- お役立ち記事
- “Revolutionizing Production: How Japanese Manufacturing is Leading the Way”
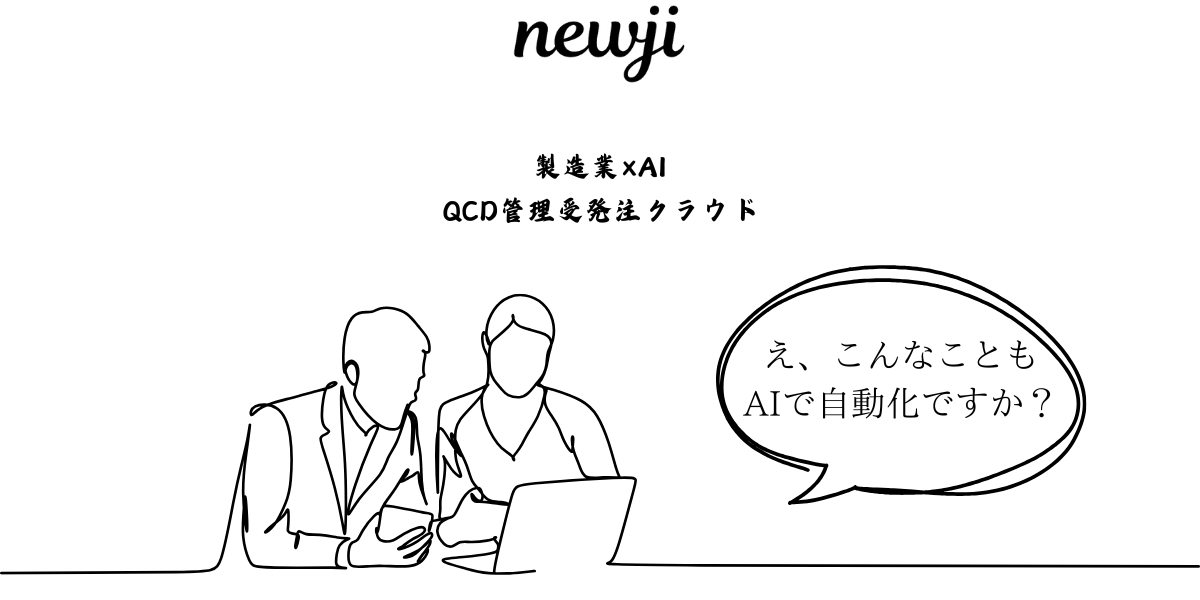
“Revolutionizing Production: How Japanese Manufacturing is Leading the Way”
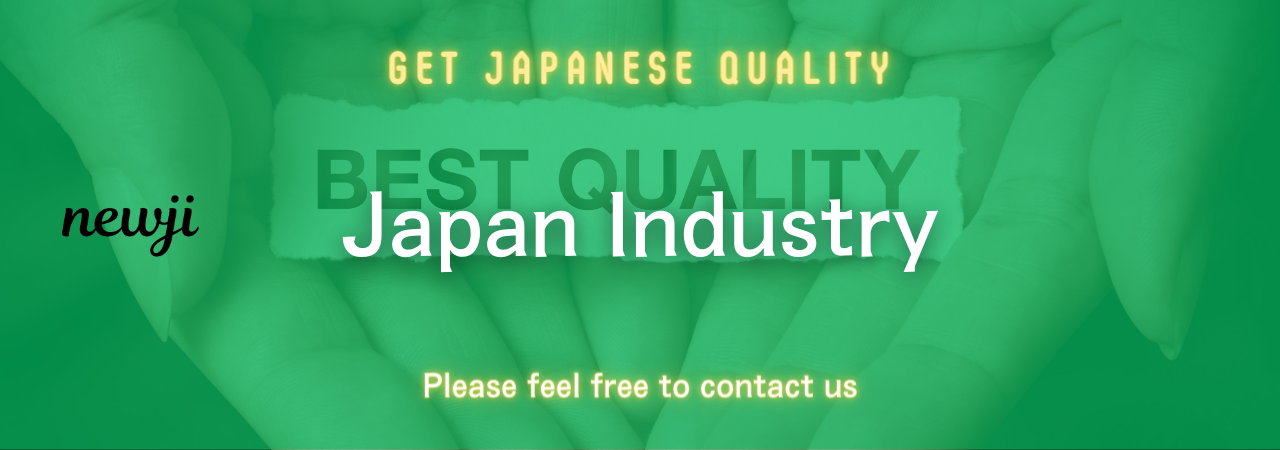
目次
Overview of Japanese Manufacturing Excellence
Japanese manufacturing has long been admired and emulated worldwide for its exceptional quality, efficiency, and innovation. Rooted in a deep-seated culture of craftsmanship and continuous improvement, often referred to as “Kaizen,” Japanese manufacturers have consistently set benchmarks in various industries, including automotive, electronics, machinery, and consumer goods. This excellence is not merely a result of advanced technology but also of robust management practices, meticulous attention to detail, and a relentless pursuit of perfection.
The legacy of Japanese manufacturing can be traced back to post-World War II reconstruction, where the focus was on rebuilding industries with an emphasis on quality and efficiency. Pioneering methodologies such as Total Quality Management (TQM) and Just-In-Time (JIT) production transformed Japanese factories into models of operational excellence. These practices have been widely adopted globally, significantly influencing manufacturing paradigms and supply chain management worldwide.
Key Advantages of Japanese Manufacturing
Superior Quality Control
One of the most significant advantages of Japanese manufacturing is its unwavering commitment to quality. Japanese companies implement rigorous quality control processes at every stage of production. Techniques such as Six Sigma and Statistical Process Control (SPC) are commonly employed to minimize defects and ensure that products meet the highest standards. This dedication to quality not only enhances customer satisfaction but also reduces costs associated with rework and returns.
Advanced Technological Integration
Japanese manufacturers are at the forefront of integrating advanced technologies into their production processes. Robotics, automation, and artificial intelligence are seamlessly incorporated to enhance precision, increase production rates, and reduce human error. Moreover, the adoption of Industry 4.0 principles, including the Internet of Things (IoT) and data analytics, enables real-time monitoring and optimization of manufacturing operations, leading to greater efficiency and flexibility.
Efficient Supply Chain Management
Efficiency in supply chain management is a hallmark of Japanese manufacturing. The Just-In-Time (JIT) inventory system, pioneered by Toyota, exemplifies this approach by ensuring that materials and components are delivered precisely when needed, minimizing inventory costs and reducing waste. Additionally, strong relationships with suppliers foster collaboration and reliability, further enhancing the overall supply chain performance.
Strong Emphasis on Continuous Improvement
The philosophy of continuous improvement, or Kaizen, is deeply ingrained in Japanese manufacturing culture. This approach encourages all employees, from top management to shop floor workers, to identify opportunities for incremental enhancements in processes, products, and services. By fostering a culture of constant learning and adaptation, Japanese manufacturers maintain their competitive edge and sustain long-term growth.
Technical Skills and Innovations in Japanese Manufacturing
Precision Engineering
Japanese manufacturers are renowned for their precision engineering capabilities. Whether in the production of automotive parts, electronics, or machinery, the ability to produce components with exact specifications is crucial. This precision ensures compatibility, reliability, and performance, which are essential for maintaining product quality and customer trust.
Lean Manufacturing Techniques
Lean manufacturing, a philosophy centered on eliminating waste and maximizing value, is extensively practiced in Japanese factories. Techniques such as value stream mapping, 5S (Sort, Set in order, Shine, Standardize, Sustain), and kanban systems are integral to streamlining operations and enhancing productivity. These methods not only reduce costs but also improve workflow efficiency and employee satisfaction.
Innovation in Materials and Processes
Japanese manufacturers continuously invest in research and development to innovate materials and manufacturing processes. Advanced composites, lightweight alloys, and high-strength materials are developed to meet the evolving demands of various industries. Additionally, innovative manufacturing processes, such as additive manufacturing (3D printing) and nanotechnology, are explored to create cutting-edge products with superior performance characteristics.
Sustainable Manufacturing Practices
Sustainability is a growing priority in Japanese manufacturing. Companies are adopting environmentally friendly practices, such as reducing energy consumption, minimizing waste, and utilizing renewable resources. Sustainable manufacturing not only addresses environmental concerns but also enhances operational efficiency and corporate reputation, aligning with global trends towards eco-friendly production.
Supplier Negotiation Techniques with Japanese Suppliers
Building Long-Term Relationships
Successful negotiations with Japanese suppliers hinge on the establishment of long-term, trust-based relationships. Japanese business culture places significant emphasis on mutual respect, reliability, and loyalty. Investing time in cultivating these relationships can lead to more favorable terms, better collaboration, and a willingness to accommodate special requests or adjustments in the partnership.
Understanding Cultural Nuances
Cultural understanding is critical when negotiating with Japanese suppliers. Practices such as bowing, exchanging business cards with both hands, and adhering to formal communication protocols demonstrate respect and appreciation for Japanese customs. Being aware of and sensitive to these cultural nuances can facilitate smoother negotiations and foster a more positive business environment.
Emphasizing Quality and Reliability
Japanese suppliers prioritize quality and reliability above all else. During negotiations, emphasizing your company’s commitment to these values aligns with the supplier’s priorities. Highlighting your own quality control measures, production standards, and reputation can build confidence and encourage the supplier to invest in the partnership, knowing that their products will be supported by a reliable buyer.
Flexibility and Adaptability
Demonstrating flexibility and adaptability can be advantageous in negotiations with Japanese suppliers. Being open to adjusting order sizes, delivery schedules, or payment terms in response to the supplier’s needs can strengthen the partnership. This willingness to accommodate can lead to more collaborative problem-solving and a more resilient supply chain.
Market Conditions and Trends in Japanese Manufacturing
Globalization and International Trade
Globalization has significantly influenced Japanese manufacturing, pushing companies to expand their presence in international markets. Japanese manufacturers are increasingly establishing production facilities abroad to cater to local markets, reduce shipping costs, and mitigate trade barriers. This global expansion enhances their competitiveness and responsiveness to diverse market demands.
Technological Advancements and Industry 4.0
The advent of Industry 4.0 is reshaping Japanese manufacturing by integrating digital technologies into the production process. This includes the use of IoT devices, big data analytics, and artificial intelligence to optimize operations, predict maintenance needs, and enhance product customization. These technological advancements enable Japanese manufacturers to stay ahead in innovation and maintain their leadership position.
Shift Towards Sustainable Practices
Sustainability remains a key trend in Japanese manufacturing. Companies are increasingly adopting green technologies, such as renewable energy sources, eco-friendly materials, and waste reduction initiatives. Compliance with international environmental standards and responding to consumer demand for sustainable products are driving this shift, positioning Japanese manufacturers as leaders in responsible production.
Aging Workforce and Talent Management
Japan faces demographic challenges, including an aging workforce, which impacts the manufacturing sector. To address this, Japanese companies are investing in automation, robotics, and advanced training programs to enhance workforce efficiency and attract younger talent. Additionally, fostering a work environment that values employee well-being and continuous learning is crucial for maintaining productivity and innovation.
Best Practices for Procurement and Purchasing from Japan
Thorough Supplier Evaluation
Conducting comprehensive evaluations of potential Japanese suppliers is essential before entering into procurement agreements. This includes assessing their financial stability, production capabilities, quality control systems, and compliance with international standards. Visiting supplier facilities and conducting audits can provide valuable insights into their operations and reliability.
Establish Clear Communication Channels
Effective communication is vital for successful procurement and purchasing from Japan. Establishing clear and consistent communication channels helps in articulating requirements, addressing issues promptly, and ensuring that both parties are aligned in their expectations. Utilizing formal communication methods and maintaining regular contact can prevent misunderstandings and foster a collaborative partnership.
Leverage Local Expertise
Engaging local experts or consultants who understand the Japanese market and business culture can enhance procurement strategies. These individuals can provide valuable guidance on negotiation techniques, cultural practices, and market trends, enabling more informed decision-making and smoother interactions with Japanese suppliers.
Implement Robust Contractual Agreements
Drafting detailed and robust contractual agreements is crucial when procuring from Japan. Contracts should clearly outline terms and conditions, including specifications, delivery schedules, pricing, quality standards, and dispute resolution mechanisms. Legal advisors familiar with Japanese law can ensure that contracts protect the interests of both parties and comply with relevant regulations.
Challenges and Disadvantages of Sourcing from Japan
Higher Production Costs
One of the primary challenges of sourcing from Japan is the higher production costs compared to some other manufacturing hubs. Factors such as higher labor costs, stringent quality standards, and advanced technological integration contribute to increased expenses. While the quality justifies the costs, budget-conscious companies may find this a significant hurdle.
Language and Communication Barriers
Language differences can pose challenges in communication with Japanese suppliers. Misunderstandings or delays in information exchange can hinder procurement processes and project timelines. Although many Japanese business professionals speak English, nuances and technical terms may still lead to occasional communication issues.
Cultural Differences
Cultural differences extend beyond language and can influence business practices, decision-making processes, and negotiation styles. Japanese companies may prioritize consensus-building and long-term relationships over quick decisions, which can slow down negotiations for companies accustomed to more direct and rapid transactional approaches.
Limited Flexibility in Customization
While Japanese manufacturers excel in quality and precision, they may have limited flexibility in customizing products to specific requirements, especially for smaller orders. The emphasis on standardized processes and economies of scale can make it challenging to accommodate unique or highly specialized requests without incurring additional costs or extended lead times.
Strategies for Overcoming Procurement Challenges
Invest in Language and Cultural Training
Addressing language and cultural barriers through training can enhance communication and relationship-building with Japanese suppliers. Investing in language courses for procurement teams and educating them on Japanese business etiquette and cultural norms can lead to more effective interactions and reduce misunderstandings.
Negotiate Long-Term Partnerships
Focusing on long-term partnerships rather than short-term transactions can alleviate some of the challenges associated with sourcing from Japan. Building trust and mutual understanding over time allows for more flexibility, better negotiation power, and collaborative problem-solving, which can mitigate issues related to cost and customization.
Utilize Technology for Enhanced Communication
Leveraging digital communication tools, such as video conferencing, collaboration platforms, and translation software, can bridge communication gaps and streamline procurement processes. These technologies facilitate real-time interactions, documentation sharing, and efficient information exchange, making it easier to manage complex procurement activities.
Optimize Procurement Processes
Streamlining internal procurement processes can help manage higher costs and lead times associated with sourcing from Japan. Implementing efficient procurement workflows, adopting just-in-time inventory practices, and using data analytics to forecast demand can reduce costs and improve responsiveness to market changes.
Conclusion
Japanese manufacturing continues to lead the global market through its unwavering commitment to quality, innovation, and efficiency. For companies engaged in international procurement and purchasing, leveraging the strengths of Japanese suppliers can result in superior products, reliable supply chains, and long-term competitive advantages. However, navigating the challenges of higher costs, language barriers, and cultural differences requires strategic planning and a deep understanding of Japanese business practices. By adopting best practices, investing in relationship-building, and embracing continuous improvement, companies can successfully harness the benefits of sourcing from Japan and drive their production capabilities to new heights.
資料ダウンロード
QCD調達購買管理クラウド「newji」は、調達購買部門で必要なQCD管理全てを備えた、現場特化型兼クラウド型の今世紀最高の購買管理システムとなります。
ユーザー登録
調達購買業務の効率化だけでなく、システムを導入することで、コスト削減や製品・資材のステータス可視化のほか、属人化していた購買情報の共有化による内部不正防止や統制にも役立ちます。
NEWJI DX
製造業に特化したデジタルトランスフォーメーション(DX)の実現を目指す請負開発型のコンサルティングサービスです。AI、iPaaS、および先端の技術を駆使して、製造プロセスの効率化、業務効率化、チームワーク強化、コスト削減、品質向上を実現します。このサービスは、製造業の課題を深く理解し、それに対する最適なデジタルソリューションを提供することで、企業が持続的な成長とイノベーションを達成できるようサポートします。
オンライン講座
製造業、主に購買・調達部門にお勤めの方々に向けた情報を配信しております。
新任の方やベテランの方、管理職を対象とした幅広いコンテンツをご用意しております。
お問い合わせ
コストダウンが利益に直結する術だと理解していても、なかなか前に進めることができない状況。そんな時は、newjiのコストダウン自動化機能で大きく利益貢献しよう!
(Β版非公開)