- お役立ち記事
- Risk-based maintenance (RBM) and its practice as rational maintenance
月間77,185名の
製造業ご担当者様が閲覧しています*
*2025年2月28日現在のGoogle Analyticsのデータより
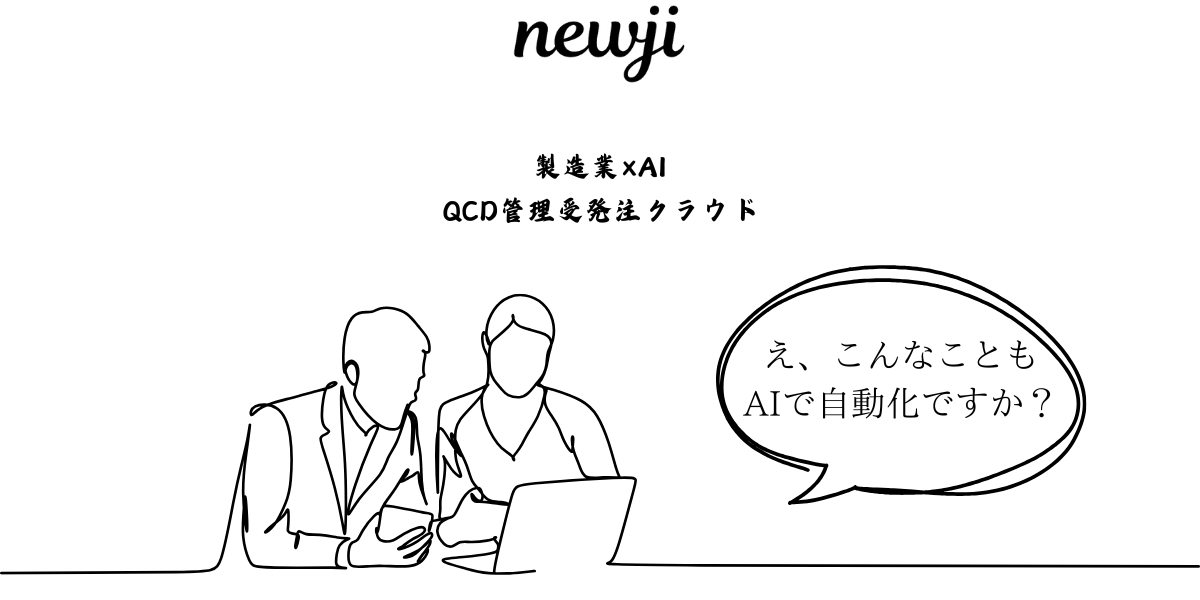
Risk-based maintenance (RBM) and its practice as rational maintenance
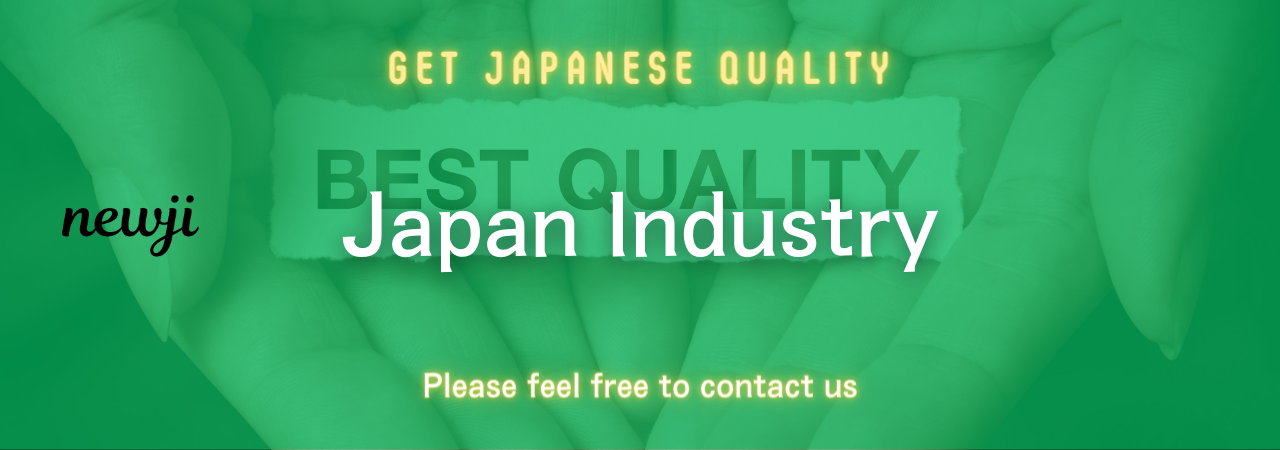
Understanding Risk-Based Maintenance (RBM)
Risk-Based Maintenance, commonly referred to as RBM, is a systematic approach to maintaining equipment by prioritizing tasks based on the risk of failure and its impact on operations.
Unlike traditional maintenance strategies, which often follow set schedules or respond to breakdowns, RBM aims to optimize resources by focusing efforts where they are needed most.
This approach is particularly useful in industries where equipment reliability is essential for safety, production efficiency, and cost management.
RBM considers multiple factors, including an asset’s condition, its criticality in operations, the likelihood of failure, and the potential consequences of such failures.
By evaluating these factors, RBM determines the maintenance actions required to minimize risk while maximizing asset performance and life.
Benefits of Risk-Based Maintenance
One of the primary benefits of RBM is improved allocation of maintenance resources.
By focusing efforts where the risk is highest, organizations can avoid unnecessary inspections or maintenance activities that don’t add value.
This makes maintenance activities more efficient and reduces downtime, resulting in high equipment availability and performance.
Additionally, RBM can be instrumental in ensuring safety.
By identifying and addressing potential failure modes that pose serious risks, the likelihood of catastrophic events is reduced.
This proactive stance protects both employees and infrastructure from potential hazards.
Cost savings also arise from RBM because it helps to avoid unplanned downtime and the associated repair costs.
By predicting and preventing failures, potential financial losses are minimized.
Over time, improved maintenance efficiency contributes to a reduction in overall maintenance costs.
Implementing RBM in Your Organization
Implementing RBM involves several key steps to be effective.
Firstly, it’s crucial to identify and classify all assets within the organization according to their importance and impact on operations.
Assets can be categorized into critical, important, or non-critical based on factors like production line placement or safety significance.
Once assets are classified, risk assessments are conducted.
This involves evaluating the likelihood of failure and the potential impact on operations.
Tools such as Failure Mode Effects and Criticality Analysis (FMECA) or Root Cause Analysis (RCA) can be used to perform these assessments.
These analyses help to pinpoint where maintenance efforts should be concentrated to mitigate risks effectively.
The development of a risk-based maintenance plan follows these assessments.
The plan should outline specific maintenance tasks, schedules, and responsible personnel.
It should prioritize high-risk assets while also ensuring that routine maintenance for less critical equipment contributes positively to the overall strategy.
For RBM to be successful, collaboration and communication across departments are vitally important.
Engineering, operations, and maintenance teams must work together, sharing data and insights to refine the method constantly.
Regular reviews of performance data ensure that the RBM strategy adapts to changing conditions and new developments.
Challenges in RBM Implementation
While RBM presents numerous advantages, there are challenges that organizations may encounter.
A significant hurdle can be the initial resistance to change.
Employees accustomed to traditional maintenance might be skeptical of the new approach and wary of its reliance on risk assessment and data analytics.
Adopting RBM also requires an investment in technology and training.
Sensors, monitoring equipment, and analytics software are essential for gathering accurate data.
Furthermore, staff must be trained to interpret data effectively and adjust maintenance plans accordingly.
Data management is another common challenge.
Collecting an immense amount of data requires robust systems to store, process, and analyze it.
Organizations need to ensure their data infrastructure is capable of handling these demands to avoid overwhelming maintenance teams with information that is difficult to act upon.
The Future of Risk-Based Maintenance
The future of RBM looks promising, with advances in technology contributing to more effective and efficient practices.
The integration of the Internet of Things (IoT) in maintenance, for example, is already enhancing the ability to monitor equipment in real-time, predict potential failures, and automate responses.
Artificial intelligence (AI) and machine learning are also transforming RBM by providing more accurate and insightful data analysis.
These technologies allow maintenance teams to predict and respond to potential issues faster than ever before, further reducing risk and improving productivity.
As organizations become more data-driven, the implementation of RBM is likely to continue to grow.
Industries with critical and expensive equipment, such as oil and gas, manufacturing, and transportation, are set to benefit significantly from ongoing advancements in RBM practices.
In conclusion, risk-based maintenance represents a strategic step forward in rational maintenance management.
By focusing efforts on high-risk areas, improving safety, and optimizing costs, RBM stands as an ideal approach to maintaining complex industrial systems.
資料ダウンロード
QCD管理受発注クラウド「newji」は、受発注部門で必要なQCD管理全てを備えた、現場特化型兼クラウド型の今世紀最高の受発注管理システムとなります。
ユーザー登録
受発注業務の効率化だけでなく、システムを導入することで、コスト削減や製品・資材のステータス可視化のほか、属人化していた受発注情報の共有化による内部不正防止や統制にも役立ちます。
NEWJI DX
製造業に特化したデジタルトランスフォーメーション(DX)の実現を目指す請負開発型のコンサルティングサービスです。AI、iPaaS、および先端の技術を駆使して、製造プロセスの効率化、業務効率化、チームワーク強化、コスト削減、品質向上を実現します。このサービスは、製造業の課題を深く理解し、それに対する最適なデジタルソリューションを提供することで、企業が持続的な成長とイノベーションを達成できるようサポートします。
製造業ニュース解説
製造業、主に購買・調達部門にお勤めの方々に向けた情報を配信しております。
新任の方やベテランの方、管理職を対象とした幅広いコンテンツをご用意しております。
お問い合わせ
コストダウンが利益に直結する術だと理解していても、なかなか前に進めることができない状況。そんな時は、newjiのコストダウン自動化機能で大きく利益貢献しよう!
(β版非公開)