- お役立ち記事
- Role and Application of Cores: Evolution of Die Manufacturing Technology and Molding Technology to Improve Product Quality
Role and Application of Cores: Evolution of Die Manufacturing Technology and Molding Technology to Improve Product Quality
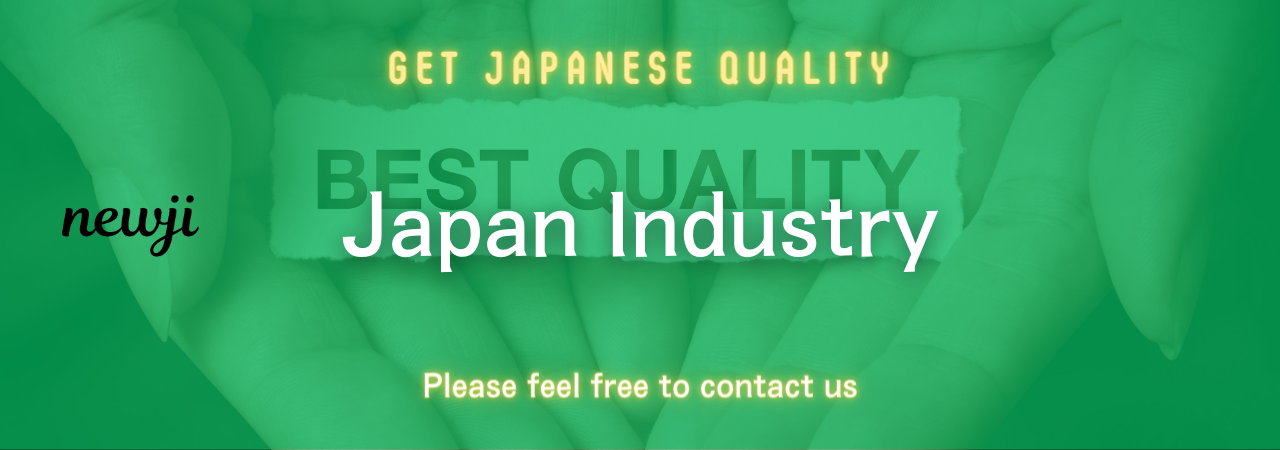
Die manufacturing technology and molding technology have undergone significant advancements over the years.
These improvements have led to better product quality and more efficient production processes.
One critical aspect of these technologies is the use of cores.
Cores play an essential role in the manufacturing of complex shapes and intricate designs.
In this article, we will explore the role and application of cores, how they have evolved, and their impact on improving product quality.
目次
Understanding the Basics: What Are Cores?
Cores are specialized components used in the molding and casting processes.
They are usually made of sand, metal, or other materials, and are placed inside the mold to form the internal cavities and intricate parts of the final product.
The primary function of a core is to create hollow sections within a casting, which would be difficult or impossible to achieve with the mold alone.
Types of Cores
Various types of cores exist, depending on the material and application.
Some common types include:
Sand Cores: Made from sand and a binder, these are most common in metal casting processes.
They are easily removable after the metal has solidified.
Metal Cores: These are used when durability and precision are essential.
Metal cores can withstand higher temperatures and pressures, making them ideal for producing high-quality components.
Ceramic Cores: Typically used in investment casting, ceramic cores provide excellent resistance to high temperatures and are easily removed after casting.
The Evolution of Core Manufacturing
The development of core manufacturing has seen significant advancements, driven by the need for higher precision, better quality, and lower production costs.
Manual Core Making
In the early days, cores were produced manually.
Craftsmen would create cores by hand, using sand and a binder.
This process was time-consuming and labor-intensive.
The quality of the cores depended heavily on the skill and experience of the craftsman.
Mechanized Core Making
With the advent of industrialization, mechanized core making techniques were introduced.
Machines automated the mixing and shaping of sand cores, reducing the reliance on human labor and improving consistency.
Mechanical core making significantly increased production speed and efficiency.
Advanced Core Making Technologies
In recent years, the introduction of advanced technologies such as 3D printing has revolutionized core manufacturing.
3D printing allows for the creation of highly complex and precise cores with minimal material waste.
This technology has opened new possibilities for intricate designs and improved product quality.
Applications of Cores in Modern Manufacturing
Cores are used across various industries to produce a wide range of products.
Here are a few examples of how cores are applied in different manufacturing processes:
Automotive Industry
In the automotive industry, cores are essential for producing engine components, such as cylinder heads and engine blocks.
These parts require precise hollow sections that can only be achieved using high-quality cores.
The use of reliable cores ensures the durability and efficiency of engine components.
Aerospace Industry
Cores play a crucial role in the aerospace industry by enabling the production of lightweight and high-strength components.
For instance, they are used to create turbine blades and other intricate parts that must withstand high temperatures and stress.
Advanced core-making technologies have significantly improved the quality and performance of aerospace components.
Consumer Goods
The manufacturing of household appliances, electronics, and other consumer goods often involves cores to create complex shapes and internal structures.
For example, cores are used to produce hollow handles, intricate casings, and other detailed parts that enhance the functionality and aesthetics of consumer products.
Improving Product Quality Through Core Technology
The use of cores has a direct impact on improving the quality of the final product.
Here’s how advanced core technology contributes to better product quality:
Enhanced Precision and Accuracy
Modern core-making technologies, such as 3D printing, allow for the production of highly precise and accurate cores.
This precision ensures that the final product meets exact specifications and tolerances, resulting in better performance and reliability.
Reduced Defects and Imperfections
High-quality cores help minimize defects and imperfections in the final product.
For example, sand cores with consistent density and strength reduce the risk of cracks, voids, and other casting defects.
This leads to higher-quality and more reliable components.
Complex Designs and Structures
Advanced core technologies enable the production of intricate and complex designs that were previously unattainable.
This capability allows manufacturers to create innovative products with enhanced functionality and aesthetics.
The use of sophisticated cores also helps reduce material waste, contributing to more sustainable manufacturing practices.
The Future of Core Technology
The future of core technology looks promising, with ongoing advancements driving further improvements in product quality and manufacturing efficiency.
Integration of AI and Automation
The integration of artificial intelligence (AI) and automation in core manufacturing is expected to revolutionize the industry.
AI can optimize core designs for improved performance and reduced material usage.
Automation will streamline production processes, further enhancing efficiency and consistency.
Sustainable Core Materials
Researchers are exploring the use of biodegradable and eco-friendly materials for core production.
These sustainable materials aim to reduce environmental impact and contribute to greener manufacturing practices.
The development of new materials can also improve the performance and durability of cores.
Customization and On-Demand Production
Advancements in core technology will likely lead to more customization and on-demand production capabilities.
Manufacturers will be able to produce specialized cores tailored to individual requirements, reducing lead times and improving customer satisfaction.
In conclusion, cores play a vital role in the evolution of die manufacturing technology and molding technology.
The advancements in core-making techniques have significantly improved product quality and manufacturing efficiency.
As technology continues to evolve, the future of core technology looks promising, with new innovations set to drive further improvements in precision, sustainability, and customization.
資料ダウンロード
QCD調達購買管理クラウド「newji」は、調達購買部門で必要なQCD管理全てを備えた、現場特化型兼クラウド型の今世紀最高の購買管理システムとなります。
ユーザー登録
調達購買業務の効率化だけでなく、システムを導入することで、コスト削減や製品・資材のステータス可視化のほか、属人化していた購買情報の共有化による内部不正防止や統制にも役立ちます。
NEWJI DX
製造業に特化したデジタルトランスフォーメーション(DX)の実現を目指す請負開発型のコンサルティングサービスです。AI、iPaaS、および先端の技術を駆使して、製造プロセスの効率化、業務効率化、チームワーク強化、コスト削減、品質向上を実現します。このサービスは、製造業の課題を深く理解し、それに対する最適なデジタルソリューションを提供することで、企業が持続的な成長とイノベーションを達成できるようサポートします。
オンライン講座
製造業、主に購買・調達部門にお勤めの方々に向けた情報を配信しております。
新任の方やベテランの方、管理職を対象とした幅広いコンテンツをご用意しております。
お問い合わせ
コストダウンが利益に直結する術だと理解していても、なかなか前に進めることができない状況。そんな時は、newjiのコストダウン自動化機能で大きく利益貢献しよう!
(Β版非公開)