- お役立ち記事
- Revolutionizing Japanese Manufacturing: The Role of Water Jet Cutting OEM Processing in Precision Engineering
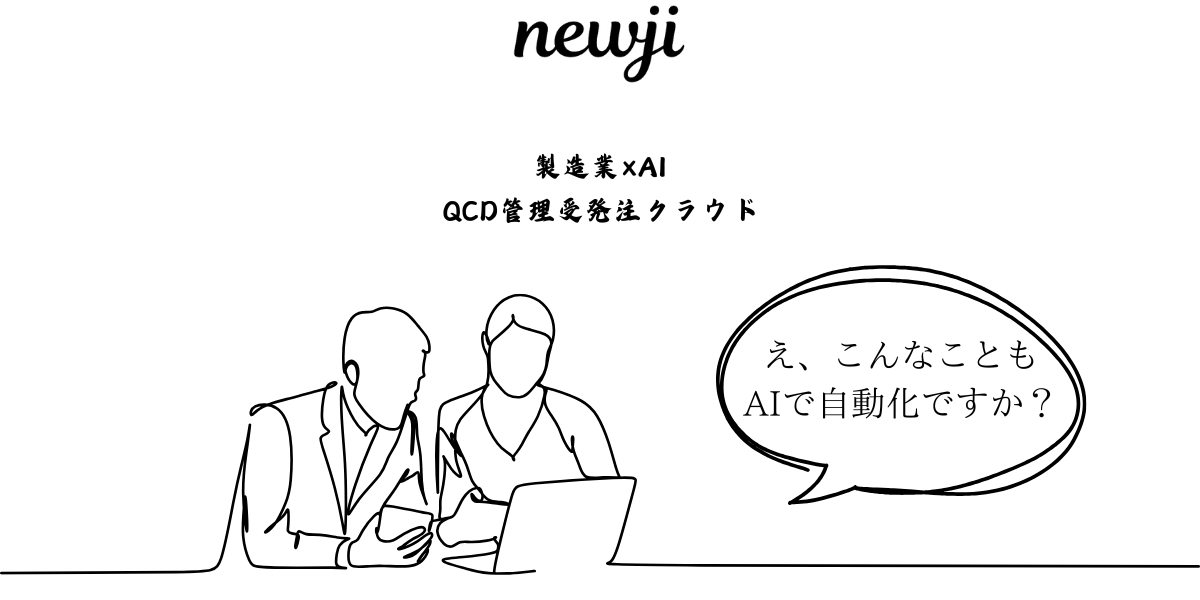
Revolutionizing Japanese Manufacturing: The Role of Water Jet Cutting OEM Processing in Precision Engineering
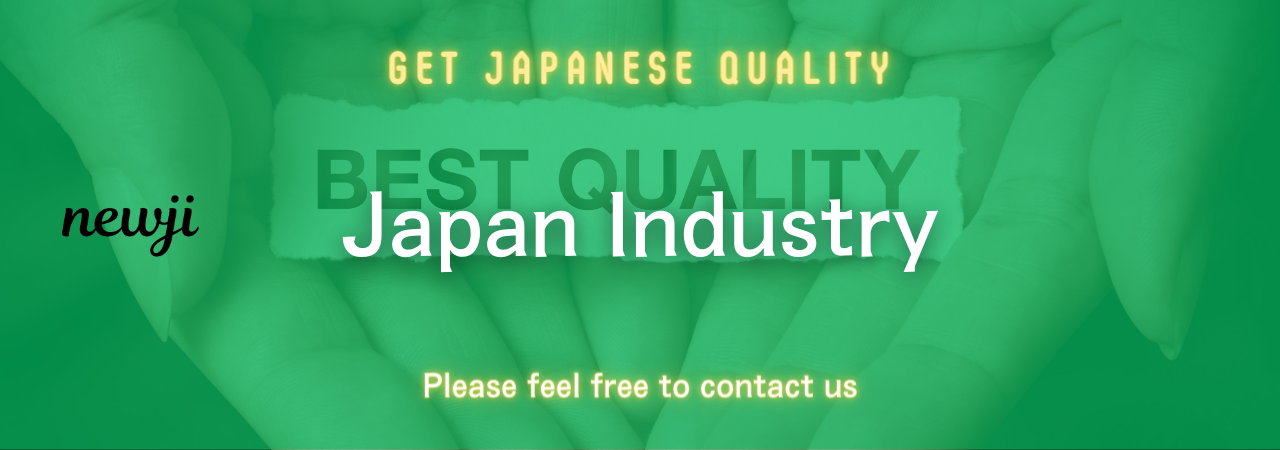
目次
Introduction to Water Jet Cutting in Japanese Manufacturing
Water jet cutting technology has become a cornerstone in modern Japanese manufacturing, particularly within the realm of precision engineering.
Its ability to deliver high-precision cuts without introducing thermal stresses makes it indispensable for complex manufacturing processes.
This article explores the pivotal role of Water Jet Cutting OEM processing in revolutionizing Japanese manufacturing, with a focus on procurement and purchasing perspectives.
Understanding Water Jet Cutting OEM Processing
What is Water Jet Cutting?
Water jet cutting is a fabrication process that uses a high-pressure stream of water, or a mixture of water and an abrasive substance, to cut materials.
Unlike traditional cutting methods, it does not generate heat, preserving the material’s integrity and reducing the risk of warping or melting.
This makes it ideal for precision engineering applications where accuracy and material properties are paramount.
OEM Processing in Water Jet Cutting
Original Equipment Manufacturer (OEM) processing refers to the outsourcing of production processes to specialized manufacturers.
In the context of water jet cutting, OEM processing allows companies to leverage specialized expertise and advanced technology without investing heavily in in-house equipment.
This collaboration enables manufacturers to maintain high-quality standards while optimizing costs and improving efficiency.
The Advantages of Water Jet Cutting in Precision Engineering
Enhanced Precision and Accuracy
Water jet cutting offers unparalleled precision, capable of achieving tolerances as tight as ±0.001 inches.
This level of accuracy is crucial in industries such as aerospace, automotive, and electronics, where component precision directly impacts performance and reliability.
Material Versatility
Water jets can cut a wide range of materials, including metals, ceramics, glass, composites, and even some hard plastics.
This versatility allows manufacturers to process diverse materials using a single cutting method, streamlining production and reducing the need for multiple specialized tools.
Minimal Material Waste
The narrow kerf width of water jet cutting minimizes material waste, contributing to cost savings and sustainable manufacturing practices.
Additionally, the lack of heat-affected zones preserves the material’s properties, reducing the need for secondary processing.
No Mechanical Stress
Since water jet cutting is a cold cutting process, it does not induce mechanical stress or alter the material’s microstructure.
This ensures that the final product maintains its structural integrity and performance characteristics.
Challenges and Considerations
Initial Investment and Operational Costs
While OEM processing can mitigate upfront costs, water jet cutting technology itself requires significant investment.
High-pressure pumps, abrasive delivery systems, and maintenance of specialized equipment contribute to ongoing operational expenses.
Material Limitations
Although water jet cutting is versatile, certain materials, such as thick titanium plates or highly abrasive composites, can pose challenges.
Manufacturers must assess material compatibility and potentially invest in specialized nozzles or abrasives to address these limitations.
Surface Finish and Tolerance Management
Achieving desired surface finishes and maintaining tight tolerances requires precise control over cutting parameters.
Variations in water pressure, abrasive flow rates, and nozzle condition can affect the quality of the cut, necessitating rigorous process monitoring and quality control measures.
Procurement and Purchasing Strategies
Supplier Selection and Evaluation
Selecting the right OEM partner is critical for successful water jet cutting integration.
Factors to consider include the supplier’s technological capabilities, experience in precision engineering, quality certifications, and ability to meet delivery schedules.
Conducting thorough supplier evaluations and site visits can provide insights into their operational standards and reliability.
Cost-Benefit Analysis
A comprehensive cost-benefit analysis helps in determining the financial viability of outsourcing water jet cutting.
This analysis should include equipment costs, maintenance expenses, labor costs, and potential savings from reduced material waste and improved production efficiency.
Long-Term Partnership and Collaboration
Building long-term relationships with OEM suppliers fosters collaboration and continuous improvement.
Engaging suppliers in joint research and development initiatives can lead to innovation, enhanced process capabilities, and mutual growth.
Supplier Negotiation Techniques
Understanding Supplier Capabilities
A deep understanding of a supplier’s technological strengths and limitations is essential for effective negotiation.
This knowledge allows buyers to set realistic expectations, identify areas for collaboration, and leverage supplier expertise to achieve desired outcomes.
Value-Based Negotiation
Instead of focusing solely on price, value-based negotiation emphasizes the overall value delivered by the supplier.
This includes factors such as quality, reliability, technical support, and flexibility.
By highlighting the importance of these elements, buyers can negotiate more favorable terms that align with their strategic objectives.
Performance Metrics and SLAs
Establishing clear performance metrics and Service Level Agreements (SLAs) ensures accountability and sets standards for supplier performance.
Key metrics may include on-time delivery rates, quality defect rates, response times, and compliance with regulatory requirements.
Regular performance reviews based on these metrics facilitate continuous improvement and address any issues proactively.
Market Conditions and Trends
Technological Advancements
The water jet cutting industry is witnessing rapid technological advancements, including improvements in pump efficiency, nozzle design, and automation integration.
Staying abreast of these developments enables manufacturers to leverage the latest technology for enhanced performance and competitiveness.
Global Supply Chain Dynamics
Global supply chain disruptions, such as those caused by geopolitical tensions or pandemics, impact the availability and cost of water jet cutting services.
Diversifying supplier bases and developing robust supply chain strategies can mitigate risks and ensure continuity in production processes.
Sustainability and Environmental Considerations
There is a growing emphasis on sustainable manufacturing practices, including the use of eco-friendly abrasives and water recycling systems in water jet cutting.
Adopting these practices not only aligns with environmental regulations but also appeals to environmentally conscious consumers and stakeholders.
Best Practices in Water Jet Cutting Procurement
Comprehensive Requirement Analysis
Conducting a thorough analysis of cutting requirements, including material types, thicknesses, tolerances, and production volumes, ensures that the selected OEM can meet specific needs.
This analysis informs the procurement strategy and helps in identifying suitable suppliers with the requisite capabilities.
Integrated Quality Management
Implementing an integrated quality management system that includes inspection protocols, feedback loops, and continuous improvement initiatives ensures consistent product quality.
Collaborating with suppliers to align quality standards and processes enhances overall manufacturing excellence.
Leveraging Technology and Data Analytics
Utilizing advanced technologies, such as IoT-enabled monitoring systems and data analytics, can optimize water jet cutting processes.
These tools provide real-time insights into operational performance, predictive maintenance needs, and opportunities for process optimization.
Case Studies: Success Stories in Japanese Manufacturing
Aerospace Component Manufacturing
A leading Japanese aerospace manufacturer partnered with a specialized water jet cutting OEM to produce high-precision turbine components.
By integrating water jet cutting into their production line, they achieved improved dimensional accuracy, reduced material waste, and accelerated production timelines, resulting in significant cost savings and enhanced product performance.
Automotive Industry Advancements
An automotive supplier collaborated with an OEM water jet cutting provider to develop lightweight, high-strength components for electric vehicles.
The precise cutting capabilities enabled the manufacturer to utilize advanced composite materials efficiently, contributing to overall vehicle performance and sustainability goals.
Future Outlook and Opportunities
Automation and Smart Manufacturing
The integration of automation and smart technologies in water jet cutting processes presents opportunities for increased efficiency, reduced labor costs, and enhanced precision.
Smart manufacturing systems can enable real-time monitoring, adaptive control, and predictive maintenance, driving continuous improvement and operational excellence.
Expansion into New Markets
As industries such as renewable energy, medical devices, and advanced electronics grow, the demand for precision-engineered components produced through water jet cutting is expected to rise.
Japanese manufacturers can capitalize on these emerging markets by leveraging their expertise and strategic partnerships with OEM water jet cutting providers.
Innovation in Material Processing
Continued innovation in material science and processing techniques will expand the capabilities of water jet cutting.
Developments such as precision multi-axis cutting and hybrid processes combining water jet cutting with other fabrication methods will enhance the versatility and applicability of this technology in complex engineering applications.
Conclusion
Water jet cutting OEM processing plays a transformative role in Japanese precision engineering, offering significant advantages in terms of precision, material versatility, and efficiency.
By adopting strategic procurement and purchasing practices, manufacturers can effectively collaborate with OEM partners to harness the full potential of water jet cutting technology.
As the manufacturing landscape evolves, embracing technological advancements and best practices will be essential for maintaining competitiveness and driving innovation in Japanese manufacturing.
資料ダウンロード
QCD調達購買管理クラウド「newji」は、調達購買部門で必要なQCD管理全てを備えた、現場特化型兼クラウド型の今世紀最高の購買管理システムとなります。
ユーザー登録
調達購買業務の効率化だけでなく、システムを導入することで、コスト削減や製品・資材のステータス可視化のほか、属人化していた購買情報の共有化による内部不正防止や統制にも役立ちます。
NEWJI DX
製造業に特化したデジタルトランスフォーメーション(DX)の実現を目指す請負開発型のコンサルティングサービスです。AI、iPaaS、および先端の技術を駆使して、製造プロセスの効率化、業務効率化、チームワーク強化、コスト削減、品質向上を実現します。このサービスは、製造業の課題を深く理解し、それに対する最適なデジタルソリューションを提供することで、企業が持続的な成長とイノベーションを達成できるようサポートします。
オンライン講座
製造業、主に購買・調達部門にお勤めの方々に向けた情報を配信しております。
新任の方やベテランの方、管理職を対象とした幅広いコンテンツをご用意しております。
お問い合わせ
コストダウンが利益に直結する術だと理解していても、なかなか前に進めることができない状況。そんな時は、newjiのコストダウン自動化機能で大きく利益貢献しよう!
(Β版非公開)