- お役立ち記事
- Robots Revolutionizing Japanese Manufacturing: The Future of Industry 4.0
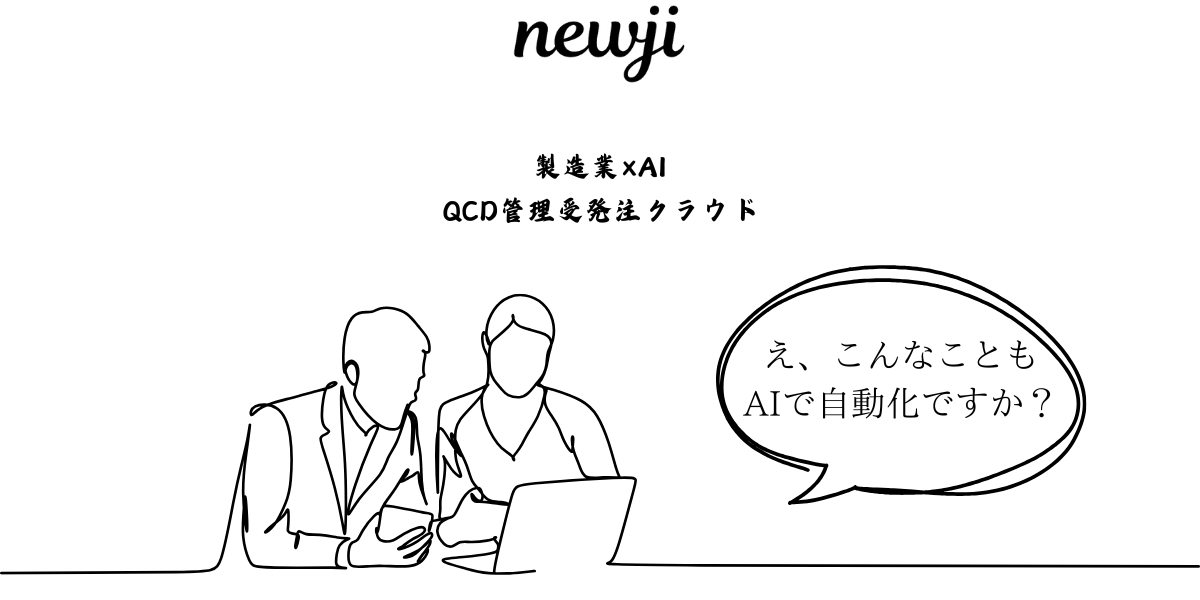
Robots Revolutionizing Japanese Manufacturing: The Future of Industry 4.0
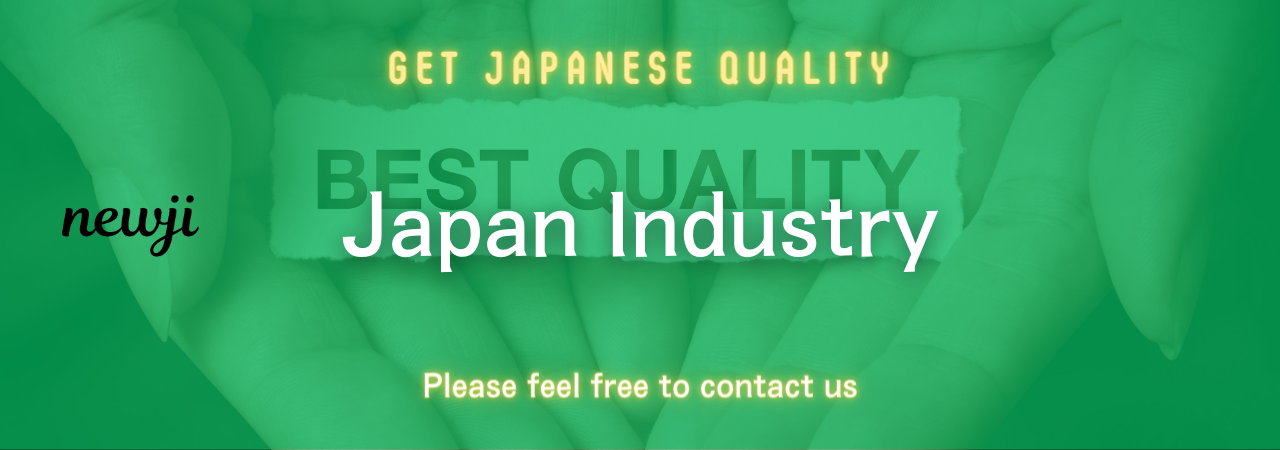
目次
The Dawn of Industry 4.0: A New Era in Manufacturing
As we stand at the precipice of Industry 4.0, it is evident that we are witnessing the dawn of a new era in manufacturing. This revolution is characterized by the integration of cutting-edge technologies such as artificial intelligence (AI), the Internet of Things (IoT), and robotics into traditional manufacturing processes. Nowhere is this transformation more apparent than in Japan, a nation renowned for its technical prowess and innovation in manufacturing.
Overview of Robotics in Japanese Manufacturing
Japan has long been at the forefront of robotics technology, a position it continues to hold with authority. Japanese manufacturing companies have embraced robots not just as tools of production, but as integral components of their operational strategy. The adoption of robots has led to significant enhancements in efficiency, quality, and scalability, as well as improved worker safety.
Japanese robots are now capable of performing a wide range of tasks, from assembly and welding to painting and packaging. Their precision, combined with speed, has allowed for greater flexibility and a reduction in production errors. As a result, Japanese manufacturers can produce high-quality products consistently, meeting the stringent quality standards expected in today’s global marketplace.
Advantages of Robotics in Japanese Manufacturing
Increased Efficiency and Productivity
One of the paramount advantages of integrating robots into manufacturing is the substantial boost in operational efficiency. Robots can work continuously without the need for breaks, ensuring that production lines run smoothly around the clock. This constant operation significantly increases output and reduces cycle times, leading to higher productivity levels.
Enhanced Quality Control
Robots excel in performing repetitive tasks with precision, drastically reducing the occurrence of human errors. This capability is especially critical in industries where even minor deviations can lead to significant defects. With robots, manufacturers can maintain consistent quality, meeting the high standards necessary to remain competitive in the global market.
Cost Reduction
While the initial investment in robotics technology can be substantial, the long-term cost savings are undeniable. By improving efficiency and reducing waste, robots help to lower overall production costs. Moreover, the reduction in defects and improved quality control translate into fewer recalls and less material waste, further driving down costs.
Improved Worker Safety
Robots can undertake hazardous tasks that would otherwise pose significant risks to human workers, such as handling dangerous chemicals or operating heavy machinery. This shift not only ensures worker safety but also allows employees to focus on more complex and intellectually stimulating tasks, thereby enhancing job satisfaction and productivity.
Challenges and Disadvantages
High Initial Investment
The integration of advanced robotics into manufacturing processes requires a significant upfront capital investment. This includes not only the cost of the robots themselves but also necessary infrastructure enhancements and workforce training programs. For small and medium-sized enterprises (SMEs), these financial barriers can be daunting.
Technological and Skill Barriers
The successful implementation of robotics technology demands a workforce that is well-versed in its operation and maintenance. This requirement necessitates comprehensive training programs and possibly the hiring of skilled technical personnel, both of which can be resource-intensive. Additionally, there can be a steep learning curve associated with the transition to automated systems.
Maintenance and Downtime
Just like any other sophisticated machinery, robots require regular maintenance to operate optimally. Unplanned downtime due to technical malfunctions can disrupt production schedules and result in substantial financial losses. Therefore, it’s critical to establish robust maintenance protocols and have contingency plans in place to address potential breakdowns.
Job Displacement
The rise of robotics in manufacturing has sparked concerns over job displacement, as robots replace human workers in specific job roles. While automation can lead to the creation of new job categories, there is still an inherent risk of unemployment for those whose skills are rendered obsolete. Thus, it’s imperative to balance automation with workforce development programs that can reskill and upskill employees.
Supplier Negotiation Techniques for Procuring Robotics
Understand Market Conditions
Before entering negotiations with suppliers of robotics technology, it’s essential to have a thorough understanding of the current market conditions. This includes knowing the latest advancements in robotics, the key players in the market, and prevailing pricing trends. Armed with this knowledge, procurement professionals can approach negotiations with confidence and a clear understanding of what constitutes a fair deal.
Build Long-Term Relationships
In the realm of robotics procurement, fostering long-term relationships with suppliers can yield substantial benefits. By cultivating trust and establishing a track record of successful transactions, buyers can often secure favorable terms, such as bulk discounts or extended warranties. Moreover, solid relationships with suppliers can provide access to exclusive technological innovations and priority support services.
Leverage Volume Purchases
One of the most effective negotiation strategies is leveraging volume purchases. By committing to larger orders, buyers can often negotiate lower unit prices and additional concessions from suppliers. This approach not only generates cost savings but also establishes the buyer as a key client, potentially leading to enhanced service levels and preferential treatment.
Prioritize Total Cost of Ownership (TCO)
When evaluating offers from suppliers, it’s crucial to consider the total cost of ownership (TCO) rather than just the initial purchase price. TCO encompasses all costs associated with the acquisition, operation, and maintenance of the robotics technology over its lifecycle. By focusing on TCO, procurement professionals can identify offers that provide the greatest long-term value, even if they involve a higher upfront investment.
Best Practices for Implementing Robotics in Manufacturing
Conduct a Detailed Needs Assessment
The first step in implementing robotics is conducting a comprehensive needs assessment to determine where automation can deliver the most significant benefits. This process involves analyzing current production workflows, identifying bottlenecks, and assessing the potential impact of robotics on overall efficiency. By clearly understanding the specific needs and goals, manufacturers can make informed decisions about which robotic solutions to adopt.
Develop a Robust Integration Plan
Seamless integration of robotics into existing manufacturing processes requires a well-thought-out plan. This plan should outline the stages of integration, define key performance indicators (KPIs), and establish a timeline for implementation. Additionally, it should address potential challenges and include contingency plans to mitigate risks and ensure a smooth transition.
Invest in Training and Development
To maximize the benefits of robotics, it’s essential to invest in comprehensive training programs for the workforce. Employees should be trained not only in the operation of the robots but also in troubleshooting and maintenance. Continuous education and development programs can help workers stay abreast of technological advancements and enhance their ability to contribute effectively to the automated production environment.
Monitor and Optimize Performance
Once the robots are operational, it’s vital to continuously monitor their performance against the established KPIs. Regular assessments can help identify areas for improvement and ensure that the robots are delivering the anticipated benefits. By optimizing performance through ongoing evaluation and adjustment, manufacturers can fully realize the potential of their robotics investment.
The Future of Robotics in Japanese Manufacturing
The future of robotics in Japanese manufacturing looks incredibly promising, with advancements in AI and machine learning poised to take automation to new heights. These technologies are enhancing the capabilities of robots, enabling them to perform more complex tasks and make autonomous decisions. As a result, robots will increasingly take on roles that require high levels of precision and adaptability, further revolutionizing the manufacturing landscape.
Collaborative robots, or cobots, are another exciting development. Designed to work alongside human workers, cobots are enhancing the synergy between human ingenuity and robotic efficiency. This collaboration is driving innovation and enabling manufacturers to tackle more diverse and complex projects, thereby expanding their capabilities and market reach.
Conclusion: Embracing the Robotics Revolution
In conclusion, the integration of robotics into Japanese manufacturing is not just a trend but a pivotal shift towards the future of Industry 4.0. The myriad benefits, from increased efficiency and improved quality control to cost savings and enhanced worker safety, underscore the transformative power of robotics.
However, it’s crucial to acknowledge and address the challenges that come with this transition, such as the high initial investment and potential job displacement. By employing effective negotiation techniques, adhering to best practices for implementation, and continuously evolving with the technology, manufacturers can harness the full potential of robotics.
The future is bright for Japanese manufacturing as it leads the way in embracing the robotics revolution, setting a benchmark for the global industry to follow.
資料ダウンロード
QCD調達購買管理クラウド「newji」は、調達購買部門で必要なQCD管理全てを備えた、現場特化型兼クラウド型の今世紀最高の購買管理システムとなります。
ユーザー登録
調達購買業務の効率化だけでなく、システムを導入することで、コスト削減や製品・資材のステータス可視化のほか、属人化していた購買情報の共有化による内部不正防止や統制にも役立ちます。
NEWJI DX
製造業に特化したデジタルトランスフォーメーション(DX)の実現を目指す請負開発型のコンサルティングサービスです。AI、iPaaS、および先端の技術を駆使して、製造プロセスの効率化、業務効率化、チームワーク強化、コスト削減、品質向上を実現します。このサービスは、製造業の課題を深く理解し、それに対する最適なデジタルソリューションを提供することで、企業が持続的な成長とイノベーションを達成できるようサポートします。
オンライン講座
製造業、主に購買・調達部門にお勤めの方々に向けた情報を配信しております。
新任の方やベテランの方、管理職を対象とした幅広いコンテンツをご用意しております。
お問い合わせ
コストダウンが利益に直結する術だと理解していても、なかなか前に進めることができない状況。そんな時は、newjiのコストダウン自動化機能で大きく利益貢献しよう!
(Β版非公開)