- お役立ち記事
- Risk-Based Design for Conceptual Machine Design: Basics and Practical Applications
月間76,176名の
製造業ご担当者様が閲覧しています*
*2025年3月31日現在のGoogle Analyticsのデータより
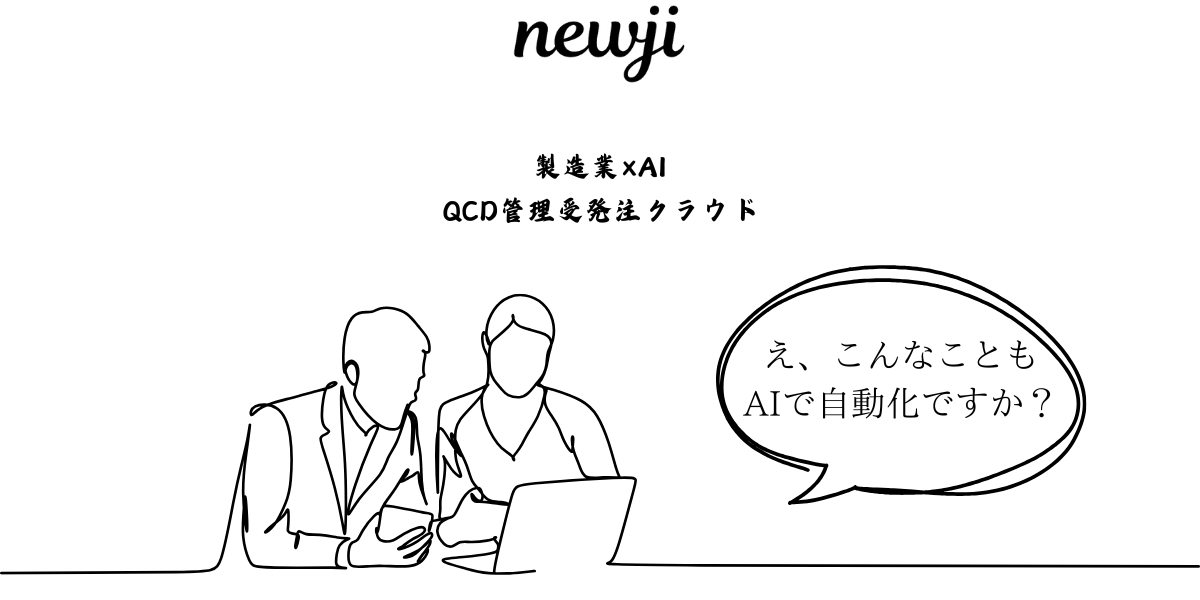
Risk-Based Design for Conceptual Machine Design: Basics and Practical Applications
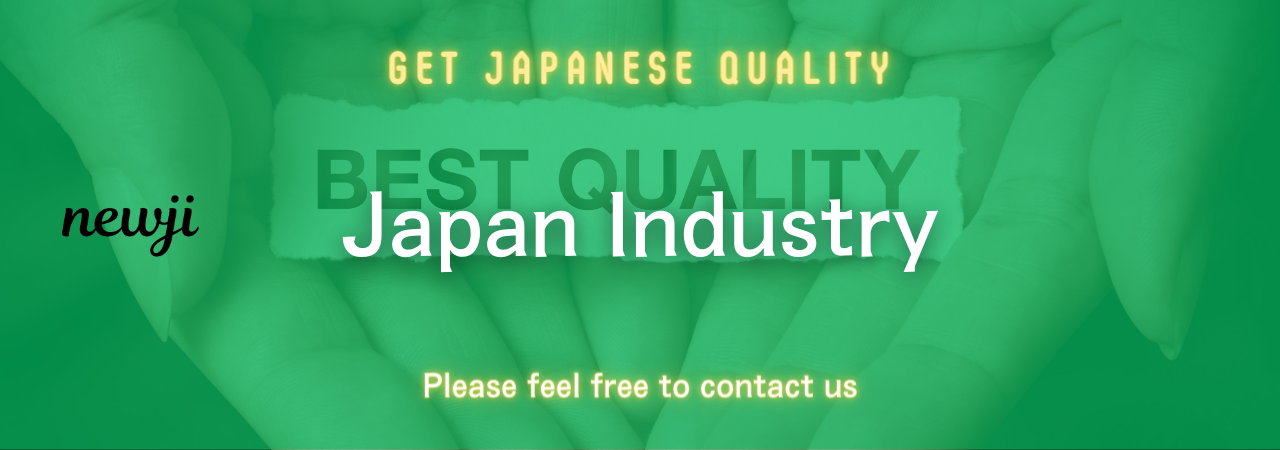
目次
Understanding Risk-Based Design
Risk-based design is a strategic approach that integrates risk assessment and management into the entire design process of machines and systems.
This concept focuses on identifying potential risks early in the design phase, allowing for informed decision-making to mitigate these risks before they manifest into real issues.
The primary goal of risk-based design is to ensure that machines not only meet functional requirements but also adhere to safety, regulatory, and cost-effectiveness standards.
By embedding risk management into the design process, engineers and designers can foresee potential failures, enhancing the reliability and safety of the final product.
The Importance of Risk-Based Design
Incorporating risk-based design into machine conceptualization is crucial for numerous reasons.
Firstly, it helps in identifying safety hazards before they occur, reducing the likelihood of accidents and ensuring that systems remain secure for operators and the environment.
Moreover, understanding the risks involved can significantly decrease the overall design and development costs by highlighting areas where resources could be inefficiently used.
By efficiently managing the risks associated with machine design, companies can shorten the time to market.
This approach aligns product development with market needs, thereby enhancing competitiveness.
Moreover, a well-documented risk-based design process demonstrates due diligence and can be invaluable during regulatory reviews or legal disputes.
Core Principles of Risk-Based Design
A few core principles guide the risk-based design methodology.
One of the foundational elements is to view the design process through the lens of risk assessment.
This involves identifying risk scenarios and assessing their impact on the design’s objectives.
It’s crucial to differentiate between high-priority risks and those that are less significant, allowing for strategic allocation of resources.
Risk-based design requires continuous monitoring and iteration.
Designers must be vigilant in updating risk assessments as new information becomes available or as a project evolves.
This principle ensures that the design remains responsive to changing conditions and incorporates the latest technological and safety standards.
Additionally, collaboration and communication among teams play a vital role.
By promoting interdisciplinary collaboration, potential risks can be viewed from multiple perspectives, enhancing the robustness of the risk analysis and related design solutions.
Steps in Applying Risk-Based Design
Applying risk-based design involves several key steps that align with the broader design and development process.
Below are some steps typically followed:
1. **Risk Identification**: This initial phase involves brainstorming potential risks associated with the machine design.
This can be done through techniques such as failure modes and effects analysis (FMEA) and hazard analysis.
2. **Risk Analysis and Evaluation**: Once potential risks are identified, each risk is analyzed to assess its likelihood and impact.
This step might involve quantitative or qualitative techniques to prioritize risks based on their severity.
3. **Risk Control**: At this stage, strategies to control prioritized risks are developed.
These strategies can include measures like redesigning parts of the machine, implementing additional safety features, or incorporating monitoring systems to provide early warning of potential failures.
4. **Implementation and Monitoring**: The chosen risk control measures are then implemented.
Continuous monitoring ensures that these measures effectively mitigate risks and that new risks are promptly identified and addressed.
5. **Documentation and Feedback Loop**: Throughout the process, documentation is crucial for future reference, regulatory compliance, and knowledge sharing.
Feedback from monitoring and post-implementation evaluation feeds into future design projects, creating a loop of continuous improvement.
Practical Applications of Risk-Based Design
Risk-based design is particularly relevant in high-stakes industries such as aerospace, automotive, and medical device manufacturing.
In these sectors, the consequences of design failures can be catastrophic, making risk management essential.
For instance, in the automotive industry, risk-based design ensures that vehicles meet stringent safety standards.
By preemptively addressing potential design flaws, manufacturers can prevent costly recalls and enhance consumer trust.
In the medical devices field, risk-based design helps ensure that products are safe and effective for clinical use.
Regulatory bodies, like the FDA, often require detailed risk assessments to approve new medical devices.
Even in less regulated industries, risk-based design provides substantial value by fostering innovation.
By freeing resources from low-risk areas, companies can invest in R&D to explore new technologies and product features.
Challenges and Considerations
While the benefits of risk-based design are clear, implementing this approach comes with challenges.
One significant hurdle is the potential for analysis paralysis, where teams over-analyze risks at the expense of design progression.
Balancing thorough risk assessment with forward momentum in project timelines is key.
Another challenge is ensuring that all team members have the skills and understanding required to conduct effective risk assessments.
This might require additional training or hiring new talent with specific expertise.
Finally, while collaboration is essential, it can also lead to complexity in decision-making.
Managing interdisciplinary teams effectively requires strong leadership and clear communication channels.
Conclusion
Risk-based design is a valuable approach for any organization involved in the conceptual machine design.
By integrating risk management into the design process, companies can enhance safety, reduce costs, and improve product quality.
Despite the challenges, the structured, proactive management of risks can lead to significant competitive advantages, making risk-based design an essential practice in innovative and responsible engineering.
資料ダウンロード
QCD管理受発注クラウド「newji」は、受発注部門で必要なQCD管理全てを備えた、現場特化型兼クラウド型の今世紀最高の受発注管理システムとなります。
ユーザー登録
受発注業務の効率化だけでなく、システムを導入することで、コスト削減や製品・資材のステータス可視化のほか、属人化していた受発注情報の共有化による内部不正防止や統制にも役立ちます。
NEWJI DX
製造業に特化したデジタルトランスフォーメーション(DX)の実現を目指す請負開発型のコンサルティングサービスです。AI、iPaaS、および先端の技術を駆使して、製造プロセスの効率化、業務効率化、チームワーク強化、コスト削減、品質向上を実現します。このサービスは、製造業の課題を深く理解し、それに対する最適なデジタルソリューションを提供することで、企業が持続的な成長とイノベーションを達成できるようサポートします。
製造業ニュース解説
製造業、主に購買・調達部門にお勤めの方々に向けた情報を配信しております。
新任の方やベテランの方、管理職を対象とした幅広いコンテンツをご用意しております。
お問い合わせ
コストダウンが利益に直結する術だと理解していても、なかなか前に進めることができない状況。そんな時は、newjiのコストダウン自動化機能で大きく利益貢献しよう!
(β版非公開)