- お役立ち記事
- Roadmap and practical examples for successful DX promotion in the manufacturing industry
月間76,176名の
製造業ご担当者様が閲覧しています*
*2025年3月31日現在のGoogle Analyticsのデータより
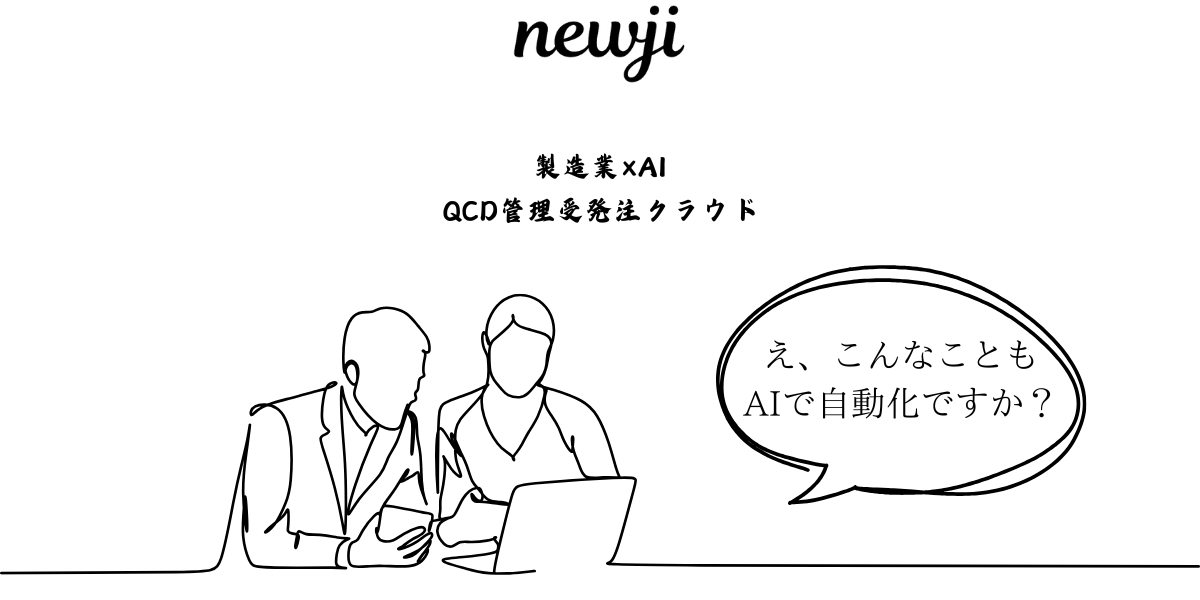
Roadmap and practical examples for successful DX promotion in the manufacturing industry
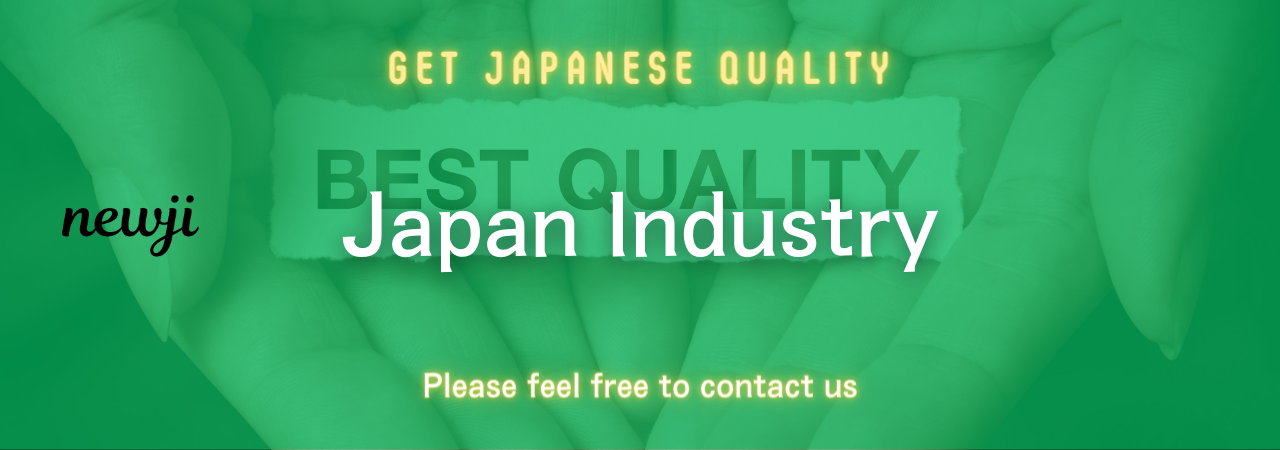
目次
Understanding Digital Transformation in Manufacturing
Digital Transformation (DX) is reshaping industries, and manufacturing is no exception.
The integration of digital technology into all areas of business operations, processes, and models allows for significant improvements in efficiency, agility, and innovation.
For the manufacturing industry, DX involves the adoption of technologies such as the Internet of Things (IoT), artificial intelligence (AI), data analytics, and cloud computing.
The goal of DX in manufacturing is to create smart factories that enhance productivity and streamline operations.
By utilizing these digital tools, manufacturers can reduce costs, improve quality, and respond quickly to market changes.
Benefits of Digital Transformation in Manufacturing
Adopting digital transformation strategies in manufacturing offers numerous advantages.
One key benefit is increased efficiency.
Automated processes reduce human error and speed up production times.
Another major advantage is enhanced customer satisfaction.
With real-time monitoring and automated quality control, manufacturers can ensure that products meet customer expectations consistently.
Digital transformation also fosters innovation.
With data analytics, manufacturers can gain insights into market trends and consumer preferences, leading to the development of new products and services.
Furthermore, integrating IoT in manufacturing enables predictive maintenance, minimizing downtime and extending equipment lifespan.
Steps to a Successful DX Roadmap
Manufacturing firms embarking on a digital transformation journey need a clear roadmap to guide their efforts.
Here are some steps to create a strategic DX roadmap:
1. Assess Current Capabilities
Before initiating any transformation, it is crucial to assess the current state of your manufacturing processes.
Understand existing capabilities, technologies in use, and areas that require improvement.
This assessment will help determine which digital tools and strategies are most suitable for your organization.
2. Define DX Goals
Set clear, achievable goals for your digital transformation.
These objectives should align with your overall business strategy and cater to both short-term improvements and long-term growth.
Identify key performance indicators (KPIs) to measure progress and success.
3. Develop a Strategic Plan
Create a strategic plan that outlines the steps required to achieve your DX goals.
This plan should cover technology adoption, process changes, and workforce training.
Consider creating a digital transformation team to oversee the implementation of the roadmap.
4. Invest in Technology
Select the technologies that will best support your DX goals.
Focus on scalable, integrated solutions that can grow with your organization.
Common technologies to consider include cloud-based platforms, IoT devices, AI-powered analytics, and advanced robotics.
5. Foster a Digital Culture
Successful digital transformation requires a cultural shift within the organization.
Encourage a digital mindset among employees by providing training and promoting collaboration.
Leadership should demonstrate a commitment to digital change and support innovative ideas.
6. Monitor and Adapt
Digital transformation is an ongoing process, requiring continuous monitoring and adaptation.
Regularly review the progress of your DX initiatives, using KPIs to identify areas for improvement.
Be prepared to make changes to your roadmap as new technologies emerge and market conditions evolve.
Practical Examples of DX in Manufacturing
Many manufacturers are already leveraging digital transformation to gain a competitive edge.
Here are some practical examples of how DX is being implemented in the industry:
Smart Factories
Smart factories are at the forefront of digital transformation in manufacturing.
These facilities integrate IoT, AI, and automation to optimize production processes.
For instance, real-time data from connected devices can be used to monitor equipment health and predict maintenance needs, reducing downtime.
Digital Twin Technology
Digital twins are virtual replicas of physical assets or processes that are used to simulate and analyze real-world scenarios.
In manufacturing, digital twin technology allows companies to test production lines and product designs before actual implementation.
This leads to increased efficiency and reduced risk of costly errors.
Advanced Robotics
Robotics has long played a role in manufacturing, but recent advancements are pushing the boundaries of what is possible.
Collaborative robots, or cobots, can work alongside human operators, performing repetitive tasks with precision.
This increases productivity and allows human workers to focus on more complex activities.
AI-Driven Quality Control
AI technology is revolutionizing quality control in manufacturing.
Machine learning algorithms can analyze production data to identify defects and ensure product quality.
This real-time analysis allows manufacturers to address issues quickly and reduce waste.
Challenges and Considerations
While digital transformation offers significant benefits, it also presents challenges that manufacturers must address.
One major challenge is data security.
As more devices and processes become connected, ensuring the security of sensitive data is paramount.
Another consideration is the cost of technology adoption.
Manufacturers must weigh the initial investment against potential long-term benefits.
Additionally, achieving a seamless integration of new technologies with existing systems can be complex.
A phased approach to implementation can help mitigate disruptions.
Conclusion
Digital transformation is a critical component of the modern manufacturing landscape.
By embracing digital technologies and developing a strategic roadmap, manufacturers can enhance efficiency, foster innovation, and improve customer satisfaction.
While challenges exist, the potential rewards of digital transformation make it an essential pursuit for any manufacturing company looking to thrive in an increasingly competitive market.
資料ダウンロード
QCD管理受発注クラウド「newji」は、受発注部門で必要なQCD管理全てを備えた、現場特化型兼クラウド型の今世紀最高の受発注管理システムとなります。
ユーザー登録
受発注業務の効率化だけでなく、システムを導入することで、コスト削減や製品・資材のステータス可視化のほか、属人化していた受発注情報の共有化による内部不正防止や統制にも役立ちます。
NEWJI DX
製造業に特化したデジタルトランスフォーメーション(DX)の実現を目指す請負開発型のコンサルティングサービスです。AI、iPaaS、および先端の技術を駆使して、製造プロセスの効率化、業務効率化、チームワーク強化、コスト削減、品質向上を実現します。このサービスは、製造業の課題を深く理解し、それに対する最適なデジタルソリューションを提供することで、企業が持続的な成長とイノベーションを達成できるようサポートします。
製造業ニュース解説
製造業、主に購買・調達部門にお勤めの方々に向けた情報を配信しております。
新任の方やベテランの方、管理職を対象とした幅広いコンテンツをご用意しております。
お問い合わせ
コストダウンが利益に直結する術だと理解していても、なかなか前に進めることができない状況。そんな時は、newjiのコストダウン自動化機能で大きく利益貢献しよう!
(β版非公開)