- お役立ち記事
- Revolutionizing Precision: The Future of Japanese Manufacturing with Anodizing OEM Processing
月間76,176名の
製造業ご担当者様が閲覧しています*
*2025年3月31日現在のGoogle Analyticsのデータより
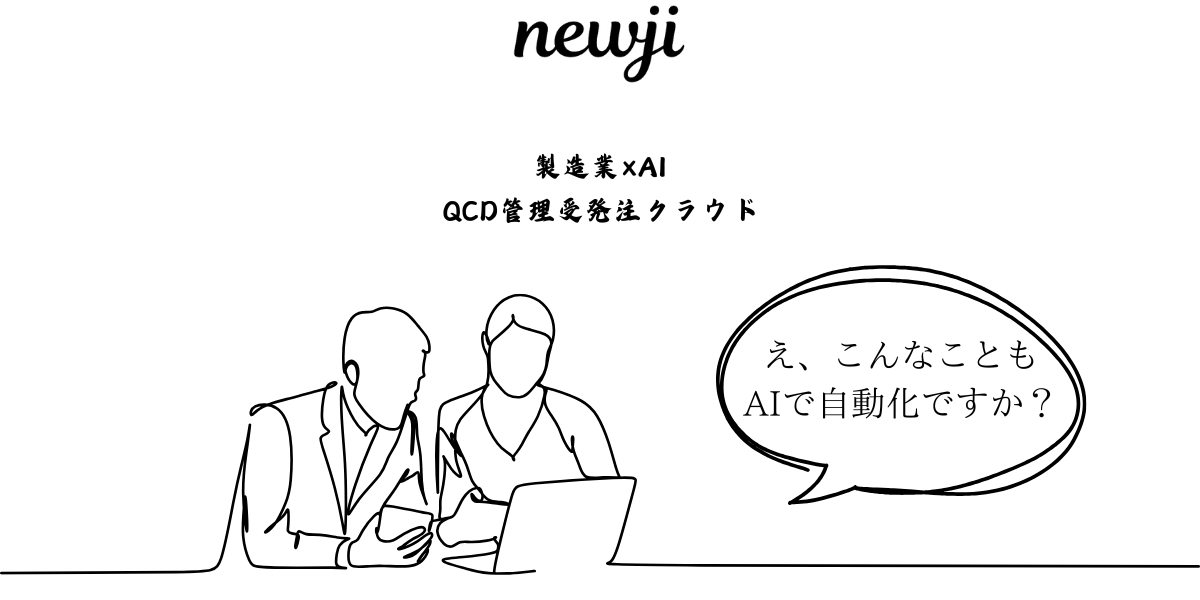
Revolutionizing Precision: The Future of Japanese Manufacturing with Anodizing OEM Processing
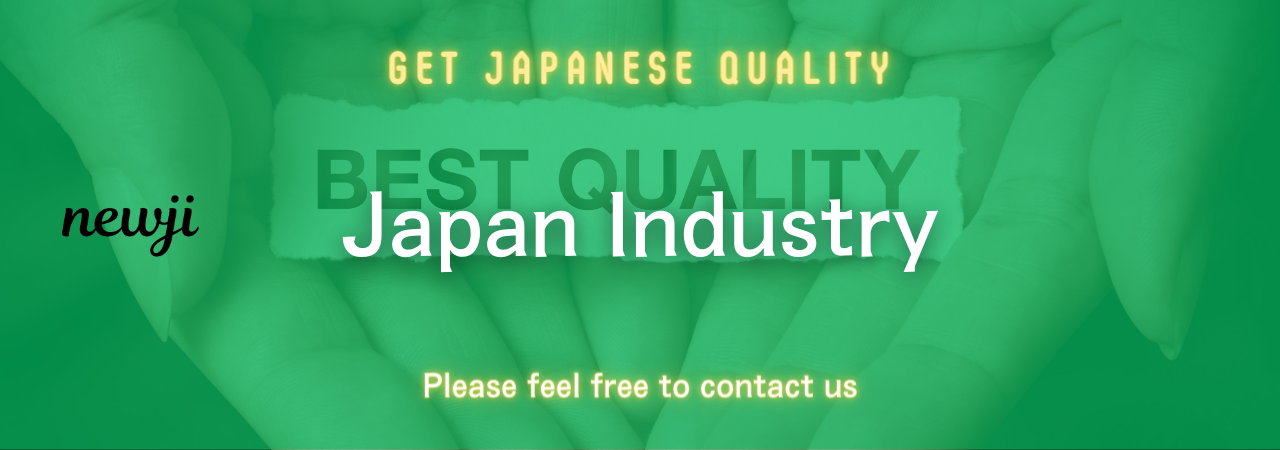
目次
Introduction to Anodizing OEM Processing
Anodizing is a unique electrochemical process that transforms the surface of metals, particularly aluminum, into a durable, corrosion-resistant, anodic oxide finish.
This finish not only improves aesthetic appeal but also enhances functional properties such as wear resistance and thermal conductivity.
Over the years, Japanese manufacturers have developed advanced anodizing techniques that set industry standards.
OEM, or Original Equipment Manufacturer, processing refers to the production of components that are designed to incorporate into other companies’ products.
In this context, companies leverage the specialized anodizing capabilities of Japanese manufacturers to enhance their products’ performance and aesthetics.
The Advantages of Anodizing OEM Processing
Aesthetic Versatility
One of the most significant advantages of anodizing is its ability to produce a variety of finishes.
Japanese manufacturers excel in creating vibrant, consistent colors and textures that meet client specifications.
This versatility is invaluable for industries ranging from consumer electronics to automotive, where product appearance is paramount.
Corrosion Resistance
Anodized layers serve as a protective barrier, significantly increasing resistance to corrosion.
This makes anodized products ideal for harsh environments, where durability is crucial.
Japanese manufacturers invest heavily in quality control to ensure that anodized layers meet stringent international standards, providing peace of mind for global clients.
Enhanced Durability
The anodizing process strengthens the surface of metals, making them more resistant to wear and tear.
This durability extends the product life cycle, reducing maintenance costs and downtime.
Japanese suppliers are known for their precision and attention to detail, ensuring consistent quality across large production runs.
Eco-Friendly Process
Anodizing is an environmentally friendly finishing process, emitting few harmful byproducts.
Japanese companies prioritize environmentally sustainable practices, often exceeding regulatory requirements.
This commitment to green manufacturing aligns with the growing demand for eco-conscious products in the global market.
Challenges and Disadvantages
Initial Cost
The primary drawback of anodizing is the initial cost involved in setting up the process.
Specialized equipment and strict process controls are necessary to achieve high-quality anodized finishes.
However, Japanese manufacturers offer scalable solutions that can mitigate these costs through economies of scale.
Process Complexity
Anodizing requires precise control of various parameters, including temperature, voltage, and chemical composition.
Any deviation can result in subpar finishes or inconsistencies.
Japanese manufacturers are renowned for their expertise and meticulous process control, but the complexity still necessitates experienced operators and rigorous monitoring.
Material Compatibility
Anodizing is most effective on aluminum and certain aluminum alloys.
This limits its applicability to other metal types, possibly restricting its use in diverse industries.
Japanese manufacturers continuously innovate to expand the range of materials that can be effectively anodized, but material compatibility remains a consideration.
Supplier Negotiations: Techniques and Best Practices
Understanding Market Dynamics
Effective supplier negotiation begins with a thorough understanding of market conditions.
In Japan, the anodizing industry is marked by high competition and technological advancements.
Keeping abreast of market trends, price fluctuations, and technological developments is crucial for informed negotiations.
Building Long-Term Relationships
Japanese business culture highly values long-term relationships and mutual trust.
Approaching negotiations with a collaborative mindset rather than a transactional one can yield long-term benefits.
Demonstrating a commitment to future business can often secure better terms and conditions.
Quality Over Cost
While cost competitiveness is important, prioritizing quality over low prices is essential in negotiations with Japanese suppliers.
Anodizing requires high precision and consistency, and cutting corners can lead to substandard results.
Japanese suppliers appreciate clients who value quality, often reciprocating with superior service and product offerings.
Transparent Communication
Clarity and honesty are vital in negotiations.
Clearly outlining your requirements, expectations, and constraints helps Japanese suppliers propose the most suitable solutions.
Transparency builds trust and avoids misunderstandings that can derail projects.
Leverage Technology
Japanese manufacturers are at the forefront of technological innovations.
Leveraging the latest technology in discussions can highlight your company’s forward-thinking approach and interest in high-quality results.
This can create a favorable impression and open doors to advanced anodizing techniques that may offer competitive advantages.
Understanding Market Conditions
Economic Influences
The global and Japanese economies inevitably impact the anodizing market.
Economic downturns can slow demand, while growth periods see increased investment in high-quality finishes.
Being aware of these cycles can help in timing negotiations and securing favorable contracts.
Technological Innovations
Japan’s relentless pursuit of innovation results in regular advancements in anodizing technology.
Staying updated on the latest trends and technologies positions your negotiations on solid ground, allowing you to request the latest processes that can differentiate your products.
Supply Chain Dynamics
Global supply chain issues, such as raw material shortages or logistical disruptions, can impact the cost and availability of anodizing services.
Japanese suppliers often exhibit remarkable resilience and adaptability, but understanding these dynamics can help in setting realistic expectations and contingency plans.
Best Practices for Procurement from Japanese Suppliers
Due Diligence
Thoroughly researching potential suppliers is the first step in successful procurement.
Look for suppliers with a proven track record, solid financial footing, and positive customer reviews.
Site visits and audits can provide deeper insights into a supplier’s capabilities and quality control measures.
Benchmarking
Regularly benchmarking against industry standards and other suppliers ensures you are obtaining competitive terms.
It helps identify areas where a supplier excels or needs improvement.
Japanese suppliers, known for their precision and quality, set high benchmarks, making it crucial to assess their performance continually.
Risk Management
Risk management is integral to procurement, covering everything from financial stability to geopolitical influences.
Developing a risk management plan that includes supplier diversification and contingency arrangements can protect your supply chain from disruptions.
Performance Metrics
Establishing clear performance metrics and regularly reviewing them ensures both parties are aligned with agreed standards.
Common metrics include delivery times, defect rates, and compliance with quality standards.
Japanese suppliers often have rigorous internal metrics and appreciate clients who uphold similar standards.
Continuous Improvement
The Japanese concept of Kaizen, or continuous improvement, is vital in maintaining competitive edges.
Collaborating with suppliers on process improvements, joint development projects, and feedback mechanisms fosters innovation and continuous quality enhancements.
Conclusion
Revolutionizing precision through anodizing OEM processing offers substantial benefits across various industries.
Japanese manufacturers, with their expertise, dedication to quality, and technological advancements, are at the forefront of this transformation.
However, success requires a thorough understanding of the anodizing process, effective negotiation strategies, and a proactive approach to supplier management.
By embracing these best practices, companies can fully leverage the advantages of anodizing OEM processing, ensuring high-quality, durable, and aesthetically superior products that meet the demands of a competitive global market.
資料ダウンロード
QCD管理受発注クラウド「newji」は、受発注部門で必要なQCD管理全てを備えた、現場特化型兼クラウド型の今世紀最高の受発注管理システムとなります。
ユーザー登録
受発注業務の効率化だけでなく、システムを導入することで、コスト削減や製品・資材のステータス可視化のほか、属人化していた受発注情報の共有化による内部不正防止や統制にも役立ちます。
NEWJI DX
製造業に特化したデジタルトランスフォーメーション(DX)の実現を目指す請負開発型のコンサルティングサービスです。AI、iPaaS、および先端の技術を駆使して、製造プロセスの効率化、業務効率化、チームワーク強化、コスト削減、品質向上を実現します。このサービスは、製造業の課題を深く理解し、それに対する最適なデジタルソリューションを提供することで、企業が持続的な成長とイノベーションを達成できるようサポートします。
製造業ニュース解説
製造業、主に購買・調達部門にお勤めの方々に向けた情報を配信しております。
新任の方やベテランの方、管理職を対象とした幅広いコンテンツをご用意しております。
お問い合わせ
コストダウンが利益に直結する術だと理解していても、なかなか前に進めることができない状況。そんな時は、newjiのコストダウン自動化機能で大きく利益貢献しよう!
(β版非公開)