- お役立ち記事
- Revving Up Efficiency: How Japanese Manufacturing Leads the Way in Automation Innovation
月間77,185名の
製造業ご担当者様が閲覧しています*
*2025年2月28日現在のGoogle Analyticsのデータより
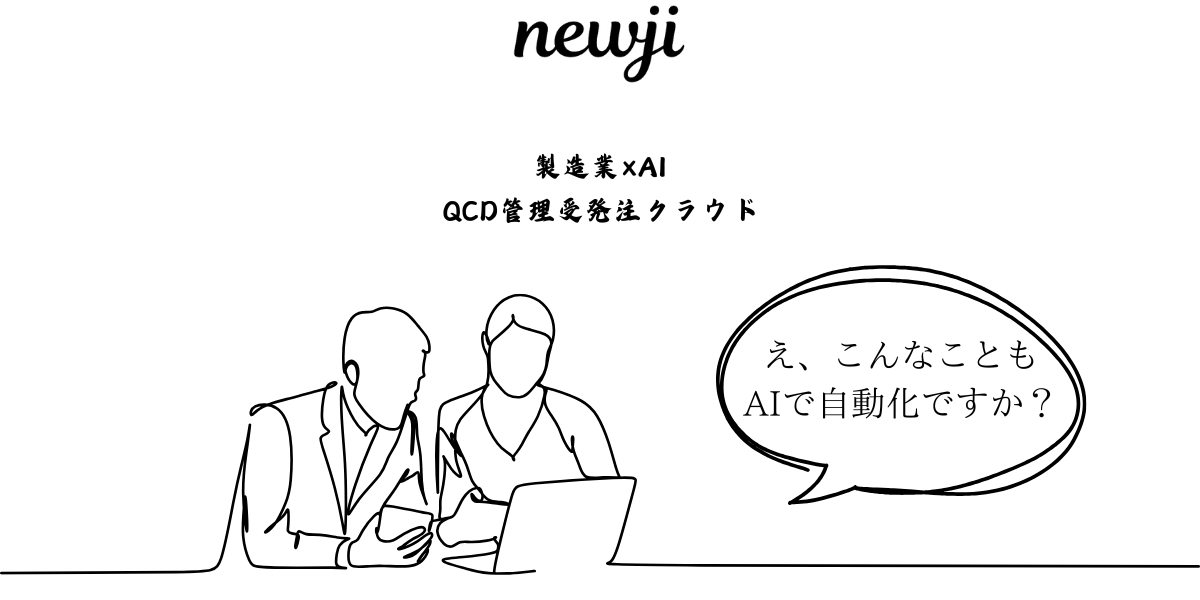
Revving Up Efficiency: How Japanese Manufacturing Leads the Way in Automation Innovation
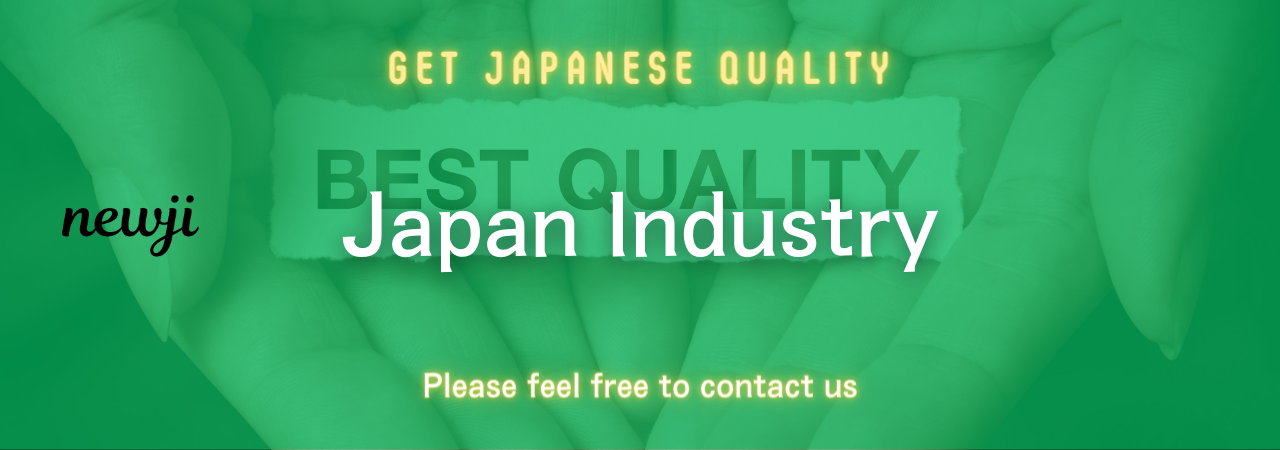
目次
Introduction to Japanese Automation Innovation
Japanese manufacturing has long been synonymous with precision, reliability, and innovation. In the realm of automation, Japan continues to lead the way, setting benchmarks that are emulated worldwide. This leadership is not by chance but the result of decades of dedicated research, strategic procurement, and a relentless pursuit of excellence. Understanding how Japanese manufacturers excel in automation can provide valuable insights for global companies seeking to enhance their own production capabilities.
The Pillars of Japanese Automation Excellence
1. Advanced Technology Integration
Japanese manufacturers prioritize the integration of cutting-edge technologies into their production lines. Robotics, artificial intelligence, and Internet of Things (IoT) devices are seamlessly incorporated to enhance efficiency and reduce human error. This technological adoption ensures that Japanese factories remain at the forefront of innovation.
2. Precision Engineering
Precision is a hallmark of Japanese manufacturing. Automation systems are designed with meticulous attention to detail, ensuring that each component performs optimally. This precision reduces waste, improves quality control, and increases the overall reliability of the production process.
3. Continuous Improvement (Kaizen)
The Kaizen philosophy of continuous improvement is deeply ingrained in Japanese manufacturing culture. By constantly seeking ways to refine and enhance automation processes, Japanese companies ensure that their systems remain efficient and adaptable to changing market demands.
4. Skilled Workforce
Even with high levels of automation, the role of skilled workers remains critical. Japanese manufacturers invest heavily in training their workforce, ensuring that employees can effectively manage, maintain, and optimize automated systems. This synergy between human expertise and machine efficiency drives superior outcomes.
Advantages of Japanese Automation in Manufacturing
1. Enhanced Efficiency and Productivity
Automation significantly reduces production time and increases output. Japanese factories can operate around the clock with minimal downtime, leading to higher productivity levels compared to manual or less automated setups.
2. Improved Quality Control
Automated systems ensure consistency and precision in manufacturing processes. This leads to fewer defects, higher product quality, and greater customer satisfaction. Advanced quality control measures can be implemented seamlessly within automated lines.
3. Cost Reduction
While the initial investment in automation technology can be substantial, the long-term savings are considerable. Reduced labor costs, minimized waste, and decreased downtime contribute to lower overall production costs.
4. Flexibility and Scalability
Japanese automation systems are designed for flexibility, allowing manufacturers to adapt quickly to changing market demands and production needs. Scalability ensures that as businesses grow, their automation systems can be expanded and upgraded accordingly.
5. Enhanced Safety
Automated systems handle hazardous tasks, reducing the risk of workplace injuries. This not only protects employees but also minimizes costs related to accidents and safety compliance.
Challenges and Disadvantages
1. High Initial Investment
The cost of implementing advanced automation technology can be prohibitive, especially for smaller manufacturers. This includes expenses related to equipment, installation, and training.
2. Technical Complexity
Advanced automation systems require specialized knowledge to operate and maintain. This can lead to challenges in hiring and retaining skilled personnel, as well as increased reliance on external support.
3. Potential for Job Displacement
Automation can lead to reduced demand for certain manual labor roles, raising concerns about job displacement. Balancing automation with workforce development is crucial to mitigating this impact.
4. Dependence on Technology
High reliance on automated systems makes manufacturers vulnerable to technical failures, cybersecurity threats, and supply chain disruptions related to technology components.
Supplier Negotiation Techniques in Japanese Manufacturing
1. Building Long-Term Relationships
Japanese companies emphasize building enduring relationships with suppliers. Trust and mutual respect are foundational, leading to more favorable negotiation outcomes and collaborative problem-solving.
2. Emphasizing Quality and Reliability
Negotiations often focus on ensuring that suppliers meet stringent quality and reliability standards. This includes detailed specifications, rigorous testing protocols, and continuous quality improvement initiatives.
3. Leveraging Volume and Consistency
Japanese manufacturers typically place large, consistent orders with suppliers. This predictability allows for better pricing negotiations, prioritized production schedules, and more stable supply chains.
4. Incorporating Kaizen in Supplier Agreements
Including continuous improvement clauses in supplier agreements encourages ongoing enhancements in quality and efficiency. This collaborative approach benefits both parties and fosters innovation.
5. Strategic Partnerships
Rather than viewing suppliers purely as vendors, Japanese manufacturers often establish strategic partnerships. This collaborative dynamic facilitates shared goals, joint development projects, and integrated supply chain solutions.
Market Conditions Influencing Automation
1. Global Competition
The competitive global marketplace drives Japanese manufacturers to continuously innovate and enhance their automation capabilities. Staying ahead in technology adoption ensures a competitive edge in terms of cost, quality, and delivery.
2. Labor Shortages
A decline in available labor forces in Japan necessitates higher levels of automation. Robotics and AI systems compensate for workforce shortages, maintaining productivity levels despite demographic challenges.
3. Technological Advancements
Rapid advancements in technology provide new opportunities for automation. Japanese manufacturers are quick to adopt and integrate these innovations, maintaining their leadership in the field.
4. Sustainability and Environmental Regulations
Increasing emphasis on sustainability compels manufacturers to adopt energy-efficient automation technologies. Automated processes can optimize resource usage, reduce waste, and ensure compliance with environmental regulations.
5. Customer Demand for Customization
Modern consumers expect personalized products. Advanced automation allows Japanese manufacturers to offer customizable solutions without sacrificing efficiency or increasing costs significantly.
Best Practices in Japanese Automated Manufacturing
1. Comprehensive Planning and Strategy
Successful automation begins with meticulous planning. Japanese manufacturers develop detailed strategies outlining technology adoption timelines, budget allocations, and workforce training programs.
2. Integration of IoT and Smart Technologies
Utilizing IoT and smart technologies enables real-time monitoring and data analysis. This integration allows for predictive maintenance, efficient resource management, and informed decision-making.
3. Emphasis on Training and Development
Investing in employee training ensures that the workforce can effectively manage and optimize automated systems. Continuous education keeps staff updated on the latest technologies and best practices.
4. Lean Manufacturing Principles
Implementing lean manufacturing principles alongside automation reduces waste, enhances process efficiency, and maximizes value creation. This synergy leads to streamlined operations and cost savings.
5. Robust Quality Assurance Systems
Automated quality assurance systems monitor every stage of production. This ensures that products meet stringent quality standards, reducing defects and enhancing customer satisfaction.
6. Flexible Production Systems
Designing flexible automation systems allows manufacturers to quickly adapt to changing production needs. Modular components and scalable technologies facilitate easy adjustments and expansions.
Case Studies of Japanese Automation Leadership
1. Toyota’s Just-In-Time Production
Toyota revolutionized manufacturing with its Just-In-Time (JIT) production system, which heavily relies on automation. By synchronizing production schedules with demand, Toyota minimizes inventory costs and enhances efficiency.
2. Fanuc’s Robotics Innovations
Fanuc, a leading Japanese robotics company, has pioneered advancements in industrial robots. Their robots are known for precision, reliability, and versatility, making them integral to various manufacturing sectors globally.
3. Mitsubishi Electric’s Smart Factory Solutions
Mitsubishi Electric has developed comprehensive smart factory solutions that integrate automation, IoT, and data analytics. These solutions enhance operational visibility, optimize processes, and drive continuous improvement.
Strategies for Implementing Japanese Automation Practices
1. Assessing Current Capabilities
Before adopting automation, evaluate existing processes, technologies, and workforce skills. Identify areas where automation can deliver the most significant benefits and align with strategic goals.
2. Investing in the Right Technology
Choose automation technologies that complement your production needs. Consider factors such as scalability, compatibility with existing systems, and the ability to integrate with future innovations.
3. Engaging Stakeholders
Involve all relevant stakeholders, including employees, suppliers, and management, in the automation process. Their input and support are crucial for successful implementation and adoption.
4. Fostering a Culture of Continuous Improvement
Encourage a mindset of continuous improvement within the organization. Regularly review and refine automation processes to enhance efficiency and adapt to changing market conditions.
5. Ensuring Robust Training Programs
Develop comprehensive training programs to equip employees with the necessary skills to manage and operate automated systems. Ongoing education and support are essential for maximizing the benefits of automation.
Future Trends in Japanese Manufacturing Automation
1. Increased Use of Artificial Intelligence
AI will play a more significant role in automation, enabling smarter decision-making, predictive maintenance, and enhanced process optimization. Japanese manufacturers are investing in AI to further refine their automated systems.
2. Expansion of Collaborative Robots (Cobots)
Cobots, designed to work alongside human workers, are becoming more prevalent. These robots enhance productivity while maintaining human oversight and flexibility in production processes.
3. Enhanced Data Analytics
Advanced data analytics will provide deeper insights into production processes. This will enable more precise forecasting, improved quality control, and better resource management.
4. Sustainable Automation Solutions
There is a growing emphasis on developing environmentally sustainable automation technologies. Energy-efficient systems and eco-friendly materials will become standard in Japanese manufacturing automation.
5. Greater Integration of Augmented Reality (AR)
AR technology will be integrated into manufacturing processes to aid in training, maintenance, and real-time monitoring. This enhances the ability of workers to interact with and manage automated systems effectively.
Conclusion
Japanese manufacturing’s leadership in automation innovation is a testament to its commitment to quality, efficiency, and continuous improvement. By integrating advanced technologies, fostering skilled workforces, and building strong supplier relationships, Japan sets a high standard in the global manufacturing landscape. While challenges such as high initial investments and technical complexities exist, the advantages of enhanced productivity, quality control, and cost reduction make automation a worthwhile endeavor. As global market conditions evolve, Japanese manufacturers continue to adapt and innovate, ensuring their position at the forefront of automation technology. Companies worldwide can learn valuable lessons from Japanese practices, adopting best-in-class strategies to rev up their own manufacturing efficiency and competitiveness.
資料ダウンロード
QCD管理受発注クラウド「newji」は、受発注部門で必要なQCD管理全てを備えた、現場特化型兼クラウド型の今世紀最高の受発注管理システムとなります。
ユーザー登録
受発注業務の効率化だけでなく、システムを導入することで、コスト削減や製品・資材のステータス可視化のほか、属人化していた受発注情報の共有化による内部不正防止や統制にも役立ちます。
NEWJI DX
製造業に特化したデジタルトランスフォーメーション(DX)の実現を目指す請負開発型のコンサルティングサービスです。AI、iPaaS、および先端の技術を駆使して、製造プロセスの効率化、業務効率化、チームワーク強化、コスト削減、品質向上を実現します。このサービスは、製造業の課題を深く理解し、それに対する最適なデジタルソリューションを提供することで、企業が持続的な成長とイノベーションを達成できるようサポートします。
製造業ニュース解説
製造業、主に購買・調達部門にお勤めの方々に向けた情報を配信しております。
新任の方やベテランの方、管理職を対象とした幅広いコンテンツをご用意しております。
お問い合わせ
コストダウンが利益に直結する術だと理解していても、なかなか前に進めることができない状況。そんな時は、newjiのコストダウン自動化機能で大きく利益貢献しよう!
(β版非公開)