- お役立ち記事
- Revolutionizing Japanese Manufacturing: Unlocking Efficiency with Atmospheric Nitriding Process OEM Solutions
月間77,185名の
製造業ご担当者様が閲覧しています*
*2025年2月28日現在のGoogle Analyticsのデータより
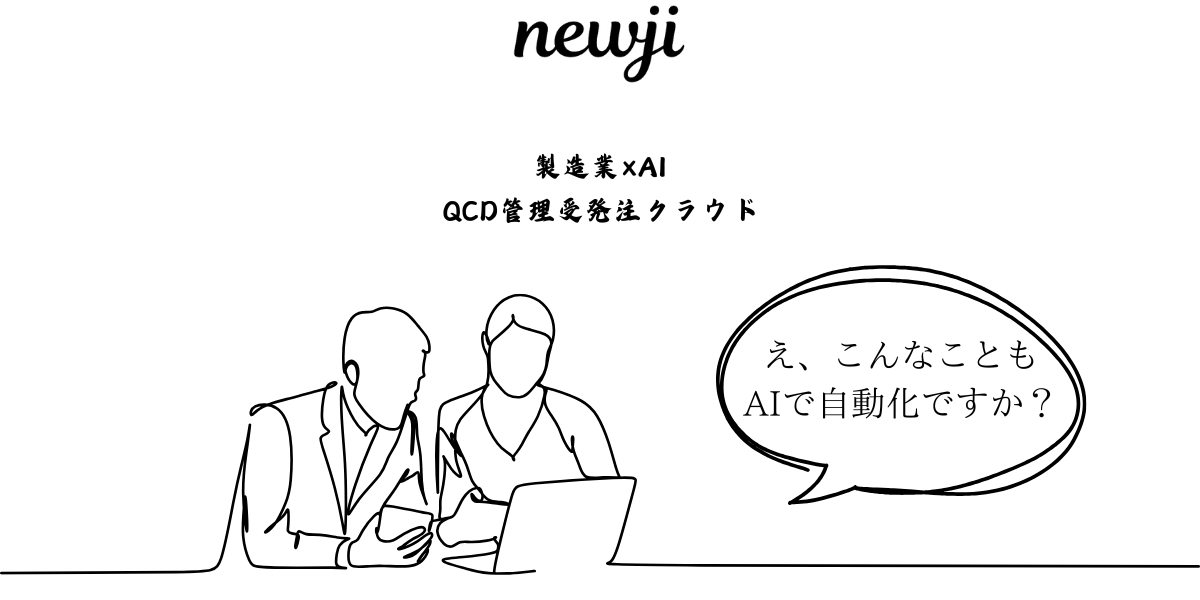
Revolutionizing Japanese Manufacturing: Unlocking Efficiency with Atmospheric Nitriding Process OEM Solutions
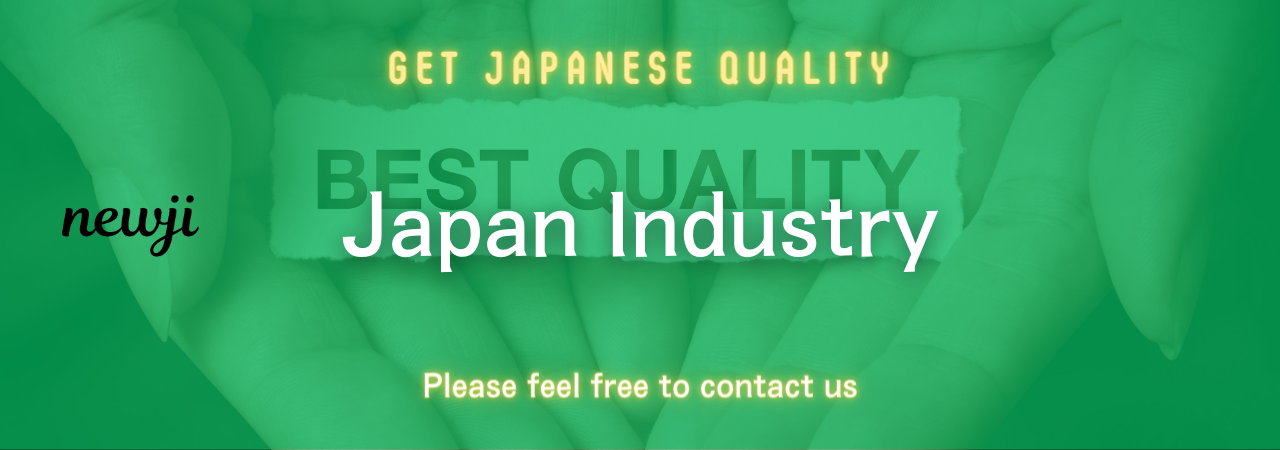
目次
Introduction to Atmospheric Nitriding in Japanese Manufacturing
Atmospheric nitriding has emerged as a pivotal process in enhancing the durability and performance of metal components within Japanese manufacturing sectors. This advanced surface treatment technique involves diffusing nitrogen into the material’s surface, resulting in improved hardness, wear resistance, and fatigue strength. As Japanese manufacturers continuously strive for excellence and efficiency, integrating atmospheric nitriding process OEM solutions has become a strategic move to maintain competitiveness in the global market.
The Role of OEM Solutions in Atmospheric Nitriding
Original Equipment Manufacturer (OEM) solutions play a crucial role in the atmospheric nitriding process by providing specialized equipment and technology tailored to meet specific manufacturing needs. These solutions encompass a range of services, including the design and production of nitriding furnaces, control systems, and maintenance services. By partnering with OEMs, Japanese manufacturers can leverage cutting-edge technology, ensuring that their nitriding processes are both efficient and effective.
Benefits of Utilizing OEM Solutions
One of the primary advantages of adopting OEM solutions is the access to state-of-the-art technology. OEMs invest heavily in research and development, ensuring that their products incorporate the latest advancements in nitriding technology. This translates to higher-quality outcomes, reduced processing times, and enhanced energy efficiency.
Furthermore, OEM partnerships provide manufacturers with comprehensive support, including installation, training, and ongoing maintenance. This support minimizes downtime and ensures that the nitriding processes operate smoothly, contributing to overall factory efficiency.
Advantages of Atmospheric Nitriding in Manufacturing
Implementing atmospheric nitriding offers several benefits that significantly impact manufacturing operations. These advantages not only enhance product quality but also contribute to cost savings and operational efficiency.
Enhanced Material Properties
Atmospheric nitriding improves the surface hardness of metal components without compromising their core properties. This results in products that are more resistant to wear, erosion, and fatigue, thereby extending their service life. Enhanced material properties reduce the need for frequent replacements, which in turn lowers maintenance costs and minimizes downtime.
Cost-Effectiveness
Compared to other hardening processes, atmospheric nitriding is relatively cost-effective. It requires lower energy consumption and shorter processing times, leading to reduced operational costs. Additionally, the improved durability of nitrided components means that manufacturers can achieve higher productivity with less frequent interruptions for maintenance and replacements.
Environmental Benefits
Atmospheric nitriding is an eco-friendly process that generates fewer emissions and consumes less energy compared to traditional hardening methods. By adopting this process, manufacturers can align with environmental standards and reduce their carbon footprint, contributing to sustainable manufacturing practices.
Challenges and Disadvantages of Atmospheric Nitriding
Despite its numerous benefits, atmospheric nitriding also presents certain challenges that manufacturers must address to ensure successful implementation.
Initial Investment Costs
The adoption of atmospheric nitriding requires significant initial investment in specialized equipment and technology. While OEM solutions can mitigate some of these costs through tailored financing options, the upfront capital expenditure can still be a barrier for some manufacturers.
Technical Expertise
Implementing atmospheric nitriding necessitates a high level of technical expertise. Manufacturers must invest in training their workforce to operate and maintain nitriding equipment effectively. The lack of skilled personnel can lead to suboptimal process performance and increased downtime.
Process Control and Consistency
Maintaining consistent process parameters is critical to achieving uniform nitrided layers. Variations in temperature, gas composition, and processing time can result in inconsistent material properties. Manufacturers must establish stringent quality control measures to ensure process reliability and consistency.
Supplier Negotiation Techniques for Atmospheric Nitriding OEM Solutions
Effective negotiation with OEM suppliers is essential to securing favorable terms and ensuring that the nitriding process aligns with manufacturing objectives. Here are some key techniques to enhance negotiation outcomes:
Thorough Market Research
Before entering negotiations, conduct comprehensive market research to understand the range of available OEM solutions, pricing structures, and technological advancements. This knowledge provides a solid foundation for informed decision-making and strengthens your bargaining position.
Define Clear Requirements
Clearly articulate your manufacturing needs, including specific performance criteria, production volumes, and quality standards. A well-defined set of requirements helps OEM suppliers tailor their solutions to your exact specifications, ensuring optimal process integration.
Leverage Long-Term Partnership Potential
Emphasize the potential for a long-term partnership with OEM suppliers. Manufacturers often receive better pricing, priority support, and customized solutions when they commit to ongoing collaboration. Highlighting the benefits of a sustained relationship can lead to more favorable negotiation terms.
Request Comprehensive Proposals
Invite OEM suppliers to submit detailed proposals that outline the scope of their solutions, including equipment specifications, service agreements, and pricing. Comparing multiple proposals enables manufacturers to identify the best value offerings and negotiate more effectively.
Focus on Total Cost of Ownership
Consider the total cost of ownership (TCO) rather than just the initial purchase price. TCO encompasses maintenance costs, energy consumption, training expenses, and potential downtime. Evaluating TCO provides a more accurate assessment of each OEM’s value proposition.
Market Conditions Influencing Atmospheric Nitriding OEM Solutions
Understanding the current market conditions is vital for making informed decisions regarding atmospheric nitriding OEM solutions. Several factors influence the availability, cost, and technological advancements in the OEM market.
Technological Advancements
Rapid advancements in nitriding technology drive continuous improvements in process efficiency and product quality. Manufacturers must stay abreast of these innovations to remain competitive and leverage the latest capabilities offered by OEM suppliers.
Global Supply Chain Dynamics
Global supply chain disruptions can impact the availability and cost of nitriding equipment and materials. Manufacturers should assess the reliability of OEM suppliers’ supply chains and consider diversification strategies to mitigate potential risks.
Regulatory Environment
Environmental regulations governing emissions and energy consumption influence the design and operation of atmospheric nitriding processes. OEM solutions must comply with these regulations, ensuring that manufacturers meet legal standards while maintaining operational efficiency.
Economic Factors
Economic conditions, such as inflation rates and currency fluctuations, affect the pricing of OEM solutions. Manufacturers should monitor economic indicators and negotiate flexible pricing arrangements to accommodate potential market volatility.
Best Practices for Implementing Atmospheric Nitriding OEM Solutions
To maximize the benefits of atmospheric nitriding, manufacturers should adopt best practices that ensure successful implementation and ongoing optimization of the process.
Comprehensive Planning and Assessment
Begin by conducting a thorough assessment of your manufacturing processes and identify areas where atmospheric nitriding can add value. Develop a detailed implementation plan that outlines the necessary steps, resources, and timelines required to integrate nitriding into your production workflow.
Partner with Experienced OEM Suppliers
Select OEM suppliers with a proven track record in delivering high-quality nitriding solutions. Experienced suppliers offer valuable insights, technical support, and customization options that can enhance the effectiveness of the nitriding process.
Invest in Training and Development
Provide extensive training for your workforce to ensure they are proficient in operating and maintaining nitriding equipment. Continuous professional development helps maintain high process standards and reduces the risk of operational errors.
Implement Robust Quality Control Measures
Establish stringent quality control protocols to monitor key process parameters such as temperature, gas composition, and processing time. Regular inspections and testing ensure that nitrided components meet the required specifications and performance standards.
Optimize Process Parameters
Continuously analyze and refine process parameters to enhance efficiency and product quality. Utilize data analytics and process monitoring tools to identify areas for improvement and implement corrective actions as needed.
Maintain Open Communication with OEM Suppliers
Foster a collaborative relationship with your OEM suppliers by maintaining open lines of communication. Regular meetings, feedback sessions, and performance reviews help address issues promptly and drive continuous improvement in the nitriding process.
Case Studies: Success Stories in Japanese Manufacturing
Examining real-world examples of Japanese manufacturers that have successfully implemented atmospheric nitriding OEM solutions provides valuable insights into best practices and potential outcomes.
Automotive Sector
A leading Japanese automotive manufacturer integrated atmospheric nitriding into their production line to enhance the durability of engine components. Partnering with a reputable OEM supplier, the company achieved a 20% increase in component lifespan and a 15% reduction in maintenance costs. The improved performance of nitrided parts contributed to higher vehicle reliability and customer satisfaction.
Electronic Manufacturing
A prominent electronics manufacturer adopted atmospheric nitriding to improve the wear resistance of connector parts used in high-stress applications. Through collaboration with an OEM supplier, the company streamlined their nitriding process, resulting in a 25% increase in production efficiency and a significant reduction in component failures during testing. This enhancement bolstered the company’s reputation for producing high-quality, reliable electronic products.
Tooling and Machinery
A Japanese tooling manufacturer implemented atmospheric nitriding to enhance the surface hardness of cutting tools. The partnership with an OEM supplier enabled the company to achieve superior tool performance, leading to a 30% increase in tool life and a corresponding decrease in production downtime. The improved tooling quality allowed the manufacturer to meet higher demand with consistent product quality.
Future Trends in Atmospheric Nitriding and OEM Solutions
As Japanese manufacturing continues to evolve, several emerging trends are shaping the future of atmospheric nitriding and OEM solutions.
Automation and Industry 4.0 Integration
The integration of automation and Industry 4.0 technologies into atmospheric nitriding processes is revolutionizing manufacturing operations. Advanced control systems, IoT-enabled sensors, and real-time data analytics enable precise process monitoring and optimization, enhancing efficiency and reducing human error.
Sustainability and Green Manufacturing
Sustainability remains a critical focus for manufacturers worldwide. Future advancements in atmospheric nitriding will prioritize energy efficiency, reduced emissions, and the use of environmentally friendly materials. OEM suppliers are developing greener nitriding solutions to help manufacturers achieve their sustainability goals.
Customization and Flexibility
Manufacturers are increasingly seeking tailored nitriding solutions to meet diverse production requirements. OEM suppliers are responding by offering more customizable equipment and adaptable process parameters, allowing for greater flexibility in handling various component specifications and production volumes.
Advanced Materials and Hybrid Processes
The development of advanced materials and hybrid processes is expanding the capabilities of atmospheric nitriding. Combining nitriding with other surface treatment techniques, such as carburizing or coating applications, results in multi-functional surfaces with enhanced properties tailored for specific applications.
Conclusion
Atmospheric nitriding process OEM solutions are transforming Japanese manufacturing by unlocking new levels of efficiency, product quality, and operational excellence. By leveraging the expertise and technology provided by OEM suppliers, manufacturers can enhance the durability and performance of their products, reduce costs, and maintain a competitive edge in the global marketplace. While challenges such as initial investment costs and the need for technical expertise exist, the long-term benefits of atmospheric nitriding make it a strategic investment for forward-thinking manufacturers. Embracing best practices, fostering strong supplier partnerships, and staying abreast of market trends will ensure that Japanese manufacturers continue to lead in innovation and quality within the manufacturing industry.
資料ダウンロード
QCD管理受発注クラウド「newji」は、受発注部門で必要なQCD管理全てを備えた、現場特化型兼クラウド型の今世紀最高の受発注管理システムとなります。
ユーザー登録
受発注業務の効率化だけでなく、システムを導入することで、コスト削減や製品・資材のステータス可視化のほか、属人化していた受発注情報の共有化による内部不正防止や統制にも役立ちます。
NEWJI DX
製造業に特化したデジタルトランスフォーメーション(DX)の実現を目指す請負開発型のコンサルティングサービスです。AI、iPaaS、および先端の技術を駆使して、製造プロセスの効率化、業務効率化、チームワーク強化、コスト削減、品質向上を実現します。このサービスは、製造業の課題を深く理解し、それに対する最適なデジタルソリューションを提供することで、企業が持続的な成長とイノベーションを達成できるようサポートします。
製造業ニュース解説
製造業、主に購買・調達部門にお勤めの方々に向けた情報を配信しております。
新任の方やベテランの方、管理職を対象とした幅広いコンテンツをご用意しております。
お問い合わせ
コストダウンが利益に直結する術だと理解していても、なかなか前に進めることができない状況。そんな時は、newjiのコストダウン自動化機能で大きく利益貢献しよう!
(β版非公開)