- お役立ち記事
- “Revolutionizing Japanese Manufacturing: The Six Sigma Approach to Perfection”
月間76,176名の
製造業ご担当者様が閲覧しています*
*2025年3月31日現在のGoogle Analyticsのデータより
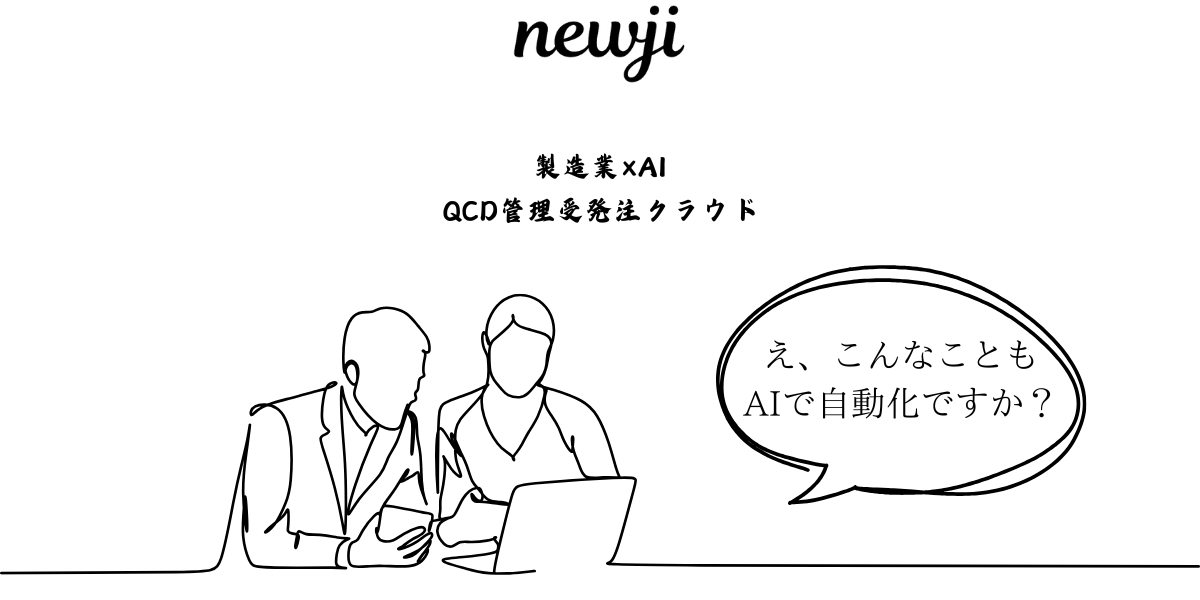
“Revolutionizing Japanese Manufacturing: The Six Sigma Approach to Perfection”
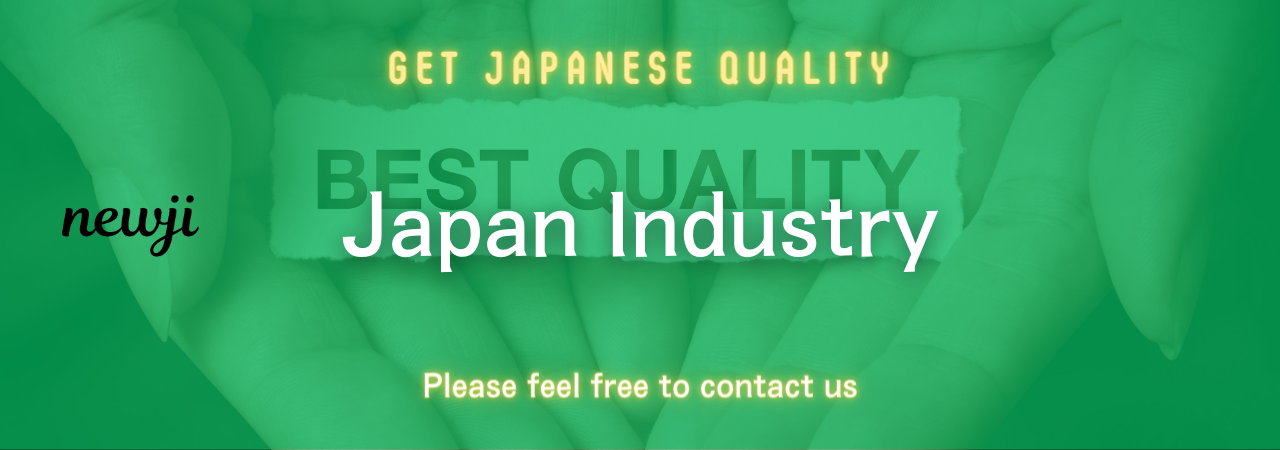
目次
Introduction to Six Sigma in Japanese Manufacturing
Japanese manufacturing has long been synonymous with quality, precision, and efficiency. Central to achieving these standards is the implementation of robust quality management methodologies. Among these, Six Sigma stands out as a transformative approach that has revolutionized manufacturing processes worldwide. In Japan, where meticulous attention to detail and continuous improvement are deeply ingrained in the corporate culture, Six Sigma has found a fertile ground for enhancing operational excellence.
Understanding Six Sigma: Principles and Methodology
Six Sigma is a data-driven methodology aimed at eliminating defects and reducing variability in processes. Originating from Motorola in the 1980s, it gained significant traction through its adoption by companies like General Electric. The core philosophy of Six Sigma revolves around the DMAIC framework: Define, Measure, Analyze, Improve, and Control. This structured approach ensures that problems are clearly identified, measured accurately, analyzed thoroughly, improvements are effectively implemented, and controls are put in place to sustain the gains.
DMAIC Framework Explained
– **Define**: Clearly outline the problem, project goals, and customer requirements.
– **Measure**: Collect data to establish baselines and quantify the extent of issues.
– **Analyze**: Identify root causes of defects and process inefficiencies.
– **Improve**: Develop and implement solutions to address root causes.
– **Control**: Monitor the improved processes to ensure sustained performance.
Advantages of Implementing Six Sigma in Japanese Manufacturing
Implementing Six Sigma in Japanese manufacturing environments offers numerous benefits that align with the nation’s commitment to quality and efficiency.
Enhanced Quality Control
Six Sigma’s rigorous data analysis ensures that defects are minimized, leading to higher quality products. This aligns perfectly with Japan’s reputation for producing reliable and durable goods.
Cost Reduction
By identifying and eliminating waste, Six Sigma helps in significantly reducing operational costs. This is particularly beneficial in highly competitive markets where cost efficiency is paramount.
Increased Customer Satisfaction
Consistently delivering high-quality products enhances customer satisfaction and loyalty. Six Sigma’s focus on meeting and exceeding customer expectations drives long-term business success.
Improved Process Efficiency
Streamlining processes through Six Sigma leads to faster production times and more efficient resource utilization. This results in increased productivity and profitability.
Challenges and Disadvantages of Six Sigma
While Six Sigma offers substantial benefits, its implementation is not without challenges, especially within the context of Japanese manufacturing.
High Implementation Costs
The initial investment in training, software, and process redesign can be significant. For some companies, especially smaller manufacturers, these costs may pose a barrier to adoption.
Resistance to Change
Employees accustomed to traditional methods may resist the structured Six Sigma approach. Overcoming this resistance requires effective change management strategies and strong leadership.
Time-Consuming Process
The DMAIC framework demands meticulous planning and execution, which can be time-consuming. In fast-paced industries, finding the time to fully implement Six Sigma can be challenging.
Requires Continuous Commitment
Six Sigma is not a one-time project but a continuous improvement philosophy. Sustaining momentum over the long term requires unwavering commitment from all levels of the organization.
Six Sigma in Procurement and Purchasing
Procurement and purchasing are critical functions in manufacturing, directly impacting cost, quality, and supply chain efficiency. Six Sigma offers valuable tools and methodologies to optimize these areas.
Supplier Negotiation Techniques
Effective supplier negotiation is essential for securing favorable terms and ensuring quality. Six Sigma provides a structured approach to negotiations by:
– **Data-Driven Decisions**: Utilizing statistical analysis to evaluate supplier performance and identify the best partners.
– **Risk Management**: Assessing and mitigating risks associated with supplier reliability and quality.
– **Value Analysis**: Focusing on total cost of ownership rather than just purchase price to ensure long-term value.
Enhancing Quality Control through Six Sigma
Six Sigma enhances quality control in procurement by:
– **Standardizing Requirements**: Establishing clear quality standards for suppliers to meet.
– **Continuous Monitoring**: Implementing metrics to continuously track supplier performance.
– **Feedback Loops**: Creating mechanisms for regular feedback and improvement with suppliers.
Streamlining Supply Chain Processes
Streamlining supply chain processes through Six Sigma involves:
– **Process Mapping**: Visualizing the entire supply chain to identify inefficiencies.
– **Waste Reduction**: Eliminating non-value-added activities to enhance flow and reduce lead times.
– **Inventory Management**: Optimizing inventory levels to balance availability with cost.
Best Practices for Adopting Six Sigma in Japanese Manufacturing
Successful adoption of Six Sigma in Japanese manufacturing requires adherence to best practices that align with the cultural and operational ethos of the industry.
Leadership Commitment
Strong commitment from top leadership is crucial. Leaders must:
– **Champion the Initiative**: Actively promote Six Sigma as a core business strategy.
– **Allocate Resources**: Ensure sufficient resources are available for training and implementation.
– **Set Clear Goals**: Define specific, measurable objectives aligned with business priorities.
Employee Training and Involvement
Comprehensive training programs are essential to equip employees with Six Sigma tools and techniques.
– **Certification Programs**: Implementing training for different levels (Yellow Belt, Green Belt, Black Belt) to build a skilled workforce.
– **Inclusive Participation**: Encouraging involvement from all departments to foster a culture of continuous improvement.
Continuous Improvement Culture
Cultivating a culture that embraces continuous improvement involves:
– **Encouraging Innovation**: Rewarding creative solutions and process enhancements.
– **Open Communication**: Facilitating transparent communication channels for sharing ideas and feedback.
– **Regular Reviews**: Conducting periodic assessments to evaluate progress and identify new opportunities for improvement.
Market Conditions and Six Sigma
Understanding market conditions is vital for effectively implementing Six Sigma. Japanese manufacturers operate in a dynamic global marketplace where adaptability and responsiveness are key.
Global Competition
Intense global competition requires manufacturers to maintain high standards of quality and efficiency. Six Sigma provides the tools to stay ahead by continuously improving processes and reducing costs.
Technological Advancements
Rapid technological changes necessitate agile manufacturing processes. Six Sigma facilitates the integration of new technologies by ensuring that processes remain robust and scalable.
Customer Expectations
Increasing customer expectations for quality and customization demand flexible and efficient manufacturing systems. Six Sigma helps in meeting these demands by optimizing processes and enhancing product quality.
Case Studies: Successful Six Sigma Implementations
Examining real-world examples of Six Sigma success can provide valuable insights and inspiration for Japanese manufacturers.
Case Study 1: Toyota Motor Corporation
Toyota, a global leader in manufacturing, has successfully integrated Six Sigma into its production systems. By combining Six Sigma with Lean principles, Toyota has achieved remarkable improvements in quality, efficiency, and cost reduction.
Case Study 2: Sony Corporation
Sony leveraged Six Sigma to enhance its product development processes. The structured approach of DMAIC helped Sony reduce defects and improve the reliability of its consumer electronics, reinforcing its market position.
Case Study 3: Panasonic Corporation
Panasonic utilized Six Sigma to streamline its supply chain operations. By identifying and eliminating inefficiencies, Panasonic achieved faster lead times and improved supplier performance, resulting in significant cost savings.
Conclusion: The Future of Six Sigma in Japanese Manufacturing
Six Sigma has proven to be a powerful tool for enhancing manufacturing processes, particularly within the context of Japanese industry. Its structured, data-driven approach aligns seamlessly with the Japanese commitment to quality and continuous improvement. As global markets evolve and technological advancements continue to shape the manufacturing landscape, Six Sigma will remain a critical methodology for achieving operational excellence. By embracing Six Sigma, Japanese manufacturers can continue to uphold their reputation for quality, drive innovation, and maintain a competitive edge in the global marketplace.
資料ダウンロード
QCD管理受発注クラウド「newji」は、受発注部門で必要なQCD管理全てを備えた、現場特化型兼クラウド型の今世紀最高の受発注管理システムとなります。
ユーザー登録
受発注業務の効率化だけでなく、システムを導入することで、コスト削減や製品・資材のステータス可視化のほか、属人化していた受発注情報の共有化による内部不正防止や統制にも役立ちます。
NEWJI DX
製造業に特化したデジタルトランスフォーメーション(DX)の実現を目指す請負開発型のコンサルティングサービスです。AI、iPaaS、および先端の技術を駆使して、製造プロセスの効率化、業務効率化、チームワーク強化、コスト削減、品質向上を実現します。このサービスは、製造業の課題を深く理解し、それに対する最適なデジタルソリューションを提供することで、企業が持続的な成長とイノベーションを達成できるようサポートします。
製造業ニュース解説
製造業、主に購買・調達部門にお勤めの方々に向けた情報を配信しております。
新任の方やベテランの方、管理職を対象とした幅広いコンテンツをご用意しております。
お問い合わせ
コストダウンが利益に直結する術だと理解していても、なかなか前に進めることができない状況。そんな時は、newjiのコストダウン自動化機能で大きく利益貢献しよう!
(β版非公開)