- お役立ち記事
- Revolutionizing Precision: The Air Micrometer DI-1000 and Japan’s Cutting-Edge Manufacturing Techniques
Revolutionizing Precision: The Air Micrometer DI-1000 and Japan’s Cutting-Edge Manufacturing Techniques
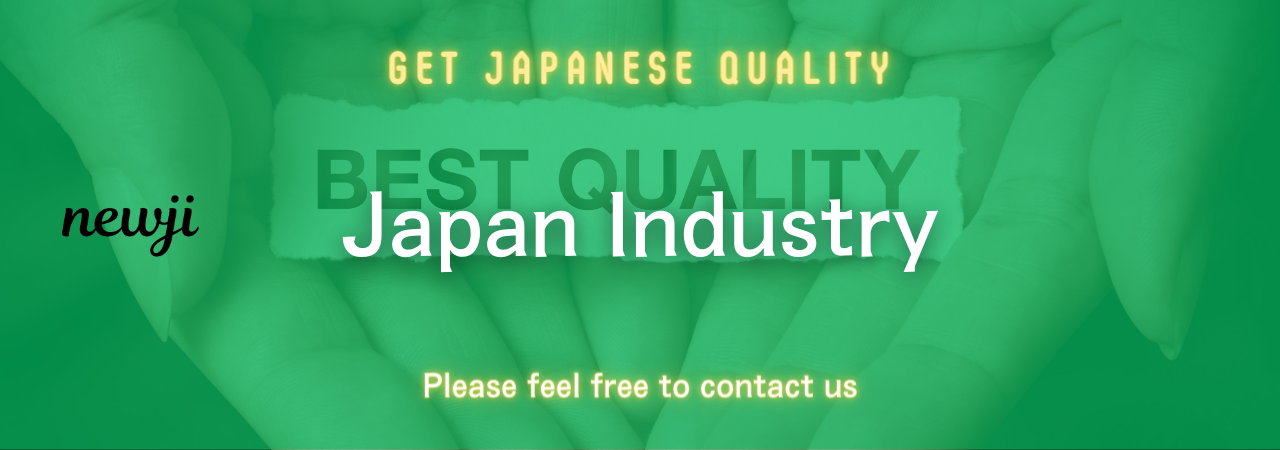
目次
Introduction to the Air Micrometer DI-1000
The Air Micrometer DI-1000 represents a significant advancement in precision measurement technology.
This innovative tool is designed to provide highly accurate measurements in various industrial applications.
Its integration into manufacturing processes can lead to enhanced quality control and increased operational efficiency.
Developed with cutting-edge technology, the DI-1000 sets a new standard for precision in the industry.
Japanese Manufacturing Techniques: A Benchmark of Excellence
Japan has long been recognized for its superior manufacturing techniques.
The principles of Kaizen, Just-In-Time (JIT) production, and Total Quality Management (TQM) are central to Japanese manufacturing.
These methodologies focus on continuous improvement, waste reduction, and maintaining the highest quality standards.
Japanese manufacturers prioritize precision and reliability, which align perfectly with the capabilities of the Air Micrometer DI-1000.
Procurement Strategies for Japanese Precision Instruments
Effective procurement strategies are essential for acquiring high-quality tools like the DI-1000.
Understanding the Japanese market and supplier landscape can provide significant advantages.
Building strong relationships with Japanese suppliers ensures reliable access to cutting-edge technology.
Leveraging Japan’s reputation for precision manufacturing can enhance the procurement process.
Advantages of Sourcing from Japanese Suppliers
Japanese suppliers are known for their commitment to quality and precision.
They offer advanced technology and innovative solutions that can significantly benefit manufacturing operations.
Sourcing from Japan provides access to tools that adhere to strict international standards.
Additionally, Japanese companies often provide excellent after-sales support and technical assistance.
Challenges in Procuring Japanese Manufacturing Equipment
Despite the advantages, procuring equipment from Japan can present challenges.
Language barriers and cultural differences may complicate negotiations and communications.
Lead times for shipping and delivery from Japan can be longer compared to domestic suppliers.
Import regulations and tariffs may also impact the overall cost and feasibility of procurement.
Supplier Negotiation Techniques for Successful Partnerships
Effective negotiation with Japanese suppliers requires a strategic approach.
Understanding Japanese business culture is crucial for building trust and fostering long-term partnerships.
Respect, patience, and clear communication are key elements in successful negotiations.
Collaborative problem-solving and mutual respect can lead to favorable terms and strong supplier relationships.
Building Trust with Japanese Suppliers
Trust is a cornerstone of Japanese business relationships.
Demonstrating reliability, consistency, and a commitment to quality can help establish trust.
Regular communication and visits to supplier facilities can strengthen the partnership.
Honoring agreements and maintaining transparency are essential for long-term success.
Negotiation Tactics Tailored to Japanese Business Practices
Japanese negotiations often involve a focus on consensus and collective decision-making.
Patience is required, as decisions may take longer to reach due to the need for internal consultations.
Emphasizing mutual benefits and long-term collaboration can enhance negotiation outcomes.
Flexibility and adaptability in negotiations can help address any unforeseen challenges.
Market Conditions Impacting Precision Measurement Tools
The market for precision measurement tools like the DI-1000 is influenced by various factors.
Global demand for high-precision manufacturing is increasing, driven by advancements in technology and industry standards.
Economic conditions, such as fluctuations in currency exchange rates, can affect the cost of procurement.
Competitive pressures and innovation in measurement technologies also play a significant role in shaping the market.
Trends in Precision Measurement Technology
Advancements in digital and automated measurement systems are driving the market forward.
Integration with Industry 4.0 and smart manufacturing practices is becoming increasingly important.
There is a growing demand for measurement tools that offer higher accuracy, faster processing speeds, and greater ease of use.
Sustainability and energy efficiency are also influencing the development of new measurement technologies.
Economic Factors Affecting Procurement from Japan
Economic stability in Japan supports consistent supply and reliable quality from suppliers.
However, fluctuations in the global economy can impact purchasing power and procurement costs.
Exchange rate volatility can affect the overall pricing of Japanese equipment.
Understanding these economic factors is essential for effective budgeting and cost management.
Best Practices for Integrating the DI-1000 into Manufacturing Processes
Successful integration of the DI-1000 requires careful planning and execution.
Aligning the tool’s capabilities with specific manufacturing needs ensures optimal performance.
Training staff on the proper use and maintenance of the DI-1000 is crucial for maximizing its benefits.
Continuous monitoring and evaluation can help identify areas for improvement and ensure sustained efficiency.
Optimizing Production Workflow with the DI-1000
The DI-1000 can streamline production workflows by providing accurate and reliable measurements.
Integrating the micrometer into existing quality control systems enhances data accuracy and traceability.
Automation features of the DI-1000 can reduce manual intervention and increase measurement speed.
Optimizing the placement and usage of the DI-1000 within the production line can lead to significant time savings.
Training and Skill Development for Effective Use
Comprehensive training programs for staff ensure that the DI-1000 is used effectively.
Understanding the technical specifications and operational procedures is essential for accurate measurements.
Regular training updates can keep the team informed about new features and best practices.
Skill development initiatives contribute to overall factory efficiency and product quality.
Advantages and Disadvantages of the Air Micrometer DI-1000
The Air Micrometer DI-1000 offers numerous advantages for precision measurement in manufacturing.
Its high accuracy and reliability enhance quality control processes.
The device’s advanced technology allows for seamless integration with automated systems.
However, there are also some disadvantages to consider when implementing the DI-1000.
Benefits of Using the DI-1000
The DI-1000 provides precise measurements, reducing the margin of error in manufacturing processes.
Its user-friendly interface and automation capabilities increase operational efficiency.
The durability and build quality of the DI-1000 ensure long-term reliability and minimal maintenance.
Enhanced data collection and analysis features support better decision-making and quality assurance.
Limitations and Considerations
The initial cost of the DI-1000 may be higher compared to traditional measurement tools.
Integration with existing systems may require additional investment in infrastructure.
Training and adaptation to the new technology can involve a learning curve for staff.
Dependence on advanced technology may pose challenges in environments with frequent power fluctuations or technical issues.
Implementing Quality Control with the DI-1000
Effective quality control is paramount in maintaining high manufacturing standards.
The DI-1000 plays a crucial role in ensuring that products meet required specifications.
By providing accurate measurements, the DI-1000 aids in identifying defects and deviations early in the production process.
Implementing systematic quality control procedures with the DI-1000 enhances overall product reliability and customer satisfaction.
Establishing Measurement Protocols
Developing standardized measurement protocols ensures consistency and accuracy across all production stages.
Defining measurement points and frequencies helps maintain uniform quality standards.
Regular calibration and maintenance of the DI-1000 are essential for sustained precision.
Documentation and record-keeping support traceability and compliance with industry standards.
Continuous Improvement through Data Analysis
Utilizing data collected by the DI-1000 enables continuous improvement in manufacturing processes.
Analyzing measurement data can reveal trends, patterns, and areas needing attention.
Implementing feedback loops based on data insights promotes ongoing enhancements in quality control.
Continuous improvement initiatives lead to higher efficiency, reduced waste, and better product quality.
Enhancing Factory Efficiency with Automation
Automation is a key driver of factory efficiency and competitiveness.
The DI-1000’s automation features contribute to streamlined operations and reduced manual labor.
Integrating the micrometer with automated production lines enhances measurement speed and accuracy.
Automation also supports real-time monitoring and instant adjustments, leading to optimized manufacturing processes.
Seamless Integration with Manufacturing Systems
Integrating the DI-1000 with existing manufacturing systems ensures seamless data flow and process synchronization.
Compatibility with Industry 4.0 technologies allows for enhanced connectivity and smart manufacturing capabilities.
Automated data collection and analysis reduce the need for manual intervention and minimize human error.
Seamless integration supports scalable and flexible manufacturing operations.
Reducing Downtime and Increasing Productivity
Automation features of the DI-1000 help in minimizing downtime by providing reliable and consistent measurements.
Real-time monitoring and instant alerts enable proactive maintenance and quick issue resolution.
Increased measurement speed enhances overall production throughput and productivity.
Efficient use of automation tools like the DI-1000 leads to cost savings and improved operational performance.
Leveraging Japanese Supplier Networks for Competitive Advantage
Building robust supplier networks in Japan can provide a significant competitive advantage.
Access to a wide range of high-quality tools and technologies supports superior manufacturing capabilities.
Collaborating with Japanese suppliers fosters innovation and continuous improvement in production processes.
Strong supplier networks enhance supply chain resilience and reliability, ensuring consistent quality and timely deliveries.
Developing Strategic Partnerships
Strategic partnerships with Japanese suppliers go beyond transactional relationships.
Collaborative efforts in product development and innovation can lead to mutually beneficial outcomes.
Sharing knowledge and expertise with suppliers fosters a culture of continuous improvement and excellence.
Long-term partnerships contribute to sustained competitiveness and market leadership.
Maximizing Supplier Relationships for Long-Term Success
Maximizing supplier relationships involves regular communication and collaboration.
Engaging in joint improvement initiatives and sharing feedback enhances product quality and service levels.
Recognizing and rewarding supplier performance fosters loyalty and commitment.
Strong supplier relationships support the development of reliable and high-quality manufacturing processes.
Conclusion: Embracing Precision and Excellence
The Air Micrometer DI-1000, combined with Japan’s cutting-edge manufacturing techniques, offers a powerful solution for enhancing precision and efficiency in manufacturing.
Effective procurement strategies, strategic supplier negotiations, and best practices in integration ensure that businesses can fully leverage the benefits of this advanced measurement tool.
By embracing these elements, manufacturers can achieve higher quality standards, increased productivity, and a strong competitive edge in the global market.
資料ダウンロード
QCD調達購買管理クラウド「newji」は、調達購買部門で必要なQCD管理全てを備えた、現場特化型兼クラウド型の今世紀最高の購買管理システムとなります。
ユーザー登録
調達購買業務の効率化だけでなく、システムを導入することで、コスト削減や製品・資材のステータス可視化のほか、属人化していた購買情報の共有化による内部不正防止や統制にも役立ちます。
NEWJI DX
製造業に特化したデジタルトランスフォーメーション(DX)の実現を目指す請負開発型のコンサルティングサービスです。AI、iPaaS、および先端の技術を駆使して、製造プロセスの効率化、業務効率化、チームワーク強化、コスト削減、品質向上を実現します。このサービスは、製造業の課題を深く理解し、それに対する最適なデジタルソリューションを提供することで、企業が持続的な成長とイノベーションを達成できるようサポートします。
オンライン講座
製造業、主に購買・調達部門にお勤めの方々に向けた情報を配信しております。
新任の方やベテランの方、管理職を対象とした幅広いコンテンツをご用意しております。
お問い合わせ
コストダウンが利益に直結する術だと理解していても、なかなか前に進めることができない状況。そんな時は、newjiのコストダウン自動化機能で大きく利益貢献しよう!
(Β版非公開)