- お役立ち記事
- “Robot introduction plan” promoted by management team—Basics of technology introduction that field leaders should know
“Robot introduction plan” promoted by management team—Basics of technology introduction that field leaders should know
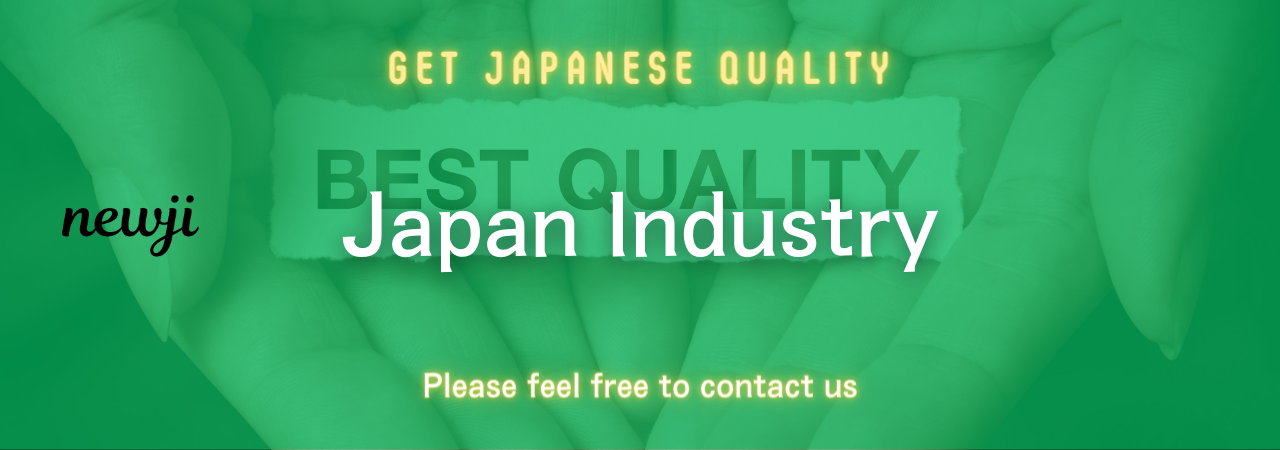
目次
Understanding the Basics of Robot Introduction
Robots are no longer just a concept from science fiction.
In today’s world, they are becoming an essential part of various industries, enhancing productivity and efficiency.
The management team often spearheads the integration of robots into operations, but it’s crucial for field leaders to grasp the basic aspects of this technology introduction as well.
To introduce robots effectively, it is vital to understand what makes them a valuable asset.
Robots can perform repetitive tasks with precision and speed, which can significantly boost productivity.
They can operate 24/7 without fatigue, ensuring continuous production, which is particularly beneficial in manufacturing and logistics industries.
The Role of a Management Team in Robot Integration
Management teams play a critical role in initiating and guiding the process of integrating robots into a company’s operations.
They must assess the company’s needs and determine the areas where robotic assistance can yield the most significant benefits.
One of the primary responsibilities of the management team is to conduct a thorough cost-benefit analysis.
This involves understanding the costs associated with purchasing and maintaining robots, as well as training staff to work alongside this new technology.
The management team must ensure that the investment in robotics aligns with the company’s strategic goals and budget constraints.
Additionally, the management team must engage stakeholders, including employees, in the conversation about robot integration.
This is crucial for minimizing resistance to change and ensuring that the workforce is prepared for the transition.
Preparing Field Leaders for Technological Changes
Field leaders are often at the forefront of implementing new technologies like robots.
Therefore, they must be well-prepared to handle the changes that come with robot introduction.
One of the first steps in preparing field leaders is education and training.
They need to understand how robots work and the benefits they bring to their specific areas of operation.
Providing comprehensive training programs can help field leaders gain the technical knowledge necessary to operate and troubleshoot robotic systems.
Field leaders should also be encouraged to develop soft skills, such as communication and problem-solving, to manage the human and technological elements effectively.
Involving Field Leaders in the Planning Process
It’s beneficial to involve field leaders in the planning process from the start.
Their on-the-ground experience can provide valuable insights into potential challenges and help identify the critical areas that would benefit most from robotic assistance.
By involving field leaders early, the management team can foster a sense of ownership and commitment, leading to smoother implementation and better outcomes.
Ensuring Smooth Implementation of Robots
Implementing robots in an organization requires careful planning and execution.
A phased approach can be effective, starting with pilot projects in selected departments.
This allows the management team to identify any issues and make necessary adjustments before a full-scale rollout.
Field leaders should be equipped with clear guidelines and support throughout the implementation phase.
Regular feedback sessions can help address concerns and ensure that the transition is as seamless as possible.
Monitoring and Evaluating the Impact of Robots
Once robots are introduced, it’s essential to monitor their performance and impact on operations.
Key performance indicators (KPIs) should be established to assess the effectiveness of robotic systems in enhancing productivity and reducing costs.
Field leaders play a crucial role in this evaluation process.
Their observations and evaluations can provide valuable data on the real-world impacts of robotic integration.
Regular reports from field leaders can help management teams make informed decisions about scaling up robot use or making adjustments to the existing setup.
Addressing Human Concerns and Workplace Dynamics
One of the challenges in introducing robots is addressing human concerns.
Employees may fear job displacement or struggle with adapting to new technologies.
It’s vital to address these concerns proactively through open communication and job transition support.
Robots should be positioned as tools that assist employees, rather than replacements.
This can be achieved by highlighting how robots can take over mundane tasks, freeing up time for employees to focus on more rewarding and strategic activities.
Field leaders can play a significant role in facilitating this transition by promoting collaboration between human workers and robots.
They can encourage teams to see robots as partners that enhance workplace capabilities and productivity.
The Future of Robotics in the Workplace
As technology advances, the role of robots in the workplace is set to expand even further.
Field leaders must stay informed about the latest developments and be ready to adapt their operations to incorporate new technological advancements.
Continual learning and adaptation are necessary for staying competitive in increasingly tech-driven industries.
By embracing robots as valuable tools and fostering a culture of innovation, companies can enhance their productivity and efficiency in the long run.
The integration of robots into the workplace is not just a trend but a strategic move towards the future.
Field leaders, with their hands-on experience and knowledge, are in a unique position to drive this transformation successfully.
資料ダウンロード
QCD調達購買管理クラウド「newji」は、調達購買部門で必要なQCD管理全てを備えた、現場特化型兼クラウド型の今世紀最高の購買管理システムとなります。
ユーザー登録
調達購買業務の効率化だけでなく、システムを導入することで、コスト削減や製品・資材のステータス可視化のほか、属人化していた購買情報の共有化による内部不正防止や統制にも役立ちます。
NEWJI DX
製造業に特化したデジタルトランスフォーメーション(DX)の実現を目指す請負開発型のコンサルティングサービスです。AI、iPaaS、および先端の技術を駆使して、製造プロセスの効率化、業務効率化、チームワーク強化、コスト削減、品質向上を実現します。このサービスは、製造業の課題を深く理解し、それに対する最適なデジタルソリューションを提供することで、企業が持続的な成長とイノベーションを達成できるようサポートします。
オンライン講座
製造業、主に購買・調達部門にお勤めの方々に向けた情報を配信しております。
新任の方やベテランの方、管理職を対象とした幅広いコンテンツをご用意しております。
お問い合わせ
コストダウンが利益に直結する術だと理解していても、なかなか前に進めることができない状況。そんな時は、newjiのコストダウン自動化機能で大きく利益貢献しよう!
(Β版非公開)