- お役立ち記事
- Risk prediction method for purchasing department to prevent material supply problems
Risk prediction method for purchasing department to prevent material supply problems
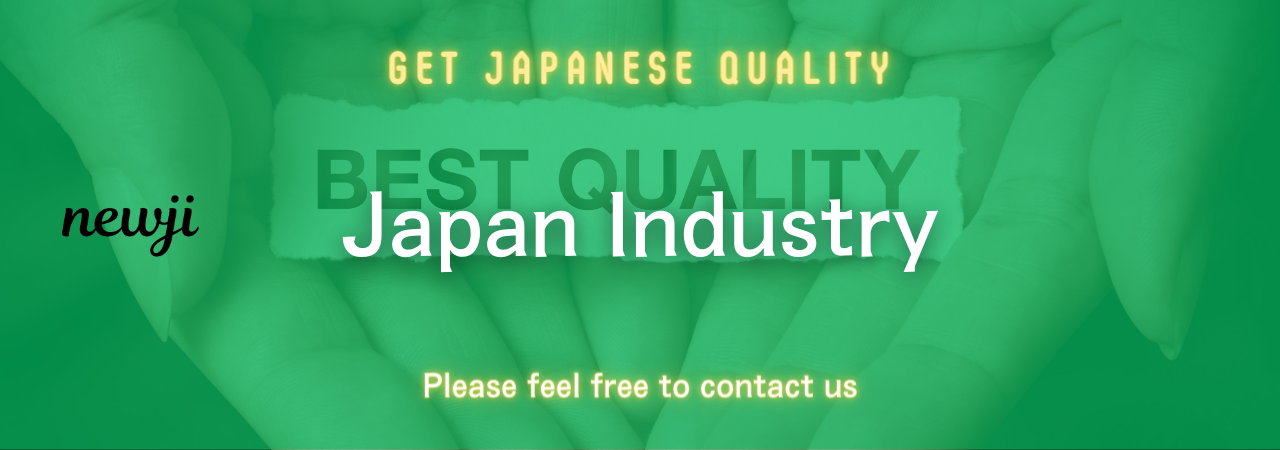
目次
Understanding the Importance of Risk Prediction in Purchasing
In today’s fast-paced business environment, the purchasing departments in organizations hold a critical role.
One of their main responsibilities is ensuring a steady and reliable supply of materials necessary for the production and delivery of goods.
However, risks such as supply chain disruptions, vendor reliability issues, and fluctuating market demands can severely impact their ability to secure these materials.
This is where risk prediction methods become vital.
By identifying potential risks before they materialize, purchasing departments can proactively address issues, ensuring smooth operations.
Key Risks in Material Supply
To effectively predict risks, it’s first essential to identify what these risks are.
There are several common risks associated with material supply that purchasing departments need to be aware of:
1. Supplier Reliability
Suppliers may have various challenges, including financial instability, operational mishaps, or logistical hurdles.
Any of these can lead to unfulfilled orders or quality issues.
It’s crucial for purchasing departments to assess the past performance and reliability of suppliers.
2. Market Fluctuations
The global market is subject to fluctuations which can lead to price volatility, affecting the availability of materials.
Market fluctuations can arise due to numerous factors such as geopolitical events, economic downturns, or sudden increases in demand.
3. Natural Disasters and Unexpected Events
Natural disasters, pandemics, and other unexpected events can disrupt supply chains.
These events might halt production, damage inventories, or delay transportation routes, leading to supply shortages.
Effective Risk Prediction Methods
Identifying potential risks is only the first step.
The next step involves implementing effective risk prediction methods that can help mitigate these risks.
1. Data Analytics
Data analytics is becoming increasingly important in risk management.
By analyzing historical data, purchasing departments can identify patterns and trends, gaining valuable insights into potential future risks.
Utilizing tools that process large datasets can help forecast supply chain disruptions or price changes, allowing for timely strategic decisions.
2. Supplier Risk Assessment
Regularly conducting supplier risk assessments helps in understanding the risk profile of each supplier.
This involves examining financial health, compliance records, and performance history.
Implementing regular audits and developing strong relationships with suppliers can further mitigate risks.
3. Diversification
Relying on a single supplier or a limited geographic area can be risky.
Having a diversified supplier base ensures that if one supplier is unable to meet demand, others can fill the gap.
Furthermore, diversifying the geographic sources of materials can help minimize risks associated with regional disruptions.
Implementing a Risk Prediction Strategy
Implementing an effective risk prediction strategy requires an integrated approach, combining various methods for optimal results.
Step 1: Establish a Risk Management Framework
Develop a comprehensive framework that outlines the process of identifying, assessing, monitoring, and mitigating risks.
Include key performance indicators (KPIs) to measure the effectiveness of your risk management strategy.
Step 2: Leverage Technology
Invest in technological tools that assist in risk prediction and mitigation.
Supply chain management software, predictive analytics tools, and real-time data monitoring platforms can provide critical insights and automate processes, making risk management more efficient.
Step 3: Collaborate Across Departments
Risk management in purchasing is more effective when there’s collaboration across departments.
Communicate with other departments such as operations, finance, and logistics to coordinate and share risk information.
A collaborative approach can lead to more thorough and comprehensive risk assessments.
The Benefits of Predictive Risk Management
Utilizing a predictive approach to risk management offers several benefits for purchasing departments.
1. Enhanced Decision-Making
With access to predictive insights, purchasing departments can make informed decisions, optimizing purchasing strategies and minimizing potential losses.
2. Increased Supplier Confidence
By proactively managing risk, suppliers gain confidence in your ability to maintain steady business relations, fostering stronger relationships and better terms.
3. Improved Operational Efficiency
Predictive risk management helps avoid supply disruptions, maintaining steady production and delivery schedules, which in turn boosts overall operational efficiency.
Challenges in Risk Prediction
While risk prediction offers many advantages, it’s not without challenges.
1. Data Quality
The accuracy of risk predictions largely depends on the quality of data.
Inadequate or incorrect data can lead to faulty predictions and misguided strategies.
2. Rapid Market Changes
Markets can change overnight, rendering some predictive models ineffective.
Staying updated and continuously testing and refining models is vital.
3. Resource Constraints
Developing and maintaining advanced risk prediction models might require significant resources, which can be a constraint for some organizations.
Conclusion
Incorporating risk prediction methods in purchasing departments is no longer optional, but a necessity for navigating the complex landscape of modern supply chains.
By leveraging data analytics, conducting thorough supplier assessments, and implementing a comprehensive risk management strategy, purchasing departments can safeguard against potential material supply issues.
While challenges exist, the benefits of predictive risk management—enhanced decision-making, better supplier relationships, and improved operational efficiency—make it an invaluable strategy for success in an unpredictable world.
資料ダウンロード
QCD調達購買管理クラウド「newji」は、調達購買部門で必要なQCD管理全てを備えた、現場特化型兼クラウド型の今世紀最高の購買管理システムとなります。
ユーザー登録
調達購買業務の効率化だけでなく、システムを導入することで、コスト削減や製品・資材のステータス可視化のほか、属人化していた購買情報の共有化による内部不正防止や統制にも役立ちます。
NEWJI DX
製造業に特化したデジタルトランスフォーメーション(DX)の実現を目指す請負開発型のコンサルティングサービスです。AI、iPaaS、および先端の技術を駆使して、製造プロセスの効率化、業務効率化、チームワーク強化、コスト削減、品質向上を実現します。このサービスは、製造業の課題を深く理解し、それに対する最適なデジタルソリューションを提供することで、企業が持続的な成長とイノベーションを達成できるようサポートします。
オンライン講座
製造業、主に購買・調達部門にお勤めの方々に向けた情報を配信しております。
新任の方やベテランの方、管理職を対象とした幅広いコンテンツをご用意しております。
お問い合わせ
コストダウンが利益に直結する術だと理解していても、なかなか前に進めることができない状況。そんな時は、newjiのコストダウン自動化機能で大きく利益貢献しよう!
(Β版非公開)