- お役立ち記事
- Revolutionizing Strength and Safety: The Japanese Approach to Dyneema Manufacturing
月間76,176名の
製造業ご担当者様が閲覧しています*
*2025年3月31日現在のGoogle Analyticsのデータより
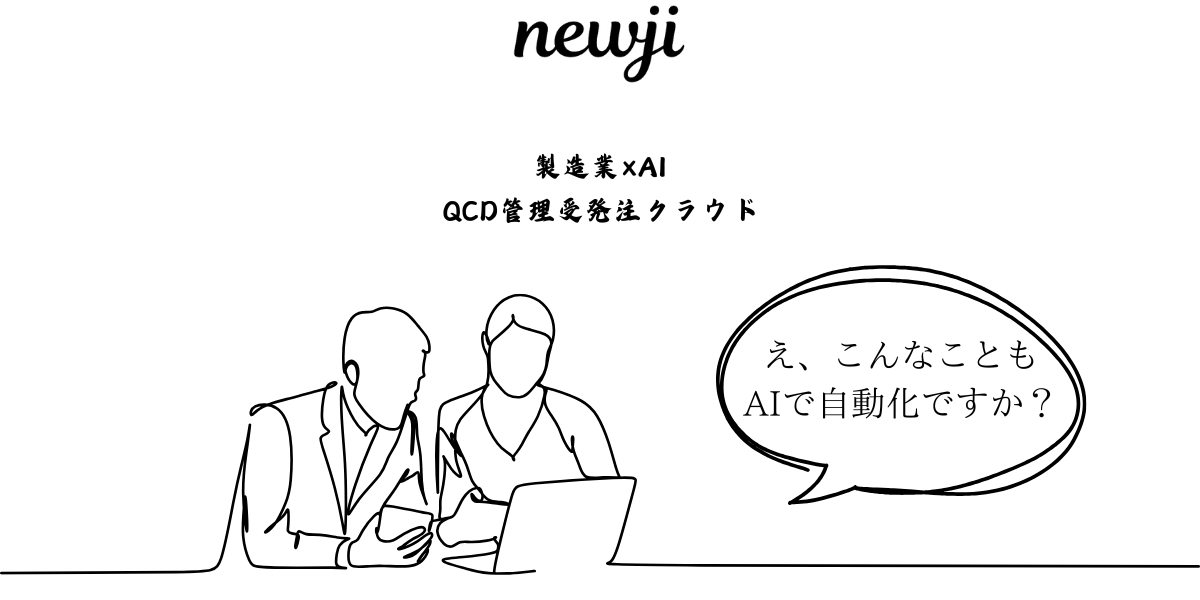
Revolutionizing Strength and Safety: The Japanese Approach to Dyneema Manufacturing
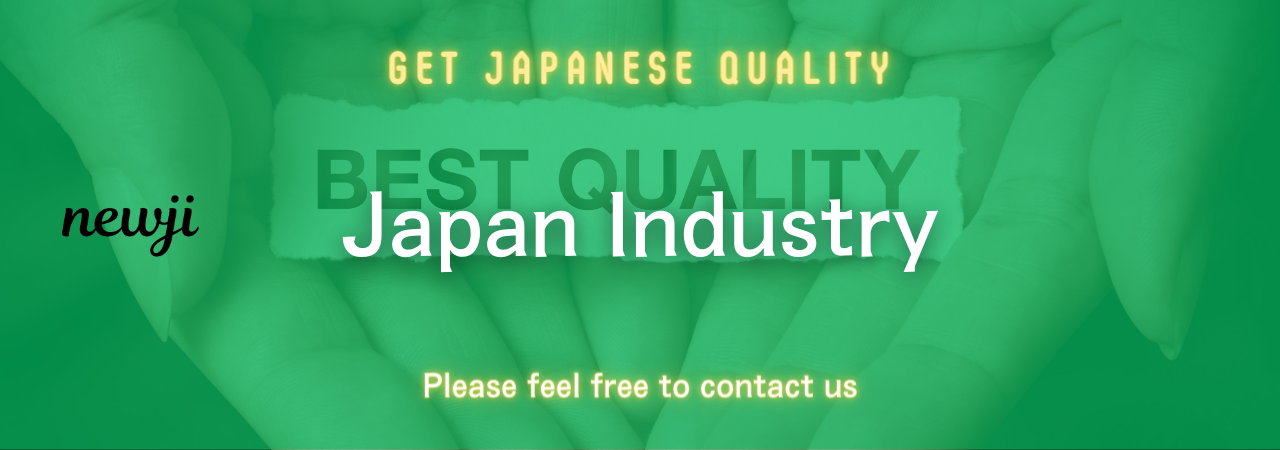
目次
Introduction to Dyneema and Its Importance
Dyneema is a high-performance polyethylene fiber renowned for its exceptional strength-to-weight ratio. Often referred to as the world’s strongest fiber, Dyneema is used in a variety of applications where strength and safety are paramount. From maritime ropes and protective clothing to aerospace components and sporting goods, Dyneema offers unparalleled durability and reliability. Its ability to withstand extreme conditions without compromising performance makes it a preferred choice in industries that demand the highest standards of safety and efficiency.
The evolution of Dyneema manufacturing has seen significant contributions from Japanese manufacturers. Japan’s meticulous approach to production, combined with advanced technology and quality control, has revolutionized the way Dyneema is produced and utilized globally. This article explores the Japanese approach to Dyneema manufacturing, highlighting its impact on strength and safety, and provides insights into the procurement and purchasing processes involved in sourcing Dyneema from Japanese suppliers.
Overview of Japanese Dyneema Manufacturing
Japan has long been a leader in the field of high-performance materials, and Dyneema is no exception. The Japanese approach to Dyneema manufacturing is characterized by precision, innovation, and a relentless pursuit of quality. Several key factors contribute to the superiority of Japanese Dyneema products:
Advanced Production Techniques
Japanese manufacturers employ cutting-edge production techniques that enhance the quality and consistency of Dyneema fibers. These techniques include:
– **Gel Spinning Technology:** This process involves dissolving polyethylene pellets in a solvent to create a gel-like substance, which is then extruded through spinnerets to form fine fibers. The precision of gel spinning ensures uniform fiber diameter and exceptional tensile strength.
– **Continuous Polymerization:** Japanese facilities utilize continuous polymerization methods that allow for consistent polymer chains, resulting in fibers with superior strength and durability.
– **Automated Quality Control:** Automation plays a crucial role in maintaining the high standards of Dyneema production. Automated systems monitor every stage of the manufacturing process, detecting and correcting any anomalies in real-time.
Research and Development
Japan’s commitment to R&D in Dyneema manufacturing leads to continuous improvements in fiber performance. Collaborative efforts between manufacturers, research institutions, and industry experts drive innovations that enhance the fiber’s properties, such as:
– **Increased Tensile Strength:** Ongoing R&D efforts focus on increasing the tensile strength of Dyneema fibers, making them even more resilient under stress.
– **Enhanced UV Resistance:** Developing Dyneema variants with improved resistance to ultraviolet light extends the lifespan of products exposed to harsh environmental conditions.
– **Thermal Stability:** Research into thermal stability ensures that Dyneema maintains its integrity and performance across a wide range of temperatures.
Stringent Quality Control
Quality is non-negotiable in Japanese manufacturing. Rigorous quality control measures ensure that every batch of Dyneema meets the highest standards. These measures include:
– **Material Testing:** Comprehensive testing of raw materials ensures that only the best quality polyethylene is used in production.
– **Process Monitoring:** Continuous monitoring of the manufacturing process allows for immediate identification and correction of potential defects.
– **Final Product Inspection:** Each Dyneema batch undergoes thorough inspection to verify properties such as tensile strength, elasticity, and durability before it reaches the market.
Advantages of Sourcing Dyneema from Japanese Manufacturers
Procurement and purchasing from Japanese Dyneema manufacturers offer numerous advantages that can significantly benefit your organization:
Superior Quality and Reliability
Japanese manufacturers are renowned for their commitment to quality. By sourcing Dyneema from Japan, you can be confident in the consistency and reliability of the product. This ensures that the end products, whether ropes, protective gear, or other high-performance items, perform reliably under demanding conditions.
Technological Innovation
Japan’s focus on innovation translates into Dyneema products that incorporate the latest advancements in fiber technology. This means access to Dyneema variants with enhanced properties, such as increased strength, improved UV resistance, and better thermal stability, giving your products a competitive edge in the market.
Comprehensive Support and Expertise
Japanese suppliers often provide extensive technical support and expertise. This can be invaluable in optimizing the use of Dyneema in your applications, ensuring that you maximize the benefits of the fiber’s unique properties. Additionally, suppliers can offer tailored solutions to meet specific project requirements.
Strong Supply Chain Management
Japanese manufacturers are known for their efficient and reliable supply chain management. This ensures timely delivery of Dyneema products, minimizing downtime and maintaining production schedules. The robustness of Japan’s logistics infrastructure further enhances the reliability of supply.
Reputation and Brand Trust
Japanese brands carry a strong reputation for excellence and trustworthiness. Partnering with reputable Japanese Dyneema manufacturers can enhance your company’s credibility and reassure your clients of the quality and safety of your products.
Disadvantages and Challenges of Sourcing from Japan
While there are significant advantages to sourcing Dyneema from Japanese manufacturers, there are also challenges that organizations need to consider:
Higher Cost
Japanese Dyneema products often come at a premium price compared to alternatives from other regions. This higher cost is justified by the superior quality and technological advancements, but it may impact budget considerations, especially for cost-sensitive projects.
Longer Lead Times
Shipping products from Japan can result in longer lead times due to the distance and complexity of international logistics. This can affect project timelines and requires careful planning to ensure that Dyneema arrives when needed.
Cultural and Language Barriers
Conducting business with Japanese suppliers may involve navigating cultural and language barriers. Understanding and respecting Japanese business etiquette is essential for building strong relationships and effective communication.
Minimum Order Quantities
Japanese manufacturers may have higher minimum order quantities compared to suppliers in other regions. This can be a challenge for smaller organizations or those with limited procurement budgets.
Regulatory Compliance
Ensuring that Dyneema products comply with the regulatory standards of your region may require additional steps and documentation, adding complexity to the procurement process.
Supplier Negotiation Techniques with Japanese Manufacturers
Successfully negotiating with Japanese Dyneema suppliers requires an understanding of Japanese business culture and effective negotiation strategies. Here are some techniques to consider:
Building Long-term Relationships
Japanese business culture places a strong emphasis on long-term relationships. Investing time in building trust and rapport can lead to more favorable terms and a more collaborative partnership. Regular communication and showing appreciation for the supplier’s efforts can strengthen the relationship.
Understanding Cultural Nuances
Respect for hierarchy, punctuality, and formality are key aspects of Japanese business culture. Demonstrating cultural sensitivity and adapting to these norms can facilitate smoother negotiations. Learning basic Japanese phrases and business etiquette can also make a positive impression.
Emphasizing Mutual Benefits
Highlighting how the partnership can benefit both parties fosters a collaborative negotiation environment. Presenting win-win scenarios where both your organization and the supplier gain value can lead to more successful agreements.
Being Patient and Persistent
Negotiations in Japan may take longer compared to other regions due to the thorough decision-making process. Patience and persistence are essential, as rushing can be perceived as disrespectful and may hinder the negotiation process.
Transparent and Clear Communication
Clear and transparent communication helps prevent misunderstandings. Providing detailed specifications, expectations, and terms ensures that both parties are aligned. Utilizing professional translators or bilingual staff can enhance communication effectiveness.
Flexible Negotiation Tactics
Flexibility in negotiations shows a willingness to accommodate the supplier’s needs and constraints. Being open to alternative solutions or compromises can lead to more favorable outcomes and strengthen the partnership.
Market Conditions and Trends in Dyneema Manufacturing
Understanding the current market conditions and trends in Dyneema manufacturing is crucial for effective procurement and purchasing. Key factors influencing the market include:
Growing Demand Across Industries
The demand for Dyneema is increasing across various industries, including maritime, construction, automotive, aerospace, and personal protective equipment. This growth is driven by the fiber’s superior strength, lightweight properties, and versatility.
Technological Advancements
Continuous advancements in Dyneema manufacturing technology are enhancing the fiber’s performance and expanding its applications. Innovations such as improved fiber cross-linking and enhanced polymerization techniques are driving the development of new Dyneema variants.
Sustainability and Environmental Concerns
Sustainability is becoming a significant consideration in Dyneema production and procurement. Japanese manufacturers are investing in eco-friendly production processes and developing Dyneema products with lower environmental impact, responding to the global demand for sustainable materials.
Competitive Landscape
The Dyneema market is becoming increasingly competitive, with new players entering the market and established manufacturers enhancing their offerings. Japanese manufacturers maintain a competitive edge through their focus on quality, innovation, and reliability.
Supply Chain Dynamics
Global supply chain disruptions, such as those caused by the COVID-19 pandemic, have highlighted the importance of resilient supply chains. Japanese manufacturers are enhancing their supply chain strategies to mitigate risks and ensure consistent supply despite global challenges.
Price Fluctuations
Fluctuations in raw material prices, particularly polyethylene, can impact the cost of Dyneema. Japanese manufacturers employ strategies such as long-term contracts and strategic sourcing to manage price volatility and maintain stable pricing for customers.
Best Practices for Procuring Dyneema from Japanese Suppliers
Implementing best practices in procurement and purchasing can optimize the process of sourcing Dyneema from Japanese manufacturers. These practices ensure efficiency, quality, and cost-effectiveness.
Thorough Supplier Evaluation
Before entering into a partnership, conduct a comprehensive evaluation of potential suppliers. Assess their manufacturing capabilities, quality control measures, financial stability, and reputation in the market. Request samples and conduct site visits if possible to verify their operations firsthand.
Clear Specifications and Requirements
Provide detailed specifications and requirements to the supplier to ensure that the Dyneema meets your project’s needs. This includes technical properties, quality standards, packaging, and delivery timelines. Clear communication helps prevent misunderstandings and ensures that the supplier can fulfill your needs accurately.
Establishing Quality Assurance Protocols
Implement robust quality assurance protocols to monitor the quality of Dyneema products. This includes setting up regular quality inspections, testing samples, and requiring certifications that demonstrate compliance with relevant standards. Partnering with the supplier to establish quality benchmarks ensures consistent product performance.
Effective Communication Channels
Maintain open and effective communication channels with your Japanese suppliers. Regular meetings, progress updates, and clear lines of communication help address any issues promptly and foster a collaborative working relationship. Utilizing communication tools that bridge language barriers can enhance understanding and efficiency.
Negotiating Favorable Payment Terms
Negotiate payment terms that align with your organization’s cash flow and financial strategies. Options such as letters of credit, milestone-based payments, or extended payment terms can provide financial flexibility while maintaining a strong partnership with the supplier.
Leveraging Technology for Supply Chain Management
Utilize technology to streamline supply chain management and enhance visibility. Implementing supply chain management software, real-time tracking systems, and data analytics can improve inventory management, predict demand, and optimize logistics operations.
Building a Collaborative Partnership
Foster a collaborative partnership with your Japanese suppliers by involving them in the development process and seeking their input on product improvements. This collaborative approach can lead to innovative solutions, improved product quality, and a more resilient supply chain.
Managing Logistics and Import Regulations
Understand and comply with import regulations and logistics requirements when sourcing Dyneema from Japan. This includes obtaining necessary permits, adhering to customs procedures, and selecting reliable logistics partners to ensure smooth transportation and delivery.
Risk Management and Contingency Planning
Identify potential risks in the procurement process and develop contingency plans to mitigate them. This includes diversifying suppliers, maintaining safety stock, and establishing alternative sourcing strategies to handle supply chain disruptions or unexpected demand changes.
Case Study: Successful Procurement of Dyneema from Japan
To illustrate the practical application of these best practices, consider the example of a global outdoor gear manufacturer looking to source Dyneema for their high-strength backpacks.
Supplier Selection
The manufacturer conducted a thorough evaluation of several Japanese Dyneema suppliers, assessing their production capabilities, quality control measures, and industry reputation. After requesting samples and conducting virtual site visits, they selected a supplier known for its advanced gel spinning technology and stringent quality assurance protocols.
Negotiation and Agreement
During negotiations, the manufacturer emphasized the need for consistent quality and timely delivery. By building a relationship based on mutual trust and understanding, they negotiated favorable payment terms and established a long-term supply agreement that included clauses for quality guarantees and flexible order volumes.
Implementation of Quality Assurance
The manufacturer collaborated with the supplier to establish quality benchmarks tailored to their specific requirements. Regular quality inspections and testing were implemented, ensuring that each batch of Dyneema met the necessary strength and durability standards.
Optimizing Supply Chain
Leveraging supply chain management software, the manufacturer tracked shipments in real-time, optimizing inventory levels and reducing lead times. Strategic partnerships with logistics providers ensured reliable transportation and minimal delays in delivery.
Results and Benefits
By sourcing Dyneema from the selected Japanese supplier, the manufacturer achieved enhanced product performance, leading to higher customer satisfaction and increased market share. The strong partnership with the supplier facilitated continuous improvement and innovation, contributing to the company’s long-term success.
Conclusion
The Japanese approach to Dyneema manufacturing exemplifies excellence in strength and safety, driven by advanced technology, rigorous quality control, and a commitment to innovation. For organizations seeking high-performance Dyneema, sourcing from Japanese manufacturers offers significant advantages, including superior quality, reliability, and comprehensive support.
However, navigating the challenges of higher costs, longer lead times, and cultural differences requires strategic planning and effective negotiation techniques. By implementing best practices in procurement and purchasing, such as thorough supplier evaluation, clear communication, and robust quality assurance protocols, companies can optimize their sourcing processes and fully leverage the benefits of Japanese Dyneema products.
As the global demand for high-strength and safe materials continues to grow, the Japanese approach to Dyneema manufacturing will remain a pivotal factor in advancing technological capabilities and ensuring the success of industries worldwide. Embracing the strengths of Japanese suppliers and fostering collaborative partnerships will enable organizations to achieve excellence in their products and maintain a competitive edge in the market.
資料ダウンロード
QCD管理受発注クラウド「newji」は、受発注部門で必要なQCD管理全てを備えた、現場特化型兼クラウド型の今世紀最高の受発注管理システムとなります。
ユーザー登録
受発注業務の効率化だけでなく、システムを導入することで、コスト削減や製品・資材のステータス可視化のほか、属人化していた受発注情報の共有化による内部不正防止や統制にも役立ちます。
NEWJI DX
製造業に特化したデジタルトランスフォーメーション(DX)の実現を目指す請負開発型のコンサルティングサービスです。AI、iPaaS、および先端の技術を駆使して、製造プロセスの効率化、業務効率化、チームワーク強化、コスト削減、品質向上を実現します。このサービスは、製造業の課題を深く理解し、それに対する最適なデジタルソリューションを提供することで、企業が持続的な成長とイノベーションを達成できるようサポートします。
製造業ニュース解説
製造業、主に購買・調達部門にお勤めの方々に向けた情報を配信しております。
新任の方やベテランの方、管理職を対象とした幅広いコンテンツをご用意しております。
お問い合わせ
コストダウンが利益に直結する術だと理解していても、なかなか前に進めることができない状況。そんな時は、newjiのコストダウン自動化機能で大きく利益貢献しよう!
(β版非公開)