- お役立ち記事
- Risks in supplier selection and key points in purchasing quality control
月間76,176名の
製造業ご担当者様が閲覧しています*
*2025年3月31日現在のGoogle Analyticsのデータより
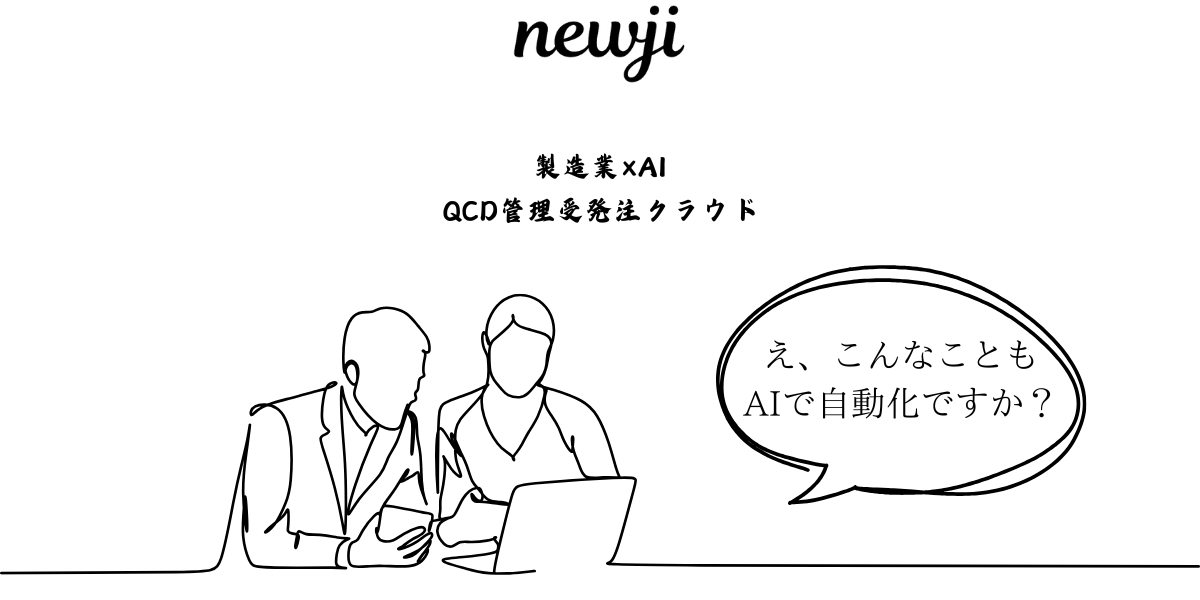
Risks in supplier selection and key points in purchasing quality control
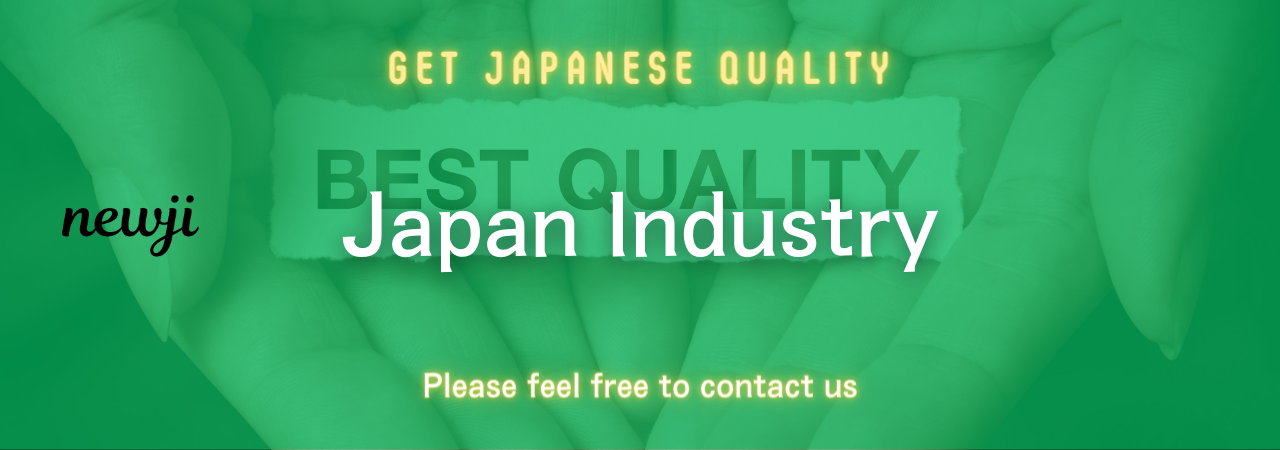
目次
Understanding the Risks in Supplier Selection
When it comes to any business, choosing the right suppliers is a critical part of ensuring your organization’s smooth and efficient operation.
However, with the advantages of a great supplier, there also come risks that can affect your business negatively if not managed properly.
This article will explore the various risks involved in supplier selection and how you can mitigate them.
Supplier Reliability
One of the foremost risks in supplier selection is reliability.
A supplier’s reliability can significantly impact your production schedules and the quality of your end products.
Unreliable suppliers may deliver late, provide inconsistent quality, or fail to deliver altogether.
To prevent this, it’s crucial to perform comprehensive due diligence before finalizing any supplier agreements.
This includes checking references, evaluating past performance, and understanding their capacity to meet your demands consistently.
Building strong relationships with your suppliers and providing feedback can also enhance reliability.
Quality Concerns
Quality control is a major concern when selecting suppliers.
Subpar materials or components can lead directly to customer dissatisfaction and harm your brand’s reputation.
It is essential to ensure that the supplier adheres to your quality standards through standards verification and regular audits.
Implementing a robust quality assurance process that includes regular inspections and ensuring your suppliers understand your quality requirements can mitigate such risks.
Considering suppliers that have certifications or adhere to internationally recognized quality standards is also beneficial.
Financial Stability
Another critical factor is the financial stability of your suppliers.
Financial instability in a supplier can lead to sudden business closures or an inability to fulfill orders, which can disrupt your supply chain.
It’s imperative to assess their financial standing to ensure they can sustain long-term partnerships.
This might involve a review of their financial statements, credit scores, and market reputation.
Choosing financially stable suppliers can decrease the risk of supply chain interruptions.
Geopolitical Risks
In today’s global market, geopolitical factors can immensely influence supplier selection.
Political instability, regulatory changes, and trade restrictions can impact a supplier’s ability to deliver.
Understanding the geopolitical landscape of a supplier’s location and assessing how these factors could affect your supply chain is crucial.
Consider diversifying your supplier base across different regions to reduce dependency on any single area potentially facing instability.
Environmental Considerations
Environmental consciousness is becoming increasingly crucial for businesses.
Suppliers that don’t adhere to environmental regulations can pose significant risks, such as fines or damage to your company’s reputation.
It’s essential to understand the environmental policies of potential suppliers and ensure their practices align with your corporate social responsibility commitments.
Choose suppliers committed to sustainability and verify their compliance with environmental standards.
Communication Barriers
Effective communication is a cornerstone of successful supplier relationships.
Language differences, cultural barriers, and time zone differences can hinder effective communication, leading to misunderstandings and delays.
To tackle this risk, establish clear communication channels and regularly update each other on any changes or issues.
Consider using technology tools that facilitate seamless communication and ensure both parties are on the same page.
Key Points in Purchasing Quality Control
Having addressed the risks in supplier selection, it’s equally important to focus on quality control in the purchasing process.
Here are some key points to consider for effective quality control.
Set Clear Specifications
Begin by setting clear and precise specifications for the goods or services you intend to purchase.
Vague specifications can lead to variations in the received products.
Ensure that both you and your supplier are on the same page regarding the essentials of quality, dimensions, materials, and other specifics.
Regular Quality Audits
Implement a system for regular audits of the supplier’s processes and products.
This will help ensure ongoing compliance with your quality standards.
It is crucial to visit supplier facilities to observe their operations and identify any potential issues firsthand.
Regular audits foster accountability and encourage continual improvement from suppliers.
Implement a Supplier Scorecard
A supplier scorecard is an effective tool for tracking and evaluating a supplier’s performance over time.
It includes metrics such as delivery timeliness, quality standards, pricing, and more.
Regularly reviewing these scorecards allows you to address any declining trends in supplier performance before they become serious problems.
Build Strong Relationships
Invest in building strong relationships with your suppliers.
Strong partnerships often translate into better cooperation, easier problem-solving, and more flexibility when unforeseen issues arise.
Regular meetings and open dialogue can encourage partners to align with your goals and quality standards.
Train and Support Your Team
Your procurement team plays a crucial role in purchasing quality control.
Invest in continuous training and provide them with the resources needed to ensure they can effectively manage supplier interactions and regulatory requirements.
A well-trained team is pivotal in executing your quality control strategy efficiently.
By understanding the risks associated with supplier selection and focusing on key points in purchasing quality control, you can significantly enhance your business’s supply chain resilience and overall success.
Careful planning, ongoing communication, and active engagement with suppliers are essential in navigating these challenges effectively.
資料ダウンロード
QCD管理受発注クラウド「newji」は、受発注部門で必要なQCD管理全てを備えた、現場特化型兼クラウド型の今世紀最高の受発注管理システムとなります。
ユーザー登録
受発注業務の効率化だけでなく、システムを導入することで、コスト削減や製品・資材のステータス可視化のほか、属人化していた受発注情報の共有化による内部不正防止や統制にも役立ちます。
NEWJI DX
製造業に特化したデジタルトランスフォーメーション(DX)の実現を目指す請負開発型のコンサルティングサービスです。AI、iPaaS、および先端の技術を駆使して、製造プロセスの効率化、業務効率化、チームワーク強化、コスト削減、品質向上を実現します。このサービスは、製造業の課題を深く理解し、それに対する最適なデジタルソリューションを提供することで、企業が持続的な成長とイノベーションを達成できるようサポートします。
製造業ニュース解説
製造業、主に購買・調達部門にお勤めの方々に向けた情報を配信しております。
新任の方やベテランの方、管理職を対象とした幅広いコンテンツをご用意しております。
お問い合わせ
コストダウンが利益に直結する術だと理解していても、なかなか前に進めることができない状況。そんな時は、newjiのコストダウン自動化機能で大きく利益貢献しよう!
(β版非公開)