーク強化、コスト削減、品質向上を実現します。このサービスは、製造業の課題を深く理解し、それに対する最適なデジタルソリューションを提供することで、企業が持続的な成長とイノベーションを達成できるようサポートします。
オンライン講座
製造業、主に購買・調達部門にお勤めの方々に向けた情報を配信しております。
新任の方やベテランの方、管理職を対象とした幅広いコンテンツをご用意しております。
お問い合わせ
コストダウンが利益に直結する術だと理解していても、なかなか前に進めることができない状況。そんな時は、newjiのコストダウン自動化機能で大きく利益貢献しよう!
(Β版非公開)