- お役立ち記事
- Revolutionizing Japanese Manufacturing: The Role of TQM in Achieving Excellence
Revolutionizing Japanese Manufacturing: The Role of TQM in Achieving Excellence
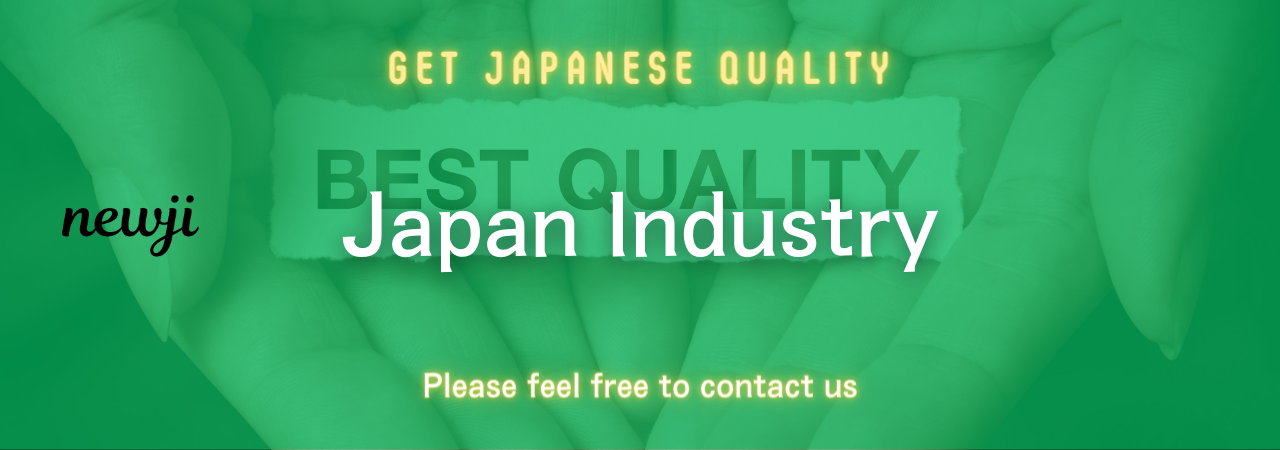
目次
Introduction to Total Quality Management (TQM)
Total Quality Management, or TQM, is a comprehensive management approach that focuses on long-term success through customer satisfaction.
In the context of Japanese manufacturing, TQM has been instrumental in fostering a culture of continuous improvement and operational excellence.
By integrating quality management into every facet of operations, Japanese companies have managed to reduce costs, enhance products, and remain competitive in global markets.
The Historical Context of TQM in Japan
The Genesis of TQM in Japan
The roots of TQM in Japan can be traced back to the post-World War II era.
Japanese industries were in desperate need of quality improvement to revive their economy.
Influenced by American quality experts like W. Edwards Deming and Joseph M. Juran, Japan adopted quality management principles that would later evolve into TQM.
These methodologies emphasized statistical quality control and the importance of worker participation in quality.
The Influence of Kaizen
Integral to TQM in Japan is the concept of Kaizen, which means “continuous improvement.”
Kaizen concentrates on small, incremental changes that steadily enhance processes and products.
This philosophy encourages every employee, from the CEO to the assembly-line worker, to focus on improving efficiency and effectiveness.
Core Principles of TQM in Japanese Manufacturing
Customer Focus
The central tenet of TQM is unwavering customer focus.
Japanese companies prioritize understanding customer needs and strive to exceed expectations.
Feedback loops are typically established to continuously gather customer insights and enhance satisfaction.
Total Employee Involvement
All employees are considered integral to the quality process.
Japanese companies involve workers at all levels in problem-solving initiatives and empower them to implement quality improvements.
This culture of ownership leads to higher morale and innovation.
Process-Centered Approach
TQM emphasizes a process-centered approach, wherein all work activities are viewed as processes with inputs, actions, and outputs.
Improvements to processes are systematically sought to enhance efficiency and reduce waste.
Integrated System
A critical component of TQM is integrating quality management across the entire organization.
Supply chain management, production, and quality assurance are interconnected to ensure coherence and efficiency.
Advantages of TQM in Japanese Manufacturing
Enhanced Product Quality
The implementation of TQM results in superior product quality due to consistent attention to detail and continuous quality checks.
This has enabled Japanese manufacturers to build a reputation for reliability and excellence.
Operational Efficiency
By optimizing processes and minimizing waste, TQM leads to significant improvements in operational efficiency.
Japanese manufacturers can achieve lower production costs while maintaining high standards.
Employee Satisfaction and Productivity
Employee participation in quality initiatives fosters a sense of responsibility and job satisfaction.
A motivated workforce translates into increased productivity and reduced turnover.
Competitive Advantage
TQM provides a competitive edge by differentiating products through quality.
Companies can leverage this to gain market share and improve profitability.
Challenges and Disadvantages of TQM
Implementation Complexity
Adopting TQM can be complex and resource-intensive, requiring a fundamental cultural shift within an organization.
This can be particularly challenging for companies lacking strong leadership or organizational commitment.
Resistance to Change
Employees may resist changes associated with TQM implementation, especially if they perceive it as threatening or unwelcome.
Overcoming resistance requires effective communication and training.
Initial Costs
The initial costs of implementing TQM, including training, process redesign, and system integration, can be substantial.
These costs may deter smaller companies from pursuing TQM.
Measurement and Monitoring
TQM necessitates rigorous measurement and monitoring of processes, which can be burdensome without the necessary infrastructure and expertise.
Supplier Negotiation Techniques with Japanese Manufacturers
Understanding Japanese Business Culture
Successful negotiations with Japanese suppliers require an understanding of their business culture, which emphasizes respect, patience, and harmony.
Building long-term relationships should be prioritized over short-term gains.
Emphasizing Quality over Price
Japanese suppliers value partners who prioritize quality over cost.
Demonstrating a commitment to quality improvement can lead to more favorable terms and collaborations.
Employing a Collaborative Approach
Negotiations should be approached collaboratively, reflecting a willingness to understand the supplier’s perspective.
This approach fosters mutual respect and trust, which are crucial in Japanese business dealings.
Due Diligence and Preparation
Thorough preparation is essential for successful negotiations.
Having a deep understanding of market conditions, supplier capabilities, and specific requirements can enhance credibility and influence negotiations.
Current Market Conditions for Japanese Manufacturing
Global Supply Chain Disruptions
Recent global events have caused significant disruptions in supply chains.
Japanese manufacturers have shown resilience by leveraging their lean manufacturing principles and supply chain agility to mitigate these impacts.
Growing Emphasis on Sustainability
Sustainability has become a major focal point for Japanese manufacturers.
Companies are investing in eco-friendly technologies and production practices to meet increasing global demand for sustainable products.
Technological Advancements
The integration of advanced technologies such as IoT, AI, and automation is transforming Japanese manufacturing.
These innovations are enabling companies to enhance precision, efficiency, and adaptability.
Best Practices in Implementing TQM in Japanese Manufacturing
Leadership Commitment
The commitment of top management is paramount in successfully implementing TQM.
Leadership must visibly support and promote a culture of quality throughout the organization.
Employee Training and Development
Continuous employee training is essential to equip staff with the skills necessary for quality improvement initiatives.
Development programs should be aligned with organizational goals and quality standards.
Customer Feedback Systems
Robust systems for collecting and responding to customer feedback are crucial for achieving customer satisfaction.
Feedback should be used to refine processes and align products with market needs.
Benchmarking and Continuous Improvement
Japanese companies conduct regular benchmarking against industry leaders to identify improvement areas.
By incorporating best practices and fostering an environment of continuous improvement, companies can ensure sustainable growth and competitiveness.
Conclusion
In conclusion, Total Quality Management has played a pivotal role in revolutionizing Japanese manufacturing industries.
By focusing on customer satisfaction, employee involvement, and process optimization, Japanese manufacturers have achieved unprecedented levels of quality and efficiency.
Despite challenges associated with TQM implementation, the benefits far outweigh the drawbacks when executed successfully.
As global market conditions evolve, Japanese companies must continue to adapt, leveraging TQM principles to maintain their competitive standing in the world of manufacturing.
資料ダウンロード
QCD調達購買管理クラウド「newji」は、調達購買部門で必要なQCD管理全てを備えた、現場特化型兼クラウド型の今世紀最高の購買管理システムとなります。
ユーザー登録
調達購買業務の効率化だけでなく、システムを導入することで、コスト削減や製品・資材のステータス可視化のほか、属人化していた購買情報の共有化による内部不正防止や統制にも役立ちます。
NEWJI DX
製造業に特化したデジタルトランスフォーメーション(DX)の実現を目指す請負開発型のコンサルティングサービスです。AI、iPaaS、および先端の技術を駆使して、製造プロセスの効率化、業務効率化、チームワーク強化、コスト削減、品質向上を実現します。このサービスは、製造業の課題を深く理解し、それに対する最適なデジタルソリューションを提供することで、企業が持続的な成長とイノベーションを達成できるようサポートします。
オンライン講座
製造業、主に購買・調達部門にお勤めの方々に向けた情報を配信しております。
新任の方やベテランの方、管理職を対象とした幅広いコンテンツをご用意しております。
お問い合わせ
コストダウンが利益に直結する術だと理解していても、なかなか前に進めることができない状況。そんな時は、newjiのコストダウン自動化機能で大きく利益貢献しよう!
(Β版非公開)