- お役立ち記事
- “Revolutionizing Manufacturing: The Impact of Coating Wires (コーティングワイヤ) on Industry Innovation”
“Revolutionizing Manufacturing: The Impact of Coating Wires (コーティングワイヤ) on Industry Innovation”
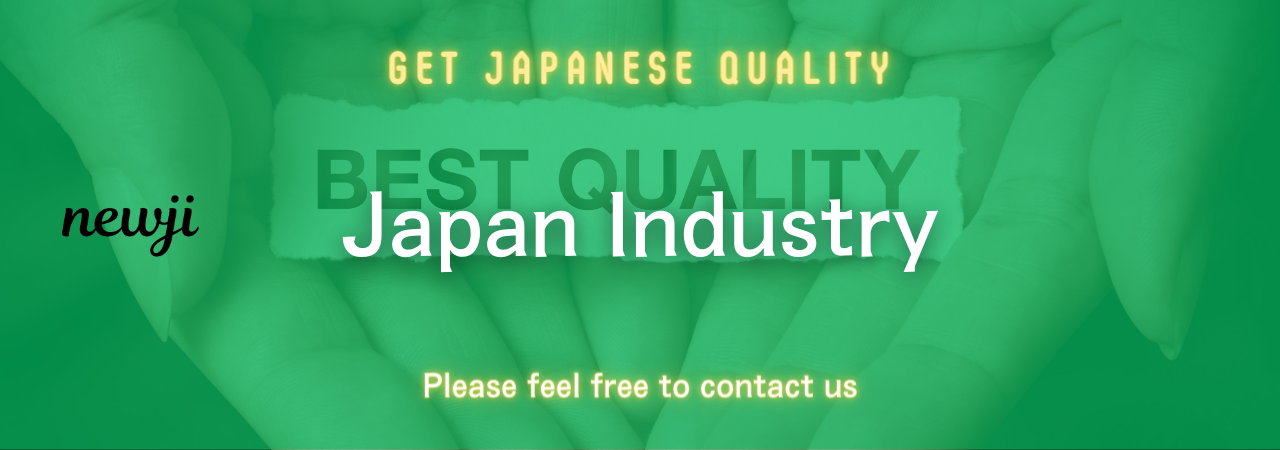
In the world of manufacturing, innovation drives progress. One particular advancement making waves in this sector is the development and application of coating wires, or コーティングワイヤ in Japanese. These coated wires are revolutionizing various industries by enhancing product quality, extending durability, and improving efficiency in processes.
目次
What Are Coating Wires?
Coating wires are essentially wires that have been coated with a layer of material to provide additional properties.
This coating can be metallic, polymeric, or ceramic, depending on the intended application.
Common coatings include tin, nickel, silver, and various types of plastics.
The process involves applying a uniform layer over the wire through methods such as electroplating, extrusion, or even chemical vapor deposition.
The result is a wire with improved characteristics compared to its uncoated counterpart.
Benefits of Coating Wires
The advantages of using coating wires are numerous and span across different facets of manufacturing.
Enhanced Durability
One of the most significant benefits is enhanced durability.
Coating provides a protective barrier against environmental factors like corrosion, oxidation, and physical wear and tear.
This means that coated wires can last longer, reducing the need for frequent replacements.
Improved Electrical Conductivity
In applications involving electrical signals, coating wires with materials like silver or tin can significantly improve their conductivity.
This ensures efficient transmission of electrical signals with minimal loss.
For example, in the electronics industry, superior conductivity is essential for the performance and reliability of devices.
Thermal Resistance
Certain coatings can also improve the thermal resistance of wires.
This is particularly important in environments exposed to high temperatures.
Ceramic coatings, for example, can withstand extreme heat, making them suitable for use in aerospace and automotive industries.
Enhanced Flexibility
Coating wires with flexible materials, such as specific polymers, can enhance their flexibility without compromising strength.
This allows for easier manipulation during manufacturing processes and installation in complex assemblies.
Applications of Coating Wires
The versatility of coating wires means they find applications in a wide array of industries.
Here are some key sectors benefiting from this innovation.
Electronics
In the electronics industry, coated wires are pivotal in the production of circuit boards, connectors, and various other components.
The improved conductivity and durability ensure that electronic devices function optimally over a longer period.
Automotive
Automobiles rely heavily on wiring for everything from ignition systems to onboard computers.
Coating wires used in automotive applications are designed to withstand extreme temperatures and harsh conditions.
This results in more reliable and long-lasting vehicles.
Aerospace
Aerospace is another sector where the use of coating wires is crucial.
The high thermal resistance and durability provided by coatings ensure that wiring systems in aircraft can operate under extreme conditions without failure.
Medical Devices
In the medical field, coating wires are often used in devices that require high precision and reliability.
For instance, coated wires are essential in medical imaging equipment and diagnostics tools, providing consistent performance and safety.
Telecommunications
The telecommunications industry also benefits from the use of coating wires, especially in long-distance data transmission.
The enhanced durability and conductivity help maintain the integrity of signals over long distances, ensuring effective communication.
The Manufacturing Process of Coating Wires
The manufacturing process of coating wires is precise and involves several key steps.
Understanding this process can provide insights into why these wires are so effective.
Surface Preparation
The first step is to prepare the surface of the wire to ensure optimal adhesion of the coating.
This typically involves cleaning the wire to remove any contaminants like oils, rust, or dirt.
The surface is then often roughened to improve the mechanical bonding of the coating.
Application of Coating
The next step is the actual application of the coating.
This can be done through various methods, each suited for different types of coatings and applications.
Electroplating involves depositing a thin layer of metal onto the wire using an electric current.
Extrusion involves coating the wire with a plastic or polymer by forcing the material around the wire through a die.
Chemical vapor deposition is another method, where a chemical vapor reacts with the surface of the wire to form a solid coating.
Curing and Finishing
After the coating is applied, it often needs to be cured or treated to achieve the desired properties.
This might involve heating, cooling, or chemical treatments.
The coated wire is then typically inspected for quality assurance to ensure that it meets the required standards.
Challenges and Future Prospects
While the benefits of coating wires are clear, there are still challenges to be addressed.
Cost
The cost of materials and the manufacturing process can be high.
However, the long-term benefits often outweigh the initial investment.
Technical Limitations
Finding the right combination of materials for specific applications can be complex.
Ongoing research and development are crucial to overcoming these challenges.
Environmental Impact
There is also a growing need to develop environmentally friendly coatings and processes.
Innovations in this area are vital for sustainable manufacturing practices.
The future prospects for coating wires are promising.
With advancements in technology, the capabilities of these wires will continue to expand, offering even more benefits to various industries.
The ongoing research into new materials and methods will undoubtedly lead to even more innovative applications.
In summary, coating wires are a significant advancement in the manufacturing sector, providing numerous benefits such as enhanced durability, improved conductivity, thermal resistance, and flexibility.
These advantages make them indispensable across various industries, including electronics, automotive, aerospace, medical devices, and telecommunications.
As research and development continue to push the boundaries, the future of coating wires looks brighter than ever, promising further innovation and efficiency in manufacturing processes.
資料ダウンロード
QCD調達購買管理クラウド「newji」は、調達購買部門で必要なQCD管理全てを備えた、現場特化型兼クラウド型の今世紀最高の購買管理システムとなります。
ユーザー登録
調達購買業務の効率化だけでなく、システムを導入することで、コスト削減や製品・資材のステータス可視化のほか、属人化していた購買情報の共有化による内部不正防止や統制にも役立ちます。
NEWJI DX
製造業に特化したデジタルトランスフォーメーション(DX)の実現を目指す請負開発型のコンサルティングサービスです。AI、iPaaS、および先端の技術を駆使して、製造プロセスの効率化、業務効率化、チームワーク強化、コスト削減、品質向上を実現します。このサービスは、製造業の課題を深く理解し、それに対する最適なデジタルソリューションを提供することで、企業が持続的な成長とイノベーションを達成できるようサポートします。
オンライン講座
製造業、主に購買・調達部門にお勤めの方々に向けた情報を配信しております。
新任の方やベテランの方、管理職を対象とした幅広いコンテンツをご用意しております。
お問い合わせ
コストダウンが利益に直結する術だと理解していても、なかなか前に進めることができない状況。そんな時は、newjiのコストダウン自動化機能で大きく利益貢献しよう!
(Β版非公開)