- お役立ち記事
- Revolutionizing Japanese Manufacturing with “Smart Maintenance” Strategies
Revolutionizing Japanese Manufacturing with “Smart Maintenance” Strategies
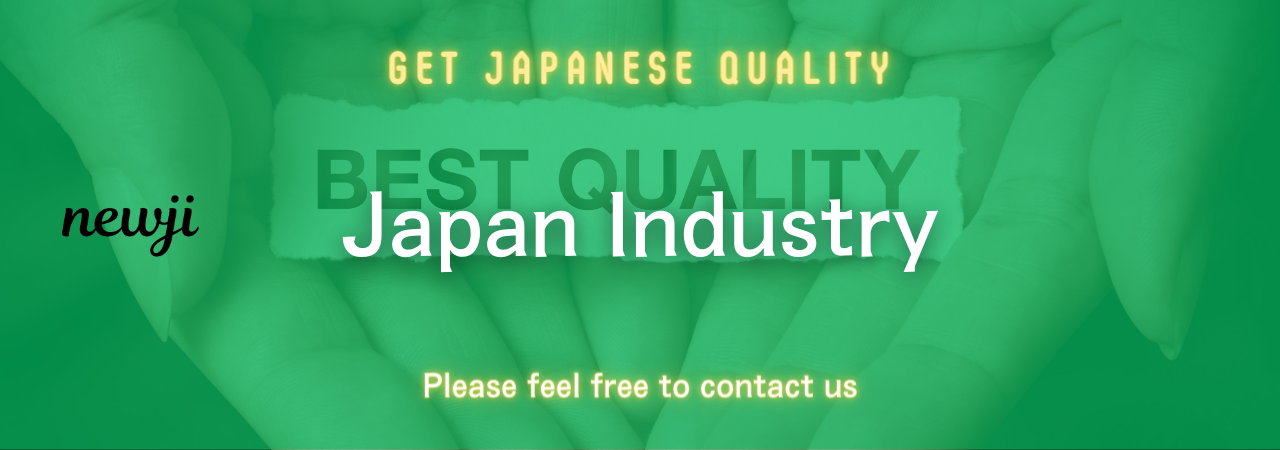
In an era characterized by rapid technological advancements and increasing global competition, Japanese manufacturing companies are seeking innovative ways to maintain their competitive edge. One of the most promising approaches to achieving this is through the adoption of “Smart Maintenance” strategies. This comprehensive guide explores the concept of Smart Maintenance, its advantages and disadvantages, best practices, market conditions, and practical insights from the field of procurement and purchasing.
目次
Understanding Smart Maintenance
Smart Maintenance integrates advanced technologies such as the Internet of Things (IoT), artificial intelligence (AI), big data analytics, and machine learning to improve the efficiency and reliability of manufacturing processes. It allows for real-time monitoring, predictive maintenance, and data-driven decision-making, ultimately reducing downtime and operational costs.
Key Components of Smart Maintenance
Several technologies underpin the successful implementation of Smart Maintenance strategies:
1. **IoT Sensors**: IoT sensors enable real-time monitoring of equipment and machinery. These sensors collect data on various parameters such as temperature, vibration, and pressure, which can be analyzed to predict potential issues.
2. **Big Data Analytics**: Analyzing large volumes of data generated by IoT sensors helps in identifying patterns and trends. This predictive capability allows for timely maintenance interventions, reducing unexpected breakdowns.
3. **AI and Machine Learning**: AI algorithms and machine learning models can predict maintenance needs by analyzing historical data. These technologies can identify potential failures and suggest optimal maintenance schedules.
4. **Cloud Computing**: Storing and processing data in the cloud enables scalability and seamless access to information across different locations. This is crucial for global manufacturing operations.
Advantages of Smart Maintenance
Smart Maintenance offers numerous benefits that can revolutionize Japanese manufacturing practices.
1. Reduced Downtime
By predicting and addressing potential failures before they occur, Smart Maintenance reduces unplanned downtime. This improves overall equipment effectiveness (OEE) and ensures smoother production processes.
2. Cost Savings
Predictive maintenance minimizes the need for expensive emergency repairs and extends the lifespan of equipment. Additionally, optimized maintenance schedules prevent unnecessary part replacements, reducing maintenance budgets.
3. Enhanced Safety
Real-time monitoring of equipment conditions helps identify safety hazards early on. Addressing these issues promptly reduces the risk of accidents and injuries in the workplace.
4. Improved Quality
Consistent machine performance ensures that production processes remain stable, resulting in higher quality products. This reduces the likelihood of defects and customer complaints.
Challenges and Disadvantages
Despite its numerous advantages, Smart Maintenance also presents certain challenges and disadvantages that organizations should consider.
1. Initial Investment
Implementing Smart Maintenance requires significant upfront investment in IoT sensors, data analytics tools, and employee training. Small and medium-sized enterprises (SMEs) may find this cost prohibitive.
2. Data Security Concerns
The reliance on cloud computing and interconnected devices raises concerns about data security. Manufacturing companies must invest in robust cybersecurity measures to protect sensitive information.
3. Integration Issues
Integrating Smart Maintenance technologies with existing legacy systems can be complex and time-consuming. Compatibility issues may arise, requiring additional resources for successful implementation.
4. Skill Gap
The adoption of advanced technologies necessitates a skilled workforce capable of managing and analyzing data. Companies may need to invest in training programs to bridge this skill gap.
Best Practices for Implementing Smart Maintenance
To maximize the benefits of Smart Maintenance, organizations should adhere to these best practices.
1. Conduct a Thorough Assessment
Before implementation, conduct a comprehensive assessment of existing equipment, processes, and maintenance practices. Identify areas where Smart Maintenance can provide the most value.
2. Start Small
Begin with a pilot project to test the feasibility of Smart Maintenance strategies. Select a specific line or piece of equipment for initial deployment, and evaluate the results before scaling up.
3. Invest in Training
Equip your workforce with the necessary skills to manage and analyze data. Training programs should cover the use of IoT sensors, data analytics tools, and predictive maintenance software.
4. Collaborate with Suppliers
Work closely with suppliers to ensure the availability of compatible IoT devices and sensors. Collaborative efforts can lead to the development of customized solutions tailored to specific manufacturing needs.
5. Focus on Data Quality
Ensure the accuracy and reliability of data collected by IoT sensors. High-quality data is essential for effective predictive maintenance and informed decision-making.
Supplier Negotiation Techniques
Effective supplier negotiation is crucial for the successful implementation of Smart Maintenance strategies.
1. Understand Market Conditions
Stay informed about market trends and the availability of IoT devices and sensors. This knowledge will help you negotiate better prices and terms with suppliers.
2. Leverage Long-Term Relationships
Building long-term relationships with suppliers can lead to more favorable terms and conditions. Suppliers may offer discounts, extended warranties, and priority support to trusted partners.
3. Consider Total Cost of Ownership
When negotiating with suppliers, consider the total cost of ownership (TCO) rather than just the initial price. Evaluate factors such as maintenance, support, and potential upgrades.
4. Emphasize Quality
Prioritize quality over cost when selecting suppliers for IoT devices and sensors. High-quality components ensure the reliability of Smart Maintenance systems and reduce the risk of failures.
5. Collaborate on Innovation
Engage suppliers in discussions about future innovations and developments. Collaborative efforts can lead to the creation of cutting-edge solutions that provide a competitive edge.
Practical Insights from the Field
Drawing from my extensive experience in procurement and purchasing, here are some practical insights for implementing Smart Maintenance in Japanese manufacturing.
1. Align with Corporate Goals
Ensure that Smart Maintenance initiatives align with the overall goals and objectives of the organization. This alignment is crucial for securing executive support and funding.
2. Monitor and Adjust
Continuous monitoring and periodic adjustments are essential for the success of Smart Maintenance strategies. Regular evaluations help identify areas for improvement and optimize performance.
3. Encourage Cross-Functional Collaboration
Smart Maintenance requires collaboration between different departments, including production, maintenance, IT, and procurement. Foster a culture of teamwork and open communication to facilitate smooth implementation.
4. Measure ROI
Track key performance indicators (KPIs) to measure the return on investment (ROI) of Smart Maintenance initiatives. Metrics such as OEE, downtime reduction, and cost savings provide valuable insights into the effectiveness of the strategy.
Future Trends in Smart Maintenance
As technology continues to evolve, several trends are expected to shape the future of Smart Maintenance in Japanese manufacturing.
1. Increased Adoption of AI
The adoption of AI and machine learning is expected to increase, leading to more accurate predictive maintenance models. AI-driven insights will further enhance decision-making and maintenance planning.
2. Integration with Industry 4.0
The integration of Smart Maintenance with Industry 4.0 technologies will create more interconnected and intelligent manufacturing environments. This will enable seamless communication between machines and systems.
3. Expansion of IIoT
The Industrial Internet of Things (IIoT) will continue to expand, with more devices and sensors being connected to the network. This will result in a richer dataset for analytics and improved maintenance capabilities.
4. Development of Digital Twins
Digital twins, virtual replicas of physical assets, will become more prevalent in Smart Maintenance. These digital models enable real-time monitoring, simulation, and optimization of maintenance activities.
5. Enhanced Cybersecurity
As the reliance on connected devices increases, cybersecurity measures will become more robust. Manufacturers will invest in advanced security protocols to protect their data and systems from cyber threats.
Conclusion
Smart Maintenance represents a significant opportunity for Japanese manufacturing companies to enhance their operational efficiency, reduce costs, and maintain a competitive edge in the global market. By understanding the key components, advantages, challenges, and best practices associated with Smart Maintenance, organizations can successfully implement this transformative strategy. Leveraging supplier negotiation techniques and practical insights from the field further enhances the likelihood of success. As technology continues to advance, staying informed about future trends will ensure that Japanese manufacturers remain at the forefront of innovation and excellence.
資料ダウンロード
QCD調達購買管理クラウド「newji」は、調達購買部門で必要なQCD管理全てを備えた、現場特化型兼クラウド型の今世紀最高の購買管理システムとなります。
ユーザー登録
調達購買業務の効率化だけでなく、システムを導入することで、コスト削減や製品・資材のステータス可視化のほか、属人化していた購買情報の共有化による内部不正防止や統制にも役立ちます。
NEWJI DX
製造業に特化したデジタルトランスフォーメーション(DX)の実現を目指す請負開発型のコンサルティングサービスです。AI、iPaaS、および先端の技術を駆使して、製造プロセスの効率化、業務効率化、チームワーク強化、コスト削減、品質向上を実現します。このサービスは、製造業の課題を深く理解し、それに対する最適なデジタルソリューションを提供することで、企業が持続的な成長とイノベーションを達成できるようサポートします。
オンライン講座
製造業、主に購買・調達部門にお勤めの方々に向けた情報を配信しております。
新任の方やベテランの方、管理職を対象とした幅広いコンテンツをご用意しております。
お問い合わせ
コストダウンが利益に直結する術だと理解していても、なかなか前に進めることができない状況。そんな時は、newjiのコストダウン自動化機能で大きく利益貢献しよう!
(Β版非公開)