- お役立ち記事
- “Revolutionizing Japanese Manufacturing: The Role of Transport Robots and Delivery Robots”
月間77,185名の
製造業ご担当者様が閲覧しています*
*2025年2月28日現在のGoogle Analyticsのデータより
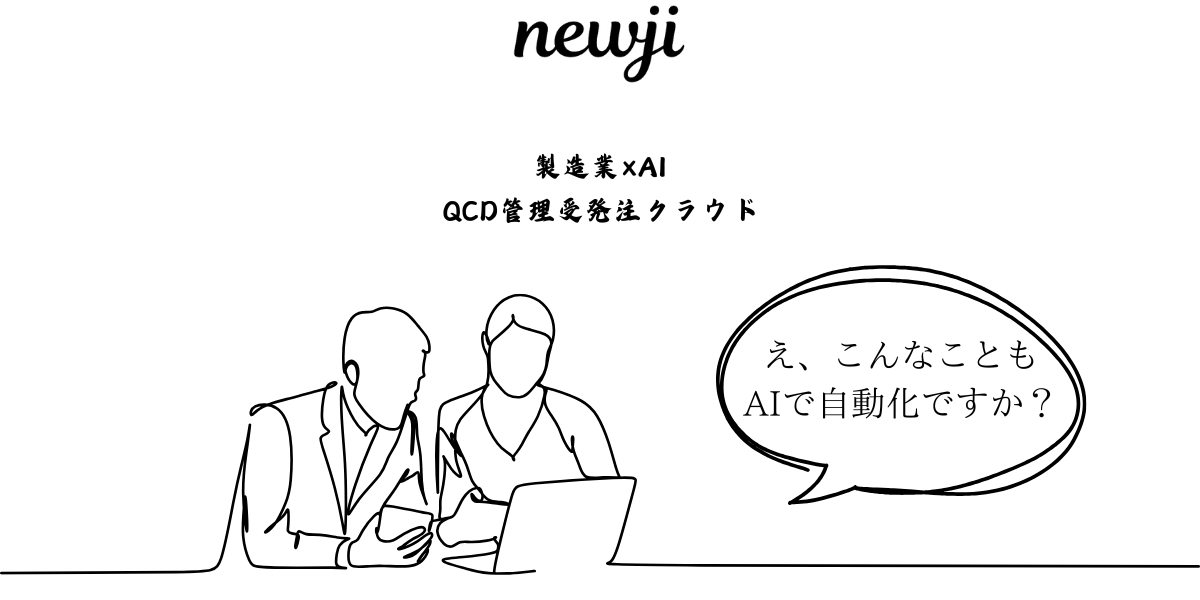
“Revolutionizing Japanese Manufacturing: The Role of Transport Robots and Delivery Robots”
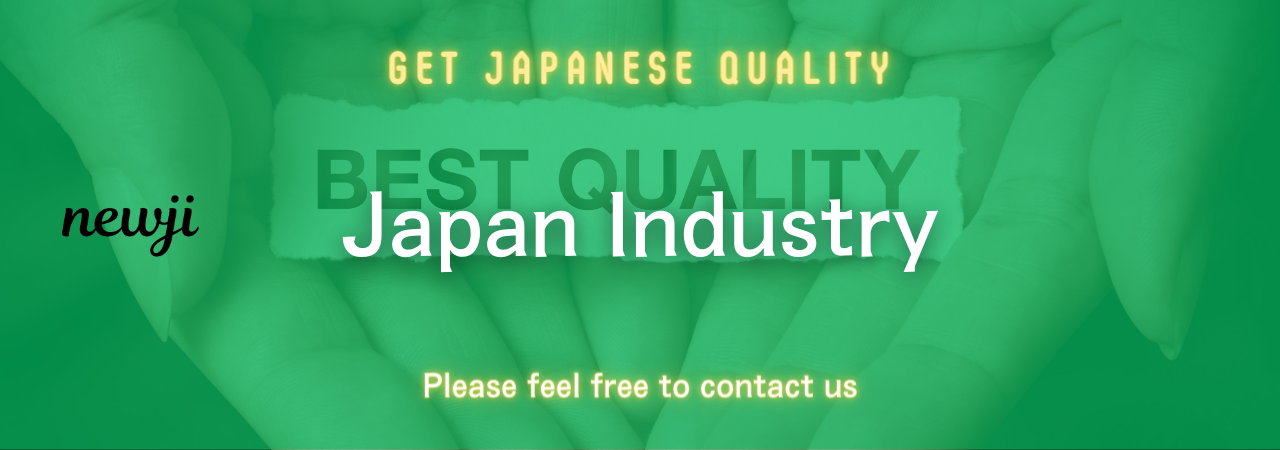
目次
Introduction to Japanese Manufacturing Innovation
Japanese manufacturing has long been synonymous with quality, precision, and innovation. In recent years, the integration of advanced robotics has further revolutionized this sector, enhancing efficiency and productivity. Transport robots and delivery robots, in particular, have emerged as pivotal components in modern manufacturing facilities. This article explores the transformative role of these robots, examining their advantages, challenges, and best practices for successful implementation.
The Rise of Transport Robots in Japanese Manufacturing
Transport robots have become integral to Japanese manufacturing processes, streamlining material movement and reducing human labor. These robots operate in various capacities, from moving raw materials to facilitating assembly line operations.
Types of Transport Robots
Transport robots come in several forms, each designed to meet specific operational needs. Automated Guided Vehicles (AGVs) are commonly used for transporting materials along predefined paths within factories. Autonomous Mobile Robots (AMRs), on the other hand, navigate more flexibly, adapting to dynamic environments without the need for fixed guides. Collaborative robots, or cobots, work alongside human workers, enhancing cooperation and efficiency on the production floor.
Benefits of Transport Robots
The integration of transport robots offers numerous benefits. They significantly increase operational efficiency by reducing the time and effort required to move materials manually. Robots operate tirelessly, ensuring consistent performance and minimizing downtime. Additionally, they enhance workplace safety by handling hazardous materials and reducing the risk of accidents associated with manual transport tasks.
Challenges in Deploying Transport Robots
Despite their advantages, deploying transport robots presents certain challenges. High initial investment costs can be a barrier for some manufacturers. Integrating robots with existing systems requires careful planning and technical expertise. Furthermore, there may be resistance from employees concerned about job displacement, necessitating comprehensive training and change management strategies.
Delivery Robots: Enhancing Manufacturing Logistics
Delivery robots play a crucial role in optimizing logistics within manufacturing settings. They ensure timely delivery of components and products, maintaining the seamless flow of the production process.
Operational Advantages of Delivery Robots
Delivery robots enhance logistical operations by providing precise and timely delivery of materials. They can operate continuously without breaks, significantly increasing the throughput of manufacturing processes. These robots also reduce human error, ensuring that materials are delivered to the correct locations efficiently.
Integration with Existing Systems
Successful integration of delivery robots with existing manufacturing systems is essential for maximizing their benefits. This involves ensuring compatibility with inventory management software, production schedules, and other operational protocols. Effective integration enables real-time monitoring and coordination, facilitating a more responsive and adaptive manufacturing environment.
Limitations of Delivery Robots
While delivery robots offer substantial benefits, they also have limitations. Navigating complex or cluttered environments can be challenging, potentially reducing their efficiency. Additionally, maintenance and technical support are critical to prevent downtime, requiring ongoing investment and expertise.
Supplier Negotiation Techniques for Robotics Procurement
Procuring transport and delivery robots involves strategic negotiations with suppliers. Effective negotiation techniques are essential to secure favorable terms and ensure successful implementation.
Understanding Supplier Capabilities
A thorough understanding of supplier capabilities is paramount. This includes assessing their technological expertise, production capacity, and reliability. Evaluating a supplier’s track record and reputation in the market helps in making informed decisions and fostering long-term partnerships.
Building Strong Partnerships
Building strong partnerships with suppliers fosters collaboration and innovation. Engaging in transparent communication, sharing goals, and aligning interests create a conducive environment for mutual growth. Strong partnerships can lead to customized solutions tailored to specific manufacturing needs.
Negotiation Tactics
Effective negotiation tactics include leveraging competitive bids to secure better pricing and terms. Negotiators should also focus on value-added services, such as training and support, which enhance the overall value proposition. Establishing clear contractual agreements that outline responsibilities, timelines, and performance metrics is crucial for avoiding disputes and ensuring successful deployment.
Market Conditions Influencing Robotics Adoption
Several market conditions influence the adoption of transport and delivery robots in Japanese manufacturing, including technological advancements, economic factors, and labor market dynamics.
Technological Advancements
Rapid advancements in robotics technology have made transport and delivery robots more capable and affordable. Innovations in artificial intelligence, machine learning, and sensor technologies have enhanced the functionality and adaptability of these robots, making them more suitable for diverse manufacturing environments.
Economic Factors
Economic conditions play a significant role in robotics adoption. Favorable economic growth and investment climates encourage manufacturers to invest in robotics to boost productivity and competitiveness. Conversely, economic downturns may limit the availability of capital for such investments, slowing down adoption rates.
Labor Market Dynamics
Labor market dynamics, including labor shortages and rising labor costs, drive the demand for automation solutions like transport and delivery robots. In regions where skilled labor is scarce, robots offer a viable alternative to maintain production levels and quality standards.
Best Practices for Implementing Transport and Delivery Robots
Implementing transport and delivery robots effectively requires careful planning and adherence to best practices. These practices ensure that the integration of robots enhances manufacturing operations without disrupting existing workflows.
Planning and Strategy
Successful implementation begins with comprehensive planning and strategic alignment. Manufacturers should define clear objectives, assess current processes, and identify areas where robots can add the most value. Developing a roadmap that outlines the stages of implementation helps in managing resources and timelines effectively.
Infrastructure Readiness
Ensuring infrastructure readiness is critical for the seamless integration of robots. This includes having the necessary physical space, power supply, and network connectivity to support robot operations. Upgrading infrastructure to meet the technical requirements of advanced robotics can prevent operational disruptions and enhance performance.
Employee Training and Adaptation
Employee training is essential to facilitate the effective use of transport and delivery robots. Providing comprehensive training programs helps employees understand how to operate and collaborate with robots, reducing resistance to change. Cultivating a culture of continuous learning and adaptation ensures that the workforce remains competent and motivated in a technologically evolving environment.
Advantages and Disadvantages of Transport and Delivery Robots
Transport and delivery robots offer numerous advantages, but they also come with certain disadvantages that manufacturers must consider.
Advantages
Transport and delivery robots significantly enhance operational efficiency by automating repetitive tasks, freeing up human workers for more complex and value-added activities. They improve accuracy and consistency in material handling, reducing errors and waste. Moreover, robots contribute to a safer workplace by handling hazardous materials and minimizing the physical strain on employees.
Disadvantages
Despite their benefits, robots come with drawbacks. High initial costs and ongoing maintenance expenses can strain budgets, particularly for smaller manufacturers. The integration process can be complex and time-consuming, requiring specialized skills and knowledge. Additionally, there is the potential for job displacement, which can lead to workforce dissatisfaction and require careful management of human-robot collaboration.
Case Studies: Successful Implementation in Japanese Manufacturing
Examining real-world case studies provides valuable insights into the successful implementation of transport and delivery robots in Japanese manufacturing.
Automotive Manufacturing
In the automotive sector, transport robots have been deployed to move heavy components between assembly lines. This has led to a significant reduction in production time and improved the overall efficiency of the manufacturing process. The successful integration of robots with existing manufacturing systems has enhanced the flexibility and responsiveness of production operations.
Electronics Manufacturing
Electronics manufacturers have utilized delivery robots to manage the intricate logistics of small and sensitive components. The precision and reliability of these robots have minimized errors and ensured timely delivery, supporting the high standards of quality expected in the electronics industry.
Food and Beverage Manufacturing
In the food and beverage industry, delivery robots have been instrumental in handling perishable goods. Their ability to operate in controlled environments and maintain consistent temperatures has ensured the integrity and safety of food products during transport.
Future Trends in Robotics for Manufacturing
The future of transport and delivery robots in manufacturing is poised for continued growth and innovation. Emerging trends will further enhance their capabilities and integration within manufacturing ecosystems.
Artificial Intelligence and Machine Learning
Advancements in artificial intelligence and machine learning will enable robots to become more autonomous and adaptable. These technologies will allow robots to learn from their environments, optimize their tasks, and make real-time adjustments to improve efficiency and effectiveness.
Internet of Things (IoT) Integration
Integration with the Internet of Things will facilitate seamless communication between robots and other connected devices within the manufacturing environment. This will enable real-time data exchange, predictive maintenance, and enhanced coordination, leading to smarter and more responsive manufacturing systems.
Collaborative Robotics
The development of more sophisticated collaborative robots will enhance human-robot interactions on the production floor. These robots will work alongside human employees, sharing tasks and responsibilities, thereby increasing overall productivity and fostering a more harmonious working environment.
Overcoming Challenges in Robotics Adoption
While the benefits of transport and delivery robots are substantial, overcoming the associated challenges is crucial for successful adoption.
Cost Management
Managing the costs associated with robot procurement and maintenance is essential. Manufacturers can explore financing options, seek government incentives, and conduct thorough cost-benefit analyses to justify the investment. Additionally, seeking scalable solutions that can grow with the business can help in managing expenses effectively.
Technical Support and Maintenance
Ensuring adequate technical support and maintenance is critical to prevent operational disruptions. Establishing relationships with reliable suppliers and having in-house technical expertise can facilitate timely troubleshooting and maintenance, ensuring that robots operate efficiently and reliably.
Workforce Adaptation
Facilitating workforce adaptation involves addressing employee concerns and providing training programs to equip them with the necessary skills to work alongside robots. Creating a culture that embraces technological advancements and promotes continuous learning can enhance employee acceptance and collaboration with robotic systems.
Regulatory and Ethical Considerations
The adoption of transport and delivery robots in manufacturing also entails regulatory and ethical considerations that manufacturers must address.
Compliance with Regulations
Manufacturers must ensure that their use of robots complies with local and international regulations regarding safety, data privacy, and labor standards. Adhering to these regulations not only ensures legal compliance but also promotes safe and ethical use of robotics in the workplace.
Ethical Implications
The ethical implications of robotics adoption, particularly concerning job displacement and worker welfare, require careful consideration. Manufacturers should engage in transparent communication with employees, explore opportunities for reskilling, and implement measures that balance automation with job creation to foster a responsible and sustainable approach to robotics integration.
Conclusion: The Future of Robotics in Japanese Manufacturing
Transport and delivery robots are transforming Japanese manufacturing, driving efficiency, precision, and innovation. While challenges such as cost, integration, and workforce adaptation exist, the benefits they offer in terms of operational excellence and competitive advantage are undeniable. By adhering to best practices, fostering strong supplier partnerships, and addressing regulatory and ethical considerations, manufacturers can successfully harness the power of robotics. As technology continues to advance, the role of transport and delivery robots is set to become even more integral, shaping the future landscape of Japanese manufacturing.
資料ダウンロード
QCD管理受発注クラウド「newji」は、受発注部門で必要なQCD管理全てを備えた、現場特化型兼クラウド型の今世紀最高の受発注管理システムとなります。
ユーザー登録
受発注業務の効率化だけでなく、システムを導入することで、コスト削減や製品・資材のステータス可視化のほか、属人化していた受発注情報の共有化による内部不正防止や統制にも役立ちます。
NEWJI DX
製造業に特化したデジタルトランスフォーメーション(DX)の実現を目指す請負開発型のコンサルティングサービスです。AI、iPaaS、および先端の技術を駆使して、製造プロセスの効率化、業務効率化、チームワーク強化、コスト削減、品質向上を実現します。このサービスは、製造業の課題を深く理解し、それに対する最適なデジタルソリューションを提供することで、企業が持続的な成長とイノベーションを達成できるようサポートします。
製造業ニュース解説
製造業、主に購買・調達部門にお勤めの方々に向けた情報を配信しております。
新任の方やベテランの方、管理職を対象とした幅広いコンテンツをご用意しております。
お問い合わせ
コストダウンが利益に直結する術だと理解していても、なかなか前に進めることができない状況。そんな時は、newjiのコストダウン自動化機能で大きく利益貢献しよう!
(β版非公開)