- お役立ち記事
- Revolutionizing Precision: How Japanese OEM Innovations are Leading the Way in Lapping and Polishing Processes
Revolutionizing Precision: How Japanese OEM Innovations are Leading the Way in Lapping and Polishing Processes
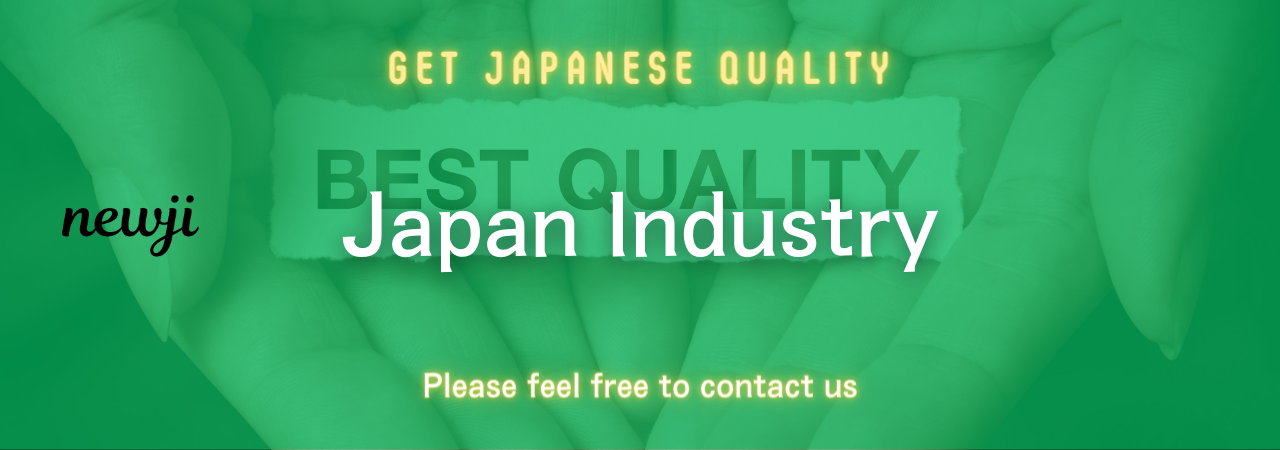
目次
Introduction to Japanese OEM Innovations in Lapping and Polishing
In the landscape of global manufacturing, precision is a cornerstone of success.
Japanese Original Equipment Manufacturers (OEMs) have long been at the forefront of developing advanced technologies that enhance manufacturing processes.
Among these innovations, advancements in lapping and polishing stand out as pivotal in achieving unparalleled precision.
This article aims to highlight the contributions of Japanese OEMs in revolutionizing lapping and polishing processes, providing practical insights for procurement and purchasing professionals.
Understanding Lapping and Polishing Processes
Lapping and polishing are crucial finishing processes in the manufacturing sector.
These techniques are employed to produce surfaces with extremely tight tolerances and minimal deviations.
Lapping is primarily used to create flat surfaces, while polishing is aimed at producing a mirror-like finish.
Both processes are vital in sectors such as electronics, automotive, aerospace, and medical devices, where exceptional surface quality is non-negotiable.
The Role of Japanese OEMs in Innovation
Japan’s commitment to precision extends beyond just creating superior products; it encompasses continuous process improvements.
Japanese OEMs have pioneered several innovations in lapping and polishing, ensuring that manufacturing processes are as precise and efficient as possible.
These innovations include the development of advanced abrasives, automated machinery, and real-time monitoring systems.
Advantages of Japanese OEMs in Lapping and Polishing
Cutting-Edge Technology
Japanese manufacturers are known for their early adoption of cutting-edge technologies.
In lapping and polishing, this means utilising high-precision equipment that achieves exacting surface finishes.
Advanced machinery, developed by Japanese OEMs, integrates automation, thereby reducing human error and increasing consistency.
Innovation in Abrasive Materials
A key area where Japanese OEMs excel is in the innovation of abrasive materials.
These materials play a crucial role in both lapping and polishing.
Japanese suppliers often use diamond abrasives, which provide superior hardness and longevity.
Innovative bonding techniques ensure that abrasives maintain their efficacy over extended use.
Consistency and Reliability
Japanese OEMs are renowned for their dedication to consistency and reliability.
The machinery and materials produced are subjected to rigorous quality control measures.
This ensures that every batch meets the stringent requirements set by industry standards, reducing variability in the final product.
Environmental Considerations
In recent years, there has been a significant push towards environmentally friendly manufacturing practices.
Japanese OEMs have responded positively by developing equipment and techniques that minimise waste and reduce the environmental impact.
This is achieved through efficient material use and recycling strategies, which are incorporated into the design and execution of lapping and polishing processes.
Challenges and Disadvantages
High Initial Costs
One of the primary challenges associated with procuring from Japanese OEMs is the high initial investment.
Advanced machinery and high-quality materials often come at a premium.
While the long-term benefits and ROI can justify these costs, the upfront expenditure can be a barrier for some organisations.
Logistical Complexities
Procurement from Japan can also involve logistical complexities including shipping, customs, and potential delays.
These factors can affect the lead times and overall supply chain efficiency.
Purchasing managers need to account for these potential issues and plan accordingly to mitigate risks.
Cultural and Communication Barriers
Working with Japanese suppliers often involves navigating cultural and communication differences.
While Japanese companies are known for their professionalism and attention to detail, initial negotiations and relationship-building can be complex.
It is essential for procurement professionals to understand these cultural nuances and employ effective communication strategies.
Best Practices for Supplier Negotiations
Building Relationships
Japanese business culture places a high value on building long-term relationships rather than focusing solely on individual transactions.
Invest time in understanding the supplier’s business values and build rapport.
This approach will foster trust and lead to more robust and fruitful partnerships.
Understanding Quality Standards
Japan has some of the highest quality standards in the manufacturing world.
Ensure that your quality expectations are well-documented and communicated clearly.
Providing detailed specifications and being transparent about your quality requirements will help in aligning both parties’ standards.
Leveraging Technological Expertise
Take advantage of the technological expertise offered by Japanese OEMs.
Engage in technical discussions with your suppliers to understand the capabilities and limitations of the machinery and materials being offered.
This knowledge will empower you to make informed decisions and negotiate more effectively.
Market Conditions and Future Trends
Increasing Demand for Precision Manufacturing
The global demand for precision manufacturing continues to grow, driven by advancements in technology and increased consumer expectations.
Sectors such as semiconductors, aerospace, and medical devices are expanding, necessitating more precise lapping and polishing solutions.
Japanese OEMs are well-positioned to meet this demand through continual innovation and high-quality production standards.
Integration of Automation and AI
Automation and Artificial Intelligence (AI) are becoming more integrated into manufacturing processes.
Japanese OEMs are leading the way in incorporating these technologies into lapping and polishing equipment.
This trend will enhance efficiency, reduce errors, and enable real-time process adjustments, contributing to superior outcomes.
Environmental Sustainability
Sustainability is no longer just a corporate responsibility but a market expectation.
Future trends show a growing emphasis on eco-friendly practices, and Japanese OEMs are likely to continue pioneering solutions that align with these values.
This may include further advancements in material recycling, energy-efficient machinery, and waste minimization.
Conclusion
Japanese OEMs have significantly impacted the lapping and polishing sector through their commitment to precision, innovation, and quality.
While there are challenges involved, the advantages they offer often outweigh the drawbacks.
Procurement professionals who understand the intricacies of supplier negotiations and market conditions will find substantial benefits in partnering with Japanese manufacturers.
By embracing the innovations in lapping and polishing from Japanese OEMs, companies can achieve higher precision, reliability, and environmental sustainability in their production processes, setting themselves apart in an increasingly competitive market.
資料ダウンロード
QCD調達購買管理クラウド「newji」は、調達購買部門で必要なQCD管理全てを備えた、現場特化型兼クラウド型の今世紀最高の購買管理システムとなります。
ユーザー登録
調達購買業務の効率化だけでなく、システムを導入することで、コスト削減や製品・資材のステータス可視化のほか、属人化していた購買情報の共有化による内部不正防止や統制にも役立ちます。
NEWJI DX
製造業に特化したデジタルトランスフォーメーション(DX)の実現を目指す請負開発型のコンサルティングサービスです。AI、iPaaS、および先端の技術を駆使して、製造プロセスの効率化、業務効率化、チームワーク強化、コスト削減、品質向上を実現します。このサービスは、製造業の課題を深く理解し、それに対する最適なデジタルソリューションを提供することで、企業が持続的な成長とイノベーションを達成できるようサポートします。
オンライン講座
製造業、主に購買・調達部門にお勤めの方々に向けた情報を配信しております。
新任の方やベテランの方、管理職を対象とした幅広いコンテンツをご用意しております。
お問い合わせ
コストダウンが利益に直結する術だと理解していても、なかなか前に進めることができない状況。そんな時は、newjiのコストダウン自動化機能で大きく利益貢献しよう!
(Β版非公開)