- お役立ち記事
- Revolutionizing Japanese Manufacturing with Smart Maintenance: The Future is Here
Revolutionizing Japanese Manufacturing with Smart Maintenance: The Future is Here
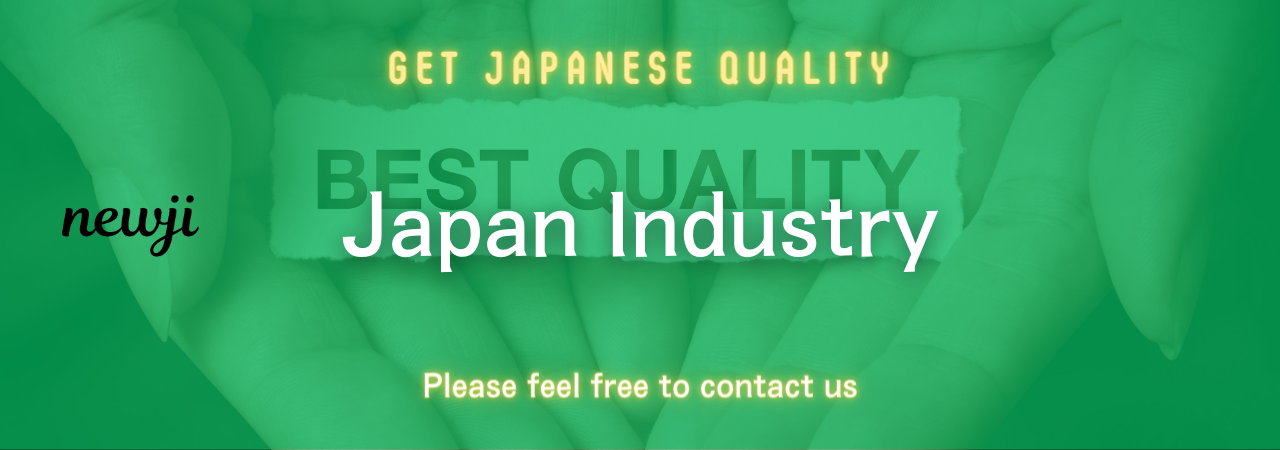
In the ever-evolving landscape of modern manufacturing, the concept of smart maintenance stands as a beacon of innovation and efficiency. Rooted in the principles of Industry 4.0, smart maintenance leverages advanced technologies to revolutionize traditional approaches to machinery upkeep and downtime management. For Japanese manufacturing, a sector renowned for its precision and high standards, the adoption of smart maintenance strategies represents not just an upgrade, but a true game-changer.
目次
The Core Concepts of Smart Maintenance
Smart maintenance encompasses the integration of the Internet of Things (IoT), artificial intelligence (AI), machine learning (ML), and big data analytics into the maintenance practices of manufacturing equipment. At its core, it seeks to transform reactive maintenance into proactive and predictive maintenance.
IoT and Sensors
IoT is pivotal in smart maintenance, as it involves embedding sensors in machinery to collect real-time data on various parameters such as temperature, vibration, and performance metrics. These sensors continuously monitor the condition of equipment and send this data to a centralized system for analysis.
Artificial Intelligence and Machine Learning
AI and ML play crucial roles in analyzing the vast amounts of data gathered by IoT devices. These technologies can identify patterns, predict potential failures, and suggest optimal maintenance schedules. The result is significantly enhanced decision-making processes based on data-driven insights.
Big Data Analytics
Big data analytics facilitates the processing of large datasets generated from IoT devices and other sources. By leveraging these analytics, manufacturers can gain a comprehensive view of their operations and make informed decisions to optimize maintenance schedules and resource allocation.
Advantages of Smart Maintenance
The implementation of smart maintenance within Japanese manufacturing offers multiple benefits that contribute to overall efficiency and competitiveness.
Reduced Downtime
With predictive maintenance enabled by IoT and AI, manufacturers can foresee potential equipment failures and address them before they occur. This minimizes unplanned downtime, ensuring continuous production and reducing associated costs.
Cost Savings
Proactive maintenance strategies help in managing repair costs more effectively by preventing catastrophic equipment failures. Regular, smaller maintenance tasks replace unexpected, large expenditures, leading to significant cost savings.
Enhanced Equipment Lifespan
Routine maintenance based on real-time data ensures that machinery is serviced optimally, which extends its operational life. This translates to long-term savings and better return on investment for high-cost manufacturing equipment.
Improved Production Quality
Consistent equipment performance results in fewer defects and higher-quality products. This high standard of production is essential for maintaining the reputation for excellence that Japanese manufacturers are famous for.
Environmental Benefits
Optimized maintenance schedules reduce energy consumption and waste, aligning with global sustainability goals and enhancing the company’s environmental credentials.
Challenges and Disadvantages
Despite the considerable benefits, the transition to smart maintenance is not without its challenges and potential downsides.
High Initial Investment
The implementation of IoT sensors, data analytics platforms, and AI solutions requires substantial initial investments. This includes costs related to technology acquisition, installation, and training of personnel.
Complex Integration
Integrating new smart maintenance systems with existing infrastructure can be complex and time-consuming. It often requires careful planning and transition strategies to avoid disrupting ongoing operations.
Data Security Concerns
The reliance on data for smart maintenance introduces significant security concerns. Ensuring that sensitive information is protected from cyber threats is paramount, necessitating robust cybersecurity measures.
Skillset Requirements
The shift towards smart maintenance demands a workforce equipped with new skills in data analytics, IoT, and AI. Training and development programs become crucial to empower employees with the necessary competencies.
Approaching Supplier Negotiations
Working with Japanese suppliers requires a nuanced approach that respects cultural norms and emphasizes long-term relationships.
Building Trust
Japanese business culture places a high value on trust and mutual respect. Investing time in understanding your supplier’s values and practices can lead to more fruitful negotiations and stronger partnerships.
Clear Communication
Ensure that communication is clear and detailed, with a focus on mutual benefits. Providing concise, well-structured proposals and being transparent about your expectations fosters better understanding and cooperation.
Flexible Negotiation
Flexibility and patience are important in negotiations. Japanese suppliers appreciate a considered approach that allows for adjustments and collaborative problem-solving.
Current Market Conditions
The market for smart manufacturing solutions in Japan is rapidly growing, driven by the country’s commitment to maintaining its leading edge in technology and manufacturing excellence.
Government Initiatives
The Japanese government supports the adoption of advanced manufacturing technologies through various initiatives and subsidies. These policies are designed to promote innovation and help companies transition to smart maintenance and other Industry 4.0 practices.
Industry Trends
There is a clear trend towards the integration of AI and IoT in manufacturing processes. Companies that adopt these technologies early are likely to gain a competitive advantage in terms of efficiency, cost savings, and product quality.
Best Practices for Implementing Smart Maintenance
To successfully implement smart maintenance, companies should follow a set of best practices that ensure smooth transition and maximized benefits.
Comprehensive Assessment
Conduct a thorough assessment of your current maintenance practices and identify areas where smart maintenance can have the most impact. This includes evaluating existing equipment, available technologies, and workforce capabilities.
Pilot Projects
Before a full-scale implementation, start with pilot projects to test the feasibility and effectiveness of smart maintenance solutions. Analyze the results to fine-tune your approach and address any potential issues.
Collaboration with Experts
Collaborating with technology providers and experts can provide invaluable insights and assistance. These partners can help navigate the complexities of integration and ensure that you achieve the desired outcomes.
Continuous Training
Invest in continuous training programs for your employees to keep them abreast of the latest technologies and best practices. A well-trained workforce is crucial for the successful implementation and ongoing management of smart maintenance systems.
Data-Driven Decision Making
Leverage the data collected from IoT devices and analysis tools to make informed decisions. Develop a culture of data-driven decision-making that permeates all levels of the organization.
Conclusion
Smart maintenance is a transformative approach that stands to revolutionize Japanese manufacturing. By leveraging IoT, AI, and big data, manufacturers can achieve unprecedented levels of efficiency, cost savings, and production quality. While there are challenges to overcome, the benefits far outweigh the disadvantages. Through strategic planning, careful execution, and continuous improvement, companies can embrace this innovative maintenance methodology and secure their position at the forefront of global manufacturing excellence.
資料ダウンロード
QCD調達購買管理クラウド「newji」は、調達購買部門で必要なQCD管理全てを備えた、現場特化型兼クラウド型の今世紀最高の購買管理システムとなります。
ユーザー登録
調達購買業務の効率化だけでなく、システムを導入することで、コスト削減や製品・資材のステータス可視化のほか、属人化していた購買情報の共有化による内部不正防止や統制にも役立ちます。
NEWJI DX
製造業に特化したデジタルトランスフォーメーション(DX)の実現を目指す請負開発型のコンサルティングサービスです。AI、iPaaS、および先端の技術を駆使して、製造プロセスの効率化、業務効率化、チームワーク強化、コスト削減、品質向上を実現します。このサービスは、製造業の課題を深く理解し、それに対する最適なデジタルソリューションを提供することで、企業が持続的な成長とイノベーションを達成できるようサポートします。
オンライン講座
製造業、主に購買・調達部門にお勤めの方々に向けた情報を配信しております。
新任の方やベテランの方、管理職を対象とした幅広いコンテンツをご用意しております。
お問い合わせ
コストダウンが利益に直結する術だと理解していても、なかなか前に進めることができない状況。そんな時は、newjiのコストダウン自動化機能で大きく利益貢献しよう!
(Β版非公開)