- お役立ち記事
- Risk management and problem solving methods when changing suppliers in the manufacturing industry
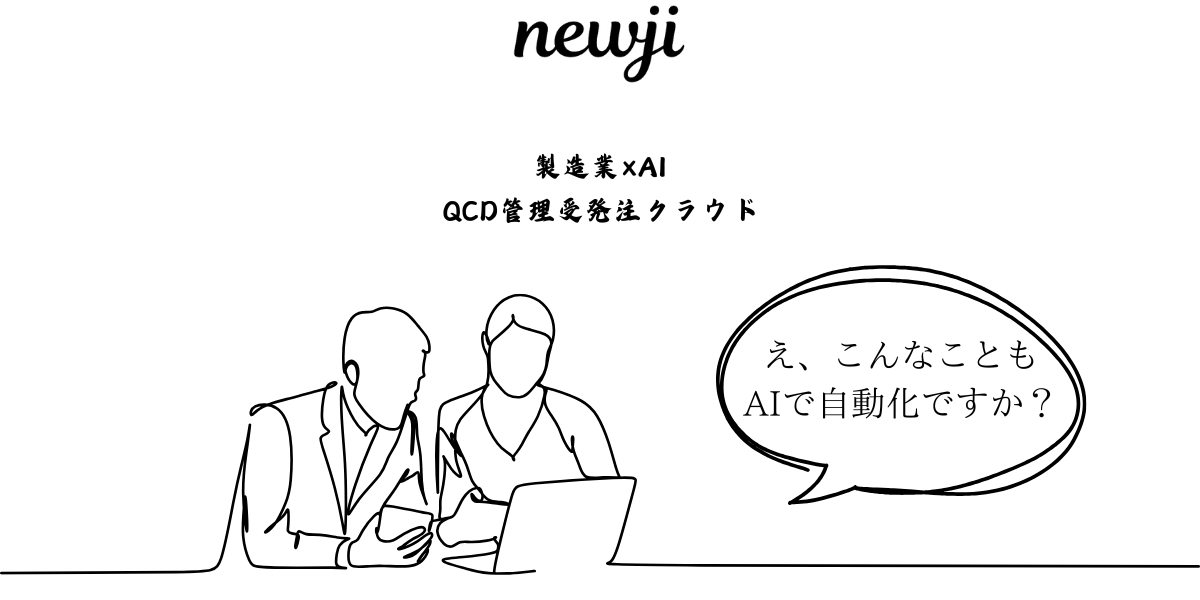
Risk management and problem solving methods when changing suppliers in the manufacturing industry
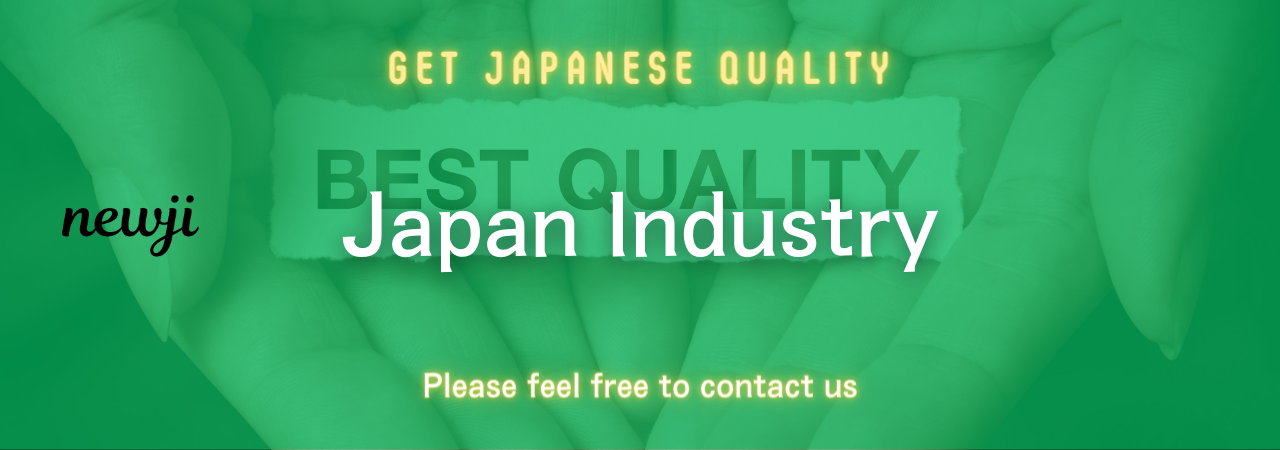
目次
Understanding Risk Management in Supplier Changes
When it comes to the manufacturing industry, ensuring continuity and efficiency involves carefully managing various aspects of the supply chain.
One crucial component that often demands strategic attention is supplier change.
Changing suppliers can be driven by numerous factors, such as cost reduction, quality improvement, or supply chain diversification.
However, these changes come with inherent risks that need to be meticulously managed.
An effective risk management strategy begins with identifying potential risks associated with changing suppliers.
Disruptions in supply can lead to production delays, increased costs, or even a compromise in product quality.
Therefore, a comprehensive risk assessment is necessary to foresee challenges and establish mitigation plans.
Conducting Thorough Supplier Evaluation
Before transitioning to a new supplier, conducting a detailed evaluation is vital.
This involves assessing the supplier’s capability to meet your demands in terms of quality, quantity, and timeliness.
An ideal supplier should align with your company’s standards and expectations.
A thorough evaluation includes on-site visits, quality audits, financial stability checks, and reviewing the supplier’s past performance.
Establishing an open line of communication with potential suppliers helps in accurately gauging their reliability and capabilities.
This step not only aids in risk identification but also strengthens the foundation of a trusted partnership.
Developing a Contingency Plan
No matter how well-prepared you are, unforeseen challenges may arise when changing suppliers.
This is where a robust contingency plan comes into play.
A well-drafted plan outlines a course of action in the event of a supply disruption, ensuring that the impact on production is minimized.
Your contingency plan should include alternative supplier options, buffer stock strategies, and defined roles and responsibilities within your organization in case of an emergency.
Engaging with multiple suppliers and maintaining a safety stock can significantly mitigate risks associated with sudden supplier inadequacies.
Problem Solving Methods in Supplier Transition
Transitioning to a new supplier involves addressing various problems that may arise both during and after the switch.
Anticipating these problems and having a structured problem-solving approach can greatly smooth out the transition process.
Effective Communication and Collaboration
Communication is a critical factor in mitigating issues during supplier changes.
All stakeholders, including internal teams and external partners, should be kept in the loop about the changes taking place.
Ensure that information flows seamlessly to avoid misunderstandings which can lead to bigger problems.
Building a collaborative environment between your organization and the new supplier helps in synchronizing processes and expectations.
Regular meetings, updates, and feedback sessions foster a healthy relationship and ensure that everyone is aligned with the project goals.
Proactive Issue Resolution Protocols
To address potential issues swiftly, having predefined issue resolution protocols is imperative.
When problems emerge, they should be escalated according to a set plan that involves root cause analysis and immediate rectification.
Utilize problem-solving frameworks such as the PDCA (Plan-Do-Check-Act) cycle to ensure a systematic approach to tackling issues.
Implementing corrective measures, followed by verification of their effectiveness, can prevent recurrences.
Leveraging Technology and Data Analytics
Incorporating technology and data analytics is crucial in modern-day problem solving.
Using data-driven insights can identify patterns and predict potential supply chain issues before they escalate.
Implement supply chain management software to monitor real-time data.
This aids in maintaining transparency and provides comprehensive visibility, enabling informed decision-making.
Predictive analytics enhance proactive measures, allowing businesses to adjust plans based on data trends.
Strategies for Successful Supplier Integration
The ultimate goal of managing risk and solving problems during a supplier change is to achieve a seamless integration.
Having strategic processes in place ensures a smooth transition and maximizes long-term benefits.
Comprehensive Training Programs
Equipping both your internal team and the supplier’s team with training programs is vital.
These programs should cover new processes, technologies, and quality expectations to ensure everyone is on the same page.
Invest in cross-training initiatives to make employees more versatile and adaptable to new systems and supplier methods.
Training improves efficiency and reduces the likelihood of errors during the transition period.
Performance Monitoring and Continuous Improvement
Once the supplier integration is complete, continuous monitoring is crucial.
Establish key performance indicators (KPIs) to measure supplier performance and ensure adherence to your predetermined standards.
Regular performance evaluations and feedback loops help identify areas for improvement.
Engage in a cycle of continuous improvement to refine processes, enhance product quality, and build a resilient supply chain.
Nurturing Long-term Partnerships
Building a long-term partnership with your suppliers goes beyond the initial integration phase.
Consider your suppliers as strategic partners rather than mere transactions.
Regularly communicate strategic goals and collaborate on innovation and improvement projects.
This collaborative approach promotes trust and accountability, resulting in a robust supply chain partnership that supports mutual growth.
In conclusion, managing risk and solving problems when changing suppliers in the manufacturing industry requires a proactive, structured approach.
By understanding the nuances of supplier evaluation, developing contingency plans, and fostering effective communication, businesses can minimize disruptions.
Leveraging technology for data-driven decisions and focusing on successful integration strategies ensures a smoother transition.
Ultimately, these efforts contribute to a resilient, efficient, and reliable supply chain.
資料ダウンロード
QCD調達購買管理クラウド「newji」は、調達購買部門で必要なQCD管理全てを備えた、現場特化型兼クラウド型の今世紀最高の購買管理システムとなります。
ユーザー登録
調達購買業務の効率化だけでなく、システムを導入することで、コスト削減や製品・資材のステータス可視化のほか、属人化していた購買情報の共有化による内部不正防止や統制にも役立ちます。
NEWJI DX
製造業に特化したデジタルトランスフォーメーション(DX)の実現を目指す請負開発型のコンサルティングサービスです。AI、iPaaS、および先端の技術を駆使して、製造プロセスの効率化、業務効率化、チームワーク強化、コスト削減、品質向上を実現します。このサービスは、製造業の課題を深く理解し、それに対する最適なデジタルソリューションを提供することで、企業が持続的な成長とイノベーションを達成できるようサポートします。
オンライン講座
製造業、主に購買・調達部門にお勤めの方々に向けた情報を配信しております。
新任の方やベテランの方、管理職を対象とした幅広いコンテンツをご用意しております。
お問い合わせ
コストダウンが利益に直結する術だと理解していても、なかなか前に進めることができない状況。そんな時は、newjiのコストダウン自動化機能で大きく利益貢献しよう!
(Β版非公開)