- お役立ち記事
- Risk assessment method for purchasing departments to ensure supply chain safety
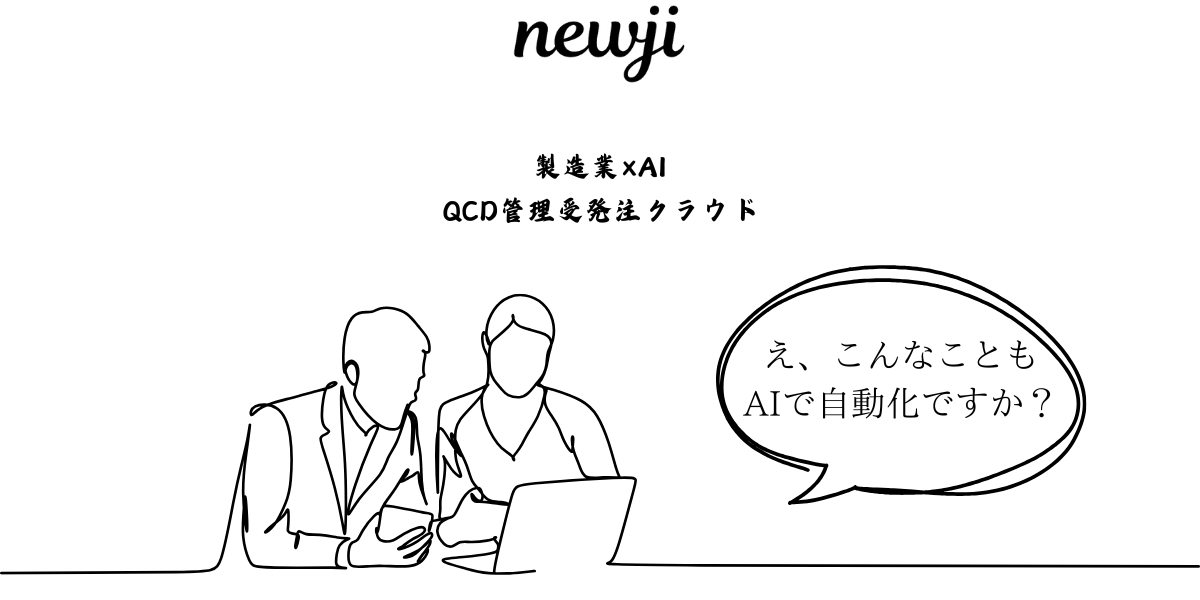
Risk assessment method for purchasing departments to ensure supply chain safety
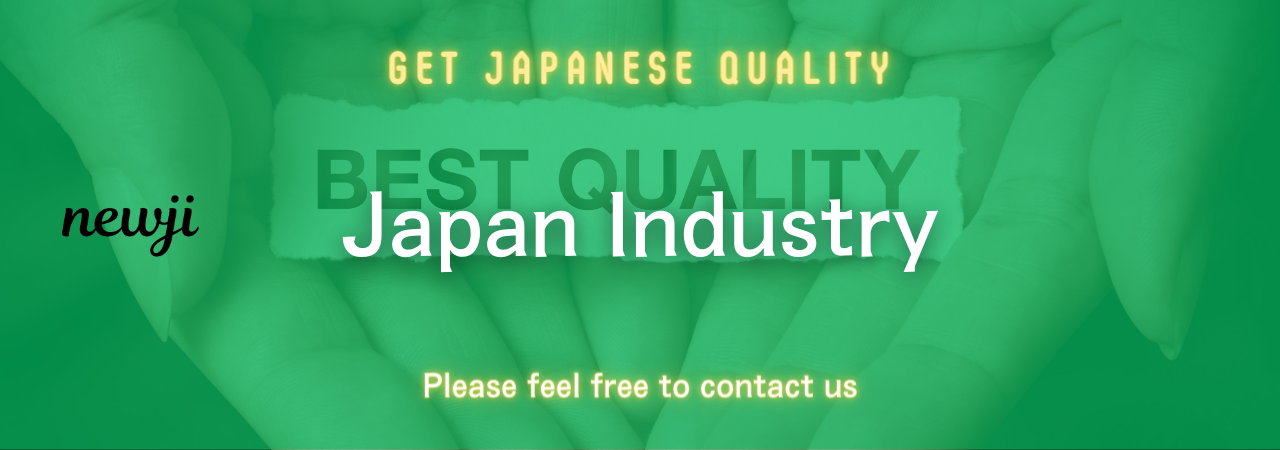
Understanding Risk Assessment in the Supply Chain
Risk assessment is an essential process in ensuring the safety and efficiency of supply chains, especially for purchasing departments.
As global markets become increasingly interconnected, supply chains grow more complex and susceptible to a variety of risks.
These can include natural disasters, political instability, financial fluctuations, and even cyber threats.
For purchasing departments, effectively assessing and mitigating risks leads to improved decision-making and ultimately safeguards the company’s bottom line.
The Importance of Risk Assessment in Purchasing
In any organization, the purchasing department plays a critical role as the frontline of the supply chain.
This department is responsible for acquiring goods and services necessary for the company’s operations.
Without proper risk assessment, the organization may encounter disruptions that result in production delays, increased costs, or damage to the company’s reputation.
Thus, the purchasing department’s ability to identify potential risks and devise strategic plans is crucial in maintaining a robust and resilient supply chain.
Identifying Risks in the Supply Chain
Conducting a thorough risk assessment begins with identifying potential risks in the supply chain.
These risks can be divided into several categories:
1. **Supplier Risks**: These involve issues such as supplier bankruptcy, lack of compliance with regulations, or failure to deliver products on time.
2. **Operational Risks**: These can arise from internal processes such as inadequate inventory management or inefficient logistics.
3. **External Risks**: These encompass factors beyond the company’s control, such as economic downturns, political conflicts, or natural disasters.
Understanding these categories is the first step in assessing the potential impact on the supply chain.
Steps in Conducting a Risk Assessment
Once risks have been identified, the purchasing department can follow a systematic approach to assess and mitigate them.
The process generally involves the following steps:
1. **Risk Analysis**: Evaluate the likelihood and impact of each identified risk.
Use quantitative methods, such as statistical analysis, and qualitative assessments, like expert judgment, to prioritize risks based on their severity.
2. **Risk Prioritization**: Not all risks are equal.
Focus on those that have the highest potential to disrupt the supply chain.
This step helps allocate resources efficiently to address the most critical issues first.
3. **Mitigation Strategies**: Develop strategies to minimize the impact of high-priority risks.
This can include diversifying suppliers, increasing inventory buffers, or investing in technology to improve process efficiency.
4. **Implementation and Monitoring**: Once strategies are in place, implement them and continuously monitor their effectiveness.
Regularly review and update risk assessment practices to adapt to changing circumstances and new insights.
Tools and Techniques for Effective Risk Assessment
Purchasing departments can leverage various tools and techniques to enhance their risk assessment process.
Some of the most widely used include:
1. **Supplier Audits and Evaluations**: Regular audits help assess supplier performance and compliance with contractual obligations.
Evaluations can identify areas needing improvement and ensure that suppliers meet necessary standards.
2. **Data Analytics**: Advanced analytical tools can provide insights into supply chain dynamics, uncovering patterns and trends that might indicate potential risks.
These tools help decision-makers make informed choices based on data-driven insights.
3. **Scenario Planning**: This technique involves creating different scenarios to explore how various risks could affect the supply chain.
By understanding possible future situations, companies can develop flexible strategies to respond effectively.
Building a Resilient Supply Chain
A resilient supply chain is one capable of adapting to and recovering from disruptions.
Building such resilience starts with a deep understanding of risk assessment.
By proactively managing risks, purchasing departments can protect the organization from potential threats and ensure a steady flow of goods and services.
Moreover, resilience fosters a competitive advantage as companies are better prepared to handle uncertainties and seize opportunities in a dynamic marketplace.
Collaboration and Communication
Effective risk assessment is not a siloed activity.
It requires collaboration and communication across various departments within the organization.
Purchasing departments should work closely with suppliers, logistics, finance, and production teams to share insights and develop coordinated risk management strategies.
By fostering a culture of collaboration, organizations can enhance their ability to identify, assess, and mitigate risks.
Continuous Improvement in Risk Management
Risk assessment is an ongoing process that evolves with the organization’s needs and the external environment.
Continuous improvement involves regularly reviewing risk management practices, incorporating feedback, and adapting to new developments.
Staying up-to-date with industry trends, emerging risks, and best practices allows purchasing departments to remain agile and responsive to changes.
In conclusion, a well-structured risk assessment method in purchasing departments ensures supply chain safety by identifying potential threats and implementing effective mitigation strategies.
Through consistent evaluation, integration of cutting-edge tools, and fostering collaboration, companies can build resilient supply chains capable of withstanding disruptions and driving success.
資料ダウンロード
QCD調達購買管理クラウド「newji」は、調達購買部門で必要なQCD管理全てを備えた、現場特化型兼クラウド型の今世紀最高の購買管理システムとなります。
ユーザー登録
調達購買業務の効率化だけでなく、システムを導入することで、コスト削減や製品・資材のステータス可視化のほか、属人化していた購買情報の共有化による内部不正防止や統制にも役立ちます。
NEWJI DX
製造業に特化したデジタルトランスフォーメーション(DX)の実現を目指す請負開発型のコンサルティングサービスです。AI、iPaaS、および先端の技術を駆使して、製造プロセスの効率化、業務効率化、チームワーク強化、コスト削減、品質向上を実現します。このサービスは、製造業の課題を深く理解し、それに対する最適なデジタルソリューションを提供することで、企業が持続的な成長とイノベーションを達成できるようサポートします。
オンライン講座
製造業、主に購買・調達部門にお勤めの方々に向けた情報を配信しております。
新任の方やベテランの方、管理職を対象とした幅広いコンテンツをご用意しております。
お問い合わせ
コストダウンが利益に直結する術だと理解していても、なかなか前に進めることができない状況。そんな時は、newjiのコストダウン自動化機能で大きく利益貢献しよう!
(Β版非公開)