- お役立ち記事
- Risk management and reliability improvement in FMEA that should be addressed by project managers in product design departments
Risk management and reliability improvement in FMEA that should be addressed by project managers in product design departments
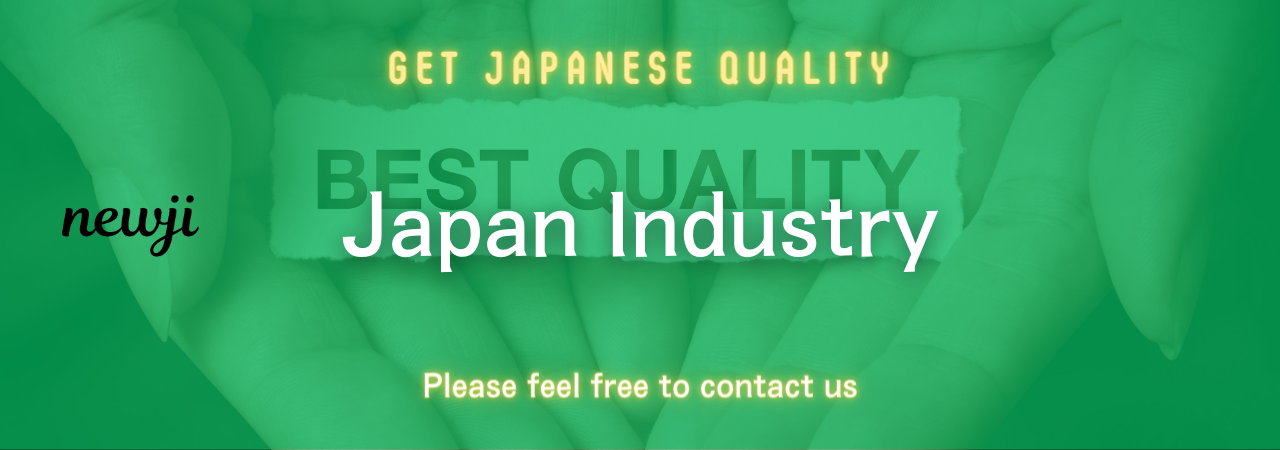
目次
Understanding FMEA in Product Design
Failure Modes and Effects Analysis, commonly known as FMEA, is a systematic approach used by project managers in product design departments to identify potential failure points in a product or process.
By identifying these potential failures, teams can assess the potential impact of each failure and prioritize actions to mitigate associated risks.
This proactive risk management tool is essential for ensuring the reliability and quality of products before they reach the market.
The Importance of FMEA in Product Design
In product design, the stakes are high as the goal is to create a product that meets customer expectations while ensuring safety and reliability.
FMEA helps the design team anticipate issues that might otherwise go unnoticed until after the product launch.
By addressing these issues early on, companies can save on costs, prevent potential failures, improve customer satisfaction, and maintain a strong brand reputation.
Project managers play a pivotal role in FMEA processes within the product design department.
They ensure that the analysis is thorough and that all possible failure modes are considered.
Their leadership in this process helps align the team on the goals of reliability and risk management.
FMEA Process: A Step-by-Step Approach
The FMEA process can be broken down into several key steps that help manage risks and improve product reliability effectively.
1. Define the Scope and Objectives
Before beginning FMEA, it’s critical to define the scope of the project and set clear objectives.
This includes understanding the specific part, system, or process being analyzed and determining the boundaries within which the analysis will take place.
Setting clear objectives helps the team focus on identifying failure modes relevant to their design project.
2. Identify Potential Failure Modes
Once the scope is identified, the next step is to brainstorm and pinpoint possible failure modes.
A failure mode is any way a process or product might fail to perform its intended function.
During this phase, the team should focus on thoroughly considering all conceivable types of failures.
3. Analyze the Effects of Each Failure Mode
After identifying potential failure modes, the team needs to evaluate the effects of each failure.
This involves understanding the consequences these failures could have on the system, the end-user, and the overall business.
Assessing the severity of each failure helps in determining its potential impact on product quality and safety.
4. Assign Severity, Occurrence, and Detection Ratings
The next step involves assigning ratings for severity, occurrence, and detection for each identified failure mode.
Severity measures the potential impact of the failure, occurrence estimates the probability of the failure happening, and detection assesses the likelihood of detecting the failure before it impacts the user.
These ratings help prioritize which failure modes need immediate attention.
5. Calculate the Risk Priority Number (RPN)
The Risk Priority Number (RPN) is then calculated by multiplying the severity, occurrence, and detection ratings.
The RPN provides a quantitative value that helps prioritize risks.
Higher RPNs indicate higher-priority failures that should be addressed with greater urgency.
Improving Reliability Through FMEA
Understanding and implementing FMEA isn’t just about identifying potential issues.
It’s about taking corrective actions to improve reliability and reduce the likelihood of failure.
1. Implement Corrective Actions
Once high-priority failure modes are identified through the RPN, the project manager guides the team in developing and implementing corrective actions.
These actions could involve design changes, material substitutions, process improvements, or implementing stricter quality controls.
2. Monitor and Review the FMEA Process
Continuous monitoring and regular reviews of the FMEA process are essential to ensure effectiveness and relevance.
The product design and development cycles are dynamic; therefore, the FMEA must adapt to changes in design specifications, regulations, and customer requirements.
3. Foster a Culture of Continuous Improvement
Project managers should encourage a culture of continuous improvement within the product design department.
By regularly updating the FMEA based on feedback and test results, the design team can consistently enhance product reliability and performance over time.
The Role of Technology in FMEA
The advancement in technology has provided new tools to aid in the FMEA process, significantly enhancing its effectiveness.
1. Software Solutions
There are various software solutions available that facilitate efficient FMEA processes.
These tools often include features for creating detailed reports, tracking changes, and sharing insights with team members.
Utilizing these software solutions can improve accuracy and streamline communication within the team.
2. Data Analytics
Data analytics can provide significant insights into product performance by analyzing real-world usage data.
Incorporating data-driven approaches into FMEA allows for the identification of failure modes that may not be evident through traditional analysis alone.
3. Automation and AI
The integration of automation and artificial intelligence into FMEA can also lead to significant efficiency improvements.
AI can help simulate potential failure modes at greater speeds and with higher accuracies, allowing project managers to focus on developing solutions.
Conclusion
FMEA is a crucial process for project managers in product design departments aiming to mitigate risks and enhance reliability.
By systematically analyzing potential failure modes and their effects, project teams can safeguard against potential issues and build products that meet high standards of quality and customer satisfaction.
The proactive application of FMEA determines the success of a product in the market and reinforces the brand’s reputation for reliability and excellence.
With the aid of new technologies, teams can make FMEA processes more efficient, paving the way for innovative and reliable product design.
資料ダウンロード
QCD調達購買管理クラウド「newji」は、調達購買部門で必要なQCD管理全てを備えた、現場特化型兼クラウド型の今世紀最高の購買管理システムとなります。
ユーザー登録
調達購買業務の効率化だけでなく、システムを導入することで、コスト削減や製品・資材のステータス可視化のほか、属人化していた購買情報の共有化による内部不正防止や統制にも役立ちます。
NEWJI DX
製造業に特化したデジタルトランスフォーメーション(DX)の実現を目指す請負開発型のコンサルティングサービスです。AI、iPaaS、および先端の技術を駆使して、製造プロセスの効率化、業務効率化、チームワーク強化、コスト削減、品質向上を実現します。このサービスは、製造業の課題を深く理解し、それに対する最適なデジタルソリューションを提供することで、企業が持続的な成長とイノベーションを達成できるようサポートします。
オンライン講座
製造業、主に購買・調達部門にお勤めの方々に向けた情報を配信しております。
新任の方やベテランの方、管理職を対象とした幅広いコンテンツをご用意しております。
お問い合わせ
コストダウンが利益に直結する術だと理解していても、なかなか前に進めることができない状況。そんな時は、newjiのコストダウン自動化機能で大きく利益貢献しよう!
(Β版非公開)