- お役立ち記事
- Revolutionizing Japanese Manufacturing: The Vital Role of OEM for Separator Parts
Revolutionizing Japanese Manufacturing: The Vital Role of OEM for Separator Parts
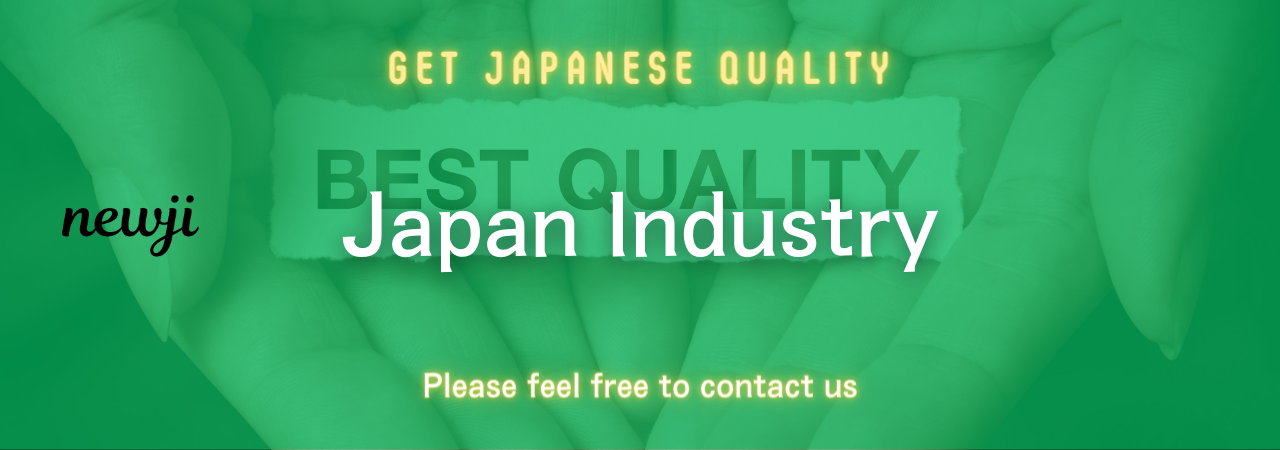
目次
Introduction to OEM in Japanese Manufacturing
Japan has long been recognized as a global leader in manufacturing excellence. Central to this reputation is the robust OEM (Original Equipment Manufacturer) ecosystem that underpins many of its industries. OEM partnerships play a crucial role in the production of separator parts, which are essential components in various manufacturing processes, including automotive, electronics, and machinery sectors. This article delves into the vital role of OEM for separator parts in revolutionizing Japanese manufacturing, exploring the advantages, challenges, negotiation techniques, market conditions, and best practices from a procurement and purchasing perspective.
The Importance of Separator Parts in Manufacturing
Separator parts are critical in ensuring the efficient and reliable operation of machinery and equipment. They function to divide and manage different components, maintaining optimal performance and safety standards. In automotive manufacturing, for instance, separators help in managing engine components, ensuring smooth operation and longevity. Similarly, in electronics, they play a role in circuit management and component isolation.
Enhancing Product Quality
High-quality separator parts directly contribute to the overall quality of the final product. They ensure that machinery operates without unexpected interruptions or failures, which can lead to increased product reliability and customer satisfaction.
Improving Production Efficiency
Efficient separator parts streamline manufacturing processes by reducing downtime and maintenance needs. This improvement in efficiency translates to higher production rates and lower operational costs, giving Japanese manufacturers a competitive edge in the global market.
Advantages of OEM Partnerships for Separator Parts
Collaborating with OEMs offers numerous benefits, particularly in the context of Japanese manufacturing’s emphasis on precision and quality.
Access to Specialized Expertise
OEMs specializing in separator parts bring deep technical knowledge and expertise. This specialization ensures that the parts produced meet stringent quality and performance standards, which is essential for maintaining the integrity of the final product.
Cost Efficiency
Partnering with OEMs can lead to significant cost savings. OEMs often have optimized manufacturing processes and economies of scale that reduce production costs. These savings can be passed on to the purchasing company, enhancing overall profitability.
Flexibility and Scalability
OEM partnerships offer flexibility in production volumes, allowing manufacturers to scale operations up or down based on demand. This adaptability is crucial in managing supply chain dynamics and responding to market fluctuations effectively.
Innovation and Continuous Improvement
OEMs are often at the forefront of technological advancements and process improvements. Collaborating with such partners fosters a culture of innovation, enabling manufacturers to incorporate the latest technologies and methodologies into their production processes.
Challenges in OEM Partnerships
While OEM partnerships offer significant advantages, they also present challenges that need to be managed carefully.
Quality Control
Maintaining consistent quality across all separator parts is paramount. Variations in quality can lead to disruptions in the manufacturing process and affect the final product. Establishing stringent quality control measures is essential to mitigate this risk.
Communication Barriers
Effective communication between the manufacturer and the OEM is critical. Language differences, cultural nuances, and differing business practices can pose challenges. Overcoming these barriers requires clear and consistent communication channels and mutual understanding.
Supply Chain Dependencies
Relying heavily on a single OEM can create vulnerabilities in the supply chain. Disruptions such as delays, natural disasters, or political instability can impact the availability of separator parts. Diversifying OEM partnerships and developing contingency plans can help mitigate these risks.
Intellectual Property Concerns
Protecting intellectual property (IP) is a significant concern in OEM partnerships. Ensuring that the OEM adheres to strict IP protection protocols is essential to prevent unauthorized use or duplication of proprietary technologies and designs.
Supplier Negotiation Techniques
Effective negotiation with OEMs is crucial for establishing mutually beneficial partnerships. Here are key techniques to consider:
Understanding Market Conditions
A thorough understanding of current market conditions, including demand-supply dynamics, pricing trends, and technological advancements, provides a strong foundation for negotiations. This knowledge enables manufacturers to make informed decisions and negotiate favorable terms.
Building Long-term Relationships
Focusing on long-term partnerships rather than short-term gains fosters trust and collaboration. Building a strong relationship with the OEM can lead to better terms, priority during supply shortages, and collaborative innovation.
Clear Communication of Requirements
Clearly articulating technical specifications, quality standards, and delivery timelines ensures that both parties have a shared understanding of expectations. Detailed documentation and regular updates can prevent misunderstandings and ensure alignment.
Leveraging Competitive Bidding
Encouraging multiple OEMs to bid for contracts can create a competitive environment that drives better pricing and terms. However, it’s essential to balance competition with the value of established relationships and the OEM’s capability to deliver consistently.
Flexible Contract Terms
Including flexibility in contract terms allows for adjustments based on changing market conditions or unforeseen challenges. Clauses related to volume adjustments, pricing reviews, and contingency plans can provide necessary adaptability.
Market Conditions Affecting OEM Partnerships
The landscape of OEM partnerships is influenced by various market conditions that manufacturers must navigate.
Global Supply Chain Dynamics
Global supply chains are subject to fluctuations due to geopolitical tensions, trade policies, and economic shifts. Understanding these dynamics helps manufacturers anticipate potential disruptions and develop strategies to maintain a steady supply of separator parts.
Technological Advancements
Rapid advancements in manufacturing technologies, such as automation and digitalization, are reshaping OEM partnerships. Embracing these technologies can enhance production efficiency and product quality, but it also requires continuous adaptation and investment.
Sustainability and Environmental Regulations
Increasing emphasis on sustainability and stricter environmental regulations influence OEM operations. Manufacturers must ensure that their OEM partners comply with these standards, which may involve adopting greener materials and sustainable manufacturing practices.
Economic Factors
Economic conditions, including inflation rates, currency fluctuations, and labor costs, impact the cost structure and pricing of OEM services. Monitoring these factors is essential for maintaining cost efficiency and competitive pricing.
Best Practices for Effective OEM Partnerships
Implementing best practices fosters successful OEM partnerships and maximizes the benefits of collaboration.
Establishing Clear Contracts
Comprehensive contracts that outline roles, responsibilities, quality standards, delivery schedules, and dispute resolution mechanisms are essential. Clear contractual agreements prevent misunderstandings and provide a framework for resolving issues.
Regular Performance Reviews
Conducting regular performance reviews with OEMs ensures that quality and performance standards are consistently met. These reviews facilitate continuous improvement and address any emerging issues promptly.
Investing in Joint Development
Collaborative development initiatives, such as co-designing new separator parts or jointly exploring innovative solutions, strengthen the partnership. Joint development fosters a sense of ownership and shared responsibility for product success.
Implementing Effective Communication Channels
Establishing robust communication channels, including regular meetings, progress reports, and real-time updates, enhances transparency and coordination between manufacturers and OEMs.
Ensuring Compliance and Ethical Standards
Adhering to compliance and ethical standards, including labor laws, environmental regulations, and anti-corruption measures, is critical. Manufacturers should work with OEMs that demonstrate a commitment to ethical practices and regulatory compliance.
Case Studies: Successful OEM Partnerships in Japan
Examining real-world examples of successful OEM partnerships provides valuable insights into best practices and practical applications.
Automotive Industry Collaboration
Japanese automotive giants frequently collaborate with specialized OEMs for component manufacturing. For example, a leading car manufacturer partners with an OEM specializing in high-precision separator parts, ensuring that engine components meet exacting standards. This collaboration enhances product reliability and performance, contributing to the manufacturer’s global reputation for quality.
Electronics Manufacturing Partnerships
In the electronics sector, OEM partnerships are pivotal in producing intricate separator components for circuit boards and electronic devices. A prominent electronics manufacturer partners with an OEM renowned for its advanced manufacturing capabilities and adherence to stringent quality controls. This partnership enables the manufacturer to innovate rapidly and maintain a competitive edge in the fast-paced electronics market.
Future Trends in OEM for Separator Parts
The OEM landscape is continually evolving, influenced by technological advancements and changing market dynamics.
Automation and Smart Manufacturing
Automation and smart manufacturing are becoming increasingly prevalent in OEM operations. The integration of IoT (Internet of Things), AI (Artificial Intelligence), and robotics enhances production efficiency, accuracy, and scalability. These technologies enable OEMs to produce high-quality separator parts with minimal human intervention, reducing errors and increasing output.
Sustainable Manufacturing Practices
Sustainability is a growing priority in manufacturing. OEMs are adopting eco-friendly materials, energy-efficient processes, and waste reduction strategies. Manufacturers partnering with OEMs that prioritize sustainability can achieve environmental compliance and appeal to eco-conscious consumers.
Customization and Flexibility
The demand for customized separator parts tailored to specific applications is rising. OEMs are enhancing their capabilities to offer flexible manufacturing solutions that cater to unique requirements. This trend allows manufacturers to differentiate their products and meet diverse customer needs effectively.
Global Collaboration and Localization
Global collaboration is shifting towards more localized production to mitigate supply chain risks. Manufacturers are seeking OEM partners in geographically strategic locations to ensure a stable supply of separator parts and reduce lead times. This localization strategy enhances supply chain resilience and responsiveness to market changes.
Strategies for Selecting the Right OEM Partner
Choosing the appropriate OEM partner is critical for the success of manufacturing operations. Here are key strategies to consider:
Assessing Technical Capabilities
Evaluate the OEM’s technical expertise, manufacturing capabilities, and technological infrastructure. Ensure that the OEM can meet the specific technical requirements and maintain high-quality standards for separator parts.
Evaluating Quality Assurance Processes
Examine the OEM’s quality assurance protocols, including certifications, testing procedures, and quality control measures. A robust quality assurance system indicates the OEM’s commitment to delivering reliable and consistent products.
Reviewing Financial Stability
Assess the financial health of the OEM to ensure long-term viability and the ability to invest in necessary technologies and processes. A financially stable partner is more likely to sustain operations and honor contractual commitments.
Considering Cultural Compatibility
Cultural alignment between the manufacturer and OEM fosters smoother collaboration and mutual understanding. Consider factors such as work ethics, communication styles, and business practices to ensure a harmonious partnership.
Analyzing Supply Chain Integration
Evaluate how well the OEM’s supply chain integrates with your own processes. Efficient supply chain integration minimizes delays, reduces costs, and enhances overall operational efficiency.
Implementing Effective Quality Control in OEM Partnerships
Quality control is paramount in maintaining the integrity of separator parts produced by OEMs. Here are strategies to ensure effective quality management:
Setting Clear Quality Standards
Define explicit quality standards and specifications for separator parts. Clear guidelines help OEMs understand expectations and align their production processes accordingly.
Conducting Regular Audits
Perform regular audits of the OEM’s facilities and processes to ensure adherence to quality standards. Audits help identify potential issues early and facilitate corrective actions.
Utilizing Advanced Testing Methods
Incorporate advanced testing techniques, such as statistical process control and non-destructive testing, to evaluate the quality of separator parts comprehensively. These methods provide accurate assessments of product integrity and performance.
Establishing Collaborative Problem-solving
Foster a collaborative approach to problem-solving between the manufacturer and OEM. Jointly addressing quality issues promotes shared responsibility and continuous improvement.
Enhancing Supply Chain Resilience through OEM Partnerships
Building a resilient supply chain is essential for mitigating risks and ensuring uninterrupted production. OEM partnerships contribute significantly to supply chain resilience in the following ways:
Diversifying Supplier Base
Partnering with multiple OEMs across different regions reduces dependency on a single supplier, minimizing the impact of localized disruptions and enhancing overall supply chain stability.
Implementing Just-in-Time Practices
Adopting just-in-time (JIT) manufacturing practices with OEM partners optimizes inventory levels, reduces lead times, and enhances responsiveness to demand fluctuations, contributing to a more resilient supply chain.
Developing Contingency Plans
Collaborate with OEMs to develop contingency plans for potential disruptions, such as natural disasters, political instability, or pandemics. Preparedness ensures a swift and effective response to unforeseen challenges.
Embracing Digital Supply Chain Solutions
Leverage digital tools and platforms to enhance visibility and coordination across the supply chain. Real-time tracking, data analytics, and integrated communication systems enable proactive management of supply chain risks.
Conclusion
OEM partnerships for separator parts are integral to the success and innovation of Japanese manufacturing. By leveraging the specialized expertise, cost efficiencies, and scalability offered by OEMs, manufacturers can enhance product quality, improve production efficiency, and maintain a competitive edge in the global market. However, navigating the challenges of quality control, communication barriers, and supply chain dependencies requires strategic negotiation, thorough market understanding, and the implementation of best practices.
As the manufacturing landscape continues to evolve with advancements in technology and shifts in market dynamics, OEM partnerships must adapt to remain effective and resilient. Embracing automation, sustainability, customization, and localization will be key to future-proofing these collaborations. By selecting the right OEM partners and fostering strong, collaborative relationships, Japanese manufacturers can continue to revolutionize their industries and deliver exceptional value to their customers worldwide.
資料ダウンロード
QCD調達購買管理クラウド「newji」は、調達購買部門で必要なQCD管理全てを備えた、現場特化型兼クラウド型の今世紀最高の購買管理システムとなります。
ユーザー登録
調達購買業務の効率化だけでなく、システムを導入することで、コスト削減や製品・資材のステータス可視化のほか、属人化していた購買情報の共有化による内部不正防止や統制にも役立ちます。
NEWJI DX
製造業に特化したデジタルトランスフォーメーション(DX)の実現を目指す請負開発型のコンサルティングサービスです。AI、iPaaS、および先端の技術を駆使して、製造プロセスの効率化、業務効率化、チームワーク強化、コスト削減、品質向上を実現します。このサービスは、製造業の課題を深く理解し、それに対する最適なデジタルソリューションを提供することで、企業が持続的な成長とイノベーションを達成できるようサポートします。
オンライン講座
製造業、主に購買・調達部門にお勤めの方々に向けた情報を配信しております。
新任の方やベテランの方、管理職を対象とした幅広いコンテンツをご用意しております。
お問い合わせ
コストダウンが利益に直結する術だと理解していても、なかなか前に進めることができない状況。そんな時は、newjiのコストダウン自動化機能で大きく利益貢献しよう!
(Β版非公開)