- お役立ち記事
- Risk mitigation process recommended by purchasing department when changing suppliers
月間76,176名の
製造業ご担当者様が閲覧しています*
*2025年3月31日現在のGoogle Analyticsのデータより
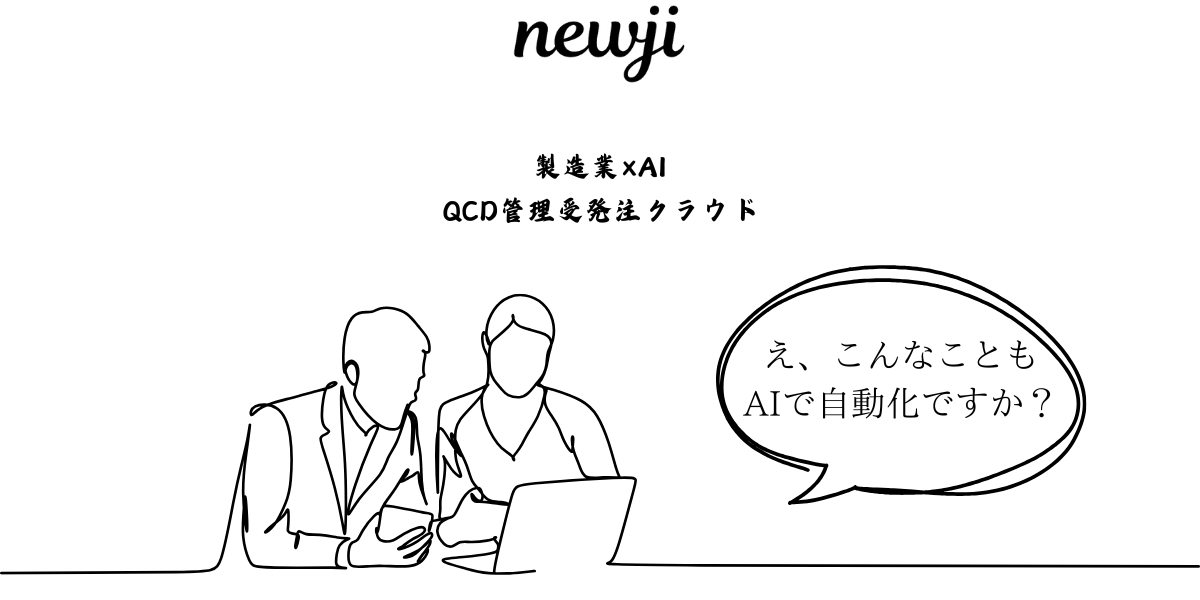
Risk mitigation process recommended by purchasing department when changing suppliers
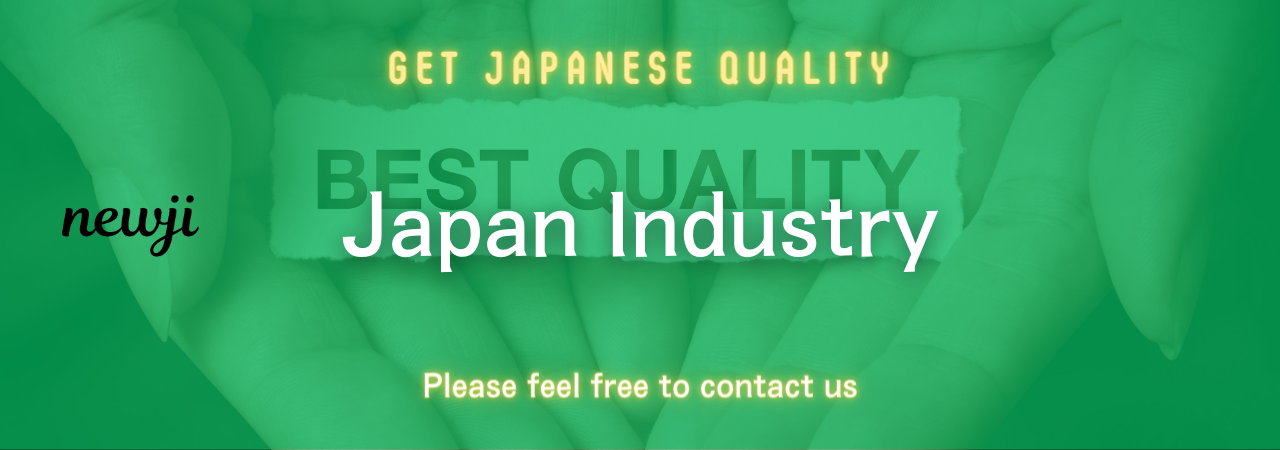
目次
Understanding Risk Mitigation in Supplier Changes
Changing suppliers is a common occurrence in the purchasing department of any business.
However, it can bring about significant risks if not handled properly.
The act of switching from one supplier to another might seem straightforward, but it involves numerous critical steps that ensure the business continues to operate smoothly.
Understanding and implementing a risk mitigation process is essential for minimizing potential disruptions.
The Importance of Risk Mitigation
Risk mitigation refers to the strategies and processes implemented to minimize potential problems that could derail the business’s operations or objectives.
When it comes to changing suppliers, these risks can range from quality issues and delivery delays to increased costs and compliance problems.
The primary goal of risk mitigation in supplier changes is to ensure continuity in operations without compromising on product quality or customer service.
An effective risk mitigation strategy means recognizably lower chances of running into unwanted surprises that could negatively impact the business.
Key Steps in Risk Mitigation
Implementing a risk mitigation process when changing suppliers involves several key steps.
Each step is critical to ensuring a smooth transition and minimizing any impact on the business’s operations.
1. Comprehensive Supplier Evaluation
The first step in the risk mitigation process is conducting a thorough evaluation of potential suppliers.
This involves assessing multiple aspects such as the supplier’s capabilities, financial health, reputation, and compliance with regulatory standards.
It’s essential to verify their ability to meet your quality standards and deliver products on time.
2. Risk Assessment and Identification
Before making any supplier changes, assess any potential risks involved.
Identify specific risks related to the new supplier’s performance, financial stability, geographic location, and political or economic conditions that could affect their operations.
This helps in understanding which areas require more focus during the transition period.
3. Developing a Transition Plan
Creating a detailed transition plan is crucial.
This plan should outline all necessary steps for switching suppliers, timelines, responsible individuals, and risk management measures.
A well-structured transition plan minimizes disruption and ensures that everyone involved understands their roles and responsibilities.
4. Stakeholder Engagement
Engaging with relevant stakeholders is vital in the supplier change process.
This includes internal teams such as purchasing, logistics, quality control, and external partners like existing and new suppliers.
Effective communication helps in aligning everyone with the transition strategy and addressing any concerns promptly.
5. Preparing Contingency Plans
A comprehensive risk mitigation process includes preparing contingency plans for unforeseen issues.
Contingency plans involve alternative strategies or backup plans that can be activated if things do not go as planned.
For instance, having backup suppliers or additional inventory can help manage unexpected disruptions or delays.
6. Contractual Safeguards
Establishing clear contractual terms with the new supplier is essential for mitigating risks.
Contracts should include clauses for quality standards, delivery timelines, penalties for non-compliance, and other critical aspects such as intellectual property rights and confidentiality agreements.
Careful drafting of the contract helps in reducing the chances of disputes and misunderstandings later on.
7. Performance Monitoring and Feedback
Once the supplier shift is underway, monitoring the supplier’s performance is crucial.
Regular audits, performance reviews, and feedback sessions help in ensuring that the new supplier meets your expectations and adheres to agreed-upon terms.
It also allows for timely identification and resolution of any issues that may arise.
Challenges and Considerations
While a risk mitigation process is indispensable, certain challenges may arise during the supplier change process.
Managing Cultural Differences
If the new supplier is located in a different country or region, cultural differences can pose a challenge.
Understanding and respecting variations in business practices, communication styles, and working norms are essential for maintaining a good relationship with the supplier.
Assessing Quality Management Systems
Verifying the new supplier’s quality management systems ensures that they can consistently deliver products that meet your quality standards.
This involves reviewing certifications, processes, and policies they follow for quality management.
Adapting to Changing Market Conditions
Market conditions, including fluctuations in supply chain dynamics, can change rapidly.
Keeping abreast of these changes allows for strategic adjustments to the risk mitigation process, ensuring that potential impacts are minimized.
Conclusion
Implementing a thorough risk mitigation process is essential when changing suppliers.
It ensures a seamless transition by identifying potential risks, preparing for unforeseen challenges, and establishing robust systems for performance monitoring and feedback.
By involving key stakeholders and maintaining open communication, companies can successfully mitigate risks, ensuring continuity and minimizing disruptions in their operations.
Remember, the success of this process largely depends on careful planning, continuous monitoring, and the ability to adapt to changing circumstances.
資料ダウンロード
QCD管理受発注クラウド「newji」は、受発注部門で必要なQCD管理全てを備えた、現場特化型兼クラウド型の今世紀最高の受発注管理システムとなります。
ユーザー登録
受発注業務の効率化だけでなく、システムを導入することで、コスト削減や製品・資材のステータス可視化のほか、属人化していた受発注情報の共有化による内部不正防止や統制にも役立ちます。
NEWJI DX
製造業に特化したデジタルトランスフォーメーション(DX)の実現を目指す請負開発型のコンサルティングサービスです。AI、iPaaS、および先端の技術を駆使して、製造プロセスの効率化、業務効率化、チームワーク強化、コスト削減、品質向上を実現します。このサービスは、製造業の課題を深く理解し、それに対する最適なデジタルソリューションを提供することで、企業が持続的な成長とイノベーションを達成できるようサポートします。
製造業ニュース解説
製造業、主に購買・調達部門にお勤めの方々に向けた情報を配信しております。
新任の方やベテランの方、管理職を対象とした幅広いコンテンツをご用意しております。
お問い合わせ
コストダウンが利益に直結する術だと理解していても、なかなか前に進めることができない状況。そんな時は、newjiのコストダウン自動化機能で大きく利益貢献しよう!
(β版非公開)