- お役立ち記事
- Risk-based maintenance (RBM) as rational maintenance and its practice
月間77,185名の
製造業ご担当者様が閲覧しています*
*2025年2月28日現在のGoogle Analyticsのデータより
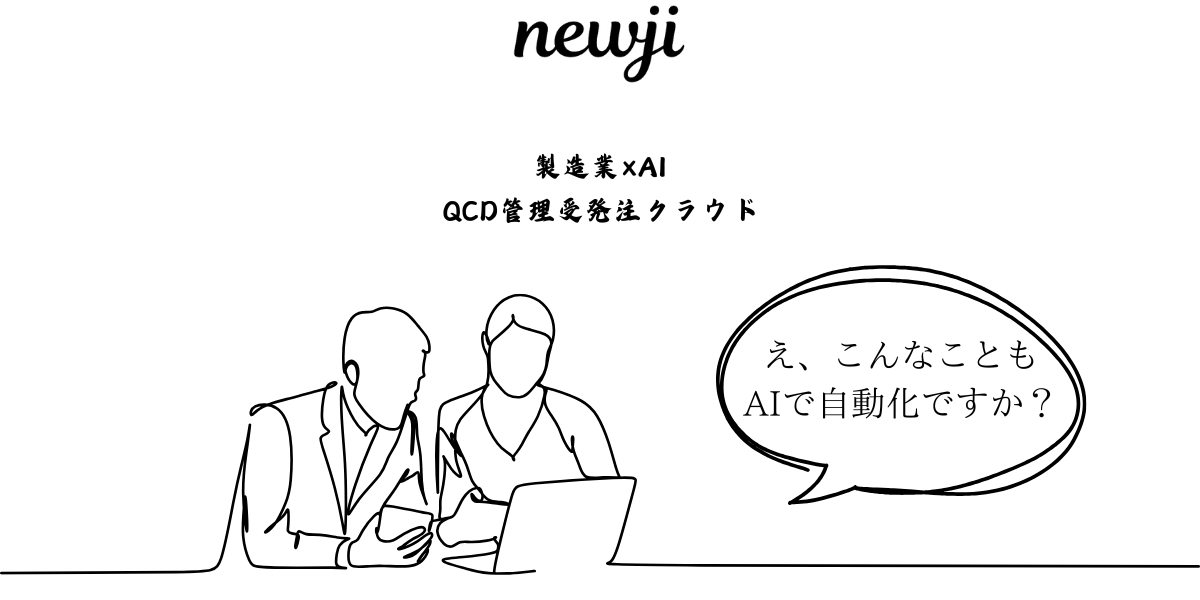
Risk-based maintenance (RBM) as rational maintenance and its practice
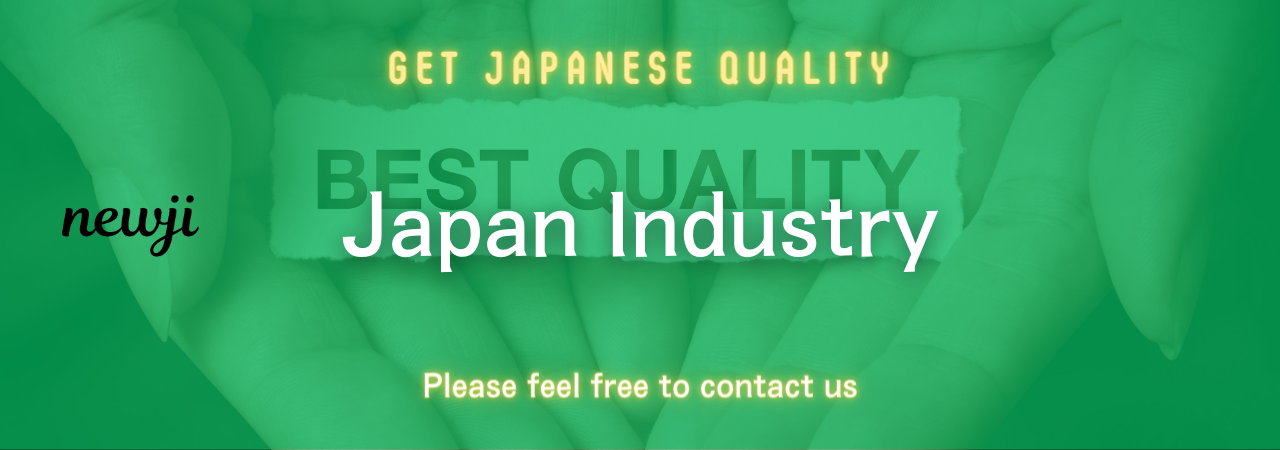
目次
What is Risk-Based Maintenance (RBM)?
Risk-Based Maintenance (RBM) is a strategic maintenance approach that prioritizes resources based on risk assessment.
Unlike traditional maintenance methods that schedule preventive tasks at regular intervals, RBM focuses on evaluating the potential risks associated with equipment failure.
This approach enables organizations to allocate their maintenance efforts where they are most needed, improving safety, reliability, and cost efficiency.
By identifying and addressing high-risk areas, RBM helps prevent unexpected downtime and extends the lifespan of assets.
The Importance of RBM in Modern Industry
RBM has gained significant attention in various industries due to its effectiveness in optimizing maintenance processes.
In sectors such as manufacturing, oil and gas, and utilities, equipment failure can lead to substantial financial losses and safety hazards.
Implementing RBM allows companies to mitigate these risks by prioritizing maintenance based on the severity and likelihood of potential failures.
By focusing on high-risk assets, businesses can enhance operational reliability and ensure compliance with safety regulations.
This proactive maintenance strategy also reduces unplanned downtime, leading to increased productivity and improved customer satisfaction.
Key Components of Risk-Based Maintenance
To successfully implement RBM, several key components must be considered:
Risk Assessment
Risk assessment is the foundation of RBM.
It involves evaluating the probability and consequences of equipment failure to identify which assets pose the greatest risk to operations.
Risk assessments typically consider factors such as asset criticality, failure history, and potential impact on safety and production.
By continuously analyzing these variables, organizations can make informed decisions on maintenance priorities and allocate resources effectively.
Failure Modes and Effects Analysis (FMEA)
FMEA is a crucial tool in RBM that helps identify potential failure modes of equipment and their effects on the system.
This analysis assists in understanding how a failure can occur and the severity of its impact.
By systematically examining components and subsystems, FMEA enables maintenance teams to develop targeted strategies to mitigate risks and enhance asset reliability.
Condition Monitoring
Condition monitoring involves using technologies such as sensors and data analytics to monitor equipment health in real-time.
By collecting data on parameters like temperature, vibration, and pressure, organizations can detect early signs of wear and potential failures.
This information allows maintenance teams to perform timely interventions, reducing the likelihood of unexpected breakdowns while optimizing maintenance schedules.
Root Cause Analysis (RCA)
Root Cause Analysis is employed to investigate the underlying causes of equipment failures.
By identifying and addressing the root causes, organizations can prevent recurrence and improve asset performance.
RCA helps in refining maintenance strategies and ensures that corrective actions are implemented effectively.
Benefits of Risk-Based Maintenance
Applying an RBM approach offers numerous benefits to organizations:
Enhanced Asset Reliability
By concentrating maintenance efforts on high-risk assets, RBM improves the reliability and longevity of equipment.
Minimized failures translate to less downtime and higher productivity, ultimately resulting in increased profitability for businesses.
Cost Efficiency
RBM optimizes maintenance budgets by channeling resources toward critical assets requiring immediate attention.
This targeted approach prevents overspending on less essential equipment, allowing organizations to allocate funds wisely while achieving significant cost savings in the long run.
Safety Improvement
The focus on risk reduction in RBM directly contributes to improved safety in the workplace.
By addressing potential failures before they occur, companies can create a safer environment for employees, reducing accident risks and ensuring compliance with industry regulations.
Informed Decision-Making
The data-driven nature of RBM enables organizations to make informed decisions based on accurate risk assessments and equipment condition analysis.
With valuable insights, maintenance teams can prioritize tasks effectively, optimizing resources and ensuring smooth operations.
Implementing Risk-Based Maintenance
For successful RBM implementation, companies should follow a structured process:
Data Collection and Analysis
Gathering data on equipment performance and failure history is the first step.
Advanced data analytics tools help analyze the information, identifying patterns and areas of concern.
This insight aids in conducting accurate risk assessments.
Identifying Critical Assets
Determine which assets are critical to operations and require prioritized maintenance.
Focus on those with high risks of failure and significant impacts on safety and production.
Risk Prioritization and Planning
Prioritize maintenance tasks based on risk levels.
Develop a maintenance plan that allocates resources efficiently, targeting high-risk assets while considering resource availability.
Continuous Monitoring and Improvement
Implement condition monitoring technologies to track asset performance in real-time.
Continuously evaluate and refine the RBM strategy to address emerging risks and improve maintenance processes.
Challenges of Risk-Based Maintenance
Despite its numerous advantages, RBM implementation can present challenges:
Data Management
Collecting and managing large volumes of data can be overwhelming without the right technology and expertise.
Investing in robust data management systems and skilled personnel is essential for effective RBM implementation.
Cultural Change
Transitioning from traditional maintenance practices to RBM may require a cultural shift within the organization.
Employee training and engagement are crucial to ensure successful adoption and implementation of the new approach.
Initial Investment
Implementing RBM necessitates upfront investment in technology and training.
However, the long-term benefits in terms of cost savings and efficiency make it a worthwhile endeavor for forward-thinking organizations.
Risk-Based Maintenance is a powerful strategy for optimizing maintenance processes and enhancing operational efficiency.
By focusing on risk reduction and informed decision-making, businesses can achieve improved reliability, cost savings, and a safer working environment.
Though challenges exist, the implementation of RBM paves the way for a more sustainable and competitive future in industries that rely heavily on asset performance.
資料ダウンロード
QCD管理受発注クラウド「newji」は、受発注部門で必要なQCD管理全てを備えた、現場特化型兼クラウド型の今世紀最高の受発注管理システムとなります。
ユーザー登録
受発注業務の効率化だけでなく、システムを導入することで、コスト削減や製品・資材のステータス可視化のほか、属人化していた受発注情報の共有化による内部不正防止や統制にも役立ちます。
NEWJI DX
製造業に特化したデジタルトランスフォーメーション(DX)の実現を目指す請負開発型のコンサルティングサービスです。AI、iPaaS、および先端の技術を駆使して、製造プロセスの効率化、業務効率化、チームワーク強化、コスト削減、品質向上を実現します。このサービスは、製造業の課題を深く理解し、それに対する最適なデジタルソリューションを提供することで、企業が持続的な成長とイノベーションを達成できるようサポートします。
製造業ニュース解説
製造業、主に購買・調達部門にお勤めの方々に向けた情報を配信しております。
新任の方やベテランの方、管理職を対象とした幅広いコンテンツをご用意しております。
お問い合わせ
コストダウンが利益に直結する術だと理解していても、なかなか前に進めることができない状況。そんな時は、newjiのコストダウン自動化機能で大きく利益貢献しよう!
(β版非公開)