- お役立ち記事
- Revolutionizing Safety: How Japan’s Automatic Stop Function is Transforming Manufacturing
Revolutionizing Safety: How Japan’s Automatic Stop Function is Transforming Manufacturing
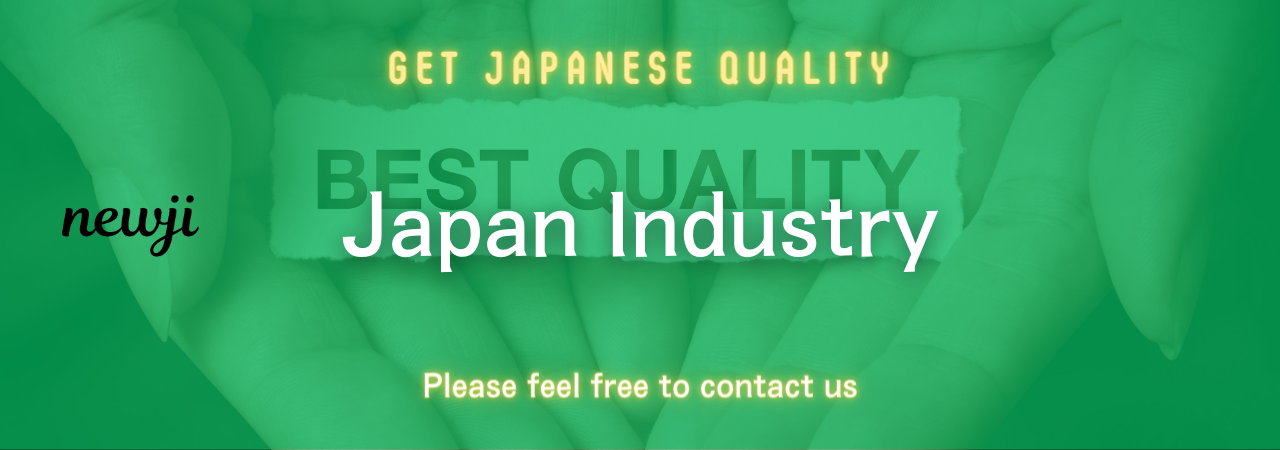
目次
Introduction to Japan’s Automatic Stop Function in Manufacturing
Japan has long been a leader in manufacturing innovation. One of their most significant advancements is the implementation of the automatic stop function. This technology is revolutionizing safety protocols across various industries.
The automatic stop function enhances workplace safety by immediately halting machinery operations during an emergency. This proactive measure minimizes the risk of accidents and ensures a safer environment for employees.
Importance of Safety in Manufacturing
Safety is a paramount concern in manufacturing settings. The industry involves complex machinery and processes that can pose significant risks to workers. Implementing effective safety measures is crucial to prevent accidents and ensure the well-being of employees.
Moreover, a safe workplace boosts employee morale and productivity. When workers feel secure, they are more likely to perform their tasks efficiently and with greater confidence.
How Japan’s Automatic Stop Function Works
Japan’s automatic stop function utilizes advanced sensors and control systems to monitor machinery operations continuously. These sensors detect anomalies or potential hazards in real-time.
Upon detecting a threat, the system triggers an immediate shutdown of the machinery. This swift response prevents accidents before they can occur, safeguarding both personnel and equipment.
Technological Components
The automatic stop function comprises several key components:
- Sensors: Detect changes in machine operation or environmental conditions.
- Control Units: Process sensor data and initiate shutdown protocols.
- Actuators: Execute the physical stopping of machinery.
Integration with Existing Systems
Integrating the automatic stop function with current manufacturing systems involves:
- Assessing compatibility with existing machinery.
- Upgrading control systems to accommodate new sensors.
- Training staff on the new safety protocols.
Advantages of Implementing the Automatic Stop Function
The automatic stop function offers numerous benefits for manufacturing companies:
- Enhanced Safety: Reduces the likelihood of workplace accidents.
- Increased Efficiency: Minimizes downtime by preventing severe equipment damage.
- Cost Savings: Lowers costs associated with accidents and machinery repairs.
- Compliance: Helps meet international safety standards and regulations.
Challenges and Considerations
While the automatic stop function presents significant advantages, manufacturers must address certain challenges:
- Initial Investment: Upfront costs for technology implementation.
- Training: Ensuring staff are adequately trained to operate and maintain the system.
- System Reliability: Maintaining high reliability to prevent false triggers or system failures.
Supplier Negotiation Techniques for Procurement
Effective supplier negotiation is critical when procuring the automatic stop function technology from Japanese suppliers. Here are some techniques to consider:
- Building Relationships: Establish trust and long-term partnerships with suppliers.
- Understanding Market Conditions: Stay informed about the market to leverage negotiation positions.
- Clear Communication: Clearly outline specifications, expectations, and contractual terms.
- Leveraging Expertise: Utilize in-house expertise to assess supplier capabilities and product quality.
Best Practices in Supplier Negotiation
Implementing best practices can lead to successful negotiations:
- Preparation: Research suppliers thoroughly before negotiation.
- Flexibility: Be willing to compromise on certain terms to reach a mutually beneficial agreement.
- Value-Based Negotiation: Focus on the overall value rather than just price.
- Long-Term Focus: Aim for agreements that support long-term business goals.
Market Conditions Affecting Procurement from Japan
Understanding the current market conditions is essential for successful procurement:
- Supply Chain Dynamics: Global supply chain disruptions can impact lead times and availability.
- Economic Factors: Exchange rates and economic stability influence pricing and purchasing power.
- Technological Advancements: Rapid technological changes require staying updated with the latest innovations.
Impact of Global Trends
Global trends such as automation and Industry 4.0 are reshaping manufacturing:
- Increased Demand for Automation: Growing need for automated safety solutions.
- Sustainability: Emphasis on eco-friendly manufacturing processes.
- Digital Transformation: Integration of digital technologies to enhance operational efficiency.
Best Practices for Implementing the Automatic Stop Function
To maximize the benefits of the automatic stop function, manufacturers should follow these best practices:
- Comprehensive Planning: Develop a detailed implementation plan that addresses all aspects of the integration process.
- Stakeholder Engagement: Involve all relevant stakeholders in the planning and execution phases.
- Continuous Training: Provide ongoing training to ensure staff are proficient with the new system.
- Regular Maintenance: Implement routine maintenance schedules to ensure system reliability and performance.
Monitoring and Evaluation
Continuous monitoring and evaluation are essential for sustained success:
- Performance Metrics: Establish metrics to assess the effectiveness of the automatic stop function.
- Feedback Loops: Create mechanisms for employees to provide feedback on system performance.
- Adaptation: Be prepared to make adjustments based on performance data and feedback.
Case Studies: Success Stories from Japanese Manufacturers
Examining real-world applications provides valuable insights:
- Automotive Industry: Japanese car manufacturers have successfully integrated automatic stop functions to enhance assembly line safety.
- Electronics Manufacturing: Electronics companies use automated safety systems to protect intricate components and ensure operational continuity.
- Heavy Machinery: Manufacturers of heavy machinery have reduced workplace accidents by implementing advanced automatic stop technologies.
Key Takeaways from Successful Implementations
Key lessons from successful case studies include:
- Customization: Tailoring the automatic stop function to specific operational needs.
- Employee Involvement: Engaging employees in the implementation process to ensure acceptance and proper usage.
- Continuous Improvement: Regularly updating and improving the system based on operational feedback and technological advancements.
The Future of Automatic Stop Functions in Manufacturing
The future of automatic stop functions looks promising, with ongoing advancements poised to further enhance safety and efficiency:
- Artificial Intelligence: Integrating AI to predict and prevent potential hazards proactively.
- Internet of Things (IoT): Connecting safety systems to broader IoT networks for real-time data analysis and decision-making.
- Advanced Robotics: Collaborating with robotic systems to create more responsive and adaptive safety measures.
Emerging Trends and Innovations
Emerging trends are shaping the evolution of safety technologies:
- Predictive Maintenance: Using data analytics to foresee equipment failures and prevent accidents.
- Collaborative Robots (Cobots): Enhancing human-robot collaboration while maintaining stringent safety standards.
- Augmented Reality (AR): Utilizing AR for training and real-time safety monitoring.
Conclusion: Embracing Safety Innovations for a Sustainable Future
Japan’s automatic stop function is a testament to the country’s commitment to manufacturing excellence and workplace safety. By adopting this technology, manufacturing companies can significantly reduce the risk of accidents, enhance operational efficiency, and achieve long-term sustainability.
Investing in advanced safety measures not only protects employees but also fosters a culture of continuous improvement and innovation. As the manufacturing landscape evolves, embracing such technologies will be crucial for staying competitive and ensuring a safe, productive work environment.
Actionable Steps for Manufacturers
Manufacturers looking to implement Japan’s automatic stop function should consider the following steps:
- Assess Current Safety Protocols: Evaluate existing safety measures to identify areas for improvement.
- Research Technology Providers: Identify reputable suppliers in Japan who specialize in automatic stop functions.
- Develop an Implementation Plan: Create a comprehensive plan that outlines the integration process, timelines, and resource allocation.
- Invest in Training: Ensure that all relevant personnel are trained to operate and maintain the new safety systems effectively.
- Monitor and Review: Continuously monitor system performance and make necessary adjustments to optimize safety and efficiency.
Leveraging Japanese Expertise in Procurement
Engaging with Japanese suppliers offers additional benefits beyond the technology itself. Japanese manufacturers are renowned for their commitment to quality, precision, and continuous improvement.
By leveraging Japanese expertise, companies can enhance their procurement strategies and foster long-term, mutually beneficial partnerships. This collaboration can lead to further innovations and efficiencies within the manufacturing process.
Building Long-Term Partnerships
Establishing strong, long-term relationships with Japanese suppliers involves:
- Mutual Respect: Understanding and respecting cultural differences and business practices.
- Clear Communication: Maintaining open and transparent communication channels to address any issues promptly.
- Collaborative Innovation: Working together to develop new solutions and improve existing processes.
Quality Assurance and Continuous Improvement
Japanese suppliers emphasize quality assurance and continuous improvement:
- High Standards: Adhering to rigorous quality standards to ensure reliable and durable products.
- Kaizen Philosophy: Embracing the Kaizen philosophy of continuous, incremental improvements.
- Feedback Integration: Utilizing feedback to enhance product offerings and address emerging needs.
Maximizing Benefits from Japanese Procurement Practices
To fully capitalize on the benefits of Japanese procurement practices, consider the following strategies:
- Integrate Lean Manufacturing: Adopt lean manufacturing principles to minimize waste and optimize processes.
- Embrace Standardization: Standardize components and processes to improve consistency and reduce costs.
- Invest in Technology: Utilize advanced technologies to enhance procurement efficiency and accuracy.
Case Example: Successful Integration of Automatic Stop Function
A leading Japanese automotive manufacturer successfully integrated the automatic stop function into their production line. The implementation resulted in:
- Reduced Accidents: A significant decrease in workplace incidents related to machinery operation.
- Improved Efficiency: Streamlined production processes with minimal downtime due to preventative shutdowns.
- Cost Savings: Lowered costs associated with accident-related expenses and equipment repairs.
Final Thoughts
Japan’s automatic stop function represents a pivotal advancement in manufacturing safety and efficiency. By adopting this technology, manufacturers can not only protect their workforce but also enhance operational performance and achieve sustainable growth.
Embracing innovative safety solutions and leveraging Japanese procurement practices can position companies for long-term success in an increasingly competitive global market. Investing in safety is an investment in the company’s future, ensuring that both employees and operations thrive in a secure and efficient environment.
資料ダウンロード
QCD調達購買管理クラウド「newji」は、調達購買部門で必要なQCD管理全てを備えた、現場特化型兼クラウド型の今世紀最高の購買管理システムとなります。
ユーザー登録
調達購買業務の効率化だけでなく、システムを導入することで、コスト削減や製品・資材のステータス可視化のほか、属人化していた購買情報の共有化による内部不正防止や統制にも役立ちます。
NEWJI DX
製造業に特化したデジタルトランスフォーメーション(DX)の実現を目指す請負開発型のコンサルティングサービスです。AI、iPaaS、および先端の技術を駆使して、製造プロセスの効率化、業務効率化、チームワーク強化、コスト削減、品質向上を実現します。このサービスは、製造業の課題を深く理解し、それに対する最適なデジタルソリューションを提供することで、企業が持続的な成長とイノベーションを達成できるようサポートします。
オンライン講座
製造業、主に購買・調達部門にお勤めの方々に向けた情報を配信しております。
新任の方やベテランの方、管理職を対象とした幅広いコンテンツをご用意しております。
お問い合わせ
コストダウンが利益に直結する術だと理解していても、なかなか前に進めることができない状況。そんな時は、newjiのコストダウン自動化機能で大きく利益貢献しよう!
(Β版非公開)