- お役立ち記事
- Risk assessment procedures to prevent procurement problems in the purchasing department
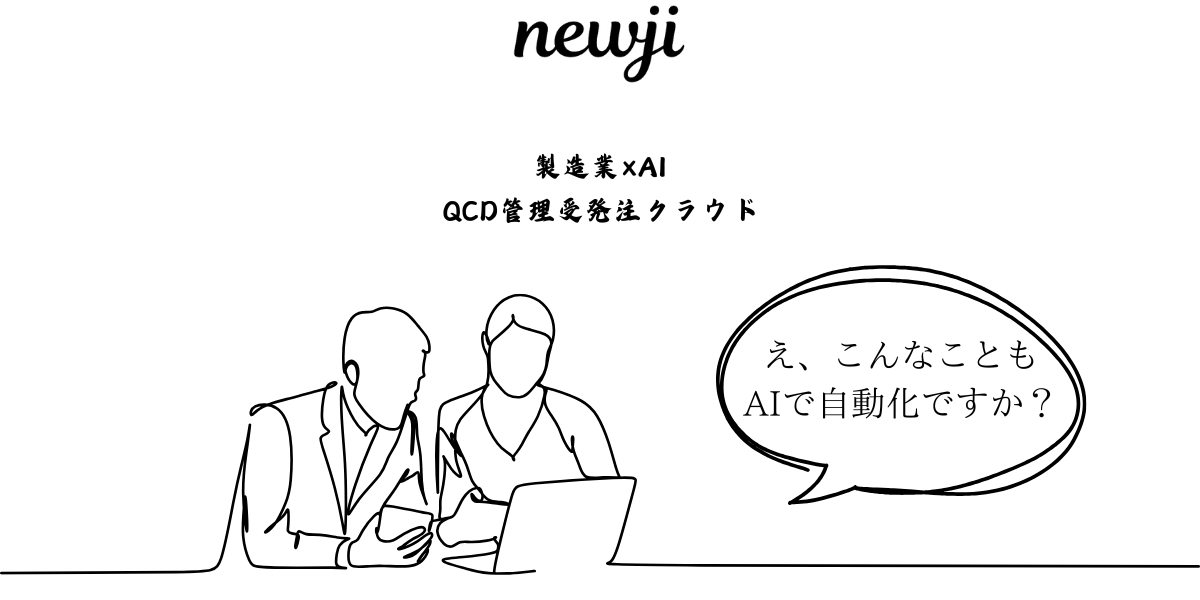
Risk assessment procedures to prevent procurement problems in the purchasing department
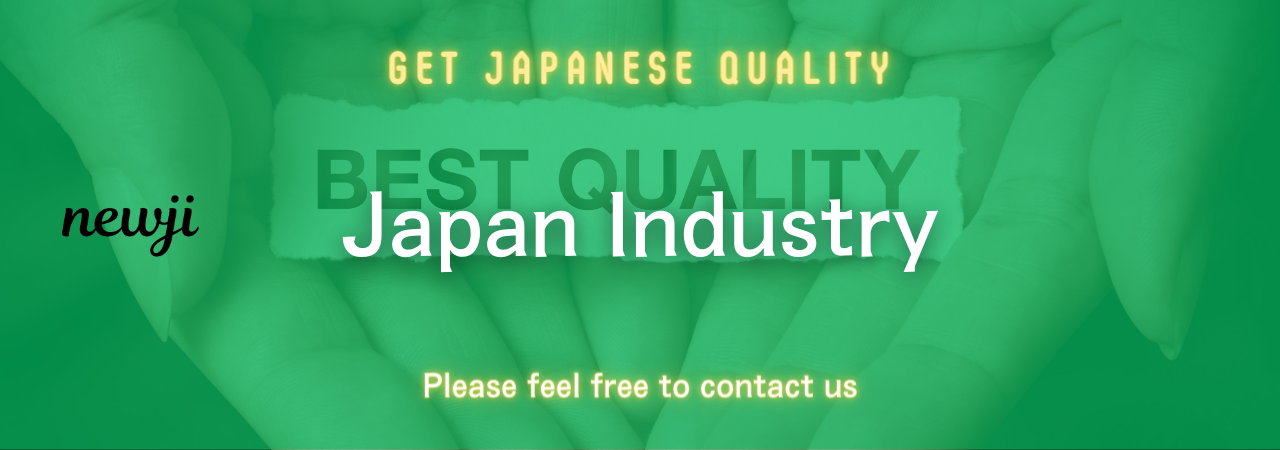
目次
Understanding Risk Assessment in Procurement
In any organization, the purchasing department plays a crucial role in ensuring that the necessary goods and services are obtained efficiently and cost-effectively.
However, the procurement process is fraught with potential problems that can arise if risks are not properly assessed and managed.
Risk assessment procedures are, therefore, critical for preventing procurement problems and ensuring smooth operations.
At its core, risk assessment in procurement involves identifying, analyzing, and prioritizing risks that may hinder the purchasing process.
It requires a strategic approach to foresee potential issues and implement measures to mitigate them.
These risks may include supplier reliability, market volatility, quality issues, and compliance with legal standards, among others.
By following well-established risk assessment procedures, procurement departments can preemptively address these challenges and avoid costly disruptions.
The Stages of Risk Assessment Procedures
The risk assessment process in procurement is typically conducted in several stages.
Each stage builds upon the previous one to create a comprehensive understanding of potential risks and how they can be managed.
1. Risk Identification
The first step in the risk assessment procedure is to identify any potential risks that could affect the procurement process.
This involves analyzing the internal and external environment in which the purchasing department operates.
Internal factors may include company policies, budget constraints, and operational limitations.
External factors could involve market conditions, supplier dependencies, and fluctuating economic conditions.
Procurement professionals can use various tools and techniques to identify risks, such as brainstorming sessions, SWOT analysis (Strengths, Weaknesses, Opportunities, Threats), and interviews with stakeholders.
It is essential to establish a detailed list of potential risks to ensure the evaluation process covers all possibilities.
2. Risk Analysis
Once risks have been identified, the next stage is to analyze them in terms of their likelihood and impact.
This involves assessing how likely each risk is to occur and what the consequences would be if it did.
Risk analysis often involves creating a risk matrix, which helps to categorize each risk based on its probability and impact levels.
This visual representation aids in prioritizing risks, so high-probability and high-impact risks are given more attention than those with low likelihood or impact.
3. Risk Evaluation
In the risk evaluation phase, the procurement team determines which risks are significant enough to require action.
It involves comparing the results of the risk analysis to the organization’s risk appetite and tolerance levels.
Following this, decisions are made on which risks need to be managed actively and which can be monitored or disregarded.
The evaluation process involves discussions with decision-makers to understand the organization’s capacity to absorb certain risks and the potential trade-offs involved in mitigating them.
4. Risk Mitigation
Risk mitigation is the stage at which the procurement department develops strategies to handle the risks that have been identified and evaluated.
Mitigation strategies can include avoiding the risk, reducing its likelihood or impact, transferring the risk to a third party (such as through insurance), or accepting it if it falls within manageable levels.
For example, if supplier reliability is identified as a risk, the procurement department might engage multiple suppliers to diversify their supply chain.
Alternatively, they may negotiate contracts with penalties for non-compliance to protect the organization against delivery failures.
5. Monitoring and Review
Risk assessment is an ongoing process.
The procurement team needs to regularly monitor risks and review mitigation strategies to ensure they remain effective over time.
This part of the process involves tracking key performance indicators and adjusting strategies in response to changes in the risk landscape.
Continuous monitoring enables early detection of new risks and provides an opportunity for the procurement department to adapt their strategies as necessary.
Benefits of Effective Risk Assessment in Procurement
Implementing a robust risk assessment process in procurement can offer numerous benefits to an organization.
1. Improved Decision-Making
By understanding and anticipating potential risks, purchasing departments can make more informed decisions.
They can weigh the pros and cons of different suppliers, contracts, and procurement strategies, enhancing overall decision-making processes.
2. Cost Savings
Proactively managing risks helps prevent costly disruptions and delays in the supply chain.
Compliance issues, delivery failures, and quality problems can be managed in advance, leading to significant cost savings.
3. Enhanced Supplier Relationships
Effective risk management fosters better relationships with suppliers, as there is greater transparency and communication about expectations and risk mitigation plans.
Strong supplier relationships can lead to improved terms, collaborations, and innovation opportunities.
4. Regulatory Compliance
By continuously monitoring risks, procurement departments are better equipped to ensure compliance with regulatory requirements and industry standards.
This reduces the likelihood of legal issues and associated penalties.
Conclusion
The purchasing department is instrumental to an organization’s success, and effective risk assessment is vital to its seamless operation.
By following structured risk assessment procedures—such as identification, analysis, evaluation, mitigation, and ongoing monitoring—the department can prevent potential procurement problems from escalating.
This strategic approach not only guards against disruptions but also supports better decision-making, cost savings, enhanced supplier relationships, and regulatory compliance.
For any organization, focusing on risk assessment in procurement is a smart investment in its operational resilience and long-term success.
資料ダウンロード
QCD調達購買管理クラウド「newji」は、調達購買部門で必要なQCD管理全てを備えた、現場特化型兼クラウド型の今世紀最高の購買管理システムとなります。
ユーザー登録
調達購買業務の効率化だけでなく、システムを導入することで、コスト削減や製品・資材のステータス可視化のほか、属人化していた購買情報の共有化による内部不正防止や統制にも役立ちます。
NEWJI DX
製造業に特化したデジタルトランスフォーメーション(DX)の実現を目指す請負開発型のコンサルティングサービスです。AI、iPaaS、および先端の技術を駆使して、製造プロセスの効率化、業務効率化、チームワーク強化、コスト削減、品質向上を実現します。このサービスは、製造業の課題を深く理解し、それに対する最適なデジタルソリューションを提供することで、企業が持続的な成長とイノベーションを達成できるようサポートします。
オンライン講座
製造業、主に購買・調達部門にお勤めの方々に向けた情報を配信しております。
新任の方やベテランの方、管理職を対象とした幅広いコンテンツをご用意しております。
お問い合わせ
コストダウンが利益に直結する術だと理解していても、なかなか前に進めることができない状況。そんな時は、newjiのコストダウン自動化機能で大きく利益貢献しよう!
(Β版非公開)