- お役立ち記事
- Revolutionizing Japanese Manufacturing: Unveiling the Next-Generation Motion Mechanism
Revolutionizing Japanese Manufacturing: Unveiling the Next-Generation Motion Mechanism
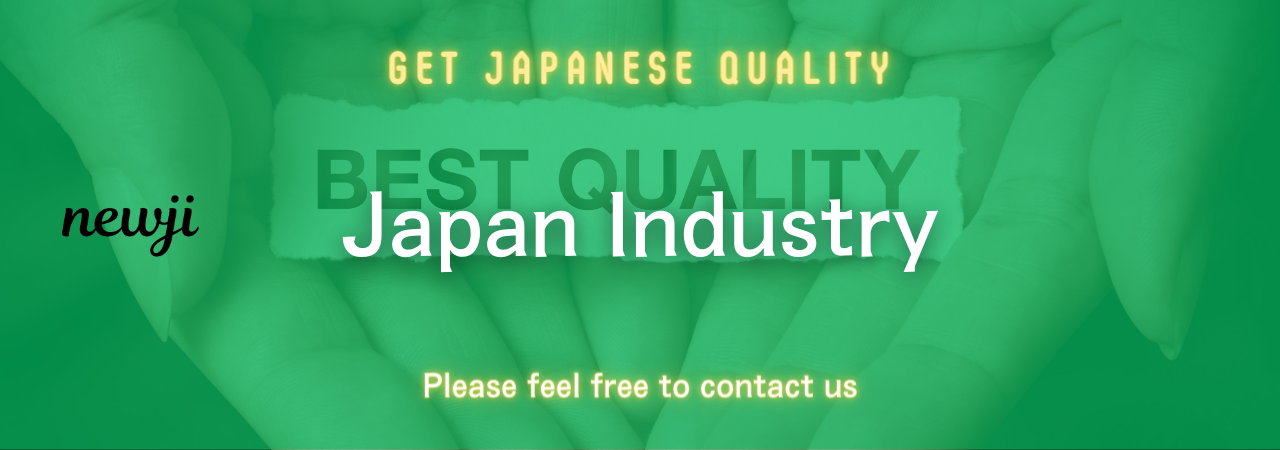
目次
Introduction to Japanese Manufacturing Prowess
In the landscape of global manufacturing, Japan emerges as a powerhouse, synonymous with precision, efficiency, and state-of-the-art innovation.
The country has carved a niche for itself by blending age-old craftsmanship with cutting-edge technology.
A key player in this technological arena is the next-generation motion mechanism, a revolutionary development poised to redefine manufacturing paradigms.
As someone deeply rooted in the procurement and purchasing sectors within the industry, I’ve witnessed firsthand the evolution of these mechanisms and their profound impacts.
This article delves into how this breakthrough is reshaping manufacturing, offering practical insights and guidance for professionals looking to leverage Japanese suppliers for enhanced operational efficiency.
The Essence of the Next-Generation Motion Mechanism
The next-generation motion mechanism builds upon Japan’s legacy of excellence in engineering and innovation.
At its core, it integrates advanced robotics, AI-driven controls, and precision engineering to enhance speed, accuracy, and reliability in manufacturing processes.
This technology stands out for its ability to optimize production cycles, reduce downtime, and increase throughput while maintaining stringent quality standards.
It’s not merely an improvement on existing technologies; it signifies a quantum leap—a bold re-imagining of how motion in manufacturing is understood and executed.
Advantages of the Next-Generation Motion Mechanism
Enhanced Precision and Accuracy
Precision is the hallmark of Japanese manufacturing, and the next-generation motion mechanism elevates this to unprecedented levels.
Using highly sophisticated sensors and AI algorithms, it ensures that each movement, whether simple or complex, is executed with flawless accuracy.
This level of precision reduces waste, improves product quality, and minimizes defects, leading to substantial cost savings.
Increased Production Efficiency
Efficiency gains are at the heart of this technological advancement.
By streamlining motion processes, manufacturers can achieve faster cycle times and higher throughput rates.
This not only boosts production volumes but also allows for more flexible production schedules, adapting swiftly to changing market demands.
Improved Reliability and Maintenance
The integration of predictive maintenance tools and robust design features ensures that the next-generation motion mechanism requires minimal intervention.
Predictive analytics anticipate wear and tear, enabling proactive maintenance and minimizing downtime.
This leads to sustained production without unexpected interruptions, a critical factor in maintaining supply chain integrity.
Environmental Impact
Environmental sustainability is a global concern, and these mechanisms contribute significantly to green manufacturing practices.
By optimizing energy consumption and reducing material waste, they help manufacturers achieve their sustainability targets, aligning with both corporate responsibility and regulatory requirements.
Challenges and Disadvantages
High Initial Costs
One of the primary barriers to adopting this technology is its high initial cost.
Investment in state-of-the-art machinery and training personnel to operate these systems can be substantial.
However, when weighed against long-term savings in operating costs and efficiency gains, the initial outlay is often justified.
Complex Integration Processes
Integrating new technologies into existing manufacturing processes is inherently challenging.
The next-generation motion mechanism requires careful planning and execution to avoid disruptions.
Comprehensive training and change management strategies are vital to seamless adoption.
Need for Skilled Workforce
As with any advanced technology, a skilled workforce is crucial.
Employees need to be adept not only at operating these mechanisms but also at troubleshooting and optimizing them.
This necessitates ongoing training and development programs to keep skills current.
Supplier Negotiation Techniques
Engaging with Japanese suppliers requires a nuanced approach, respecting cultural norms and emphasizing mutual benefits.
Understanding Japanese Business Culture
Japanese business culture values trust, respect, and long-term relationships.
It’s vital to approach negotiations with a genuine interest in understanding and valuing these perspectives.
A focus on building rapport, demonstrating commitment to the partnership, and valuing collective success over individual gain will serve as an advantage.
Emphasizing Quality and Performance
Highlight the benefits that high-quality Japanese technology can bring to your production processes.
Suppliers appreciate when buyers recognize the superior performance and reliability of their products, creating a foundation for a mutually beneficial agreement.
Leveraging Volume and Long-Term Commitment
Japanese suppliers often reward volume purchases and long-term commitments with favorable terms.
By negotiating contracts that span multiple years or include bulk purchasing terms, buyers can secure better pricing and service agreements.
Understanding Market Conditions
The Japanese manufacturing supply chain is intricately linked with global markets.
Keeping abreast of market conditions—such as raw material availability, shifts in demand, and geopolitical factors—can provide valuable insights for procurement professionals.
Market Trends and Innovations
Staying updated with trends in automation, AI, and IoT within the Japanese manufacturing sectors can help anticipate new product releases and innovations.
This foresight allows companies to position themselves advantageously, ensuring access to the latest technology.
Economic and Political Considerations
Japan’s economic policies and political climate can significantly influence manufacturing costs and availability.
Being informed about these factors aids in strategic decision-making, minimizing risks associated with supply chain disruptions.
Best Practices for Procurement and Purchasing
Drawing from years of experience, I offer these best practices to optimize procurement and purchasing efforts with Japanese suppliers.
Build Strong Supplier Relationships
Invest in regular communication and visits to supplier facilities to strengthen relationships.
Understand their challenges and work collaboratively to develop solutions, fostering a sense of partnership.
Ensure Comprehensive Training and Development
Training is key to successful integration and operation of new technology.
Ensure your team is well-equipped to handle the complex mechanisms, promoting skill enhancement sessions and hands-on workshops.
Implement Rigorous Quality Control
Japanese manufacturing thrives on quality.
Adopt rigorous quality control processes to maintain the high standards expected, leveraging tools such as Six Sigma and Total Quality Management.
Focus on Continuous Improvement
Embrace the Japanese philosophy of Kaizen, or continuous improvement.
Constantly seek ways to refine processes, enhance efficiency, and drive innovation to remain competitive.
Conclusion: Embracing the Future with Japanese Manufacturing
The next-generation motion mechanism represents a transformative force in global manufacturing, driven by the unmatched capabilities of Japanese engineering.
While the path to integration may present challenges, the benefits of improved efficiency, precision, and sustainability make it an endeavor worth pursuing.
For procurement and purchasing professionals, leveraging these advancements through strategic engagement with Japanese suppliers can unlock unprecedented opportunities.
By understanding and adopting these technologies, businesses can not only revolutionize their manufacturing processes but also secure a competitive edge in an ever-evolving global market.
資料ダウンロード
QCD調達購買管理クラウド「newji」は、調達購買部門で必要なQCD管理全てを備えた、現場特化型兼クラウド型の今世紀最高の購買管理システムとなります。
ユーザー登録
調達購買業務の効率化だけでなく、システムを導入することで、コスト削減や製品・資材のステータス可視化のほか、属人化していた購買情報の共有化による内部不正防止や統制にも役立ちます。
NEWJI DX
製造業に特化したデジタルトランスフォーメーション(DX)の実現を目指す請負開発型のコンサルティングサービスです。AI、iPaaS、および先端の技術を駆使して、製造プロセスの効率化、業務効率化、チームワーク強化、コスト削減、品質向上を実現します。このサービスは、製造業の課題を深く理解し、それに対する最適なデジタルソリューションを提供することで、企業が持続的な成長とイノベーションを達成できるようサポートします。
オンライン講座
製造業、主に購買・調達部門にお勤めの方々に向けた情報を配信しております。
新任の方やベテランの方、管理職を対象とした幅広いコンテンツをご用意しております。
お問い合わせ
コストダウンが利益に直結する術だと理解していても、なかなか前に進めることができない状況。そんな時は、newjiのコストダウン自動化機能で大きく利益貢献しよう!
(Β版非公開)